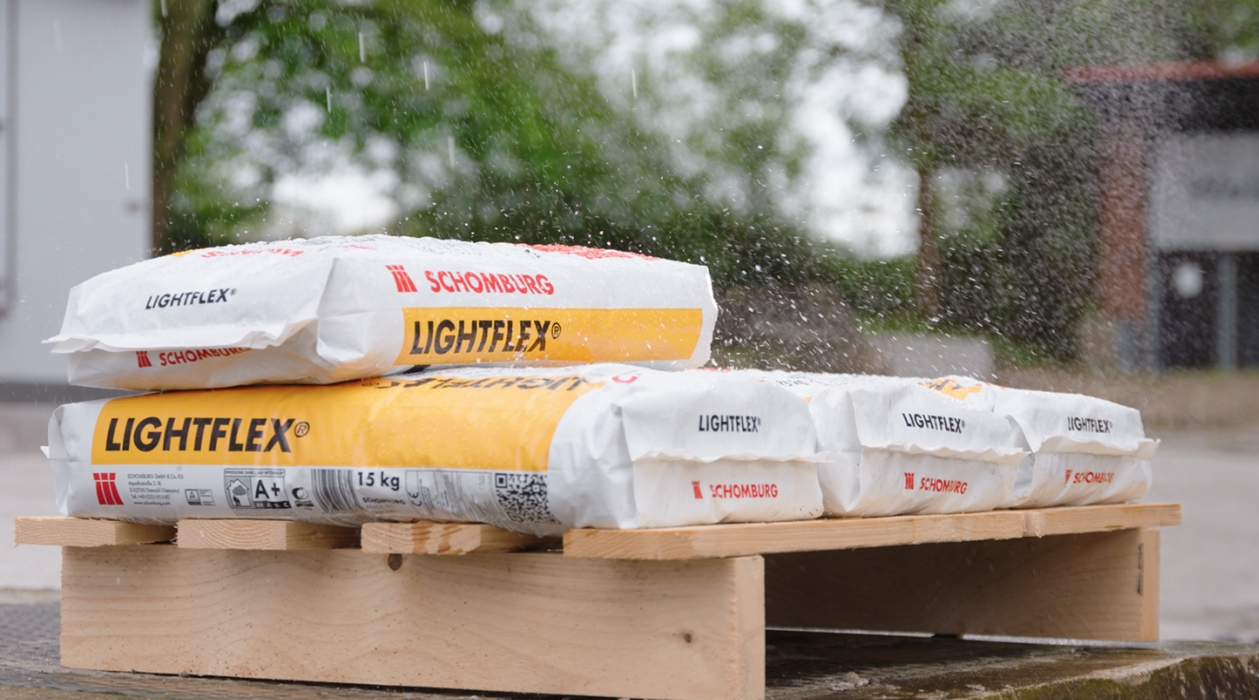
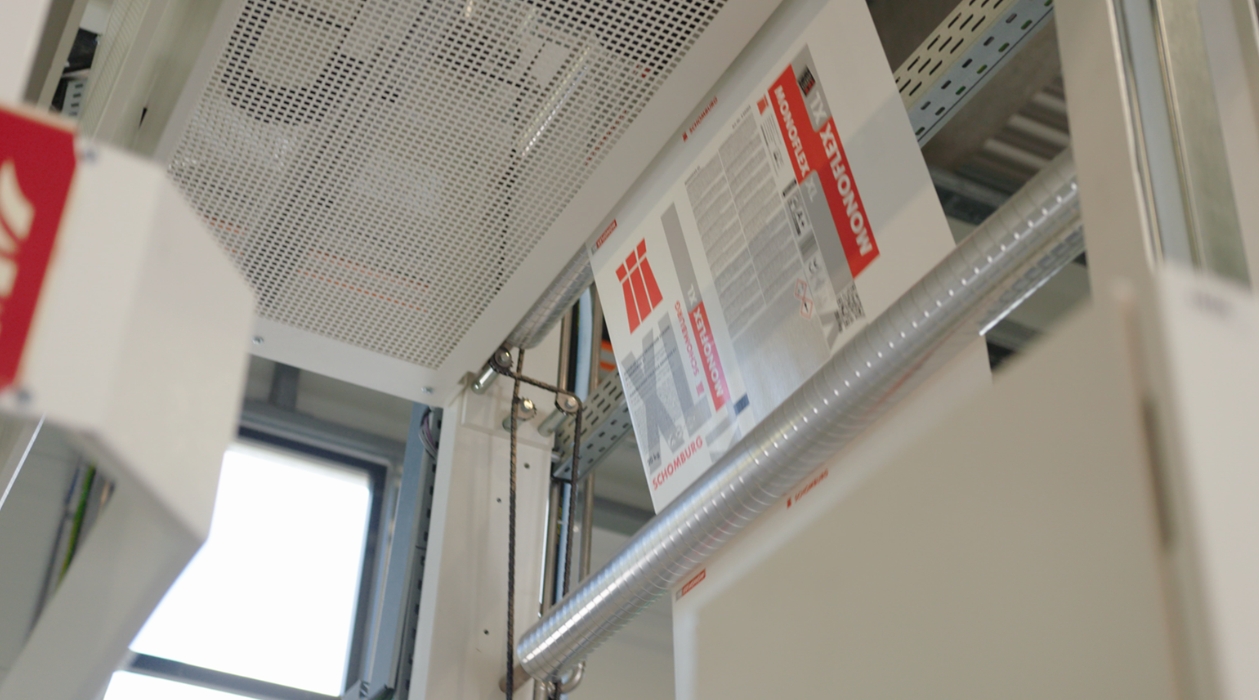
Berry Global is helping Schomburg, one of Germany’s leading construction chemicals manufacturers, meet its sustainable packaging goals by developing a high-performance ventilated PE bag solution that contains 50% post-consumer recycled plastic content (PCR).
Schomburg has moved its construction chemicals powder products from paper packaging sacks to a bespoke version of Berry’s ventilated NorDiVent® film bags as part of the company’s objectives to reduce product losses and lower its carbon footprint. The NorDiVent film meets Schomburg’s needs by offering water-resistance to protect the pack contents, pack recyclability, and the inclusion of recycled plastic resulting in a reduction in the use of virgin materials.
Since making the switch, Schomburg has seen a reduction in product losses compared to its previous packaging. At the same time Berry has downgauged the Schomburg NorDiVent bags by 7.14% while also incorporating 50% post-consumer recycled (PCR) plastic, with no compromise on the bags’ performance. The result is a reduction of approximately 39%. Global Warming Potential (GWP).
“Sustainability is fundamental to all our operations, but this must be aligned with maintaining the excellent performance of our products as part of our commitment to sustainable added value,” explained Niels Theis of Schomburg.
“Our successful partnership with Berry has delivered extremely positive results and demonstrates what can be achieved when companies work together towards a series of common goals.”
