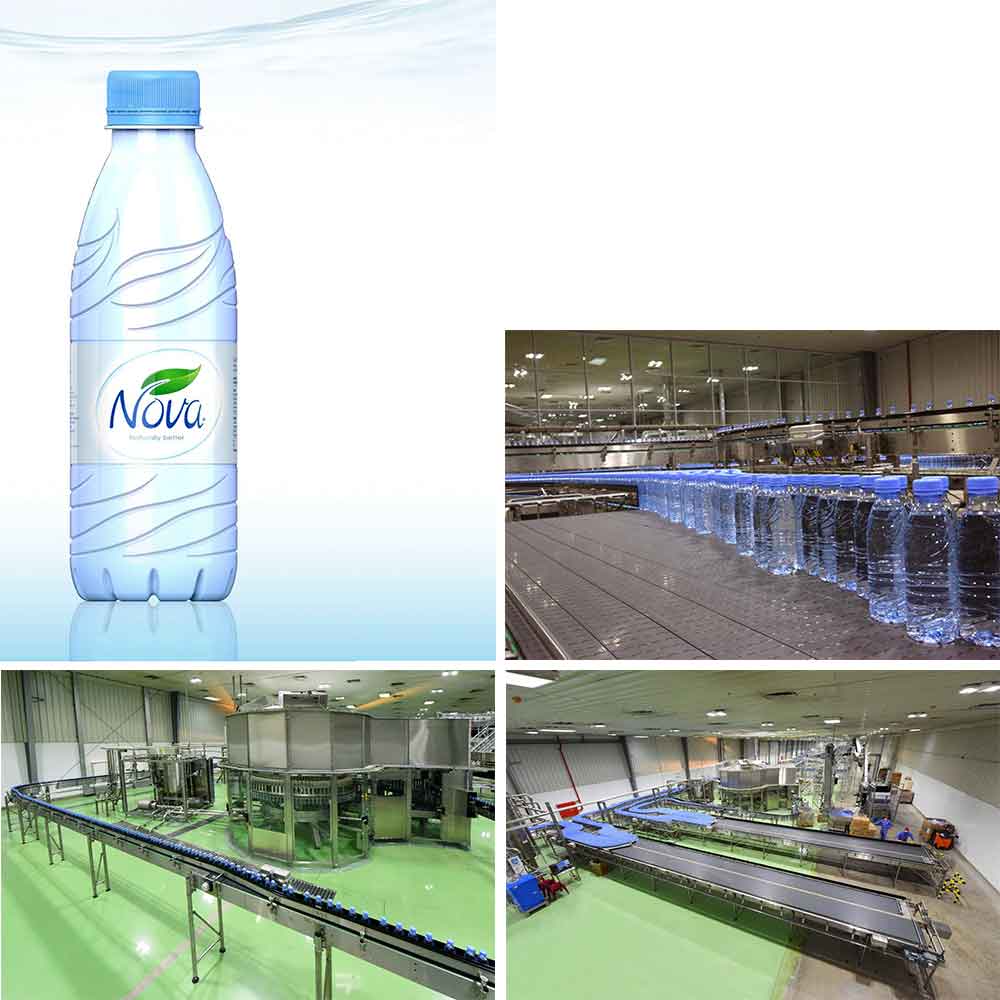
Following the successful installation two years ago of what was Sidel’s fastest bottling line in the world at the time, the Health Water Bottling Company (HWB) of Saudi Arabia decided to invest in two further lines. The original solution still runs at a speed of 134,000 bottles per hour (bph), whereas the two new Sidel complete PET water lines are both now running even faster - at the new, record-breaking output rate of 150,000 bph each, making a total installed output of 300,000 bph.
Leading a growing market
Bottled water is a growing market in the Kingdom of Saudi Arabia (KSA) and HWB leads the way with Nova water. In the country, a growing population with an increasing focus on health has resulted in a dramatically bigger demand for both still and carbonated water over recent years. In the Greater Middle East region, the top ten countries represent 92% of the total volume of the beverage market. Of these, Saudi Arabia is second only to Turkey and, according to forecasts, the market for PET-bottled water in the Kingdom is expected to grow by 7.3% CAGR over the current four-year period (2016 - 2020), outpaced only by CSD 1 .
The first company ever to be awarded the prestigious “Quality Mark” by the Saudi Arabian Standards Organisation, HWB has always endeavoured to differentiate itself from the competition by being innovative within the bottled water market. Since its inception in 1973, the company has also constantly sought the right opportunities to diversify into the marketing and distribution of beverages other than water and, consequently, now offers a comprehensive portfolio of drinks. As well as producing the market-leading, premium brand of bottled water in the region, Nova, which spearheads its water division, HWB also produces other highly reputable brands, as well as distributing Holsten, a malt drink and Power Horse, an energy drink, throughout the KSA. Thesebrands strongly reinforce the company’s reputation for only supplying products of the highest quality.
The new HWB plant is located at Al-Wase’e, 110 kilometres east of Riyadh, a strategic location with easy access to both the eastern and central provinces, as well as neighbouring Gulf Cooperation Council (GCC) countries. Al Wase’e reserve is an area of outstanding beauty where the company’s wells tap the purest and richest water in the kingdom - a highly prized commodity thanks to the clean, unpolluted nature of the environment and the resulting quality of the water. At all stages of the bottling process, the highest standards of hygiene and quality controls are applied at the HWB factory, to guarantee a product quality which conforms to national and international standards. Nicola Barusi, Sales Manager for Sidel in Saudi Arabia, says: “We have worked with HWB for the past twenty years. The company originally purchased its first Sidel blow moulder in 1997 and currently has eighteen Sidel blowing machines up and running on its sites.”
