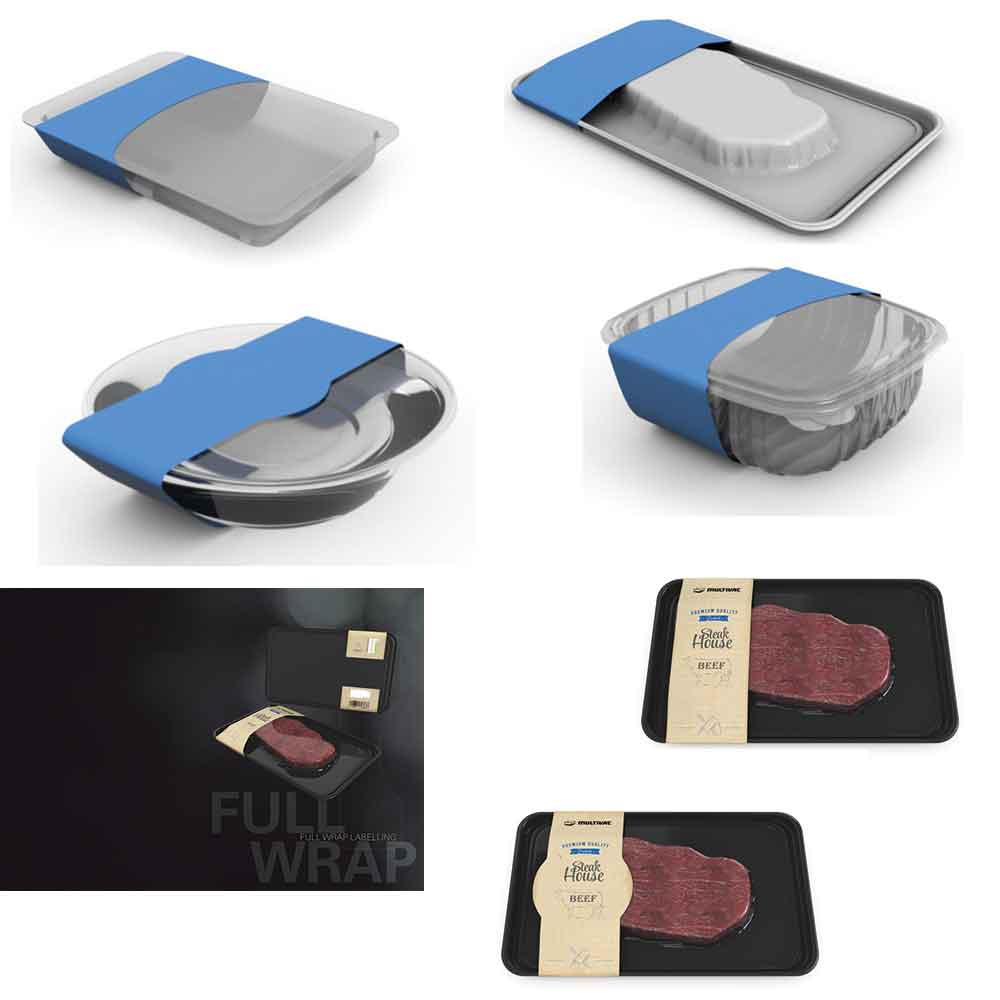
Wolfertschwenden, 11. July 2018 - From 25 to 27 September MULTIVAC will be presenting at FachPack 2018 in Nuremberg a complete range of solutions for packing food and non-food products. A major focus at the trade fair will be on the presentation of packaging concepts, which meet the growing requirement for ease of recycling and saving of resources. MULTIVAC will be demonstrating a R 105 MF thermoforming packaging machine and a T 800 traysealer, which is integrated in a completely automated line, both of which will be running recyclable materials based on paper fibre. In addition to other exhibits, the new X-line generation of thermoforming packaging machines will also be presented, which is equipped for the digitalised production technology of the future thanks to its comprehensive sensor system, and which sets a new benchmark in the market.
MultiFresh TM PaperBoard application on traysealers
MULTIVAC will be showing a T 800 traysealer, which is integrated in an automated line, for producing MultiFresh TM skin packs using pre-cut board. Pre-cut board with different weights or sealing and barrier layers can be run. The packs can be designed in such a way, that the end user is able to separate the carrier board from the plastic barrier layer and then put it into the paper recycling.
