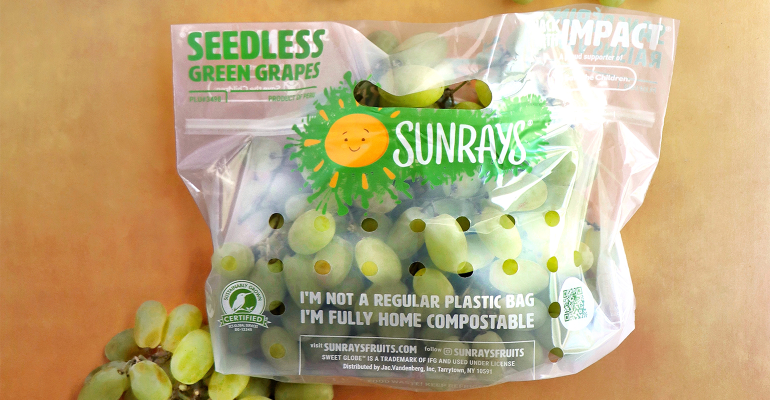
Tipa, an Israel-based supplier of compostable plastic flexible materials, has partnered with US packaging manufacturers PPC Flexible Packaging and Clearview Packaging to expand production of compostable packaging in the US.
The two packaging producers are using Tipa’s compostable films and laminates, which are circular packaging materials that incorporate biomass and leave no waste after composting.
PPC Flexible Packaging, headquartered in Buffalo Grove, IL, uses Tipa’s compostable laminates to manufacture pouches for products such as baked goods, dry foods, dietary supplements, and vitamins.
Clearview Packaging, based in Albany, NY, uses compostable films from Tipa to manufacture open bags, wicketed bags, resealable bags, and zipper bags. End-use applications include apparel, accessories, fresh produce, baked goods, and frozen food.
Drop-in compostable packaging solutions.
The compostable films and laminates “are compatible with all existing, standard machinery for plastic processing and packaging lines,” Daphna Nissenbaum, Tipa’s CEO and cofounder, tells us. “As plug-and-play solutions, they require no line adjustments for various segments of packaging, including food, fresh produce, fashion, and baked goods.”
She adds, “In practice, we provide our partners with raw materials — either resins or rolls of compostable plastic made from compostable polymers. Manufacturers like PPC and Clearview use these rolls to formulate fully customized, compostable packaging for their respective clients.”
In addition to reducing plastic waste, the business model enables the US packaging manufacturers to produce compostable packaging locally, reducing shipping-related greenhouse gas emissions.
Converting line speeds for the compostable films and laminates are the same as for conventional flexible materials.
According to Tipa, the compostable materials exhibit durability, printability, and transparency akin to that of conventional plastics, but with the benefit of sustainable end of life. In a home or industrial composter, the materials degrade into nutrient-rich soil within a few months, the company claims.
The co-extruded compostable Tipa films that Clearview is using for production of compostable packaging are suitable for food packaging and are certified as home compostable through OK Compost Home.
The Tipa materials that PPC chose exhibit good-to-excellent oxygen and moisture barrier and excellent sealing properties. These materials — a high-transparency barrier laminate and a high-barrier metallized laminate — are certified for compliance with European Union EN13432, Australian AS4736, and ASTM D6400 industrial composting standards.
Compostable fossil/bio-polymer blends.
Tipa’s compostable materials are made from proprietary blends of fossil- and bio-based polymers, “both of which are fully compostable and emulate the functionalities of conventional plastic,” Nissenbaum says. (Some fossil-based polymers, like polybutylene adipate terephthalate (PBAT), are compostable.)
The biomass for Tipa’s compostable materials comes from sources such as corn, sugarcane, and wood pulp. All its products are free of genetically modified organisms (GMOs), nontoxic, and compliant with international health/safety standards.
“Our products are all fully compostable and are between 20% [and] 80% bio-based,” Nissenbaum says. “The remaining percentage is made of fully compostable fossil-based polymers, as they are the only polymers currently on the market that meet certain properties for high-end food packaging. It’s important to note that not all bio-based polymers are compostable.”
Ultimately, she explains, all of Tipa’s products decompose and biodegrade into “fertile topsoil when disposed of in in-home or industrial composters, due to their ability to disintegrate into small renewable pieces that are naturally and safely ingested by microorganisms.”
Compostable packaging costs and benefits.
Tipa has not disclosed the cost differential between its compostable materials and petrochemical-based alternatives. But compostable products are generally pricier “because the ingredients are less readily available and therefore more expensive,” Nissenbaum says. “The raw materials used to make traditional flexible plastic are less costly, which is the main reason why conventional plastic is so ubiquitous.”
“Nonetheless, our customers and partners understand that the cost of sustainable business is worth it for the benefit of the environment: 400 million metric tons of plastic [are] produced every year — and 79% ends up in landfills,” she concludes.