Reassurance even for a satisfied customer
However, the long working relationship, the success and high efficiency (95-96%) of the first record-breaking water line, as well as the overall satisfaction of HWB with Sidel’s experienced Field Service Engineers, who have provided the customer with local support and fast reaction times for spare parts availability, was not enough. The company still had to convince its customer that it was the right partner to install two complete PET production lines running at a significantly high speed - an unprecedented speed “fuelled” by the local positive market trajectory recorded by Nova water.
Discussions for the new project lasted around six months, which were spent with Sidel talking the customer through various options and explaining the technicalities involved. This close cooperation reassured HWB that the innovative yet reliable solution that Sidel was suggesting would mean the lines would be able to reach the speeds required. All of this was achieved without compromising on continuous production efficiency throughout the lifetime of the equipment, product integrity and hygiene. During the installation of the lines, communication between the companies was efficient and regular, with the HWB team receiving timely and expert advice from the proactive Sidel team.
Pushing performance boundaries
The two lines were designed comprising a total of four Sidel Matrix™ Combis, six Sidel F35 labellers, two wraparounds and two Sidel palletisers, with the design allowing the two lines to utilise the same end-of- line solution. This approach has allowed HWB to gain a significant reduction in total cost of ownership (TCO), further enhanced by a drastically reduced footprint. In fact, as well as achieving the record-breaking speeds requested, both lines also had to occupy a zone of the production floor formerly used by a single line. Sidel’s team came up with a solution that maximised the available space by including a mezzanine floor to house part of each line on the upper floor.
HWB Plant Manager, Harry Nowers, comments: “Success in water beverage production requires a focus on maximum output and efficiency, with a commitment to hygiene, food safety and cost optimisation. With everything centred on Sidel as a single supplier, we continue to leverage the company’s knowledge of the entire water bottling process, from minimising waste of resources, to ensuring the bottle is durable and attractive to consumers. Through this additional investment in our high speed lines and our extensive understanding and experience of the market, we are looking to develop a Centre of Excellence for bottled water in the KSA.”
The newly launched Sidel Matrix system is Sidel’s most powerful solution to date in terms of performance, flexibility, cost savings and sustainability, all of which are attained under the most stringent conditions of hygiene.The four Sidel Matrix Combis – the core of the installation - deliver outstanding hygiene performance while simultaneously cutting costs to package still water and carbonated beverages. Compared to standalone equipment, the Sidel Matrix Combi reduces operating costs by up to 12% depending on the product being packaged, the package itself and production output. Furthermore, it uses up to 30% less floor space, compared with traditional standalone equipment.
Equipped with the Sidel Matrix Filler SF100 FM, it ensures high filling accuracy without product loss and its external tank that holds the beverage is easy to clean, saving time. A double-speed, filling valve is also available to reduce the headspace of the bottle in order to fill greater volumes. To ensure optimum hygiene, all parts of the SF100 FM that come into contact with the beverage are manufactured in stainless steel AISI 316L.
The two recently purchased PET complete lines – in use since June 2017 to produce the company’s Nova brand of water in 330ml format - bring the number of Sidel complete PET production lines installed for the customer up to three.
Overcoming the issues of a challenging supply chain
As well as installing the two complete, new water lines, HWB decided that - with the existing design being more than 15 years old - it would also be an appropriate time to refresh the look and branding of its Nova water bottles. The challenge was to create a lightweight bottle that ensures complete product integrity across the supply chain where high speed is combined with complicated logistics, in a country where retailers are often based long distances from HWB’s distribution centres. As well as these very practical considerations, the new bottle needed to give the popular, premium brand a more modern image.
Again the company expressed its confidence in Sidel’s capabilities. Having over 40 years of heritage in designing and implementing customised complete PET line solutions for water, strengthened by a world-leading PET packaging design expertise, it is true that Sidel has significantly reduced the weight of water bottles over the years, while retaining the bottles' durability and expanding the design possibilities for them.
The new container design features the Sidel StarLite™ bottle base, which utilises a unique shape that significantly increases base resistance and stability. By featuring two Sidel proprietary design innovations for PET bottles, the StarLite base design improves bottle rigidity while enabling a lower package weight and reduced energy consumption during production. The end result is a PET bottle that can cost less to produce, yet offers better pallet stability and higher bottle integrity throughout the supply chain without compromising on the safety standards of the contained beverage.
Vincent Le Guen, Vice President, Packaging & Tooling, who actively participated in discussions concerning the design of the new bottle and made several visits to HWB during the implementation phase of the new design, explains: "The Health Water Bottling Company was looking to refresh the look of their premium brand, while - like many other customers - looking to remain competitive by saving costs. One way for us to achieve this is to lightweight the bottle as much as is physically practical. However, in doing this, it is necessary to ensure the packaging remains attractive throughout the supply chain and the integrity of the finished product and its content is never affected. The StarLite base has enabled HWB to reduce package weight and blowing pressure, while increasing base resistance to deformation.