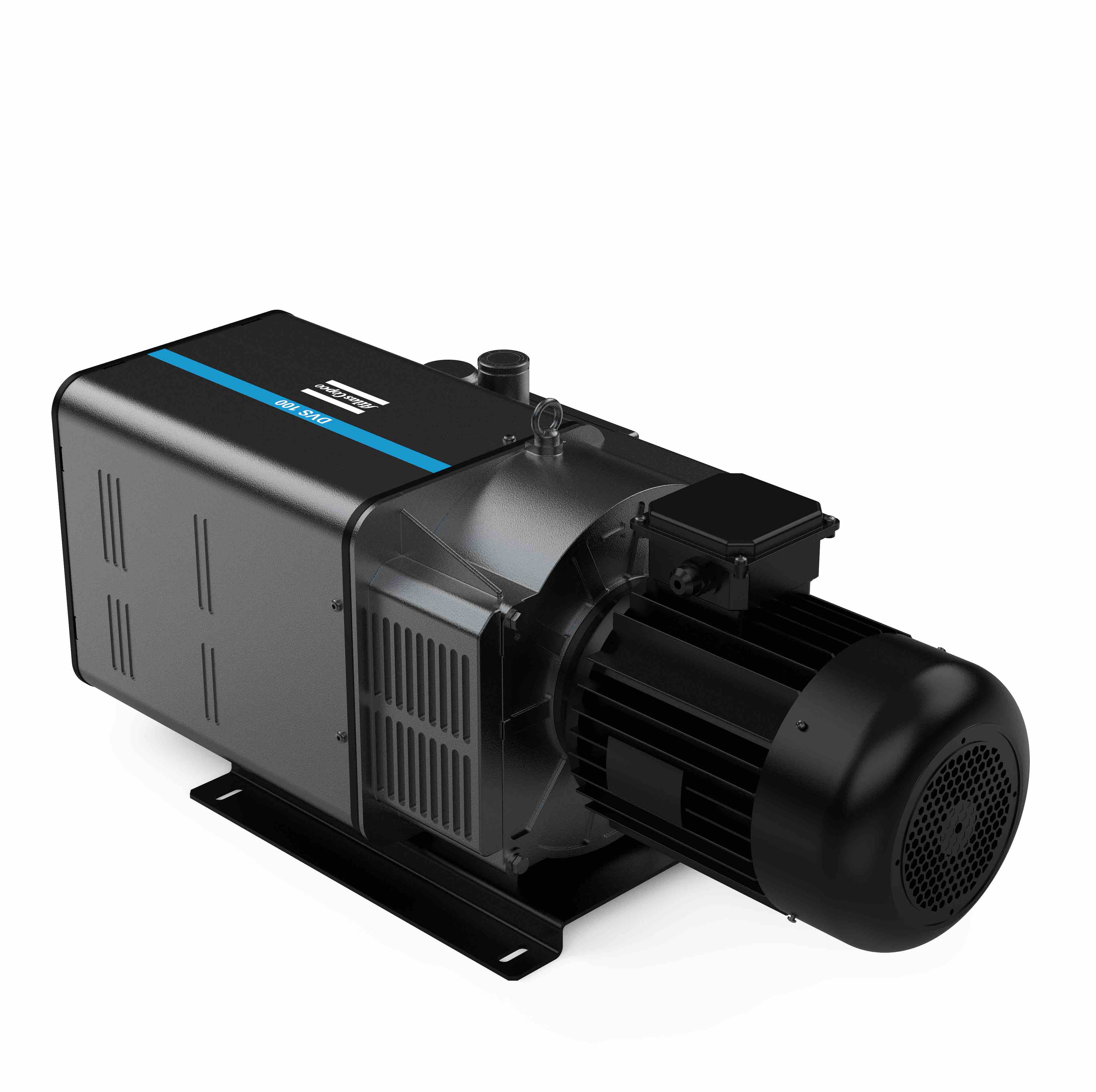
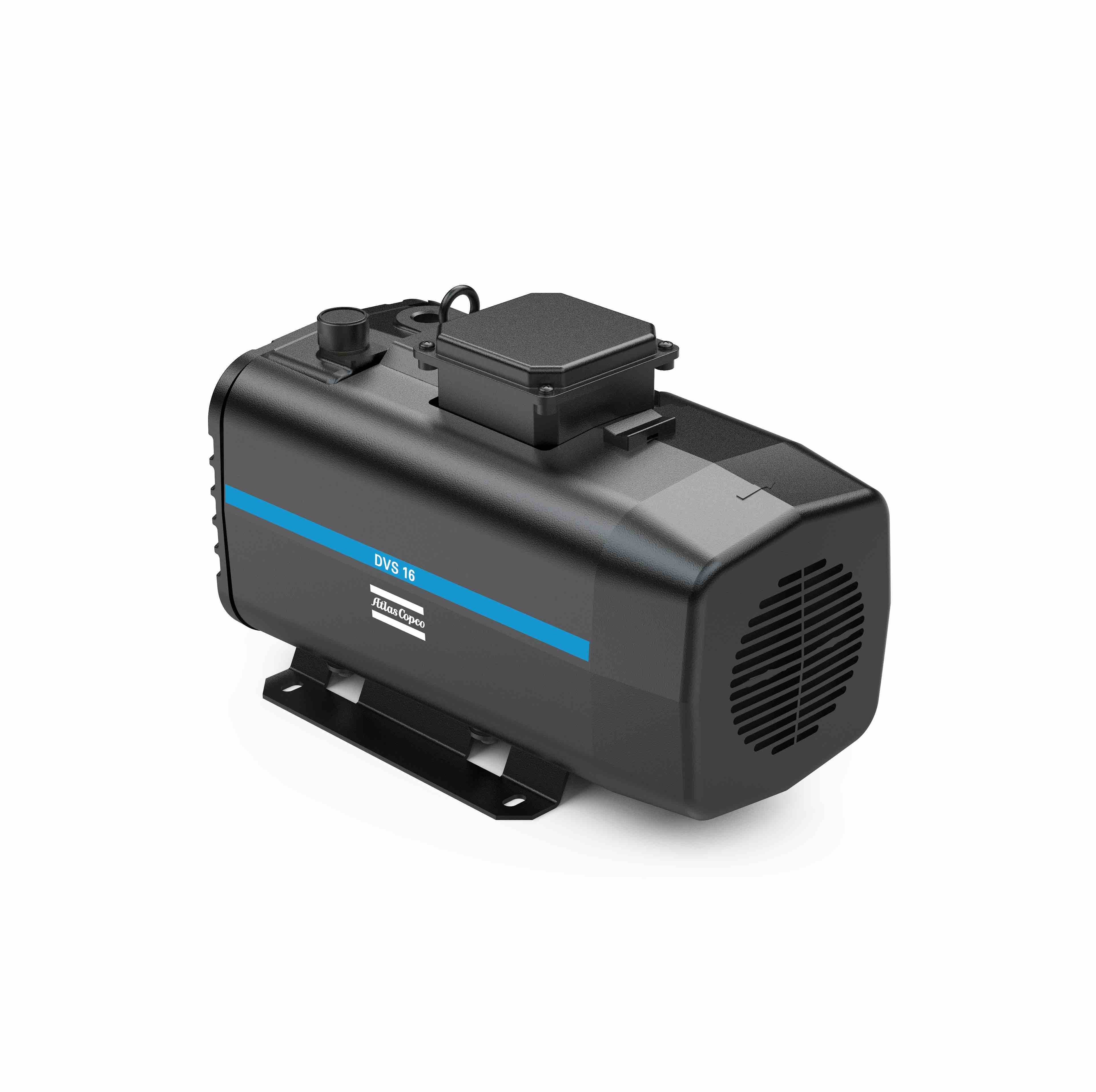
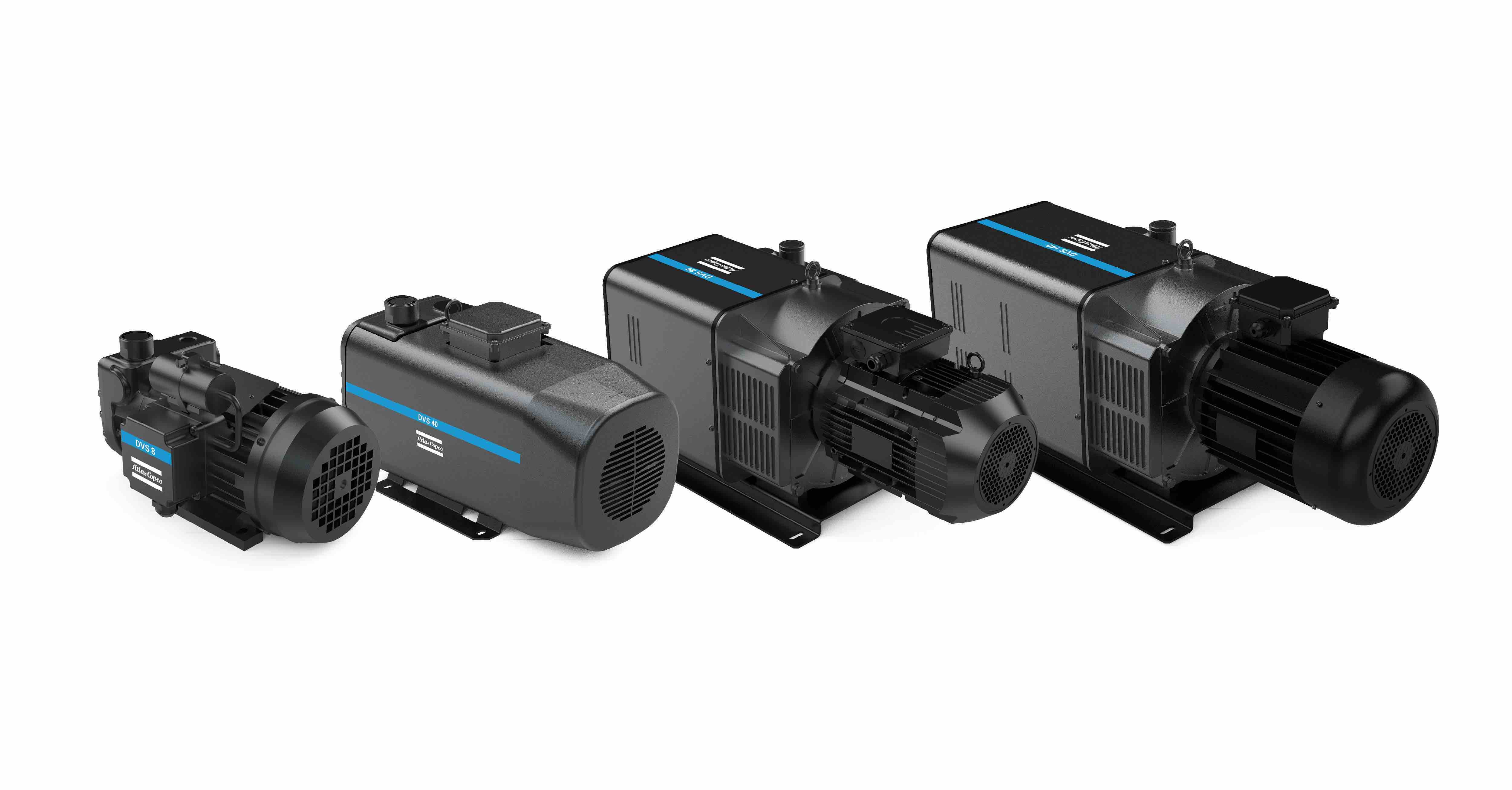
High efficiency, low wear and easy maintenance Köln, May 2023:
Nowadays, a modern vacuum technology must convince users in their everyday operations with features such as sustainability, performance and ergonomics. Atlas Copco has developed its new DVS vacuum pump series with a focus on this requirement profile. The result: the DVS models are oil-free, dry rotary vane pumps that guarantee emission-free, quiet operation and do not contaminate the processes.
