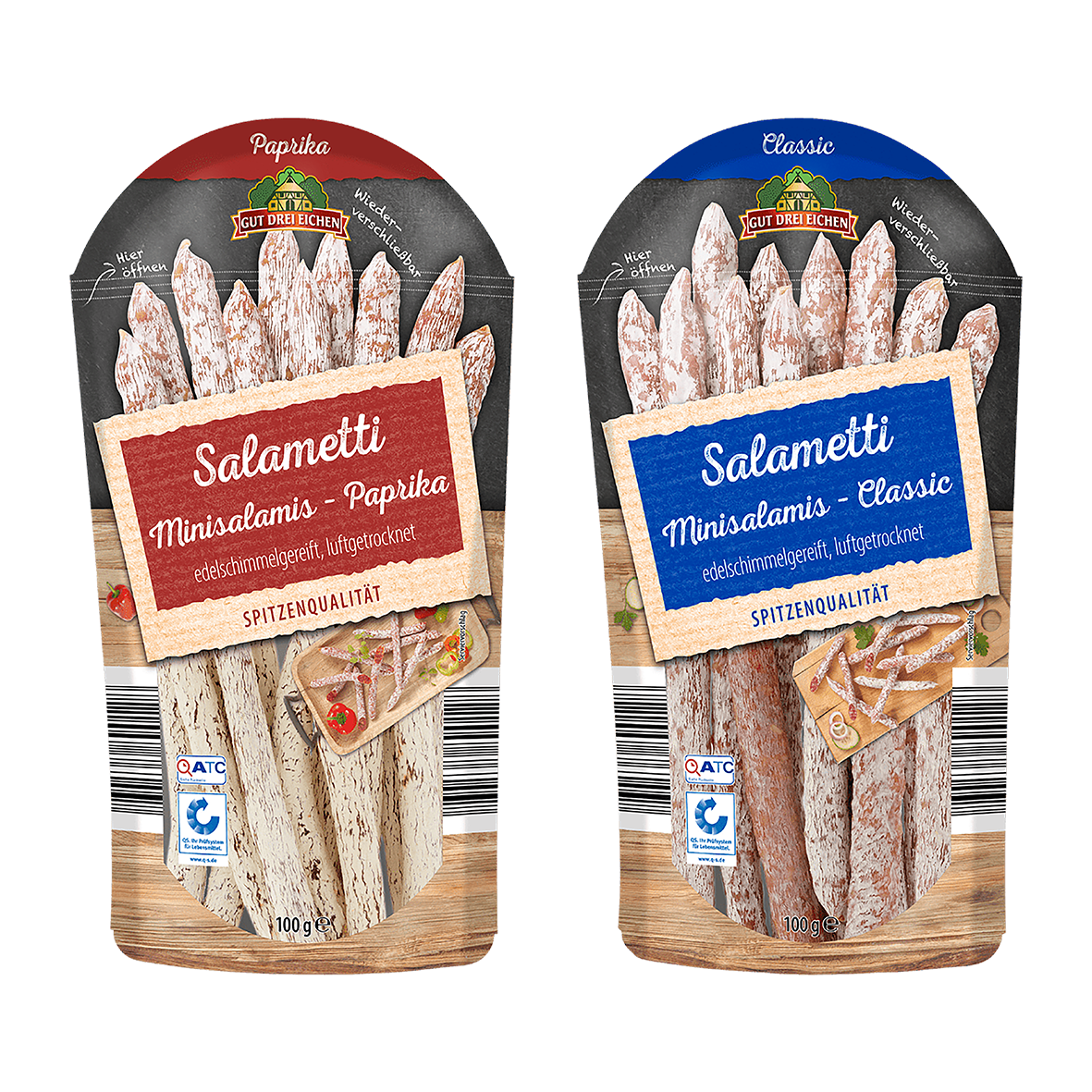
For a number of years, resealable doypacks have been a preferred packaging concept for nuts, sweet and savory snacks, as well as spices, coffee and tea – but the current barrier composites on the market are not very sustainable, due to their aluminum content. As a modern packaging alternative, SÜDPACK has now developed its first practical, PP-based doypack, which is material-efficient, entirely aluminum-free and above all recyclable. This innovative con-cept will be on display at this year’s FachPack on the SÜDPACK Stand 224 in Hall 7.
