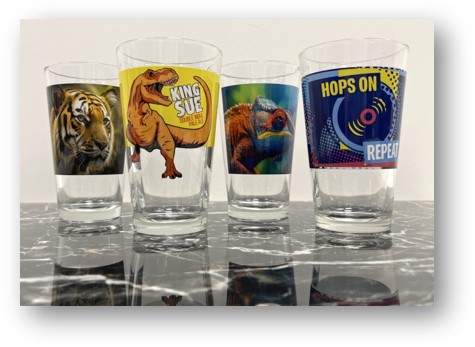
Leading printhead manufacturer, Xaar is enabling the production of ‘game-changing’ digital inks due to its Ultra High Viscosity Technology, according to global ink manufacturer, Marabu.
Ultra High Viscosity Technology is providing manufacturers with an array of new and practical production possibilities by enabling a much wider range of fluid viscosities and chemistries to be printed at around 100 centipoises (cP) at jetting temperature, equating to approximately 1000cP at ambient temperature.
This ability to jet higher viscosity fluids is opening the toolbox for ink manufacturers such as Marabu. The 165-year-old business develops digital inks as one of its three business pillars, and the options to develop new fluids for inkjet printing have been transformed through enabling the use of materials and chemistries that haven’t been possible with other inkjet printheads.
“Xaar’s Ultra High Viscosity Technology is a real step forward in industrial inkjet printing – a ‘game-changer’ – as we move from analogue to digital print,” said Tobias Lang, Marabu’s Product Manager for High Viscosity Inks.
“For example, we can create new inks that allow high-impact, reliable jetting with sharp contours, enabling the layering of durable, resistant haptic effects. In the low-viscosity era, meeting high image quality requirements demanded a more complex process, which high-viscosity inks simplify by creating a wider process window at faster production speeds.”
This has been seen recently with the successful collaboration between decorative print machine manufacturer Koenig & Bauer Kammann (Kammann), Marabu and Xaar.
Combining Xaar's printheads, Marabu's Ultra High Viscosity and Kammann's digital print innovation, creating embossed effects on glass bottles and other packaging at a laydown build height up of to 3mm, without compromising on the intricate details of the embossing and sharp contour edges, is now possible. This innovation has been driven through the collaboration of all three partners, with printhead manufacturer, ink supplier and machine builder using their expertise to open new possibilities that traditional analogue printing methods cannot deliver.
The new inks are opening eyes to new potential for inkjet printing. Xaar’s Group R&D Director, Karl Forbes highlighted some of these opportunities as part of a talk titled, ‘Seeing is believing’ at FuturePrint Tech’s ‘Digital Print for Manufacturing’ conference. Visitors saw the results of independent research from Swansea University showing the impact that high viscosity inks can have in traditional print applications with Xaar’s Ultra High Viscosity Technology.
“By improving print quality at higher speeds with less ink and energy required, the ability to jet a wide range of high viscosity, high particle loaded fluids is driving change on many levels,” said Karl.
“The collaboration between all our businesses to deliver innovation in decorative printing is a prime example of what Ultra High Viscosity is enabling. I have no doubt that this project is just the start, and the combination of new ink chemistries, machine know-how and our printheads will deliver fundamental change to many industries over the next few years.”
Ends
About Xaar
Xaar is an inkjet innovator, providing printheads and technologies for OEM and UDI customers worldwide.
By helping customers lay down precise volumes of inks and fluids with absolute pin-point accuracy, time after time, Xaar’s inkjet printheads and technologies meet the needs of numerous markets. Covering graphics, labelling, direct-to-shape, packaging, product decoration, ceramic tile and glass decoration, décor, and outer case coding applications – as well as printing with specialist functional fluids for advanced manufacturing techniques.
Collaboration is at the very core of its business. Xaar works as a trusted partner from sites in Europe, China, and North America, providing expert insights and technical support every step of the way.
With over 30 years’ experience, around 300 patents registered or pending, and major ongoing R&D investment, Xaar’s digital printhead and precision jetting technologies create infinite opportunities for today’s sustainable manufacturing innovation.