Leybold: hygienic enclosures for vacuum ...
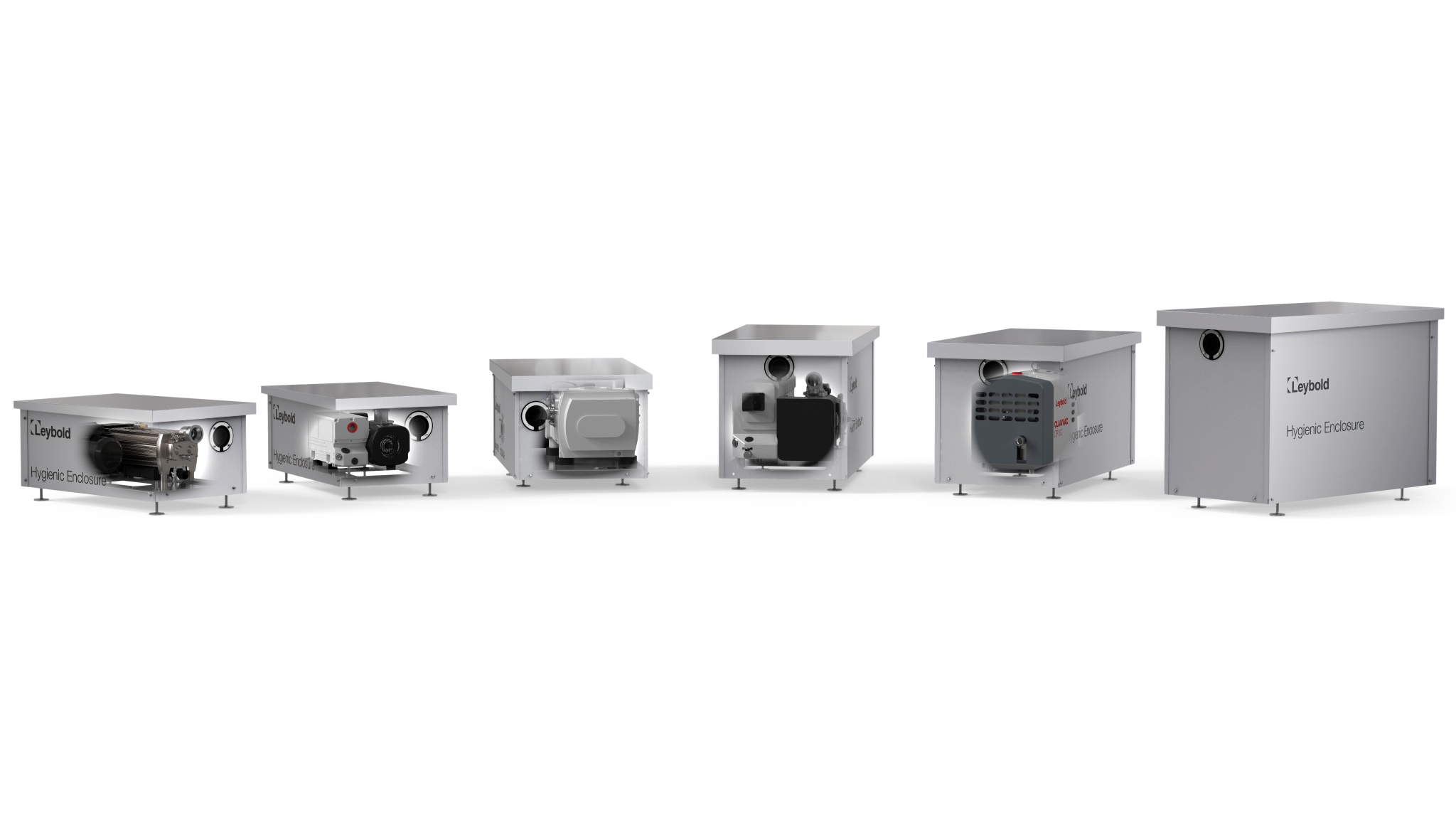
Ergonomic packaging material handling using lifters
Munich / Düsseldorf, XX March 2020 +++ Heavy lifting and repeated one-sided movements put employee
health at risk in production, warehouse and logistics. The consequences are excess strain and back pain,
along with the high sickness rates this causes. The Danish company Hovmand presents ergonomic
solutions for safe load handling at Interpack in Düsseldorf (Hall 11, Stand B15). Companies in the
packaging industry can obtain advice at the stand on the subject of ergonomics relating to their own
specific workplace needs.
At the international trade fair for packaging and process engineering, Danish manufacturer Hovmand will be presenting
its mobile battery-powered lifters made of stainless steel or aluminium. These guarantee low-impact work processes
that reduce the strain on the spine, joints and muscles. With the help of an industrial lifter, one person on their own
can grasp, lift, transport, turn and tilt loads of up to 300 kg safely and in compliance with applicable occupational safety
regulations. For example, reels of film can be removed from the pallet, transported to their destination and inserted
directly into the packaging machine. This makes it possible to use of larger reels, thereby reducing downtime on the
packaging machine; because the reels are stacked higher, warehouse capacity can be used more efficiently, too. All this
ensures smooth processes while at the same time reducing the risk of accidents and production downtime costs.
Analyse your own need for action in advance
Although many occupational health and safety measures have been defined in EU Directives, they remain noncompulsory to date. This situation can change very quickly, however. For this reason, Hovmand has developed a webbased “Ergonomics Check”. Companies in manufacturing industries can use this to analyse the day-to-day strain on
their own employees in the run-up to Interpack. The compact self-test can be accessed via the company's website:
within a few minutes, an assessment is carried out whether and to what extent there is a need for action in terms of
ergonomics at the workplace, based on nine questions. At Interpack, experts at the Hovmand stand can provide advice
on the results of the ergonomics check and configure an individual lifting solution if any action is required.
