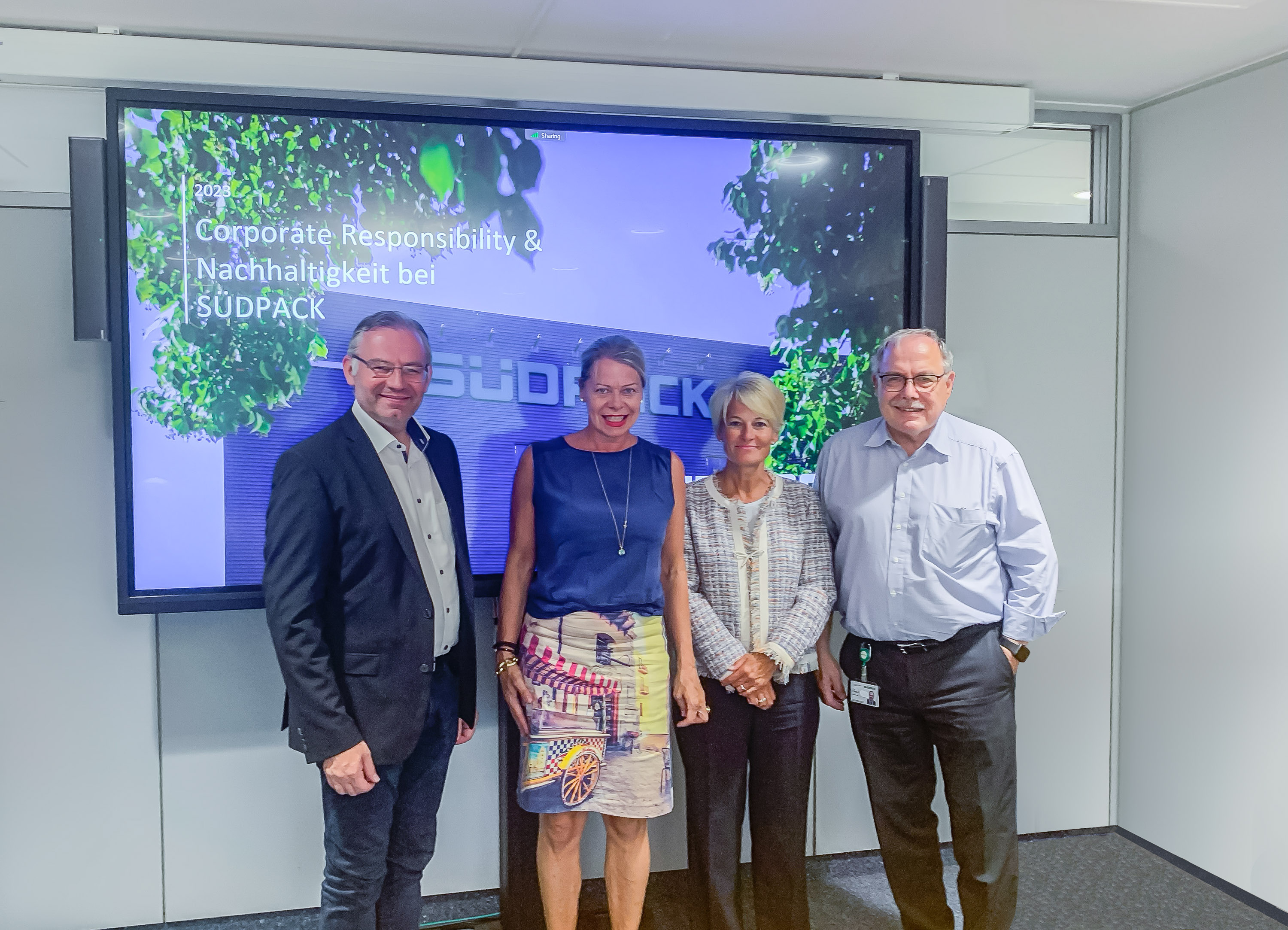
After SÜDPACK was visited by Josef Rief, a member of the Bundestag for the Biberach electoral district, on June 19 to learn more about a circular economy in the plastics industry, the same topic brought Norbert Lins to the site on July 17. The CDU politician from Baden-Württemberg has been a member of the European Parliament since 2014, the chair of the Committee on Agriculture and Rural Development since 2019 and is also active in the Committee on the Environment, Public Health and Food Safety. The main topics at the core of the spirited debate at SÜDPACK’s headquarters in Ochsenhausen included design for recycling, the use of recyclates in film production and chemical recy-cling as a complementary recycling technology.
