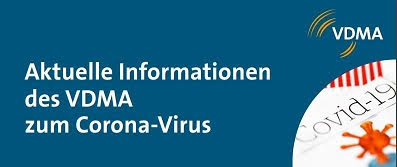
Interview with Clemens Berger, Managing Director of the Food Business Unit at Syntegon Technology in Waiblingen
Those looking for Bosch Packaging will find Syntegon since January 2020. After five decades of being part of the Bosch Group, the packaging and process specialists are now standing on their own two feet. In this interview, Clemens Berger, managing director of the Food business unit, talks about the new brand and its commitment to sustainable packaging and processes, as well as about the strategic and technological orientation of the company, which in 2019 achieved sales of around 1.3 billion euros with 6,100 associates.
Mr. Berger, the change of ownership from Bosch to CVC Capital Partners has been completed. What does this mean for you and your existing customers?
Clemens Berger: We see this as a great opportunity to become more independent and agile. Our industry is dominated by mid-sized companies, and thanks to the now independent, leaner structures, we too have shorter decision-making paths than before. This is in line with the general conditions in the industry.
With the name change, you are exchanging the established Bosch Packaging brand for the new Syntegon brand. What will be the brand core?
Berger: The Bosch name naturally carries weight in mechanical engineering. But we are confident that with Syntegon we will be able to develop our own profile as a leading process and packaging machine manufacturer. In our view, this includes a greater focus on service than has been the case to date. Syntegon offers process and packaging technology for a better life. That is our brand essence. In other words, the claim to develop intelligent and sustainable process and packaging solutions that benefit consumers and patients. The artificial word Syntegon reflects this: leveraging synergies. Driving technologies forward. And clear orientation towards the future and sustainability.
Its industry focus is on the pharmaceutical and food industries. What spectrum does your process and packaging technology cover?
Berger: We supply individual machines and see ourselves as a system supplier who develops integrated complete solutions and services for our customers. In the pharmaceutical sector, the spectrum ranges from processes to production - weighing, filling, conveying, pressing and coating, inspection, laboratory automation - to the packaging of solid and liquid pharmaceuticals. Whether capsules, ampoules or syringes. Traceability via Track & Trace is also part of it. Our portfolio is similarly broad in the food industry: from process technology for confectionery production to complete packaging lines for bars, cereals, dairy and frozen products or coffee. Aseptic filling processes are often required. We also contribute our know-how to make food production and packaging more energy efficient. Energy and resource efficiency are more in demand than ever. Syntegon has the relevant knowledge.
Are there modular approaches here or is this purely special machine construction?
Berger: Modularity is elementary for us. When developing new machines, we rely on our modular system as far as possible. This is also important for our customers, because they have to convert their lines often and quickly from one product to another. For example, to separate vegan or lactose- and gluten-free products. Modular concepts offer the necessary flexibility. On the other hand, you will hardly find machine lines that are nearly identical at different customers of ours. The demand for individual adaptations is high. We see ourselves as a special purpose machine manufacturer who relies on modular approaches to optimally implement individual customer wishes.
What role does printing technology play in your packaging solutions?
Berger: In the pharmaceutical sector, our track & trace solutions are integrated in the printing technology. Folding cartons are provided with so-called data matrix codes under close quality control. Inkjet and laser printers are used here. Otherwise, in the pharmaceutical and food sectors, our machines tend to process pre-printed packaging. In some cases, small-scale individualization of packaging is required for highly individualized pharmaceutical products or for campaigns at events in the food sector. But as soon as it goes into mass production, printing professionals take over.
The trend towards the circular economy is unmistakable in packaging. What roles do paper and board play?
Berger: This is a hot topic in the food sector. On the one hand it's about better recyclability through mono-materials instead of multi-layer films. On the other hand, packaging processes must be adapted so that the existing systems can process the new materials. This is not a trivial matter because different, often narrower temperature windows apply when sealing and welding mono films. On the other hand, our customers are in the process of replacing plastics with paper-based materials wherever possible. Due to the large number of inquiries, we are expecting adjustments on a larger scale. This also requires extensive process know-how. Plastic films and paper-based materials have very different properties. However, we are working in various cooperations on improved materials, new design approaches and guidelines for shaping recycling management. This also includes minimizing energy consumption in the overall process. Ultimately, no supplier can solve these issues alone. But together, really good, viable solutions can be found.
Do Artificial Intelligence, Connected Customers or 4.0 approaches also play a role?
Berger: Definitely. In addition to the Sustainability Officer, an Industry 4.0 officer also reports to me. Because this is a core issue for us; artificial intelligence is also increasingly being incorporated into our product developments. In one to two years we will see the first solutions on the market. Industry 4.0 is no longer a hype topic. There are practical solutions for the service and maintenance sector, machine networking or even for centralized process data evaluation in which Artificial Intelligence has a lot of potential.
Are there any regions with particular growth dynamics for Syntegon?
Berger: Fortunately yes. We are currently experiencing a significant revival in the US market. In the medium and long term, we see the greatest growth potential in the packaging markets of Asia and Africa. Thank goodness the living conditions for many people there are improving. It is now a question of ensuring that food and other products reach consumers in good condition and in good quality. Enormous quantities of food are still spoiling in the supply chains there. Sustainable packaging can change that.
Their after-sales services - including embedded engineers - are attracting attention...
Berger: ...I'm glad. Because, as mentioned at the beginning, this is one of our central issues. We want to convince our customers with fast, reliable service. In view of the complexity of today's manufacturing and packaging processes, embedded engineers are a real added value for many customers. In some cases they do not find qualified operators. Specialists who know their machines inside and out and who are also familiar with the applicable hygiene requirements in pharmaceutical and food production are very welcome. They also act as a bridge, helping us to understand customer processes and identify areas where optimization is needed. Our research, development and testing center in Königsbrunn is another factor in this customer orientation. There, we conduct tests with our customers and their products on our laboratory machines - and we have a fully equipped microbiological laboratory, among other things, so that these real-life tests can be thoroughly evaluated immediately. By the way, our service specialists are also specialized in one of the two areas of pharmaceuticals and food. It doesn't make sense otherwise, because the requirements are too different. Our customers need experts who understand their processes and general conditions.
What do you see when you imagine Syntegon in 2030?
Berger: We are the leading supplier of process and packaging technology. Syntegon consistently focuses on intelligent and sustainable technologies, because this is the only way to optimally meet our customers' requirements. We also want to become a service company - in the sense of top quality and maximum availability of our machines. With this we want to distinguish ourselves in the market and gain further market shares by 2030. The issue of sustainability will be decisive in this context.