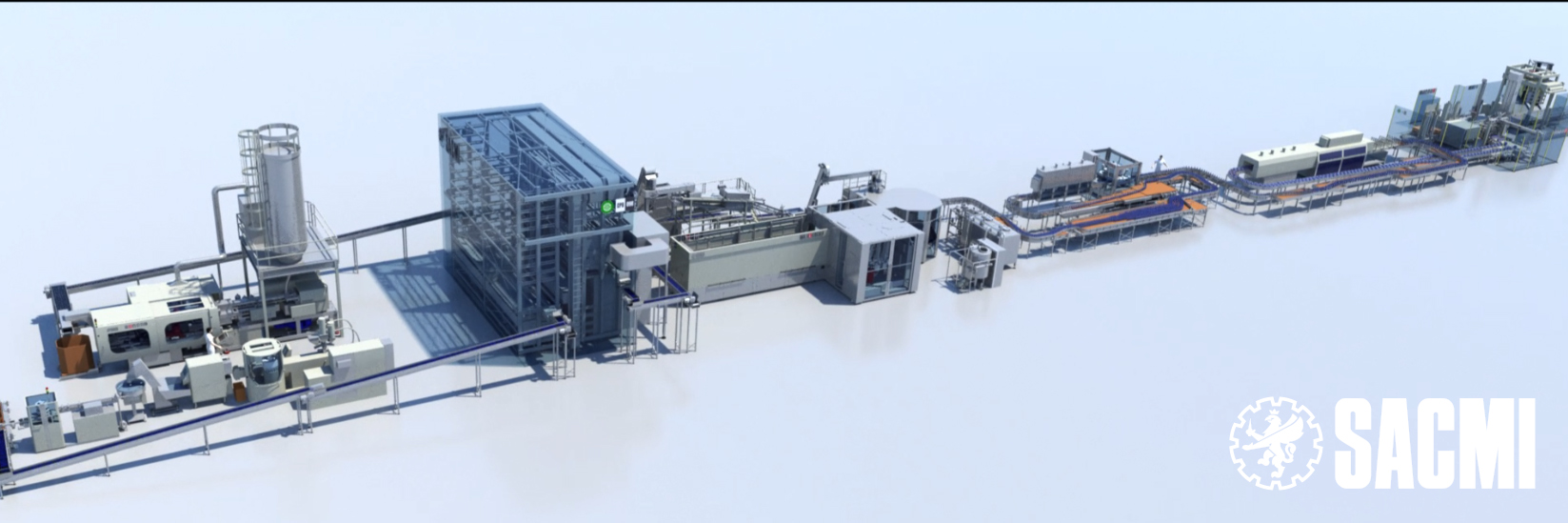
Working alongside a major local agent, the Group will be at the bi-annual fair to present all its latest beverage & dairy solutions. The range - now even more complete - incorporates technologies and services that bring all the advantages and opportunities of Industry 4.0 to this sector too
A major North African venture for Sacmi's Packaging-Beverage Division, soon to exhibit alongside local agent Ejem at the bi-annual Plastic Expo in Tunis (12-15 April 2017). Organised with the support of the country's most important plastic and chemical business associations, this fair will showcase (on over 10,000 m 2 ) the best technology and the latest trends in the industry: an industry that, in North Africa, is characterised by impressive dynamism and growing consumer interest in healthy products.
A world leader across numerous sectors and technologies (the only supplier able to provide complete “pellet to pallet” lines for beverage plants), Sacmi will exhibit - alongside the latest developments in compression technology, with its tried-and- tested CCM plastic cap manufacturing range - cutting-edge solutions for converters. These include, for example, the IPS 400, the latest addition to the IPS (injection preform moulding) range that offers major new benefits as regards process automation and flexibility. Then, there are our popular BAG IN BOX fillers (both aseptic and ultra- clean), which offer ultra-high productivity (up to 900 bags/hour per filler with 3-litre containers).
Versatility and productivity also characterise Sacmi's labelling solutions (OPERA, Formsleeve+, KUBE), machines that, thanks to a modular structure (plug&play), ensure efficient single-solution manufacturing across different labelling technologies and systems. All Sacmi machines can be combined with the advanced inspection systems developed by the Group's Automation&Service Division; these ensure outstanding quality control, in-line and at ultra-high speeds, of cap, preform, container and labelled bottles.
On an emerging market like Tunisia, what makes the difference is the Group's ability to work alongside the customer, thanks to a fast spare parts service and remote assistance software (installed throughout the range) that lets customers receive real-time support from a specialised Sacmi technician, anywhere in the world. Last but not least, the Sacmi Beverage R&D facility, certified by the industry's top international players, provides close customer support right from the design stage to identify ultra-efficient personalised solutions in keeping with both manufacturing and market needs.