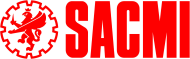
The 33rd edition of IranPET, the international symposium aimed at local and international operators in the industry, will soon be showcasing developments in IPS technology, since 2015 available in versions with up to 128 cavities and equipped with important new design features.
The latest developments in preform manufacturing injection technology will be the subject of a presentation by Sacmi at IranPET, the international symposium (the 33rd edition of which will be held this coming 11 - 12 April in Tehran) aimed at local and international operators in the PET manufacturing sector.
The focus of an ambitious medium-term investment plan, Sacmi’s technology for this industry hinges on the IPS (preform injection moulding) system, the preform production platform featuring injection technology: since 2015 this has also been available in 96 and 128-cavity (IPS 400) versions, providing manufacturers with higher PET quality, more efficient process automation and greater energy savings.
This Sacmi talk - to be given by Moraldo Masi, Business & Sales Manager of the Group’s Beverage Division – is scheduled for 3 p.m. on Monday, 11th April. This 33rd edition of the symposium takes place against the dynamic backdrop of both the country’s recent opening up to international investment and, in the PET sector, growing demand for solutions that combine high cap and container quality with cutting-edge innovations that let manufacturers make thinner, higher-performing packs and plastic caps in order to minimise environmental impact and operating costs.
One of only a handful of global players capable of leading the way in various technologies and industries, Sacmi is looking forward to presenting - alongside the popular CCM cap manufacturing series that uses compression technology - the latest developments on the IPS series. The latter offer, in addition to the proven advantages of the previous series (IPS 220), major design innovations such as preform unloading without the use of conveyors.
This talk by Sacmi (one of the international symposium’s sponsors) will have a strong focus on the technical specifications and advantages of the new platform, which has a pressing force of 400 tons and provides highly competitive cycle times (for example, the soundness of the technical solutions on the machine is clearly demonstrated by a lock-to-lock time of just 2.1 seconds). The concept of flexibility has undergone further development on the IPS400 too, although here the solutions aim for compatibility with the bulk of the moulds on the market rather than on size changeover speeds, which nevertheless remain on a par with the best the market has to offer.
Completing the picture is the excellent energy efficiency which, thanks also to the KERS energy recovery system on the post-cooler linear motor, means a consumption of just 0.2 kW/kg at maximum output rates (1220 kg/h).