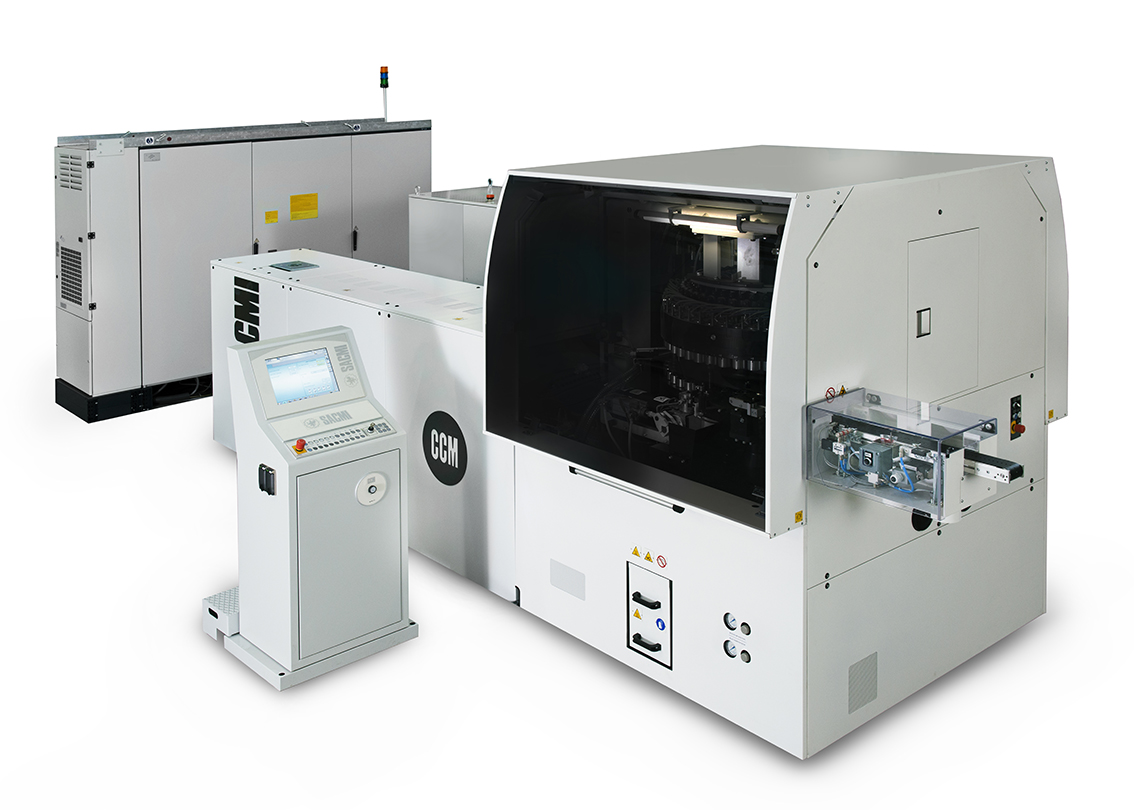
Group to take part in the fourth edition of Oman Plast, presenting all the latest developments in its CCM, IPS and CBF ranges: cap, PET preform and container- making solutions that have, thanks to cutting-edge technology, won over the global industry's biggest players
Sacmi will be taking part in Oman Plast 2018, a major Gulf event that focuses on packaging and closures solutions (Muscat, Oman Convention & Exhibition Centre, 7-9 May 2018). Thanks to unmatched quality, productivity and energy savings, Sacmi compression technology has profoundly innovated closure manufacturing and will be a prominent feature in the Group's display area (Hall 3, stand n° 957-958).
Incorporated in the CCM (continuous compression moulding) press range - which has the lowest running costs in the industry - compression technology lets manufacturers set the cap parameters and design directly via the operator interface as each mould cavity can be managed independently. Versatility and total quality control run parallel with Sacmi's capacity to provide integrated cap-preform solutions. The latter reduce weight without affecting performance (i.e. lightweight solutions), lowering energy and raw material consumption even further.
Sacmi leads the world in manufacturing HDPE caps with this technology and has succeeded in transferring its advantages to stretch-blown container manufacturing. CBF (compression blow forming) is the world's most advanced blow moulding technique and combines the very best characteristics of alternative technologies such as EBM, IBM and ISBM.
This single-stage platform is characterised by excellent thermodynamic stability, no gate on the bottom of the container, high productivity and precision-moulded necks. It lets manufacturers make containers directly from pellets, using all the main commercially available resins. Thanks to the versatility of being able to use different resins, precision and uniform thickness, Sacmi CBF machines have made huge market gains (especially in the dairy and pharma sectors).
The third essential component when it comes to providing economically advantageous solutions for the beverage packaging world is the Division that develops and produces the PET preform injection machines in the vast IPS (Injection Preform System) range.
The world's only company capable of providing a proprietary technology for every stage of beverage production – from cap-preform systems to blowing, filling and labelling – Sacmi combines plant engineering excellence with a far-reaching service to provide assistance before, during and after the sale.
Through Sacmi Middle-East, based in nearby Dubai, customers can count on spare parts assistance 7 days a week from a team consisting of engineers from the parent company and local technicians, specially trained to provide support during
all start-up, testing and after-market operations. Last but not least, service quality is enhanced further by smooth synergy with the Sacmi Group's Beverage R&D facility, certified by the international industry's top players.