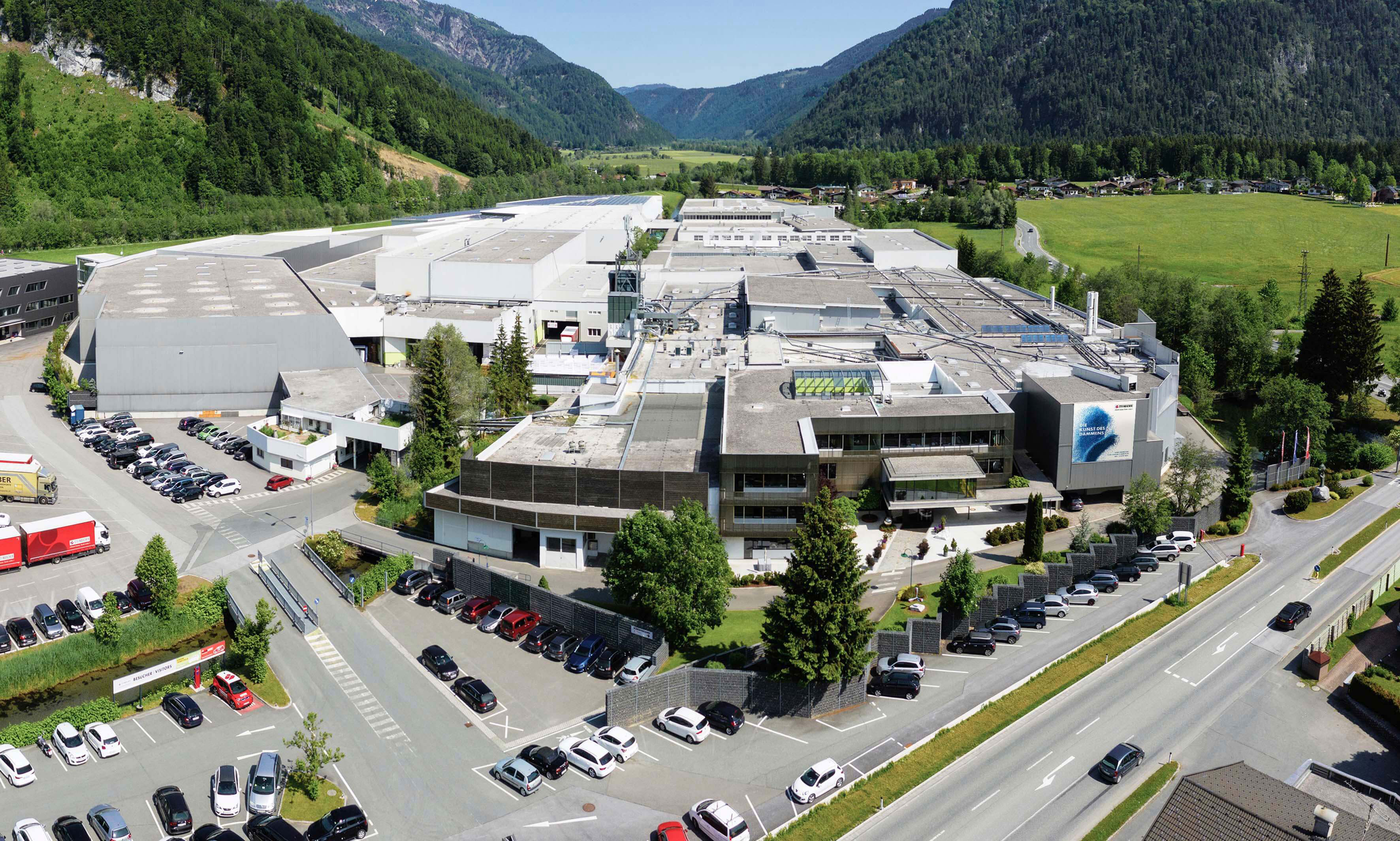
Steinbacher Dämmstoff GmbH in Austria has installed a new packaging line for PU insulation panels. A RoRo StretchPack® solution has replaced two packaging lines for packaging multiple panel sizes. Improved 6-sided packaging and automation are the headlines behind installing the new packaging line.
