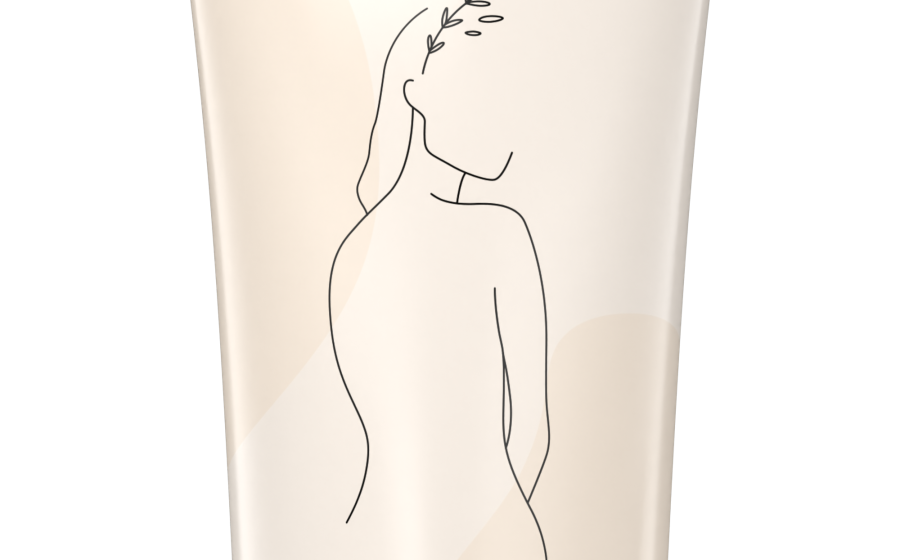
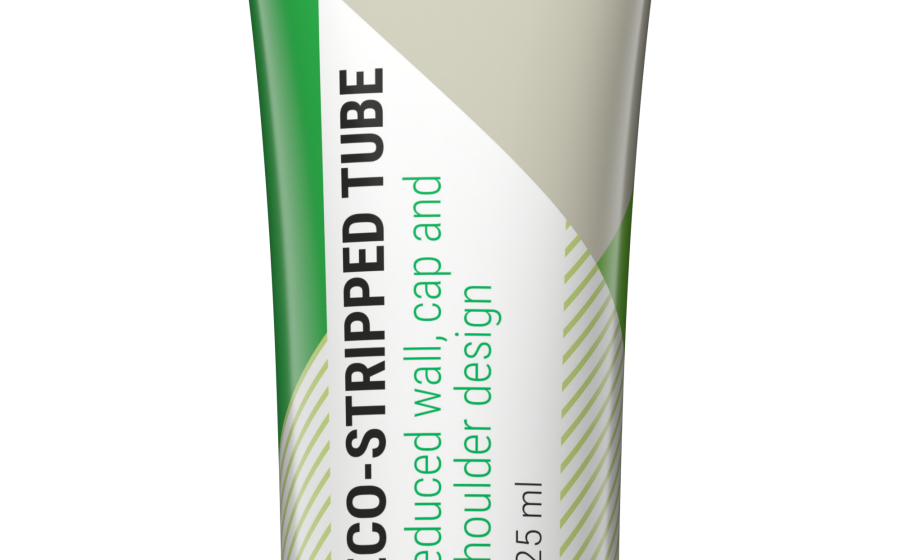
Concept extends company’s materials-reduction mindset to cap and shoulder, saving customers carbon footprint, EPR fees & shipping costs without sacrificing product protection, haptics or esthetics.
Oberdiessbach, Switzerland – Hoffmann Neopac, a global provider of high-quality packaging for pharma, beauty and oral care, has “capped off” its commitment to reducing plastics in its tube designs. The company has introduced Eco-Stripped Tube, which combines a significantly reduced sleeve wall thickness with a comparable materials reduction in the shoulder and cap. The result is a 30% reduction in overall virgin materials without sacrificing product protection, haptics or esthetics.
For cosmetics and personal care product customers, the benefits of Eco-Stripped Tubes are several. For starters, the trimmed-down tubes substantially reduce carbon impact; in fact, four Eco-Stripped Tubes can be made with the amount of materials it takes to produce three conventional tubes of the same size. Less overall plastics also means lower Extended Producer Responsibility (EPR) fees – so-called “plastic taxes” – as well as lower shipping costs.
For Neopac, reducing overall materials to create lower-profile shoulder and cap represents a materials science breakthrough. For size D50 tubes, for example, the sleek Eco-Stripped tubes sit 9.4mm lower with a 3.75g weight reduction without sacrificing performance.
The latest in Neopac’s EcoDesign series, Eco-Stripped Tube is an evolution of its LIGHTWEIGHT TUBE, which reduces sleeve wall thickness from 0.5mm to 0.35mm. The next-generation Eco-Stripped Tube builds upon this sleeve weight reduction to create a comprehensively trimmed-down tube construction. An eco-conscious substitute for standard PE, PP and coextruded tubes, Eco-Stripped Tubes are available in diameters ranging from 30-50mm, for volumes from 40-300ml. For enhanced protect protection and safety, tamper-evident (first-opening) options also are available.
Neopac estimates that, in its own packaging manufacturing operations, the new tubes will eliminate the need for as much as 7.7 tons of HDPE and PP materials per one million tubes produced. This translates to an overall carbon footprint reduction of over 29 tons of CO2 per million tubes manufactured.
“The concept behind our new Eco-Stripped Tube is ‘undress to progress’, meaning a key tool in moving toward a circular economy is overall materials reduction – and virgin plastics reduction specifically,” said Cornelia Schmid, Head of Marketing for Neopac. “As a company, we’re continuing to push our sustainability efforts further without sacrificing product protection, haptics, esthetics or other qualities brand owners hold dear.”
Other solutions in Neopac’s EcoDesign portfolio includes RECYCLED TUBE featuring 70% recycling material, 64% of which is PCR; Sugarcane Tube, made from renewable raw materials; and PICEA™ wood tube, comprised of 95% renewable material in the tube body and shoulder – including 10% of spruce wood from wood waste in sawmills.
About Hoffmann Neopac
Hoffmann Neopac is a privately-owned company, headquartered in Thun, Switzerland. The group produces high-quality metal and plastic packaging in six locations: HOFFMANN tins in Thun and Holland; Polyfoil® and plastic tubes with NEOPAC in Switzerland, Hungary and the US; and 3D Neopac in India. Its longstanding customers include internationally active pharmaceutical, cosmetics and consumer goods manufacturers in the European, North American and Asian markets.
Including its new production facility in the United States, Neopac employs around 1,250 employees and has a capacity of 1.3 billion tubes. The company is dedicated to sustainability in both its manufacturing processes with renewable electricity and corporate culture, including a dedicated eco-conscious packaging portfolio. For more information, visit www.neopac.com.