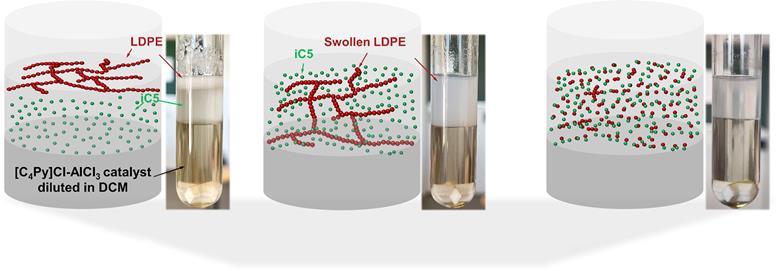
Owing to the difficulties of recycling polymers by traditional, mechanical means, attention is increasingly turning to innovative ways of chemically converting waste plastic into either new plastic or more valuable materials. Conversion of polyolefins, such as polyethylene and polypropylene, however, is particularly challenging, as the carbon–carbon bond is extremely stable, so breaking it usually takes a lot of energy. Researchers have tried to circumvent this by coupling the endothermic reaction to another exothermic reaction to produce processes that will run at low temperatures. However, the activation barriers usually mean that these require temperatures of over 200°C to run at an appreciable rate.
Chemical technologist Johannes Lercher and colleagues at the Technical University of Munich in Germany and Pacific Northwest National Laboratory in the US coupled cracking of the polymers with alkylation of the resulting alkenes by isobutane or isopentane. Both these reactions normally have large activation energies. However, in previous work Lercher and colleagues demonstrated that charged transition states of non-ionic reactants are stabilised in strongly ionic reaction environments. This can lower the activation energy of a reaction.
In the present work, the researchers propose that both these reactions have carbenium ion intermediates. This therefore allows a Lewis acidic species generated in a chloroaluminate ionic liquid to catalyse both reactions, and the coupled reaction scheme proceeds to near-full conversion at just 70°C. The researchers produced components of high-octane fuels from common consumer waste products such as LDPE packaging and FFP2 masks. The reaction requires an excess of branched alkanes such as isopentane, but Lercher argues that this would not be problematic in an industrial setting. ‘What you get out are a mixture of lighter and heavier alkanes,’ he explains. ‘The heavier ones you use as fuel, the lighter ones you recycle and use as the next alkylating agents.’
‘It is pretty fundamentally exciting,’ says polymer chemist Yutan Getzler at Kenyon College in the US. ‘There’s so much really interesting chemistry that they put out there: being able to get the barriers on these processes down is wild, it seems like a really interesting use of ionic liquids and it seems there’s potential there.’ He is also impressed by the fact that the catalyst is based on aluminium – the most abundant metal on Earth – rather than platinum or palladium. He is cautious about the fact that the end product is a fuel, however. ‘Calling it a circular carbon economy when you’re burning it – people love to do it but I philosophically disagree with that,’ he says.
Lercher is unapologetic, though, arguing that it could allow people to use waste plastic at a more local scale. ‘The plastic problem is that we distribute a man-made product that is considered to be permanent over a very-wide volume, and in order to solve the problem we have to bring it back together,’ he says. ‘I have deliberately not patented this: what we offer is a low-temperature, cheap and easily-accessible path to use that garbage instead of simply burning it.’