The traysealer line includes a multifunctional GMS 520 singlecut meat portioner from TVI, which can process all types of red meat and poultry at a very low level of processing cost for every portion in any consistency, and always optimised for weight and product trim. Pack labelling is handled by a L 310 conveyor belt labeller, which applies a D label to the packs. In addition to this, a blow-on applicator is integrated in the line for applying promotional labels, which are increasingly being used for packs on the fresh food shelves.
MultiFresh™ PaperBoard on thermoforming packaging machines
The production of MultiFresh™ PaperBoard packs on thermoforming packaging machines will be demonstrated on the R 105 MF. A high level of efficiency is a feature of this particular solution. The running of reel-fed materials also contributes greatly to this, since they have a higher level of material efficiency than pre-cut board. As regards the pack design, the spectrum ranges from unformed packs to formed packs with deeper cavities, in which products with different heights and shapes can be packed.
A new benchmark in thermoforming packaging: the X-line
Thanks to its wide range of innovative features, the new X-line generation of thermoforming packaging machines offers customers a high level of added value, when it comes to pack quality, process reliability, output and future-proofing. The machine, which has a sensor system unique in the market, produces packs of excellent quality without any loss of packs during start-up, since the machine is already set to the optimum running condition by Pack Pilot at the start of operation, and its parameters are adjusted to the ideal operating point by the extensive sensor system. This leads to significant savings as regards product, packaging materials and production time - and it also ensures that a higher level of process reliability and cycle output is achieved, which means greater machine output. The innovative die system and intuitive operating concept also contribute to a high level of process reliability. The new Multi Sensor Control ensures that optimised non-stop mode is maintained.
The constantly generated process data forms the basis for providing MULTIVAC Smart Services, which enable the packaging procedure to be run even more efficiently. The X-line is perfectly equipped for ongoing factors such as Industry 4.0, preventative maintenance, condition monitoring, benchmarking or producing comprehensive analysis of overall equipment effectiveness.
Economical solution for producing shaped contour packs, even in small batches
The R 145 thermoforming packaging machine with its innovative BAS 20 shaped contour cutter enables shaped contour packs to be produced economically, even where it is a case of small batches. Thanks to short set-up times, it offers a high degree of flexibility as regards the pack design, the format to be produced and the packaging materials used. The BAS 20 can be designed to cut without trim waste, and thistherefore contributes hugely to reduced consumption of packaging materials and to lower pack costs.
Labelling and inspection solutions
MULTIVAC will be demonstrating its comprehensive expertise in the labelling and inspection sectors with three selected exhibits. The L 35x labeller series was specially designed to apply sealing labels for closing the open edges of folded products such as for example package inserts, outserts and mailshots. The L 352 model will be presented at FachPack with a label dispenser, which applies a sealing label and self- mailer to the back of package inserts and outserts, as well as applying a label to the front edge of the product and a further label to the rear facing edge.
The L 352 can be installed on folding machines from various manufacturers, and it is able to accept the paper products directly. A central height adjustment feature on the frame enables the label dispenser to be adjusted quickly to different working heights, while separate servo drives for the top and bottom transport belts enable it to be adjusted to different paper thicknesses and formats. The machine is changed over to other label widths and labelling positions by means of dispensing edges, which can be exchanged very easily, in conjunction with special format plates for the press-on system. Depending on the folded product, this solution is capable of achieving very high speeds of up to 12,000 units per hour.
MULTIVAC will be showing the I 410 visual inspection system from its portfolio of inspection solutions. Thanks to its high-resolution and height-adjustable line scanners as well as its powerful image processing, it ensures that reliable label and quality inspection from above and below is achieved. The areas of use range from completeness checks on the packs, through to presence and position inspection of the labels, and right up to checking printed text - and this includes pattern and character recognition, character verification and inspection of legibility and codes. The progressive image-capturing technology enables extremely good images in high resolution to be transmitted and verified even at the highest speeds within the packaging procedure.
In addition to this, the exhibits will also include an I 211 checkweigher with integrated metal detector. The detector coil used works with multi-simultaneous frequency and thus offers increased sensitivity aswell as improved product compensation. This enables the smallest metal foreign bodies to be detected reliably, even at a high level of product effect.