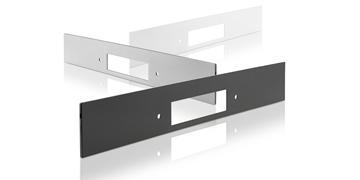
Using the know-how from four industries to drive innovation in the household appliance sector: That was the goal when the Swiss kitchen specialist V-ZUG AG brought three companies on board for a joint project. The Fürth coating specialists from Leonhard Kurz, the injection molding experts from the Swiss A. & J. Stöckli AG and the Munich machine builders from KraussMaffei were also present. Your task: You should give the control panel of the new premium oven from V-ZUG a new face. As usual in the automotive industry, the aim was to visually upgrade the panel, but at the same time to make its production more efficient. This should be made possible by in-mold decoration technology (IMD) - a process that turns two process steps (injection molding of the component and decoration) into one. IMD technology is already used in many industries. The V-ZUG joint project was a first for the Swiss household appliance industry.
IMD technology has production and economic advantages
V-ZUG is the premium kitchen specialist in Switzerland. The company produces and sells design-oriented household appliances. V-ZUG was convinced that the functionality and appearance of the high-end household appliances would benefit from IMD technology. IMD allows a wide variety of decors, even metallization is possible. Particularly important for household appliances: IMD has a "built-in" surface protection; thanks to highly resistant topcoats, surfaces are easy to clean, and the decoration is resistant to cleaning agents or moisture.
The economic advantages of the IMD process cannot be dismissed out of hand. B. aluminum. Or the desired surface look only arises during subsequent processing. Production steps such as painting or electroplating mostly take place in Asia or Eastern Europe; they are a cost factor and at the same time ensure a negative environmental balance. Because IMD enables injection molding and decoration not only in one step, but is also suitable for recycled plastic materials, the process brings decoration processes "home"; this makes them more efficient and sustainable.
Kurz delivers IMD coating and IMD tool
Due to its special knowledge of IMD technology, V-ZUG Kurz, the German expert for thin-film technology, took part in the project. Both companies have a clear design focus. Kurz develops and produces individual IMD decorations; the necessary tools and the foil feeder for the injection molding machine also come from Kurz. The IMD carrier material is fed through the injection molding tool via a film feed unit and pressed into the cavity by the injection molding material. The temperature of the material ensures that the decorative layer detaches from its carrier and connects to the plastic part. This eliminates the need for subsequent decorations, intermediate storage and other work steps. A short video shows how the process works:
https://www.plastic-decoration.com/dekorationsverarbeitung/inmold-dekor…
But IMD does even more: Due to the so-called dead-front effect, IMD applications can completely hide control elements for integrated touch functionality. They become visible only through backlighting. At Kurz, In-Mold Decoration is also combined with In-Mold Labeling (IML): During the injection molding process, conductive sensor films from the Kurz subsidiary PolyIC are applied to components. This process is used for control panels in the areas of automotive, home appliances and consumer electronics. The following always applies: Both in-mold processes enable cost-effective series production.
A. & J. Stöckli AG casts and decorates components using KraussMaffei machines
The second partner for V-Zug AG was the Swiss A. & J. Stöckli AG. The company produces high-quality plastic components for the household appliance industry, among others. In the project, Stöckli was responsible for the implementation of the oven panels using the IMD process and for the overall project coordination. This makes Stöckli the first company in Switzerland to combine injection molding and IMD technology and to implement customer-specific component realizations of this type. Stöckli installed a new IMD-capable production machine especially for this task.
This injection molding machine brought partner number three into the project - the German machine builder KraussMaffei. Its engineers found a clean cell solution that enables the oven panels to be produced with little particles: after all, the control surface of the high-end oven should have a flawless appearance. Electronic and mechanical interfaces are clearly defined in the machine. A flexible articulated arm robot makes the system ready for future components or further process steps. The film feed tool from Kurz was used in the KraussMaffei machine for the In-Mold Decoration. Due to their easily accessible two-panel construction, it is also easy to change the film for the three different panel decorations.
V-ZUG AG uses In-Mold Decoration for further series productions
V-ZUG, Leonhard Kurz, Stöckli and KraussMaffei are proud of how well the coordination was achieved in the complex project. The Combair V200, V400 and V600 oven series has been on the market since spring 2019. V-ZUG is currently working on further variants; Dishwashers are also to be decorated with the in-mold process and thus taken to the next design level. The Swiss kitchen appliance manufacturer plans to launch the new appliances this year.
LEONHARD KURZ Foundation & Co.KG
Schwabacher Str. 482
D-90763 Fürth
sales@kurz.de
www.kurz.de
Tel .: +49 911 71 41-0
Fax: +49 911 71 41-357