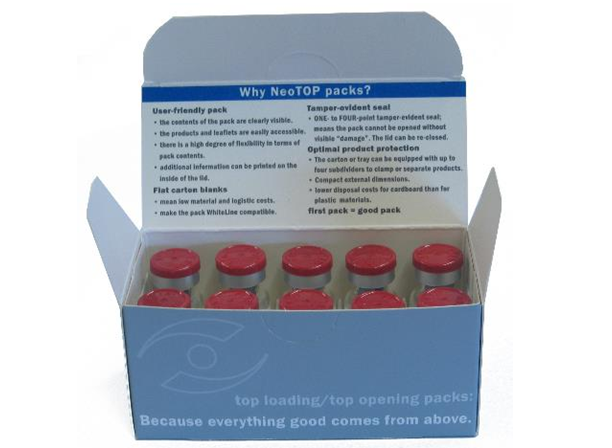
Rapid scale-up The project Includes joint investment and tech transfer to prepare segregated and dedicated manufacturing capacity at Catalent’s Bloomington facility in Indiana to prepare for rapid scale-up and cGMP commercial manufacturing of the investigational vaccine candidate. Catalent plans to hire approximately 300 additional employees at the site for this program starting in July to meet operational readiness for 24×7 manufacturing by January 2021. The 875,000 sq.-ft. facility provides sterile formulation, with drug substance development and manufacturing and drug product fill/finish capacity across liquid and lyophilized vials, prefilled syringes, and cartridges as well as primary and secondary packaging. Scale-up in production will include the use of two new high-speed machines, including a Dividella NeoTOP 1604 top-load cartoner for packaging vials. Unprecedented timeline In a joint news release (see Resources), Catalent CEO John Chiminski commented: “We are proud to collaborate with Johnson & Johnson in its efforts to combat the coronavirus pandemic and save lives.” “Both our organizations have committed to ambitious goals and are executing innovative strategies to meet the forecasted demand on an unprecedented timeline,” said Mr. Chiminski. “We will apply our extensive experience in quickly scaling up manufacturing operations for late-stage and commercial products,” he added. Monomaterial advantage Dividella Sales Director and member of the extended Board, Peter Grassl, said the advantages of choosing the modular 1604 went beyond the machine’s very high speed of up to 160 packages per minute, resulting in 1600 vials per minute. “Remember that vaccines also have to be transported, usually in cold chain, which is expensive. Therefore, it is very important to our customers to have the smallest possible package in order to save money on transport and storage, but at the same time the vials in the package must be securely packed in order to avoid breakages during transport. The bottom line is that those packs have to be as compact and lightweight as possible while still delivering protection. The NeoTOP 1604 is designed to embrace the monomaterial topload solutions that are so important in meeting these challenges,” said Mr. Grassl. “A further bonus is that they give easier access to vials – for hard-pressed healthcare workers under pressure and wearing full Personal Protective Equipment (PPE),” he pointed out. “This is why top load monomaterial packages are preferred by the doctors, because accessibility to the product is better, with no need to struggle in opening blisters or sideload packages while wearing gloves,” Mr. Grassl said. Maximizing OEE The NeoTOP’s ability to run at very high speeds, processing up to 160 multi-vial packs per minute, would be crucial in achieving the Overall Equipment Effectiveness (OEE) and uptime that would be vital in producing a CV-19 vaccine at sufficient scale. “Catalent already uses one of our NeoTOP machines and therefore knows about its great performance, needed for such critical production. Their trust in Dividella also convinced them we could meet their very aggressive timeline,” Peter Grassl explained. Catalent recently completed qualification of its 1,400 m2 secondary packaging expansion at Bloomington to add five new integrated packaging suites featuring new high-speed, automated secondary packaging capabilities with no glass-to-glass contact. This project involved collaborating with packaging industry leaders, OPTIMA, Mikron and Dividella Modular concept The NeoTOP modular concept, allowing easy reconfiguration, was an important consideration in both projects, and especially in CV-19 vaccine production. “Modularity is key for such a COVID machine, because the estimated run time of the CV-19 vaccine is only a couple of years. After that Pandemic is under control, those machines will –most likely- be used to pack different products and pack configuration in the future,” Mr. Grassl explained “Therefore, Dividella’s modularity and flexibility are key in order to re-utilize the machine. For example, the machine could be easily retrofitted to pack syringes instead of vials in the future thus making the machine a great long-term investment and reduce total cost of ownership, or TCO,” he concluded.