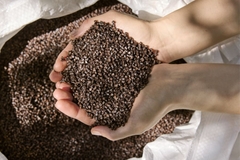
After five years of R&D, Lignin Industries has developed Renol, a patented bio-based material developed from lignin. The process is to incorporate lignin into recyclable bio-based plastic, creating a sustainable alternative to conventional materials.
Christopher Carrick, founder and CTO at Lignin Industries, tells Packaging Insights: “Customers across a number of sectors and geographies will be able to trial the integration of Renol into their products before conducting full-scale market launches.”
“Hellyar’s decades of experience and expertise in polymers ensures that Renol meets rigorous performance and processability standards required by customers across sectors like automotive and domestic goods.”
Gaining momentum
Lignin is a secondary material that does not compete with food production. It is sourced from forestry and agricultural industries, where over 700 million tons of lignin are annually either discarded, incinerated or utilized in low-value energy applications.
The partnership with Hellyar Plastics leverages the company’s dual expertise as both a compounder and distributor. At Hellyar’s Whitstable factory, Renol has been incorporated within acrylonitrile butadiene styrene and PP applications. These materials are now being used in advanced development projects for sectors such as domestic goods and construction, with product launches expected shortly.
David Hellyar, chairman at Hellyar Plastics, says: “We have been working with Lignin Industries for 18 months already, researching the technology and testing market applications. We have been particularly impressed by Renol repeatedly performing to the high standards required by the industry.”
“As our first customers are poised to bring products to the market that incorporate Lignin Industries’ patented technology, we expect the wider industry to recognize Renol’s place in the market as a scientifically-backed means of reducing emissions while meeting the industry’s standards.”
Overcoming barriers
Carrick points out that the industry is currently driven by cost competitiveness.
“The challenge is the potential scale of production and consistency over time in repeat processes. Thirdly, the awareness of the compatibility and flexibility of bio-based plastics in this industry is, or at least has been, traditional. It is used to working with fossil-based raw materials only and has typically been skeptical of new materials.”
“Finally, to decrease the fossil dependency, the industry has only been focusing on introducing recycled materials. We are convinced that the plastic industry will never succeed in reaching its climate goals without using both recycled and biobased raw materials. These two parallel paths need to be taken at the same time,” he adds.
The partnership between Lignin Industries and Hellyar Plastics addresses these challenges through strategic solutions, significantly minimizing the need for additional investment.
“The partnership demonstrates Renol’s suitability for scalability and high-demand sectors. As more companies start working with bio-based plastics, industry acceptance will increase over time and its place in the industry will be normalized through usage,” Carrick concludes.