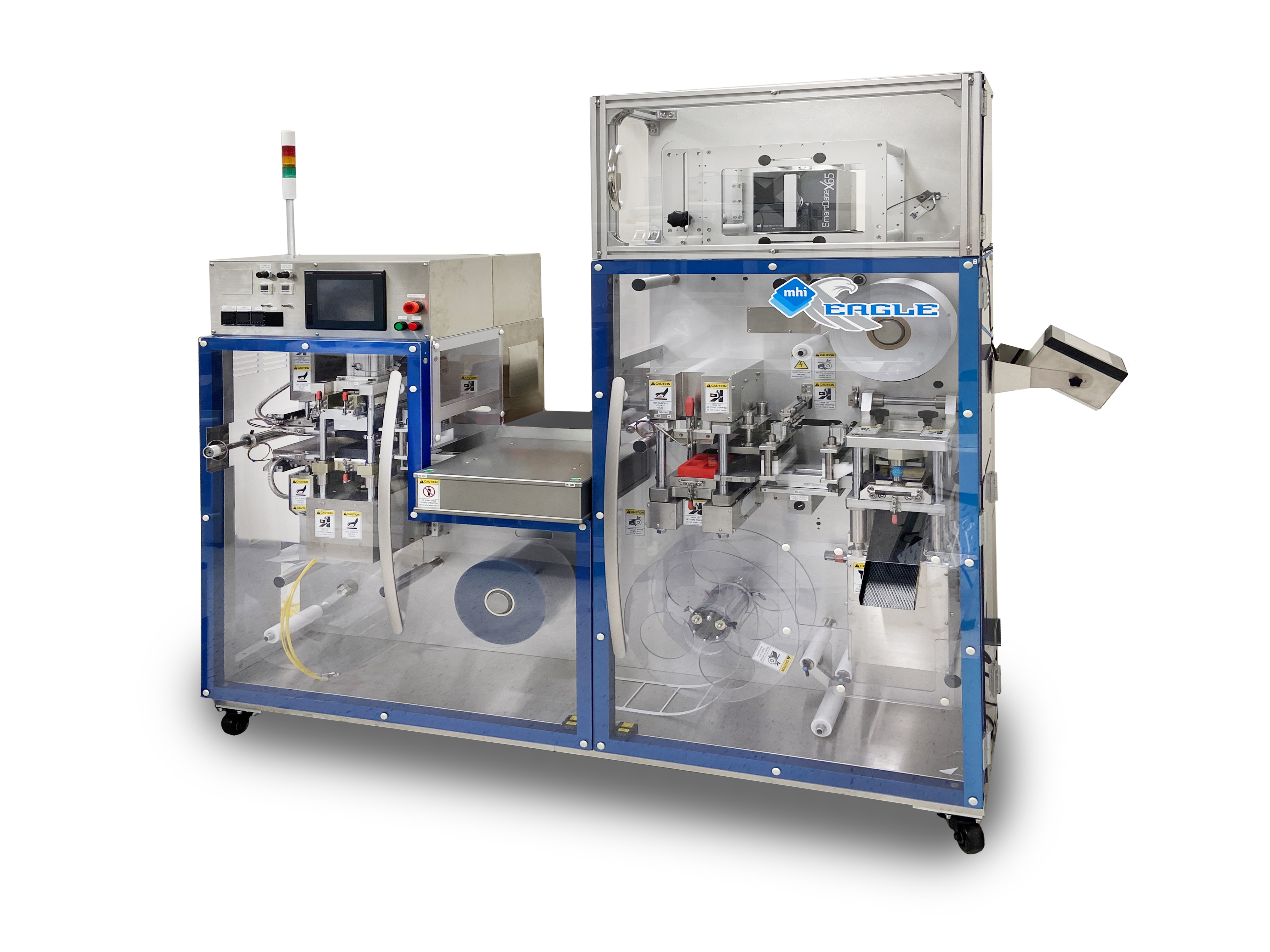
Versatile module ideal for packaging development,
rapid prototyping and small-scale production.
Norwell, MA –– Maruho Hatsujyo Innovations (MHI) – the U.S. subsidiary of Maruho Co. Ltd, a Japanese healthcare company with subsidiaries in Europe and the U.S. with global sales of $800 million – will showcase its EAGLE-Omni blister machine with an upgraded printer configuration at Pack Expo 2020, September 27-29 in Las Vegas. Ideal for packaging development, materials testing and production, the versatile unit performs forming, sealing and punching operations at sequential stations. MHI will be located at Booth SL-6738, in the Healthcare Packaging Expo section.
Measuring just over two meters in length and 1.6 meters tall, the reasonably compact EAGLE-Omni offers a format area of 150x95 mm, and a forming depth of 30mm (3cm) with an upgrade available to 40mm. The machine handles a wide range of forming materials – including PVC, PVDC, ACLAR, PP, PET and ALU – and all typical lidding substrates including ALU, paper, PVC, PET, and laminates. The EAGLE-Omni can produce up to 20 blisters per minute, and is suitable for packaging solids, powders, liquids or devices.
At Healthcare Packaging Expo, the thermoformer will be outfitted with an upgraded printing setup, whose attributes include a print area of 75X128mm. This allows you to cover the majority of your blister with pertinent information, such as lot codes, batch numbers, expiration dates and more.
The cost-effective, deep-draw EAGLE-Omni is capable of everything from manual prototyping to fully automated operation. The option of a 40mm forming depth makes it ideal for nutritional products larger than traditional tablets or capsules, such as gummies, devices and other delivery formats. The machine allows seamless development and production combined with rapid, low-cost prototyping, and features recipe-driven format change, easy changeover, and various feeding solutions.
Among the Eagle-OMNI’s differentiating benefits is the ease and expediency with which prototypes can be produced, thanks to the company’s recently launched 3D-printed blister tool prototyping capabilities.
“Combined with our cost-effective 3D-printed tool prototyping, the EAGLE-Omni allows new packages to be tested for barrier, stability, and durability quickly and at a fraction of the usual expense,” said Hideo Yonenaga, President of the MPM division for MHI. “Previously, lead times were measured in weeks or even months, and prototyping was often prohibitively expensive. The new 3D-printed tool prototyping allows us to expediently showcase the wide array of high-quality blisters that machines like the Eagle-OMNI can produce.”
About Maruho Hatsujyo Innovations
Maruho Hatsujyo Innovations (MHI), the U.S. subsidiary of Maruho Corp. Ltd., was created in 2014. MHI distributes the high quality medical packaging machinery produced by Maruho Hatsujyo Kogyo (MHK). With more than 220 employees, MHK has over 60 years of experience in the manufacturing sector, including the design of high-performance blister machinery and high-precision metal components. MHK is Japan’s second largest medical packaging machinery company.
For more information, visit www.mhi-innovations.com.