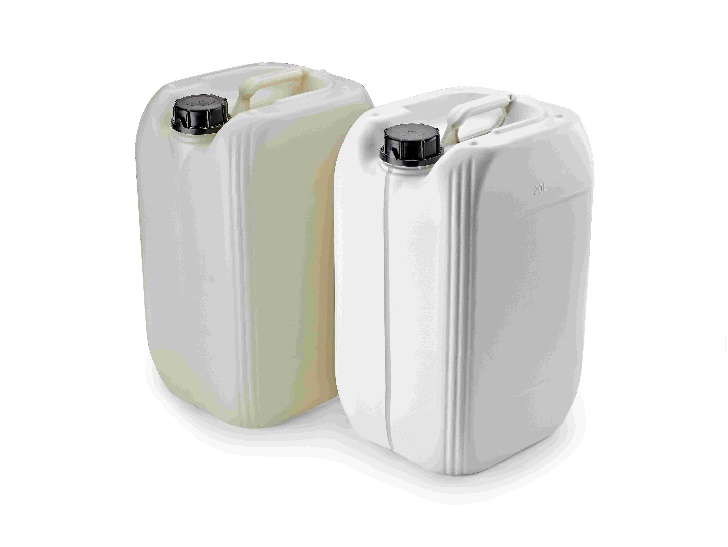
Berry Global’s technical and manufacturing skills have achieved a significant breakthrough in the packaging of hazardous liquids. The company has now launched the first 20 and 25 litre containers containing 35% recycled material, which have UN Approval for the transport of hazardous goods for five of the six model liquids in the UN assessment.
In addition to the existing UN approval for water, the new containers also have approval for wetting solution, acetic acid, white spirit, and N-butyl acetate.
The introduction of these new containers into the company’s popular Optimum range will support companies both in meeting their sustainability goals and satisfying consumer demands for more sustainable packaging solutions. It will also help businesses comply with forthcoming legislation covering the required minimum amount of recycled material in a pack.
The inclusion of 35% recycled HDPE (rHDPE) into the Optimum containers provided a technical challenge in order to achieve UN accreditation. Typical processing of the material can sometimes produce varying results due to its composition, but UN approval requires processing to be stable and repeatable to ensure the quality and consistent performance of the finished container.
To ensure this, Berry is taking its rHDPE from controlled sources, focusing on post-industrial packaging such as IBCs, drums, and HDPE canisters. This minimises any variations in the material. In addition, the containers retain their low weight, both reducing the amount of material required in production and maximising ease of handling for the end-user.
“We believe these new containers offer one of the highest contents of recycled material with UN approval currently available on the market,” commented Rudolph Pfeiffer, General Manager for Berry Global BMS. “We are very pleased to be able to provide our customers with a solution to the packaging of challenging products that supports their sustainability commitments without compromising on quality or performance.”
The new Optimum containers are available with standard DIN61 and ASTM63 neck finishes, suitable for a range of standard and vented closures, and can also be specified in a range of colours. The containers’ design with interlocking top and base allows safe and easy stacking.
Typical applications include chemicals, hazardous goods, agriculture and horticulture, automotive care and pool care. Berry says additional container sizes are now in development.
About Berry
At Berry Global Group, Inc. (NYSE: BERY), we create innovative packaging and engineered products that we believe make life better for people and the planet. We do this every day by leveraging our unmatched global capabilities, sustainability leadership, and deep innovation expertise to serve customers of all sizes around the world. Harnessing the strength in our diversity and industry-leading talent of 46,000 global employees across more than 250 locations, we partner with customers to develop, design, and manufacture innovative products with an eye toward the circular economy. The challenges we solve and the innovations we pioneer benefit our customers at every stage of their journey. For more information, visit our website, or connect with us on LinkedIn or Twitter.