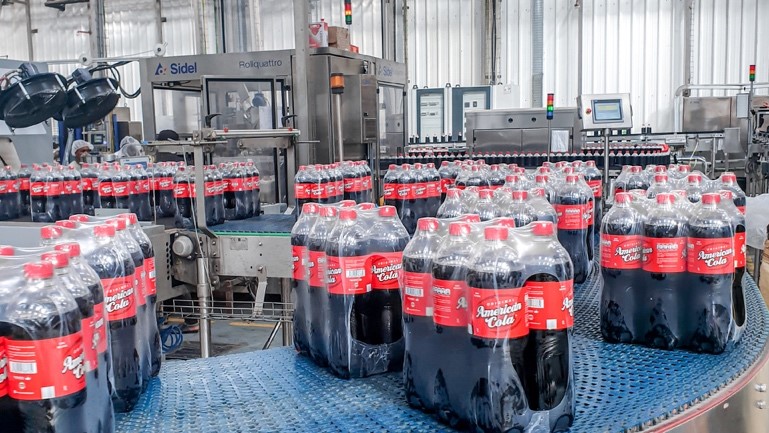
To expand its carbonated soft drink (CSD) brands “Planet”, “Bubble Up” and “American Cola” and meet market needs for home consumption with larger formats, Nouvelle Brasserie de Guinée (Braguinée) reached out to Sidel for help with the remote tuning of its packaging line to produce 1L bottles. In just three days, Sidel’s multi-expertise team from around the world were mobilised to guide and empower the customer, using Sidel’s latest remote line-adaptation technologies and leveraging effective digital solutions for quick set-up of larger formats.
Braguinée is a family-owned company and part of Gaselia Group. It opened its plant, equipped with a Sidel PET packaging line, in 2018 in Conakry, capital of Guinea. Braguinée is one of the top three players on the Guinean CSD market with growing demand for its products. Its best-known products are “Planet”, available in six flavours, “Bubble Up”, in three flavours, and “American Cola”. It also manufactures other beverages such as energy drinks, juices and bottled water.
As Gaselia Group had already experienced successful collaboration with Sidel since 2009, Braguinée once again turned to its trusted partner to align with market demand. The company was previously producing beverages in small, on-the-go formats (300 ml and 350 ml) and needed to adapt its production for home consumption with a larger format (1L).
With travel restrictions due to Covid and to ensure a fast launch of the new 1L bottle, line tuning was carried out remotely thanks to Sidel Remote Video Assistance and Remote Access solutions. The complete packaging line with a Combi SF300 for CSD, installed in 2018, can now manage not only on-the-go formats but also 1L bottles for three of its flagship brands (“Planet”, “Bubble Up” and “American Cola”) with high efficiency, running at 22,000 bottles per hour (bph).
with in-depth equipment expertise to ensure a safe and efficient line adjustment to the new format. To do so, an international team of high-level Sidel experts from Pakistan, Italy, Portugal and the United Arab Emirates were mobilised to ensure flawless line conversion. Remote collaboration, continuous availability of Sidel experts, accurate and clear communication between both parties as well as specific documentation facilitated the successful installation of the new equipment parts required to run the new 1L bottle format.
“A fast release of our new product on the market with minimum line downtime was possible thanks to strong collaboration and excellent project management by Sidel. Everything was planned in detail, from parts installation to line start-up, and we could count on the expert team at every step of the project. They also showed great teaching skills and, thanks to the digital solutions they used, they quickly transferred Sidel's expertise to our team. Learning by doing was a great way to develop our operators’ technical skills even further!” remembers Amadou Ndiaye, Technical Director at Braguinée.
Right combination of digital tools for efficient remote support
Line tuning for the new format involved a combination of complementary digital remote solutions: Remote Video Assistance (RVA) and Remote Access to customer equipment. Braguinée’s team could successfully check all mechanical aspects: correct installation and adjustment of parts, validation of machine operations, and optimisation of line efficiency. In addition to live chat and drawing-over functionalities, the video-supported Augmented Reality feature accurately guided the customer. With Sidel’s expert hands showing the movements and pointing to details in real time on the equipment, seamless exchanges were possible. This resulted in Sidel experts having complete situational awareness and in accurate corresponding actions from the customer’s operators. Also, during line adaptation, Sidel experts checked all settings and set the correct ones for the new format to ensure its quality and maintain optimal line efficiency.
“Despite the distance and Covid restrictions, Sidel was able to provide the same high quality of line conversion services to the customer with the help of our digital solutions, thus enabling greater flexibility in the whole process. The remote services also gave an additional advantage for Braguinée by saving on travel-related project time and costs for the Sidel team,” says Hannes Oeschger, Lead Customer Care Manager at Sidel.