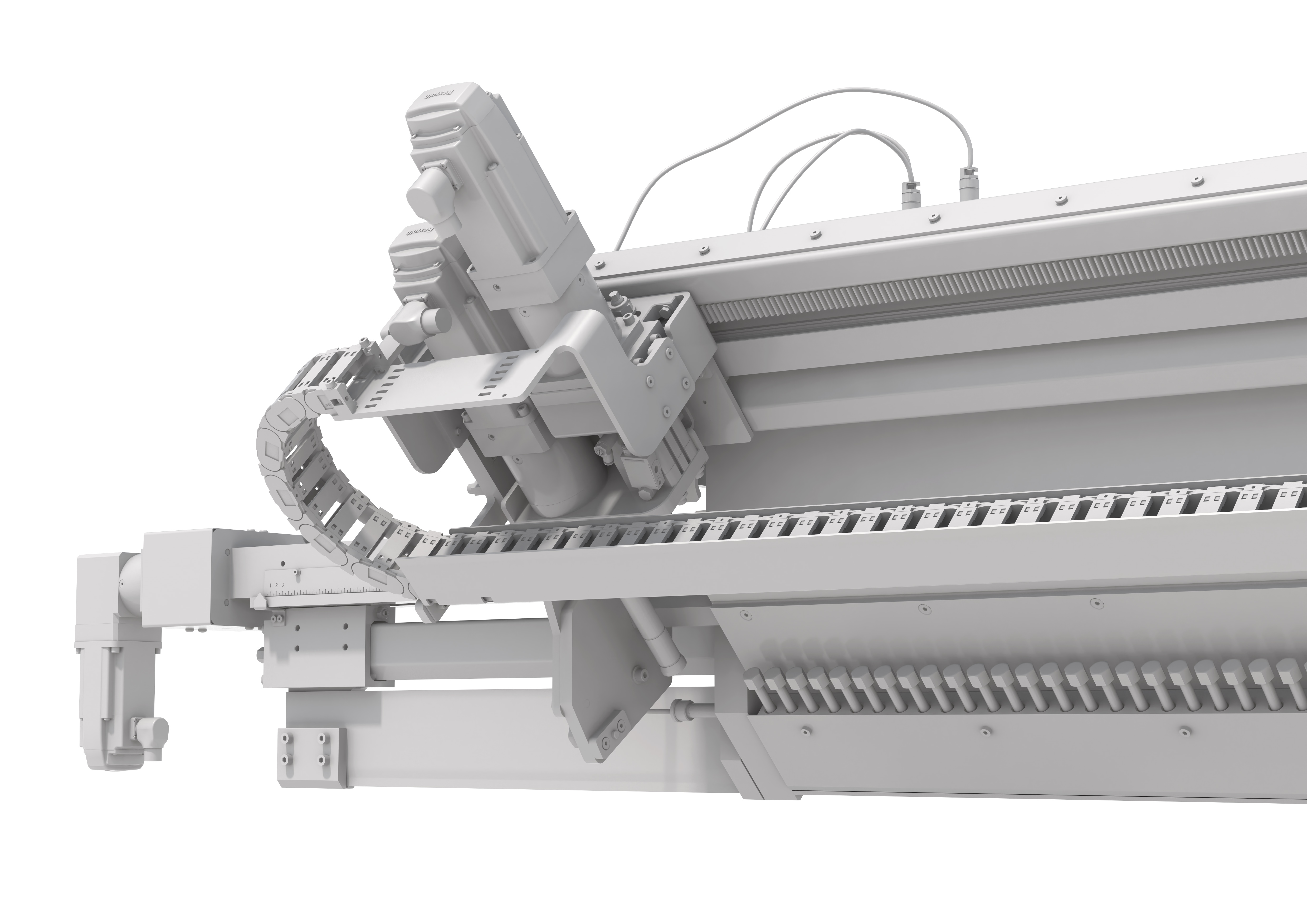
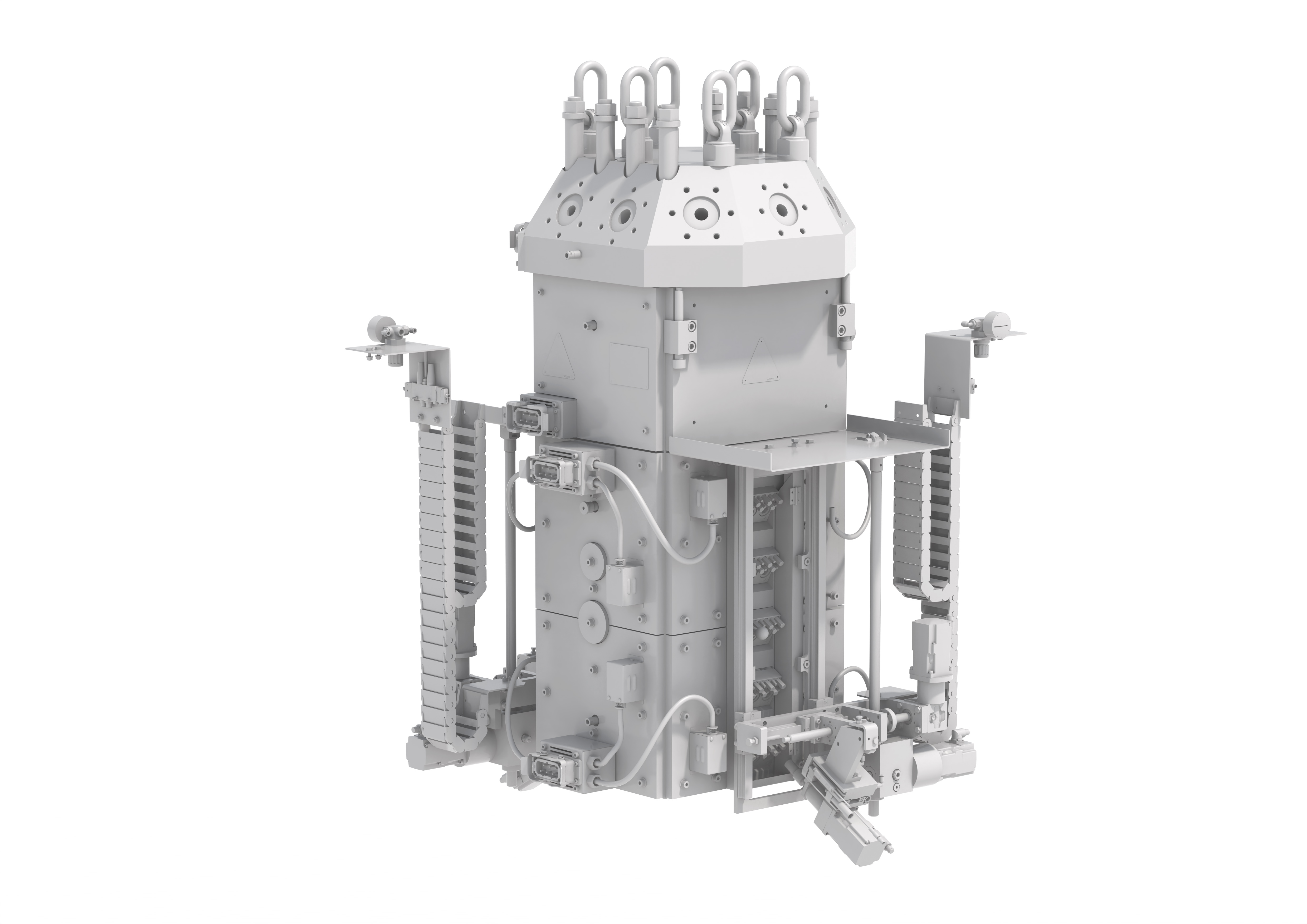
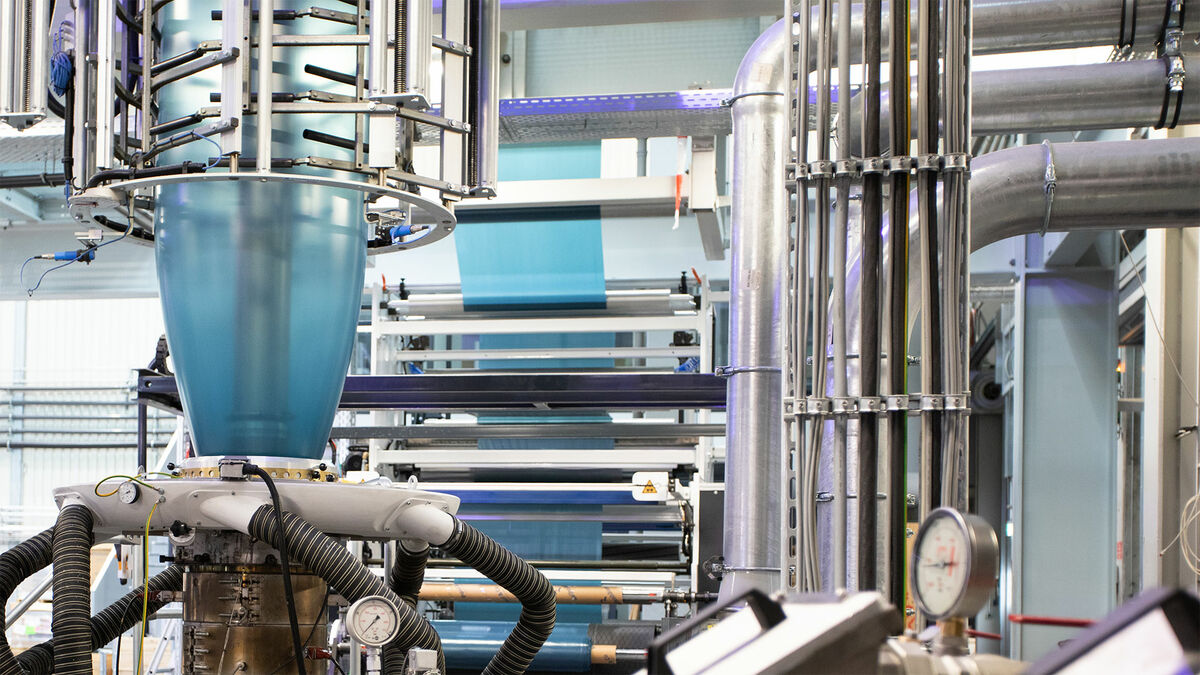
The Reifenhäuser Group will showcase its latest solutions for sustainable and efficient blown and flat film production at PLASTINDIA 2023 in New Delhi, India, from February 1 to 5. (Hall 4H-FP, Booth C D 20)
Highlights include the processing of low-quality recyclate into high-quality blown film, the PAM automation option for coextrusion adapters and flat dies, and the production of high-barrier tube film in just one process step. The machine manufacturer will be represented at India's leading plastics trade show by its Reifenhäuser Blown Film and Reifenhäuser Cast Sheet Coating business units, each specializing in blown film and flat film technologies.
