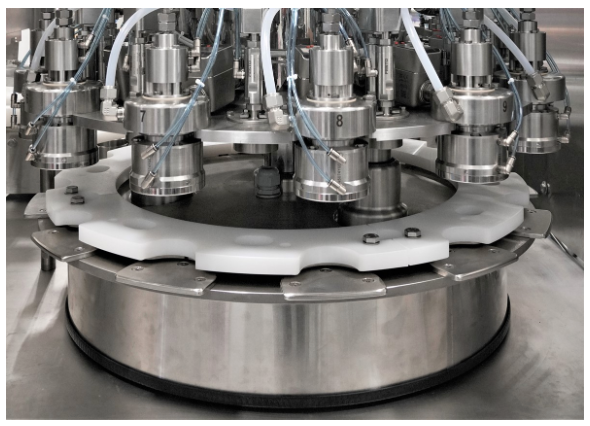
Pneumatic Scale Angelus (PSA), one of several Barry-Wehmiller companies represented in BW Packaging Systems, will introduce its new CB100C rotary counter-pressure filler at the Craft Brewers Conference, Minneapolis. Building upon the capabilities of PSA’s CB50C counter-pressure canning line, the CB100C leverages a 12-head rotary filling turret design, coupled with a dual-station seamer, to allow craft beverage producers to increase their throughput to more than 100 cans per minute. This will be the fifth consecutive innovation that PSA has debuted at the Craft Brewers Conference.
“Our CB100C system uses the same isobarometric filling principles as our CB50C system,” said Mike Davis, Global Can Filling Product Line Leader for PSA. “But, the addition of the 12-head rotary filling turret also means that we’re able to move more cans smoothly through the line without creating any increase in product agitation as filling speeds increase. Ultimately, this allows us to eliminate unwanted reductions in carbonation levels seen with other filling methods.”
Counter-pressure technology allows craft beverage producers to fill highly carbonated beverages, in excess of 2.7 volumes of CO2. In isobarometric filling, they can be filled and the product going into the can are at equal pressure, maintaining carbonation solubility throughout the filling process.
Since PSA introduced the CB50C system, the machine has seen great success, confirming an anticipated need for counter-pressure technology, based on increasing consumer demand for carbonated beverages. Leading into the CB100C’s launch, PSA is already seeing strong demand for its rotary version.
"Our counter-pressure design has been well-received by the craft beverage community,” said Adam Brandt, Vice President of Sales for PSA. “Not only does it allow brewers to expand their portfolios, but it also offers them better control and autonomy over their production parameters. With the addition of the CB100C, they can now more than double production volumes.”
The CB100C employs magnetic flowmeter technology to help brewers get a perfect fill with little waste, and an under-cover gas flush system keeps dissolved oxygen levels low. In addition, industry-leading double-seam technology keeps cans sealed tight, extending critical shelf life. The system is optimized for sleek and standard can bodies, and is designed with quick-change adjustments for easy changeovers accommodating various can heights and body diameters with no valve change required. A compact footprint and an intuitive HMI for individual fill-head volume adjustments simplify operation.