High efficiency at competitive costs
"This makes them ideally suited for a wide range of applications, and they are used in packaging and pneumatic conveying processes, medical systems and analytical equipment, as well as in Pick and place for several automated industries" outlines Atlas Copco's product manager Carol Pignatelli. In these work processes, the dry rotary vane pumps offer their users specific advantages: The DVS models are quiet, low-wear and energy-saving and take up very little space. They are predestined for applications in which high efficiency must be achieved at competitive costs.
Proven functional principle, robust construction
This is achieved on the one hand by the proven functional principle of the rotary vane pump and on the other hand by the use of robust materials. For example, a rotor with graphite blades rotates inside the DVS pumps. The centrifugal forces press the vanes against the inside of the housing wall and hermetically seal the chamber for a safe, uninterrupted operating vacuum. "Thanks to the high-quality graphite alloy, the vacuum can be generated with minimal friction losses", explains Atlas Copco's product manager Carol Pignatelli
Air cooler manages temperature profile
The efficient pump mechanism and the design ensure minimal wear – and this in turn leads to long maintenance intervals and easy servicing of the DVS. In addition, the vacuum pumps are thus designed for maximum operating times. The temperature management also contributes to this: To reduce the temperature of the discharged air, the exhaust air is passed through an air cooler.
Interplay of proven components
The DVS series is also equipped with an inlet filter, non-return valve, exhaust silencer, a noise-containing canopy and an energy-efficient IE3 electric motor. The bottom line is that the interaction of these components forms the technological basis for a reliable pump with maximum vacuum performance and lower life cycle costs. The dry rotary vane vacuum pumps of the DVS series are available with a nominal suction volume flow of 5 m3 /h to 140 m3 /h and an ultimate vacuum of up to 120-150 mbar(a). "For higher flow rates, we recommend our dry claw vacuum pumps and systems of the DZS series", adds product manager Carol Pignatelli.
Important advantages of the DVS series at a glance
- The DVS series ensures clean, emission-free operation and no contamination of the process.
- Highly resistant graphite blades ensure durability, low wear and easy maintenance.
- Proven and reliable design principle
- DVS series is suitable for harsh industrial applications due to its low noise level and small footprint.
- Long service intervals, easy maintenance due to modular design and simple, efficient pump mechanism construction
- Air-cooled vacuum pumps with direct drive designed for oil-free vacuum operation
Atlas Copco Vacuum Technique
Great ideas accelerate innovation. At Atlas Copco Vacuum Technique we collaborate with our customers to turn industrial ideas into leading edge technology in vacuum and abatement solutions. Our passionate people, expertise and service bring sustainable value to industries everywhere. Atlas Copco is based in Stockholm, Sweden with customers in more than 180 countries and about 49 000 employees. Revenues of BSEK 141 in 2022.
At Atlas Copco Industrial Vacuum, we have revolutionized vacuum technology. Our state-of-the-art vacuum pumps and systems exemplify today’s connected and digitalized industry. Our teams of exceptional and passionate people engineer customer-centric vacuum solutions that offer better energy efficiency, consumer safety, improved productivity and a sustainable future. Our products are the invisible force that drive all industrial applications and manufacturing and our division includes the Atlas Copco, Edwards and Leybold brands. We are headquartered in Cologne, Germany with production centers in Germany, France, Belgium, Czech Republic, the United States and China