For some time Steinbacher was looking for a new solution for packaging their PU insulation panels. The primary reason was the need for better packaging quality. Production manager at Steinbacher in Erpfendorf, Mr Markus Brandstätter tells:” It is important for us to have waterproof packaging. Our end-customers do always store the panels outside on the construction site, and in peak time we do not always keep the panels under the roof before shipping”. Mr Markus Brandstätter continues, ”Our previous packaging solution was simply not waterproof, which posed a risk of water between the panels when storing the panels outside”.
Previously, the standard-size PU panels (1200x600 mm) were packed by putting a sleeve around a bundle of PU panels, resulting in 4-sided packaging. The bundles were then stacked on a pallet, which was wrapped using stretch wrap film. The large-size panels were previously packed utilizing heat shrink, but there were constant problems with the weldings. So, neither of the packaging methods provided full waterproofness.
Six-sided packaging - sealed and waterproof
”A few years ago, we came across RoRo StretchPack® produced by Tentoma”, Mr Markus Brandstätter says. RoRo StretchPack® is horizontal 6-sided packaging utilizing a tubular stretch hood film. Only the two film ends need to be welded to achieve sealed and waterproof packaging. Packaging and sealing are done in the same process. It is developed by Tentoma in Denmark, inspired by the well-proven vertical stretch hood packaging technic, typically used for 5-sided packaging of pallets.
Mr Markus Brandstätter explains.” After the initial assessment, we sent different sizes of product samples to Tentoma for test packaging. When the packaging samples returned to Austria, they were thoroughly tested regarding packaging quality, environmental impact, and logistics. We also investigated consumables, potential savings, and automation, to evaluate the business case”.
Removing heat shrink packaging provides energy savings
Maximum energy efficiency and cost savings to improve sustainability are focus areas for Steinbacher. Mr Markus Brandstätter says,” Previously 20-30% of the packaging was done using heat shrink. This is now replaced by RoRo StretchPack® packaging. By direct comparison between our previous packaging solution and RoRo StretchPack® packaging, overall, we have reduced energy consumption by about 50% on the packaging line”.
Film consumption is also an important parameter in relation to both cost and sustainability. Steinbacher is monitoring the film consumption per pallet. Even though that Steinbacher has gone from 4-sided to 6-sided packaging, they have got a film reduction per pallet by using RoRo StretchPack®. Mr Markus Brandstätter adds: ” Now that we have become familiar with the new packaging line, we will optimize the process to further film reductions.
A structured project process
”Summarizing the project process went very well from the first contact till installation and commissioning”,
Mr Markus Brandstätter states, ”It was a structured process with good communication with Tentoma. We had fixed monthly meetings, and later fixed weekly meetings when the FAT (Factory Acceptance Test) approached. Both the FAT and the installation were well planned and executed”.
In connection with the installation, Tentoma trained three employees from Steinbacher as key users on the new packaging line. Mr Markus Brandstätter concludes, ”After the introduction, our employees felt confidential with the new packaging line. We are satisfied with the capacity and the packaging quality of the new RoRo StretchPack® packaging solution”.
Benefits for Steinbacher Dämmstoff GmbH
- 6-sided packaging and waterproofness
- Improved and uniform satisfied quality
- Removed heat shrink from the packaging
- 50% energy savings on the packaging line
- Automation and reduced number of processes in the packaging line
Read more about RoRo StretchPack® www.tentoma.com
Testimonial video with Steinbacher: https://vimeo.com/843173747
For further information please contact Tentoma at info@tentoma.com or by phone: +45 79 30 62 10
Steinbacher Dämmstoff GmbH has installed a new packaging line for PU insulation panels. It is an Austrian full-service provider of insulation materials (EPS/PU/PE/Stone wool) servicing Central Europe. It is a family company having facilities in Austria, Poland and Germany.
Production manager, Mr Markus Brandstätter: ”We are satisfied with the capacity and the packaging quality of the new RoRo StretchPack® packaging solution”.
Bundles of PUR panels in new 6-sided packaging. Uniform packaging by use of a stretch hood film, with sealing in each for full sealing.
View of Steinbacher’s new inline RoRo StretchPack® packaging line.
- The film stand (FS) contains up to 12 km of film, which reduces the number of film shifts.
- The film unit (FU) welds the front end of the tubular film to create a hood.
- The gripper unit (GU) stretches and moves the film to the packaging lane. The film is rolled off the GU, while the panels are packed.
- The back sealing unit (BU) seals the 6-sided packaging.
- The in-feed conveyor receives the panels directly from the production line.
- The output conveyor transports the packed panels to a labelling machine and a palletizing system.