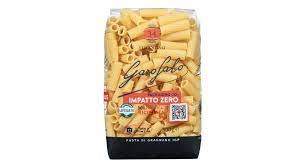
Italian pasta manufacturer Garofalo introduced a novel new package with a film made by GT Polifilm and Polivouga that uses certified circular polypropylene (PP) from SABIC, part of its TRUCIRCLE program to accelerate a circular plastic economy. The sustainable material is derived from advanced recycling and converted into a biaxially oriented polypropylene (BOPP) film for this application, which is the first mono-PP pasta packaging material in the market containing 30% of post-consumer recycled (PCR) content. Garofalo introduced the first pasta bags made from the new packaging to Italian stores in March 2023.
“At Garofalo, we are fully committed to the quality and environmental compatibility of our products. Of course, this innovative new recycled pasta packaging is just one example of our sustainable initiatives, but marks an important step forward. It shows how food manufacturers and packaging suppliers are working together to bring about much needed change. As a packaging product that is both made with recycled content and fully recyclable, it also meets with a better consumer appeal,” says Dr. Sergio De Gennaro, quality assurance manager, Pastificio Lucio Garofalo S.p.A.
The PCR content in the bags is based on post-consumer used plastics, which is turned into pyrolysis oil in an advanced recycling process. At SABIC, the pyoil is used in the production of new polymers with the same specifications as virgin plastics from conventional feedstock. Polivouga, a vertically integrated Portuguese manufacturer of flexible films for packaging products uses a SABIC PP 525PC grade from SABIC’s TRUCIRCLE portfolio of certified circular polymers to produce the basic BOPP film for the new pasta packaging solution. GT Polifilm, a specialist in the production of flexible polypropylene products for automated packaging in the food industry, adds a cast PP film to the BOPP film to create a mono-material structure, which is then converted to tailor-made pasta bags. Once used, the mono-PP bags can easily be recycled again in existing PP waste streams.
“For such solutions to work in the long-term, the partners in the material value chain must closely collaborate,” Abdullah Al-Otaibi, general manager, ETP & Market Solutions, SABIC says. “With our TRUCIRCLE program, we are pushing for innovative business models to transform our industry from a linear to a circular one and help prevent the valuable material of end-of-life plastic applications from being wasted. Within a year, this remarkable joint project has shown what can be achieved to make this vision come true if all players work together to maximize post-consumer plastic recycling and sustainability.”
SABIC’s circular materials are produced using a mass balance accounting scheme according to the International Sustainability & Carbon Certification (ISCC) PLUS program, which follows a set of predefined and transparent rules for tracking the material flow across complex supply chains from the feedstock to the final application.
While flexible plastic packaging is often the more sustainable alternative, a lot of food is packaged in paper/plastic combinations or laminates which are difficult to recycle and may have a bigger carbon footprint due to higher resource consumption. As a more responsible solution, flexible mono-material with PCR content is potentially the preferred packaging route for a growing number of brand owners and retailers, while it is also supported by EU authorities and NGOs.
“The development and manufacture of sustainable and economically viable packaging solutions to help reduce food and plastic waste is firmly rooted in our DNA. The incorporation of recycled content has been a key area of focus for us over the past few years,” Ragionier Talamo, Sole Director at GT Polifilm adds. “By supporting the circular economy, adding value to plastics and promoting their recycling into new packaging products, we hope to make a significant contribution to solving the enormous challenge of improving recycling rates and minimizing plastic waste.”
Tiago Barros, Executive Manager at Polivouga, comments: “As a producer of flexible films, we are well aware of our responsibilities in turning our own and our customers’ sustainability goals into reality, and we are very committed to the challenge. Our new BOPP product demonstrates the determined journey we have embarked on with SABIC. We welcome the advanced recycling route offered by SABIC as an opportunity to make a meaningful contribution to the circularity of plastics in BOPP films. In collaboration with strong global partners, this breakthrough project is demonstrating the feasibility of reusing plastic waste in safe food-grade packaging rather than losing its value to landfill or incineration.”
SABIC’s certified circular polymers are only part of its TRUCIRCLE portfolio and services for circular solutions. The program also includes design for recyclability, mechanically recycled products, certified renewable polymers from bio-based feedstock and closed loop initiatives to recycle plastic back into high quality applications and help prevent valuable used plastics from becoming waste.