NorDiVent features a durable and waterproof construction which ensures that air is let out in a dust-free manner. This provides effective moisture protection for products that need to be kept dry and enables sacks to be stored outdoors. The film’s high tear resistance offers further product protection and helps avoids spillages and product waste throughout the supply chain. The quality of the film also allows printing in up to eight colours to create impactful branding and maximise on-shelf presence.
As part of Berry’s B Circular initiative, PCR plastic can be incorporated into the NorDiVent film, currently achieving levels of up to 50% which Berry can adapt to meet specific customer and application requirements.
“The solution we have devised for Schomburg demonstrates our technical skills in the design and manufacture of products that support both our own and our customers’ sustainability objectives, while maintaining the highest levels of quality and reliability,” said Frank Heseding, Sales Director for Berry Global’s Flexible Films Division.
“It underlines our belief that we can achieve sustainability through innovation and when all areas of the supply chain are aligned.”
*The Global Warming Potential (GWP) savings presented are based on comparisons between the materials used in our NorDiVent FFS film with 50% recycled plastic content and NorDiVent films made from 100% prime resins. All data used in these calculations are sourced from recent, peer-reviewed publications, primarily from the UK and EU, with references available upon request. The calculations are conservative, utilising ceiling values for the various polymers in the product’s bill of materials.