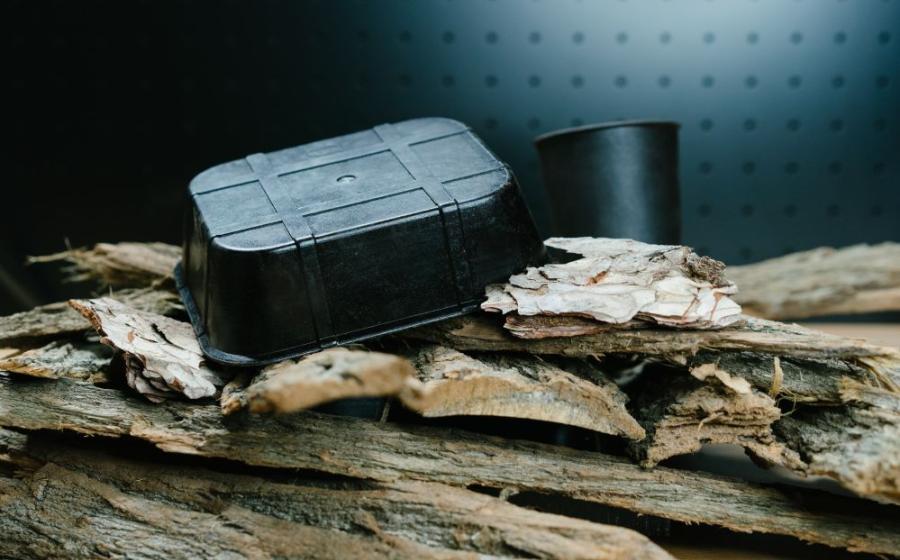
Founded in 2022 by Mikhail Skalkin, Dr. Nikolay Semenov and Lev Bolshakov, with offices in the UK and Belgrade, Serbia, Bpacks’ R&D work is led by materials scientists Dr. Semenov and new head of innovation Dr. Aleksandra Nešić. It combines bark from timber production, used coffee grounds and other bio-based materials to create sheets and granules/pellets that can be used by packaging manufacturers to create a variety of materials.
As it is currently filing patents, the company remains tight-lipped about its production process, but says it doesn’t involve solvents: “The production process starts with compounding, followed by the creation of pellets or sheets, and concludes with the casting of solid packaging, which takes place either by injection molding or thermoforming.”
The resulting biodegradable material can handle high-moisture products but “should fully decompose in moist soil within one to two months,” claims the company. “It is 100% home-compostable.”
According to Skalkin: “Traditional bio packaging often struggles to compete with its plastic counterparts in terms of pricing and integration complexity. Our bio-based plastic substitute can be manufactured using existing plastic production equipment, eliminating the need for plastic factories to purchase new equipment.
“Moreover, our packaging is 100% bio-based, with up to 75% of materials sourced from production waste [such as bark and used coffee grounds],” noted Skalkin, who said annual bark production was estimated to be between 300 and 400 million m3.
‘The majority of bark ends up as waste. We are giving it a new life’
Currently, Bpacks head of innovation Dr. Aleksandra Nešić told AgFunderNews, most biodgradable bioplastics are made from agricultural feedstocks such as corn, soybeans, sugarcane or brewery residues to create materials such as polylactic acids (PLAs), or in some cases wood pulp from the paper industry to create cellulose-based products.
“In the rigid packaging industry, PLA is the most used, but cellulose based packaging is also coming back to the market because some products cannot be packed in PLA and for some products it is too expensive.
“Other [bioplastics] such as PBAT [Polybutylene Adipate Terephthalate from sugarcane or cornstarch] or PHAs [Polyhydroxyalkanoates made via microbial fermentation with various sugary feedstocks] are out there but in very low amounts.”
Bark, she said, “is a massively underutilized natural resource and it’s almost free as a raw material. Some of it is utilized for extracts because it has some interesting properties [anti-microbial, antioxidant, anti-inflammatory, immunomodulatory, astringent, anti-ulcer, and wound-healing properties], although those extractions typically require high amounts of harmful chemicals or petroleum-based chemicals.
“But the majority ends up as waste. We are giving it a new life.”
Integration with existing infrastructure
According to Bolshakov: “There are plenty of bio-based packaging solutions out there but cost and scale is an issue and some of them face integration challenges [to fit into existing infrastructure for packaging materials production]. We’re introducing a new technology that integrates with current equipment. So if a manufacturing company wants to replace its plastic pellets, this can be done easily and seamlessly with our granules.
“Our lab has limited capacity but we can also license our technology [to manufacture the granules] to plastic packaging companies. It doesn’t require expensive bespoke equipment, so existing production equipment can be used.”
Properties of the material can be tuned both by altering the ratios of the ingredients used in the 100% bio-based formulation, but also by altering the process parameters, said Bolshakov, who said the company has thus far been funded by the founders’ capital and a small group of private investors.
Extending shelf-life
Bpacks’ packaging is ideal for fruits and vegetables and meats, where internal testing shows it can extend shelf-life thanks to its anti-microbial properties, added Bolshakov, who is now validating this via testing at independent third-party labs.
He added: “The increase in shelf-life is a key advantage to potential customers, plus we think we can be competitive with petroleum-based products.”
According to Precedence Research, bioplastics currently make up less than 1% of the global plastics market, but are expected to grow significantly in the coming years as firms are under increasing pressure to reduce their carbon footprint and meet legislative requirements. In 2021, the global bioplastics market size was estimated at $11.2 billion, and it is projected to reach $46.1 billion by 2030.