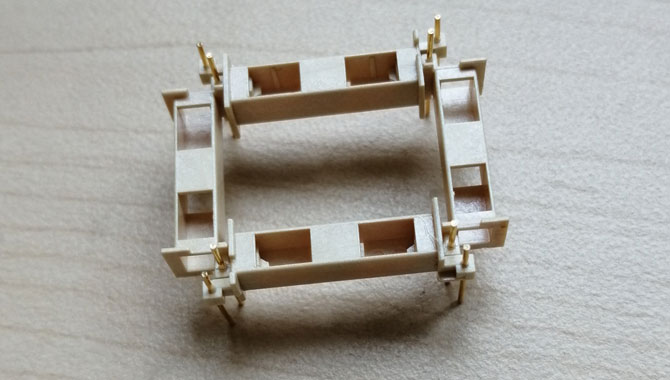
A key challenge for the thin-wall injection moulding process is the 0.5mm average wall thickness of the bobbin, with the thinnest part less than 0.4mm, meaning the risk of the part warping during moulding is high. This was overcome through the application of an in-mould vision pressure sensor.
For the insertion of the bobbin’s ‘golden wire’ – which requires sufficient torque to achieve the necessary coil welding requirements – RPC Ace Shanghai’s innovative high-precision insert moulding technology enables the mould to integrate stamping, cutting and coiling marking.
Equally important, RPC Ace Shanghai’s experience in accurate and complicated mould fabrication was crucial to meeting the higher precision levels for some of the bobbin’s dimensions, for example where the CPK (Complex Process Capability) is greater than 1.33.
RPC Ace Shanghai was also able to apply an innovative smart automatic feeding system to stabilise the tolerances of the bobbin’s ‘golden wire’ insert to between +0.1 - 0.5mm.
The entire project underlines the strong working partnership that was established between Schneider China and RPC Ace Shanghai, comprising initial brainstorming, design finalisation, process testing and troubleshooting, in-mould structure and feeding system optimisation, and OEE ramp-up. This led to the project receiving the Innovate Golden Prize in Schneider China’s 2018 GSC China Best Recognition awards.