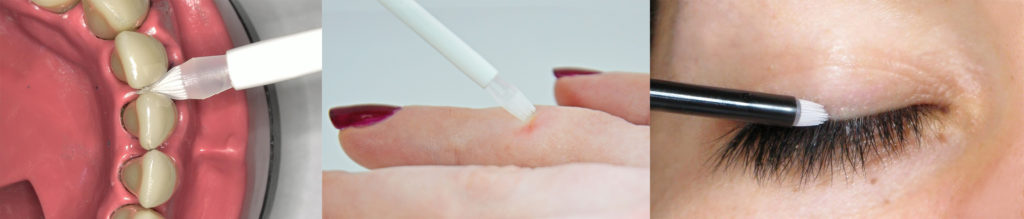
IMPROVEMENT IN TOPICAL & TRANSDERMAL APPLICATION Patients can today easily find deposition systems for liquid and semi-liquid drugs, but they face a real lack of suitable application systems for these formulations, in particular if looking for precise and hygienic dosing with pharma-applicators. This is even more the case when a combined deposition and application is required. Current application systems like cotton tips, flocked applicators, spatulas, nail polish brushes or fingers present major drawbacks such as a lack of sterility, application and dosage precision, poor hygiene and fibre detachment. Therefore, GEKA has adapted its proven technology used in cosmetics to provide systems that combine these two attributes to fulfil pharmaceutical and cosmetic needs. The systems use applicators with extremely delicate microbristles (Figure 1), resulting from many years of expertise in injection-moulding technology and patented processes (EP1465759B1, Method And Device Of The Production Of Brushes). These applicators allow users to uptake formulations under hygienic conditions and to apply these with high precision – even for the most sensitive and pinpoint application areas. As just targeted areas will be touched with the very fine bristles, an increased efficiency and reduced side effects of application are the result. CONTRIBUTION TO INCREASED COMPLIANCE & PERFORMANCE The benefits of microbristle applicators are: 1. Increased application precision (Figure 2): Track precision: bristles do not spread, but create a precise, continuous track Dot precision: bristles do not spread, but create a precise dot Targeted areas: MBA™ reach several areas with their adjusted rigidity and perfect resilience. 2. Increased dosage precision: The MBA™ technology and expertise in topography/design allows us to design applicators with specific shape and geometry for a defined load and release dose of the drug in a consistent and patient-independent way. 3. Guarantee of purity and hygiene: Pure pharma-grade plastics (e.g. LDPE) are used for production without additives, glues, metal or loose fibers. Automated production in one step Radio sterilisation at 25 kGy Depending on the design of the customised MBA™, a wide range of materials (polyolefin and TPE) can be offered. 4. Guarantee of traceability: Full traceability up to the raw materials is ensured. Microbristle systems are not limited to a specific application field and can be used for various market segments (as shown in Figure 3) such as: Dermal care (Rx medicated skin care dermatology, OTC skin care, cosmetic skin care) Oral health care, e.g. mucus membrane treatment, aphthae Dentistry, e.g. easing dentists’ gestures Dental for patients, e.g. bleaching treatments, interdental brushes Eye care, e.g. drops and ointment, infections, sty, lashes/brow treatments Hair / scalp treatments Animal health Ear / nasal / foot / rectal / vaginal care Diagnostics. TEST METHODS & RESULTS GEKA Healthcare can provide services such as sharing methods or realising customised tests using its specifically developed Performance Test Method, for example, to evaluate dosage pick-up and release, or calculation of standard deviation to monitor the consistency of application. Therefore a specific machine with a movement precision of 0.1 mm, included camera system and exact scale is used. This test system was created in collaboration with Ansbach University of Applied Sciences (Figure 4) and allows us to recreate the movement of the applicator during usage by consumer (various positions and angles of the applicator) and to measure uploaded and released quantities of formulations. Dosage Precision Increase The graph in Figure 5 illustrates the difference between standard polyamide (PA) brushes and the GEKA Healthcare MBA™ for the uploaded dose (dose “charged” on the applicator and ready to be applied on the skin) and for the released dose (dose effectively applied on the skin). The product used is water and the system used is the dip-in applicator 28730. In conclusion, the difference between uploaded and released quantity is over four times smaller when using an MBA™, rather than the PA brush. Dosage Precision Consistency Figure 6 illustrates the consistency of dosing for a standard PA brush and for a MBA™ applicator. The product used is water and the system used is the dip-in applicator 28730. The standard deviation is more than ten times smaller for the released quantity with MBA™ compared with a standard PA brush, which means much higher consistency of dose really applied to the patient. The standard deviation for the uploaded quantity is also much smaller for the MBA™. DESIGN & PLATFORM NEEDED FOR A SPECIFIC TRANSDERMAL USE Different designs GEKA Healthcare offers MBA™ in different shapes and sizes, for example with 4.7 bristles per mm². Figure 7 shows convex and concave applicators, applicators with reservoir zones and comb-, brush-, and paint-type applicators. Upon test methods, the specific applicator topography is designed to perfectly match the drug characteristics (e.g. viscosity, surface tension). The length of bristles, space between bristles, bristle density, entire wettable surface and the surface tension of the applicator material can be defined. Different Platforms MBA™ can be combined with various packaging systems as Figure 8 shows: a) Dip-in formats with single usage sticks The drug is contained in any standard bottle of customer’s choice and the single-stick applicator will be delivered beside the bottle. The quantity of sticks per patient is to be defined by the pharma company. The patient deposits a drop of drug on the applicator, and then applies it on the target. Once used, the single-usage stick can be thrown away. b) Dip-in formats with multi-dose packs A complete multi-use packaging is perfectly adapted for warts, scars and wound care. It can contain a small polyethylene terephthalate (PET) or polypropylene (PP) bottle equipped with a wiper ensuring the removal of excess product before the application and a screw-on cap equipped with an MBA™ applicator. The MBA™ can also be combined with temper-evident, child-resistant and standard screw caps with thread according to DIN 168. c) Dip-in single-dose blow fill seal (BFS) packs Together with rommelag (Buchs, Switzerland), a cost-efficient alternative to expensive and complicated dosing systems has been developed. BFS bottelpack® containers are aseptically formed, filled and sealed in one operation cycle in a closed environment. The dip-in microbristle applicator is inserted during the BFS process. The convenient, single-dose device allows for an intuitive, simple use combined with hygienic and precise deposition and application. It uses an advanced aseptic BFS process according to US Pharmacopeia, FDA and GMP guidelines. d) Flow-through tube ‘Twist’n’brush’ GEKA partnered with Neopac (Oberdiessbach, Switzerland), the packaging specialist for Polyfoil® high barrier tubes, to develop this singledose tube packaging. It is based on the original Twist’n’use™ closure system with integrated tamper-evident function: when the nozzle is twisted, the internal tamper-evident pin is detached and the liquid or semi-liquid contents can be applied precisely, without being contaminated. The ultra-fine, soft, pharma-grade plastic bristle brush allows a convenient and gentle topical application of the medicinal products, with utmost precision and hygiene. For medical applications (such as wound care) the entire tube and applicator will be sterilised with gamma rays prior to filling. In order to fulfil the maximum standards of quality, safety and consistency, GEKA manufactures under strict compliance with the stringent ISO 9001:2008 and applicable GMP guidelines. It guarantees complete traceability of production right down to the raw material. Also ISO 13485 and 15378 are proposed for new developments, as well as the completion of the necessary DMF. A cleanroom is available (particle limit value according to clean room class 8, ISO 14644) to produce under controlled atmospheric conditions.