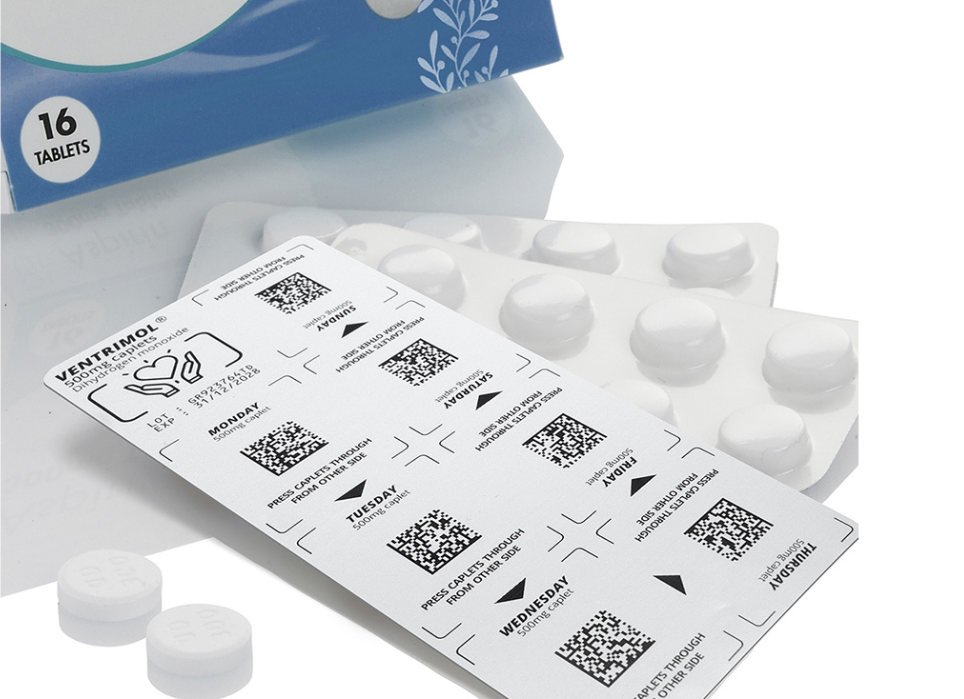
Domino Revolutionizes Pharmaceutical Packaging with Enhanced K600G Individual Dose Serialization Solution
Domino Printing Sciences (Domino) has unveiled a series of groundbreaking enhancements to its K600G advanced variable data printing solution, designed to simplify and streamline individual dose serialization for pharmaceutical manufacturers. This latest innovation underlines Domino’s commitment to addressing emerging regulatory needs while advancing operational efficiency for the pharmaceutical industry.
The K600G, originally launched in 2020, was developed to enable high-speed, serialized coding on critical pharmaceutical packaging materials such as labels, Tyvek medical-grade papers, and blister foils. Now, Domino has introduced several significant updates aimed at making the solution easier to integrate, operate, and maintain — a step forward for manufacturers looking to adopt next-generation serialization practices.
“Individual dose serialization is the future of pharmaceutical regulations,” says Ian Chapman, Strategic Manager for Digital Coding at Domino. “We are preparing our customers for these inevitable changes by providing solutions like the K600G that combine advanced technology with user-friendly design. As the first major global coding and marking supplier to offer this capability, we are dedicated to supporting our customers every step of the way.”
Feedback-Driven Innovation
The upgrades to the K600G were guided by feedback from manufacturers, including a prominent South African pharmaceutical company that participated in early trials. Domino responded by re-engineering the system with an emphasis on operator ergonomics, usability, and compact design.
The new K600G system has a 35% smaller footprint, allowing seamless integration into existing pharmaceutical packaging lines, including space-constrained clean room environments, without significant line modifications. A single touchscreen interface consolidates all controls, simplifying production management and enhancing operator efficiency.
Reduced Downtime and Enhanced Reliability
Domino’s upgrades extend beyond design to operational performance. The enhanced K600G features industry-leading automated maintenance systems, including the i-Tech CleanCap for automated printhead cleaning and capping, and i-Tech ActiFlow, which prevents air bubble formation for consistent nozzle performance. Together, these features minimize downtime and eliminate the need for regular manual cleaning, delivering both reliability and ease of use.
The machine’s integrated frame now includes clear maintenance instructions, enabling swift consumable changes to further reduce production interruptions. These improvements align with Domino’s broader commitment to providing solutions that enhance customer experience while ensuring maximum productivity.
Futureproofing Pharmaceutical Production
The enhancements to the K600G are part of Domino’s broader mission to help pharmaceutical manufacturers adapt to evolving regulatory landscapes. By incorporating advanced variable data printing capabilities, Domino ensures its customers can meet the demands of future individual dose serialization requirements.
“With the K600G, we are not only solving today’s challenges but also futureproofing our customers’ operations,” says Tony McNulty, Chief Product Officer at Domino. “This development is a testament to our collaborative approach to innovation — listening to customer feedback, adapting, and delivering solutions that exceed expectations.”
The improved K600G represents a milestone in pharmaceutical packaging, offering a smarter, more accessible pathway to adopting advanced serialization practices. With these enhancements, Domino reaffirms its leadership in innovative coding and marking solutions, supporting the pharmaceutical sector in meeting both current and future challenges.