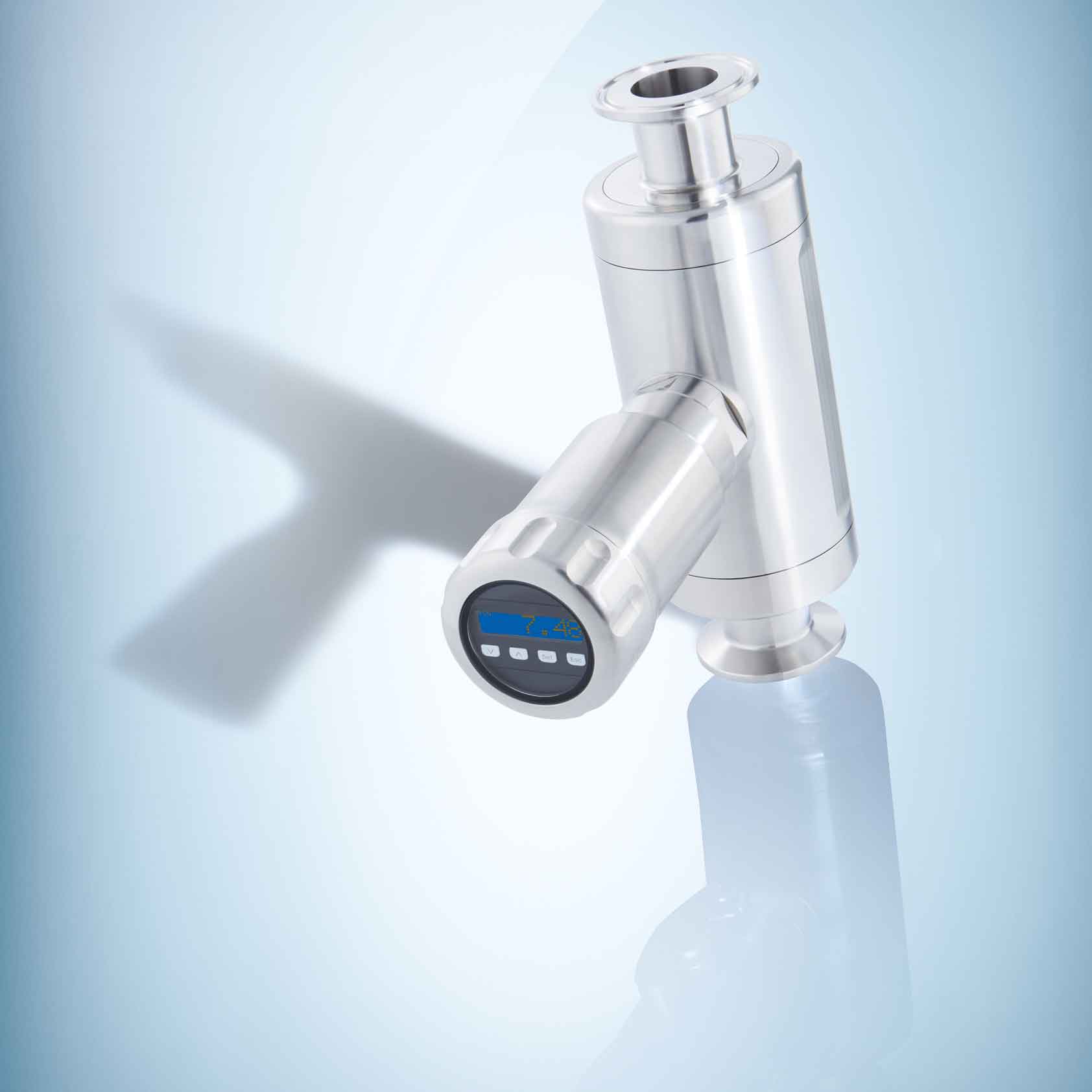
Waldkirch, June 2017 - At this year’s drinktec, SICK will present sensors for an automated production process for the food and beverage industry. The sensors not only communicate at the controller level, but also at the higher data level. The additional interface to the data or software system enables new analyses and functions to be performed, which increase flexibility, quality, efficiency, and transparency in production.
Backward compatibility means that SICK sensors can already do both: They send data reliably to the PLC, but also to the data world. Where the customer benefits is that this proven technology can continue to be used going forward, but it is still possible to take advantage of the additional benefits on a gradual basis.
Stainless steel DOSIC® for flexible flow measurement
SICK present the DOSIC® stainless steel sensor for flow measurement. It detects the flow volume of conductive and non-conductive liquids based on non-contact ultrasonic technology. With its measurement channel and stainless-steel housing, the ultrasonic flowmeter is suitable for measuring tasks in hygienic environments. The compact and rugged design makes the sensor ideal for a wide range of application possibilities, including those where space restrictions or aggressive media play a role. Installation is quick and easy, and does not require medium calibration. The seal-free, self-draining measuring tube enhances process reliability. Up to two configurable digital and analog outputs as well as the IO-Link interface ensure the right output signal. The DOSIC® is EHEDG-certified and FDA-compliant.
Hall A4, Stand 304