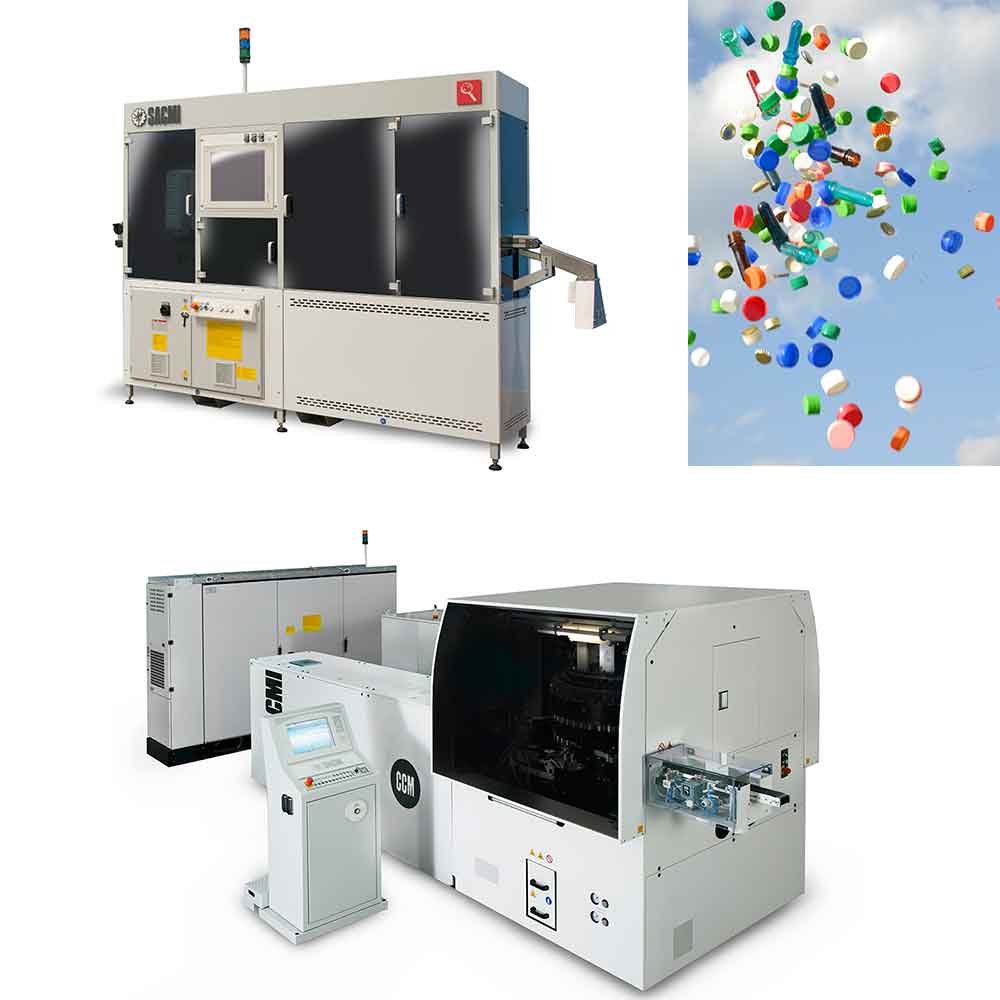
The country's main plastic-rubber industry event will see the Group attend with the successful compression press range, now enhanced with new cap-preform integrated design services. Alongside these solutions, Sacmi will also showcase CHS inspection systems for total cap quality control and the advanced Sacmi line supervisor, which manages orders and monitors all plant performance parameters, even remotely.
With no less than 300 m 2 of display space, Sacmi will be out in force at the 32 nd edition of Chinaplas, the international plastics-rubber fair being held from 24 to 27 April 2018 at the National Exhibition and Convention Center in Hongqiao (Shanghai). The star of the stand (hall 2H, n° B61) will undoubtedly be Sacmi cap manufacturing and quality control technology.
Sacmi compression technology for cap manufacturing sets the global standard: over the last 15 years it has won over markets thanks to advantages in terms of quality, performance and energy savings. Through its range of CCM (continuous compression moulding) compression presses, this technological solution offers the lowest cycle times in the industry, with productivity as high as 2,000 caps per minute with just 48 moulds.
Offering intrinsic advantages in terms of productivity, energy savings and reliability, compression technology operates at lower temperatures, thus reducing on-material stress and extending the working life of both machine and plant. Compared to alternative solutions such as injection, this technology also has the capacity to manufacture lighter, better-performing caps; moreover, their weight and other parameters can be modified easily via the operator interface.
Efficient and flexible, Sacmi CCM machines also let manufacturers cover the entire cap range on the market; this is because they can manufacture caps of different designs using the same mould and provide an enormous variety of designs. A further Sacmi strong point is the capacity to provide integrated cap-preform design services that combine weight and cost reduction with solutions that are innovatively designed. For example, one of flagships of the Sacmi range is an innovative slitting machine series, specifically designed to manage every aspect of cap finishing, even where caps are manufactured using non-CCM presses; moreover, the company – one of just a handful in the world capable of managing every aspect of production – can provide targeted consultancy services right from the product design stage.
Sacmi is also a leading designer of quality control systems and, alongside the compression presses, completes the range with the CHS (closures handling system), the platform for total in-line high-speed cap inspection. The latest CHS version released on the market can perform comprehensive cap inspection thanks to perfect 2D reconstruction of the 3D perimeter. Developed by the Sacmi Automation & Inspection Systems Division, this advanced solution uses the advanced algorithms already successfully implemented on labelled container, preform and decorated metal cap inspection systems. Both machine and inspection system can be controlled remotely using the advanced Sacmi line supervisor which allows real-time monitoring of plant performance and management of production orders by interfacing directly with the customer's ERP.
Present in China for over 30 years, Sacmi combines advanced technology with far-reaching, efficient after-market assistance. A key factor on a market like China where over 50% of consumers (source: IPSOS) now see quality and safety as crucial to their purchasing decisions, leading local producers to seek out ever-more reliable, versatile, higher quality solutions with European technology.