Member for
5 years 3 monthsCity
Gurgaon
Company Logo
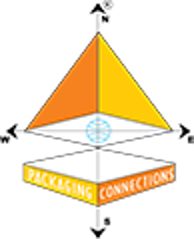
Company Name
Sanex Packaging Connections Pvt Ltd
Company profile
Packaging Consultants
Designation
Technical Lead
Email
info@packagingconnections.com
First Name
Grania
Gender
Female
Last Name
Jain
LinkedIn Url
Member type
Packaging Categories
Phone
9301455800
State
Haryana