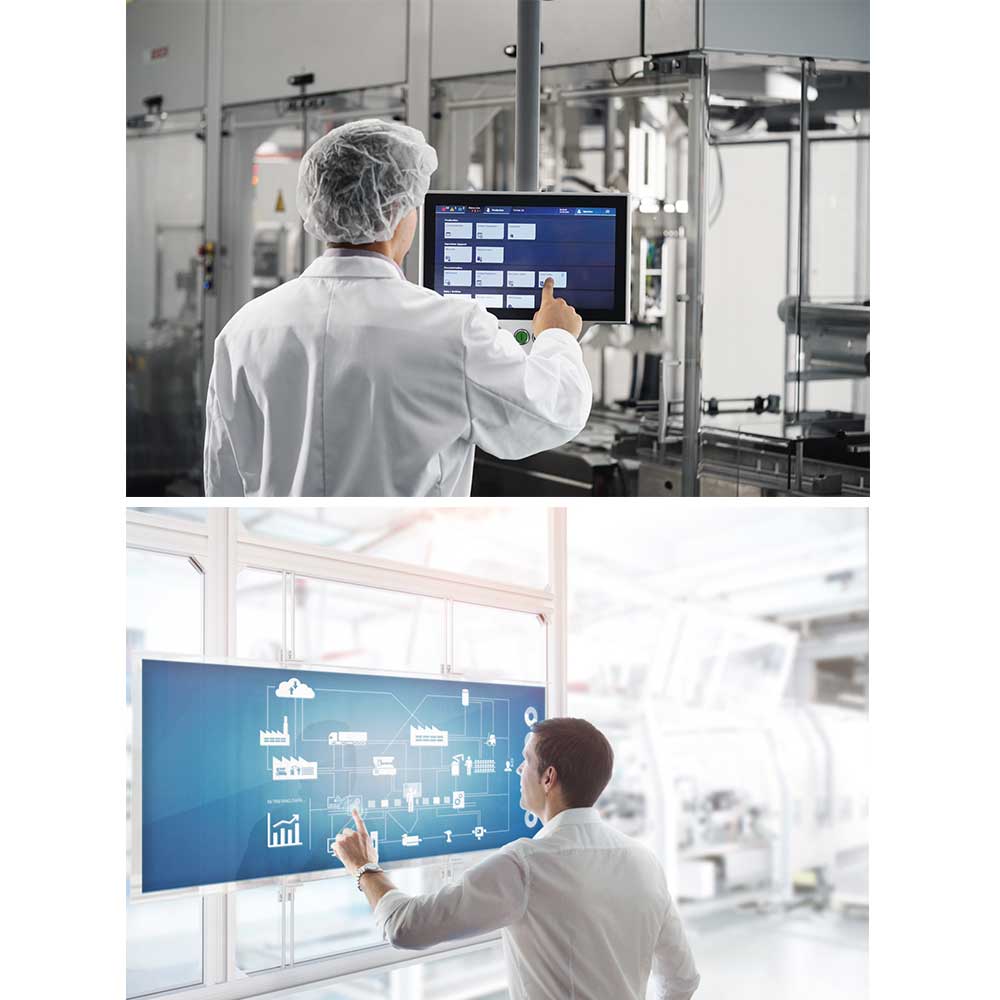
- Safe format changes thanks to RFID technology
- Efficient maintenance support – on-site and via remote connection
- Augmented and Virtual Reality applications offer support with maintenance, troubleshooting and training
Stuttgart/Düsseldorf, Germany – At interpack 2017, Bosch Packaging Technology shows how industry 4.0 solutions provide higher efficiency in modern manufacturing. “All of our industry 4.0 applications focus on humans,” says Dr Stefan König, president of Bosch Packaging Technology. “Machine operators, as well as maintenance and service staff receive the best possible support in their daily work – and can thus complete it faster and more efficiently.”
For instance, efficient and correct format changes with all format parts reliably installed in the right position, are a prerequisite for low downtime. In the future, machine operators will receive valuable support thanks to the Format Part Management based on RFID technology. The format parts are identified through an RFID tag. Via the format part ID, operators receive relevant information about the format change. This not only reduces changeover times, it also prevents potential mistakes.
Efficient maintenance support
With the Maintenance Support System (MSS), operators and maintenance engineers are supported in the efficient execution of all kinds of maintenance activities. Thanks to the analysis of machine data in real-time, they receive all required information to their mobile devices. This enables them to react quickly, reduce walking distances and save time for the search for spare parts. The Operations Assistant makes it possible to create and store step-by-step instructions including text, images and videos. Via the visualization app Maintenance Assistant, operators receive real-time information and instructions for upcoming maintenance and cleaning jobs.
In case they do require external help, experienced Bosch specialists can connect with customer machines via the safe VPN data connection of the Remote Service. Whether support for set-up, remote diagnosis, troubleshooting or the installation of software updates is required – Remote Service makes it possible to correct faults efficiently before they lead to production disruptions. Additional images, videos and audio files can be exchanged with the Shopfloor Remote Assistant. For example, if a spare part needs changing, the Bosch technician can highlight it on the image. Moreover, Bosch offers data-based services allowing Bosch experts to evaluate and analyze production data and to make recommendations for action.
Transparency in real-time
Operators want to be informed about the condition of their lines at any time. The Line Dashboard provides a clear visualization of all relevant parameters. Wherever the operators are, the Line Dashboard delivers the appropriate information including alarm notification in case of a defect. This helps to reduce walking distances and downtime.
With developments in Augmented and Virtual Reality, Bosch takes transparency and efficiency one step further, and showcases first application areas at interpack. “We will literally take industry 4.0 solutions to the next dimension,” König says. “Augmented and Virtual Reality offer completely new possibilities to support staff with maintenance, troubleshooting or during trainings by supplementing real live images by additional information, or even simulating three-dimensional environments.”
New dimensions for maintenance, troubleshooting and training
On the mandrel wheel machine PME 4081, Bosch demonstrates how employees could perform maintenance activities even faster thanks to Augmented Reality (AR). To do so, they receive step-by-step instructions on their tablet, consisting of real machine images, as well as detailed visual and textual information. This way even service staff without expert knowledge can remedy faults and carry out format changes quickly and reliably.
AR glasses further speed up this process: instructions are projected directly into the field of view, so that operators have both hands available for the format change. This not only results in an efficient and correct execution of the task. It also brings a welcome change to daily work, as well as a positive user experience. New AR applications also make troubleshooting a lot more efficient. In case of a malfunction, the operator is shown the exact position of the component on his tablet, enabling him to locate and correct the defect faster.
Thanks to Virtual Reality (VR), operators can view the virtual image of their real machine, for instance via a smartphone which is integrated into a pair of glasses. VR applications especially facilitate error location and troubleshooting. They can, however, also be used for virtual trainings, such as learning about format changes under near real-life conditions. Trainers can view the simulation live and give supporting instructions immediately. For operators, this is an efficient and safe way of training, as faults have no direct consequences. Moreover, the production process does not need to be interrupted.
“At interpack we want to explore these entirely new possibilities for our industry together with our customers,” König explains.