EVO Fusion: safe processing of low recyclate grades Reifenhäuser Blown Film presents the technical solution to one of the biggest challenges in processing recyclate - the often low and fluctuating quality of the input material. Producers have so far found it difficult to set up a stable production process for higher-quality end products made from recyclate. With EVO Fusion, blown film producers can now process previously unusable, low-cost recyclate into high-performance blown films for end-use applications such as trash bags or mailing bags.
The key lies in the twin-screw technology of the EVO Fusion extruder, which improves melt homogeneity and ensures a stable process. Processors can also degas the system very easily and effectively, removing unwanted. components in the recyclate. The EVO Fusion process also enables direct extrusion, which eliminates the need for energy- and cost-intensive regranulation of the material. This means that fluff (film shreds), all types of production waste, and PCR material can also be processed directly. To process better quality regranulate, Reifenhäuser recommends the EVO Ultra single-screw extruder. This machine processes recycled material as reliably as other raw materials, thanks to optimized barrier as well as shear and mixing parts.
Eugen Friedel, Director Sales at Reifenhäuser Blown Film, explains: "Our technologies for recyclate processing offer the ideal prerequisite for participating on the growing market for products with high recyclate content. Moreover, India already has legal requirements governing the use of recyclate which our customers can easily meet thanks to EVO Fusion."
PAM option: automated adjustment of coextrusion adapter and die Precise, autonomous, mechatronic - with the PAM option, Reifenhäuser Cast Sheet Coating will demonstrate at PLASTINDIA how flat film producers can fully automate the adjustment of coextrusion adapter and die. In the past, this was mostly done manually. This enables faster start-up of production, higher output, and improved overall equipment efficiency (OEE). Scrap and material usage are significantly reduced. Once recipes have been set, they can be stored and recalled at any time. They can therefore be reproduced exactly - even by inexperienced line operators.
At the heart of the PAM system are motorized screwdrivers which profile the film layers on the coextrusion adapter automatically with high precision and set and control the die flex lip. Depending on the die design, it is also possible to adjust the dust bar, width, and lip opening automatically by adjusting the lower die lip. The PAM option is exclusively available for the Reifenhäuser Coextrusion Adapter Pro, the only coextrusion system on the market that allows profiling of individual layers while the line is running. For flat dies, PAM is available as an optional feature for Reifenhäuser dies and also as a retrofit option for third-party systems.
Benjamin Pott, Sales Manager at Reifenhäuser Cast Sheet Coating, explains, "The PAM option is a unique solution on the market to enable producers to achieve enormous increases in line efficiency. It can be selected independently for coextrusion adapters and dies - but in combination, the automated components develop their full potential." The Reifenhäuser Group, one of the few machine builders on the market, manufactures all hot parts in-house - extruder, coextrusion system, and die. With this hot part competence, Reifenhäuser can design all process-related interfaces to match each other perfectly - PAM takes the whole thing to a new level.
High-barrier film for tubes in only one process step At PLASTINDIA, the Cast Sheet Coating business unit will introduce a sustainable production process for PE-rich recyclable high-barrier film for tubes. These types of film are mainly used in oral or beauty care products. In the past this required several lamination and conversion steps upstream of the tube manufacturing process.
The new Reifenhäuser single step flat film coextrusion process simplifies production and increases productivity by outputs up to 80% higher than other technologies. The process also offers significant cost savings by reducing EVOH layer thickness by up to 30% while maintaining the necessary barrier properties. The properties of the film ensure seamless integration into established processing methods and thus a short time to market
About the Reifenhäuser Group
The Reifenhäuser Group is the leading provider of innovative technologies and components for plastics extrusion. Founded in 1911, the company supplies high-technology solutions all over the world. With its technologies and the know-how of its 1,750 employees, Reifenhäuser has the world's largest network of expertise in plastics extrusion technologies. The CEO of the Group is Bernd Reifenhäuser.