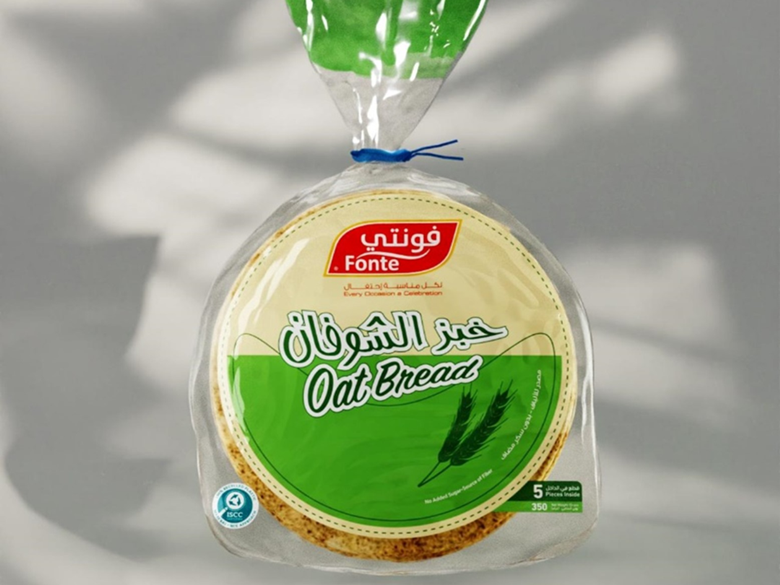
Used to package FONTE’s Oat Arabic Bread, the bags make use of two food-contact, certified circular polyethylene resin grades from SABIC’s TRUCIRCLE portfolio and are produced by Napco National, a vertically integrated manufacturer of flexible film and packaging products in Saudi Arabia.
Reportedly, the bags incorporate 100% mass-balanced certified content of recycled feedstock from mixed post-consumer plastic streams. These are converted into pyrolysis oil via advanced recycling, which SABIC then uses to produce new polymers that claim to offer the same purity and quality as conventional virgin plastics.
The move marks the first circular packaging project in Saudi Arabia as part of SABIC’s TRUCIRCLE programme, which aims to accelerate the implementation of a circular economy for plastics.
SABIC highlights that its circular materials are produced using mass balance accounting in line with the ‘predefined and transparent rules’ of the ISCC PLUS programme – ensuring that the material flow is tracked throughout complex supply chains.
Sanjay Mishra, who heads the ETP and Performance Polymers business at SABIC, explains: “With our TRUCIRCLE program, we are pushing for innovative business models to transform our industry from a linear to a circular one and help prevent the valuable material of end-of-life plastic applications from being wasted.
“Within a relatively short time, this remarkable joint project has shown what can be achieved to make this vision come true if all players work together to maximize post-consumer plastic recycling and sustainability.
“Moreover, the project also addresses a major trend towards more sustainable food packaging in Saudi Arabia, and is the first circular packaging application of its kind in the country.”
“At Masdar, our strategic focus extends across the entire spectrum of Fast-Moving Consumer Goods (FMCG),” continues Mohammed Binmahfoodh, CEO at Masdar Alhayat for Food Industries. “Our mission to integrate quality and sustainability into every aspect of our operations aligns seamlessly with Vision 2030.
“As Masdar’s leading brand, FONTE is fully committed to addressing the plastic challenge that all food producers are facing. While this new bread bag is just one of our products, it demonstrates how important value chain players can work together to bring about much-needed change.
“As the availability of high-quality recycled plastics in KSA is increasing, we look forward to transferring the success of this partnership project with SABIC and Napco as a role model to further packaging applications in our ‘Saudi Made’ food products offering.”
Chadi Radi, senior director at Napco National, adds: “Napco is firmly dedicated to the advancement of sustainable packaging across various sectors in the plastic industry within the Kingdom of Saudi Arabia and throughout the Gulf region. We understand the pressing need to address environmental challenges and are committed to supporting our customers in achieving their sustainability objectives.
“Through our innovative approach, we strive to develop packaging solutions that minimize environmental impact, promote circularity and maximize the value of the plastic life cycle.
“At Napco National, we welcome the advanced recycling route offered by SABIC as an opportunity to contribute to the circularity of plastics in flexible packaging films. This collaboration has led to a successful implementation of circular plastic film in the food sector.”
Alongside certified circular polymers, the TRUCIRCLE portfolio comprises of design for recyclability, mechanically recycled products, certified renewable polymers from biobased feedstocks, and closed-loop initiatives intended to prevent valuable plastics from becoming waste by recycling them back into high-quality applications.
A previous collaboration saw Estiko Packaging Solutions create a multi-layer film from a random polymer grade of SABIC’s PP QRYSTAL copolymer and create and ISCC PLUS certified pouch – said to contain 60% otherwise ‘ocean-bound’ plastic – to Coldwater Prawns of Norway’s frozen prawns.
More recently, SABIC has partnered with Pashupati Group to convert plastic waste into pyrolysis oil for use as feedstock in the production of SABIC’s certified circular polymers; and its work with BASF and Linde has resulted in a demonstration plant said to heat its large-scale steam cracking furnaces with renewable electricity.
Meanwhile, UK retailer Morrisons reported last year that its lightweighting efforts had removed 110 tonnes of plastic from its bread bags thus far, alongside other developments.