Doypacks are among the most common and flexible packaging concepts for dried sausages and meat, cheese snacks, coffee, tea, spices and sweets. But there is a growing awareness of sustainable alternatives, even in the case of these popular pouch packs with a practical zip.
SÜDPACK is about to launch an innovative packaging concept for this product area, namely its new mono-plastic solution. It is polypropylene-based and therefore supports the statutory demand for recyclable packaging – with the same functionality. “In addition to reducing the carbon footprint by substitut-ing aluminum, the principal goal of this development was also to optimize re-cyclability and improve material efficiency,” says Holger Hoss, Product Manager at SÜDPACK.
Outstanding material properties
The material is extremely rigid and offers all the properties that are necessary for the efficient and safe packaging of food in doypacks. Depending on the products to be packaged, the films can be equipped with different barrier properties. Based on what is needed, the pouches can be aroma proof and guarantee optimal protection against moisture, UV radiation or oxygen. By substituting the aluminum barrier with a coextruded barrier layer, the shelf life of salami sticks could be guaranteed for up to 70 days during a pilot project for the zur Mühlen Group, for example. Thanks to an integrated transparent panel, consumers have a clear view of the product with this packaging.
Another important aspect: reducing the film thickness by around ten percent achieved a weight saving of 26 percent compared to conventional packaging, resulting in a reduction in DSD fees.
Excellent machinability
These high-performance films also boast excellent machinability, which results in a high level of process and packaging reliability. “This wasn’t a foregone con-clusion,” says Holger Hoss. Because “Single-material solutions require much more sensitive processing and in most cases, the technical design of current machine peripherals isn’t suitable for such packaging materials.” Due to its wide transparent seal, however, SÜDPACK’s new material can mostly, or with only minor parameter adjustments, be used on existing doypack lines that are actually designed for processing aluminum composites.
At the same time, the structure of the sealing layer ensures the simple and efficient integration of resealing systems, such as zippers, based on polypro-pylene and polyethylene. These are already available on the market for flat pouches and doypacks. In short: SÜDPACK’s new high-performance film not only boasts outstanding density and sealing properties for both the folded base and zipper area, but is also completely sustainable.
Added value on all levels
This effect is further intensified when the packaging film is printed using SÜD-PACK’s new SPQ technology. The benefit: reduced ink and solvent consumption with significantly improved print quality. “The substitution of aluminum with our recyclable mono-material solution, combined with excellent material effi-ciency and sustainable printing technology, results in an overall improvement in the carbon footprint of every single doypack,” summarizes Holger Hoss. In light of the shortage of aluminum on the market, SÜDPACK customers also benefit from improved supply reliability – as well as an attractive, modern and extremely sustainable packaging concept that allows clear product differentia-tion at POS.
About SÜDPACK
SÜDPACK is a leading manufacturer of high-tech films and packaging materials for the food, non-food, and medical product industries. The solutions ensure maximum product protection as well as additional pioneering features with minimum material input.
The family business, which was founded by Alfred Remmele in 1964, is head-quartered in Ochsenhausen. The production sites in Germany, France, Poland, Switzerland, the Netherlands and the USA are equipped with the latest plant technology and manufacture to the highest standards, including the capacity to operate under clean room conditions. The global sales and service network ensures a high degree of proximity to the customer and comprehensive appli-cation technology support in more than 70 countries.
With its state-of-the-art Development and Application Center at its headquar-ters in Ochsenhausen, the innovation-oriented company offers its customers an optimal platform for carrying out application tests and for developing indi-vidual and tailor-made solutions.
SÜDPACK is committed to sustainable development and fulfills its responsibility as an employer and towards society, the environment, and its customers by developing packaging solutions that are unparalleled in their efficiency and sustainability.
www.suedpack.com