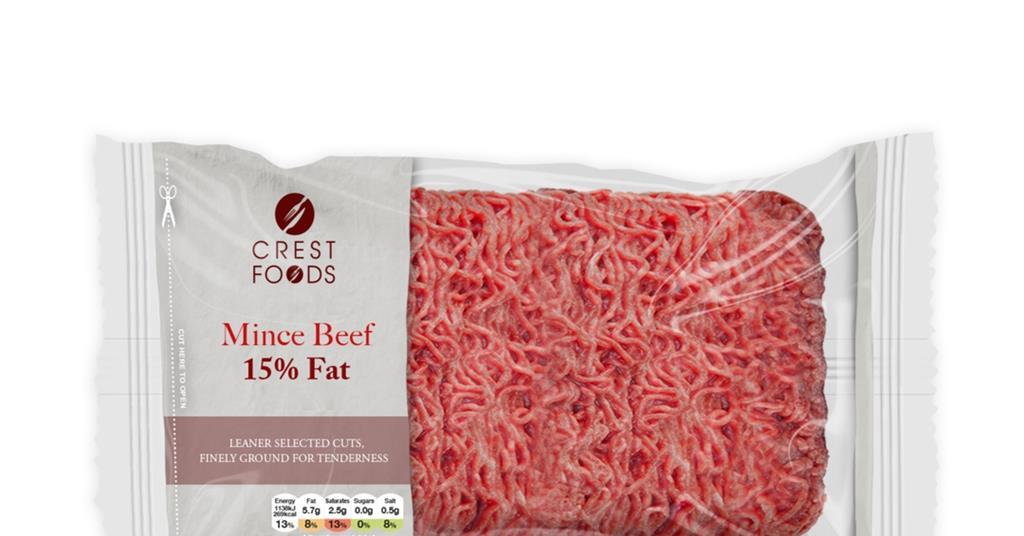
CRYOVAC brand recycle-ready PP-based laminates have a thickness of 52 microns and are fortified with an EVOH barrier. SEE said the combined performance delivers a ‘superior’ oxygen and moisture barrier to keep food fresh and extend shelf life, while using between 65% to 77% less plastic compared to traditional tray lidding and thermoforming options.
The new laminates comply with On-Pack Recycling Label (OPRL) guidelines and CEFLEX standards. They are certified as 90% recyclability by Cyclos and can be recycled in polypropylene (PP) streams.
Marta Lara, senior marketing manager, food retail, EMEA at SEE, commented, “Our aim was to create a high-barrier laminate packaging solution that is easily printable, while supporting food processors’ goals to improve sustainability and reduce costs. SEE analysis of market prices for other thermoforming and tray lidding options, compared to the CRYOVAC laminates shows the new recycle-ready solution can lower total packaging costs by 50% to 75%.”
CRYOVAC brand recycle-ready PP-based laminates are designed for horizontal fill form seal (HFFS), tray lidding and thermoforming applications. They are described as ‘ideal’ for packaging minced meat, fresh red meat, poultry, smoked and processed meats, dairy and cheeses. The laminates are available in both plain and printed formats and anti-fog and non-anti-fog versions.
“Optimising the presentation of foods through anti-fogging helps to engage consumers to boost sales and reduce the risk of wastage,” Marta added. “The laminates further support sustainability goals through a high barrier that reduces spoilage and extends shelf life, as well as the material’s recyclability.”
SEE added that non-shrinkable-film field tests of the CRYOVAC laminates with customers on high-speed HFFS systems recorded packaging speeds of up to 120 packs per minute (ppm) and sealing temperatures up 185°C. Tests of shrinkable film applications showed packaging speeds of up to 80ppm and sealing temperatures reaching 165°C.
Marta said, “Innovations in food packaging mean that food processors don’t have to choose between performance, cost savings and sustainability. Technology and expertise are constantly evolving to develop food packaging solutions that improve efficiencies, productivity, safety and quality, and circularity.”