As one of the leading manufacturers of flexible packaging solutions and one of the key driving forces for a functioning circular economy in the plastics industry, SÜDPACK welcomes in principle the EU Commission’s proposal for a regulation for packaging and packaging waste. At the same time, the export-oriented company group also sees significant room for improvement when it comes to the mandatory rates for the use of recyclate and to clarifying outstanding is-sues and terminology.
Design for recycling
As SÜDPACK understands it, the categorization of the materials in terms of their recyclability is defined based on the recycling capacities within the Euro-pean internal market. “The rapid definition of the term ‘recyclable at scale’ as well as the definition of the corresponding waste streams are a prerequisite in this case so we can continue to operate effectively and, most particularly, in-vest in new products and technologies,” explained Valeska Haux, VP Strategic Marketing at SÜDPACK.
Chemical recycling as a complementary technology
The current draft of the PPWR (Packaging and Packaging Waste Regulation) also includes chemical recycling as a complementary recycling technology in addi-tion to mechanical recycling. This really hits home with SÜDPACK. Within the scope of its ZERO WASTE strategy, the film manufacturer and its cooperation partner CARBOLIQ have proven that this advanced form of chemical recycling can be used to keep plastic fractions in the loop that cannot currently be recy-cled mechanically. In particular, this includes multilayer films that are used for packaging products that are contact sensitive, such as food and medical goods. “Compared to the thermal recycling of these plastic fractions, chemical recy-cling can reduce the carbon footprint by about 50 percent,” highlighted Haux – while also pointing out: “When it comes to the mass balance method to be used, however, there is still no clear understanding. That is why we recom-mend the “fuel exempt” method and already presented the proposal through CEFLEX.”
Use of PCR in contact-sensitive materials
According to the PPWR, the proposed use rate of recyclates that are approved for contact with food or medical goods is ten percent. As SÜDPACK interprets the situation, food law constraints mean that this rate can only be achieved in the European internal market by using chemical recycling. “CEFLEX has calcu-lated that this would require a recycling capacity of roughly 1.1 million tons per year. At the moment, however, we do not expect this capacity to be available by 2030. It would therefore make sense to postpone the target and to first develop the necessary framework and capacities. To do so, the chemical indus-try will need – as will SÜDPACK within the framework of its commitment to chemical recycling – the appropriate planning and investment security,” accen-tuated Carolin Grimbacher, Managing Partner of SÜDPACK. Last but not least, “a mass balance approach is an essential precondition for the recognition of chemical recycling and for meeting recyclate use rates.”
Use of reusable packaging
Another point of discussion during the visit was that reusable packaging cannot currently be used in the markets supplied by SÜDPACK. SÜDPACK is therefore advocating for the avoidance of creating cannibalization effects between “re-usable” and “recyclable” packaging in the legislative procedure and to instead look at the two concepts separately.
Norbert Lins views SÜDPACK’s concrete suggestions as an important impetus in light of the upcoming vote on the PPWR draft by the Environment Committee, because “pioneering legislation such as the PPWR require the industry’s ac-ceptance, expertise and, even more, its willingness to invest.”
About SÜDPACK
SÜDPACK is a leading manufacturer of high-performance films and packaging materials for the food, non-food and medical goods industries. All of its solu-tions ensure maximum product protection as well as additional pioneering features with minimum material input.
The family business, which was founded by Alfred Remmele in 1964, is head-quartered in Ochsenhausen. The production sites in Germany, France, Poland, Switzerland, the Netherlands and the USA are equipped with the latest plant technology and manufacture to the highest standards, including the capacity to operate under clean room conditions. The global sales and service network ensures a high degree of proximity to the customer and comprehensive appli-cation technology support in more than 70 countries.
With its state-of-the-art Development and Application Center at its headquarters in Ochsenhausen, the innovation-oriented company offers its customers an optimal platform for carrying out application tests and for developing individual and tailor-made solutions.
SÜDPACK is committed to sustainable development and fulfills its responsibility as an employer and towards society, the environment and its customers. For its particularly sustainable product developments and consistent commitment to a functioning circular economy in the plastics industry, SÜDPACK has received numerous awards. Further information is available at www.suedpack.com