Safe reel handling with different reel sizes
Another topic at Interpack will be Hovmand’s newly developed flexible lifting equipment: Flex Fork and Double Boom,
rotating fork and a crane arm solution. The stand will feature an IMPACT 130 lifter with a Flex Double Boom for
transporting reels of film, which can be raised from the bottom using this piece of lifting equipment. “The special
feature here is the underlying carriage construction – this means that customers themselves can conveniently adjust
the width to suit different reel sizes during use,” explains managing director Søren Hovmand. Normally, handling
different crate widths and reel sizes requires investment in an additional device. The variable adjustment options
provided by the Flex Double Boom eliminate these additional costs.
Hovmand always aims to make its lifting equipment as modular as possible: “In this way we’re able to avoid timeconsuming and cost-intensive customisations and offer a wide range of lifter configurations for occupational health and
safety that are individually tailored to meet the respective requirements. This gives our customers access to serially
produced solutions that are more flexible and cost-effective,” says Søren Hovmand.
Hovmand GmbH
Rupert-Mayer-Str. 44
D-81379 Munich
www.hovmand.com
T: +49 (0) 89 785 76 76 0
E: mail@hovmand.com
In order to select the right lifting solution from over 100,000 configuration options, Hovmand has developed a Virtual
Engineering App. With its integrated environment scan and the latest Apple ARKit™ technology, Hovmand's sales
department can use the app to configure the lifting aid on site at the prospective customer’s premises and display it live
in 3D in the workspace.
The ergonomics check can be accessed via the following link: https://www.hovmand.com/de/ergonomie-check
ABOUT HOVMAND
Hovmand is the world's leading manufacturer of mobile battery-operated lifters made of stainless steel and aluminium,
providing significant support for ergonomic operations in production, warehouse and logistics. The focus here is on
solutions for improved occupational safety. The Danish family company with sales headquarters in Munich has been
developing, producing and selling lifting and transport equipment for more than 45 years. Its mobile and modular lifters
facilitate the day-to-day handling of heavy loads such as crates, drums, reels and kettles. Hovmand supplies companies
in the industrial, pharmaceutical, chemical, cosmetics and food production sectors. Søren Hovmand is the owner and
managing director of the company, which was founded in 1972.
For further details, see: www.hovmand.com.
PRESS CONTACT
Natalie Lumma
Carta GmbH
Iggelheimer Str. 26, 67346 Speyer
Tel.: +49 (0) 6232 100 111 25
E-mail: lumma@carta.eu
Web: www.carta.eu
COMPANY CONTACT
Janet Reichel, Head of Marketing
Hovmand GmbH
Rupert-Mayer-Str. 44, 81379 München
Tel.: +49 (0) 89 785 76 76 40
E-mail: jrl@hovmand.com
Web: www.hovmand.com
Cologne, 11.03.2020 – Low-noise, oil-free vacuum solutions, energy efficiency and optimized data evaluation are the requirements in analytics and the associated research and laboratory environments, such as mass spectrometry. Vacuum technology functions almost as a heart in most systems, as it enables processes to run. Often however, little attention is paid to the correct choice of vacuum components, which is nevertheless an essential factor for the efficiency of analytical or even manufacturing processes.
Oil-free vacuum is the method of choice here. With the ECODRY series, Leybold offers a clean, silent, compact and low-maintenance pump for use in analytical or research laboratories. This pump class lies exactly in the transition area between small laboratory devices and large machines. However, the most significant innovation is undoubtedly the reduction of the noise level: "The pump is compact, low-vibration, powerful, easy to operate and very quiet in its design", states Product Manager Alexander Kaiser.
The ECODRY plus was developed exactly in line with the requirements of systems such as mass spectrometers and electron microscopes. It is therefore also suitable for use in large accelerators, because there is no contamination by dust or oil. It offers users a high degree of comfort, pumping speed performance and flexibility.
Equipped with two flexible interfaces, the pump can also be remote-controlled. When used in commercial analysis systems, it is often integrated into the plant control system and can be started, stopped, varied in speed and also monitored as required.
Pictures: ECODRYplus - Copyright Leybold
The devices of the TURBOLAB series are plug-and-play high vacuum pump systems and offer a wide range of variants: They are compact, fully assembled and can be put into operation immediately. Different configurations cover the vacuum requirements of applications in the R & D markets and analytical applications. The unique oil-free hybrid bearing of the TURBOVAC i/iX turbopumps and the choice of different dry-compressing fore vacuum pumps allows hydrocarbon-free operation. These compact pump systems are delivered fully assembled and ready for operation.
They include a turbomolecular pump, a backing pump and an innovative TPU display unit. Both compact tabletop and mobile cart versions are available and offer flexible and convenient operation. Installation kits for variable mounting of the turbopump away from the pumping station frame can also be obtained.
A wide range of accessories, such as sealing gas and / or venting valve, backing vacuum safety valve, cooling unit, heating tape, etc. facilitates the adaptation to individual requirements.
Pictures: TURBOLAB Variants and TUBOLAB DATA Viewer - Copyright Leybold
Today, data and its correct interpretation are essential factors in machine-based research and development, but also in manufacturing. Therefore, the measurement technology associated with vacuum technology is crucial for the evaluation of processes from basic research to industrial manufacturing. Leybold therefore offers a wide range of measuring instruments, sensors and components.
systems can be equipped with THERMOVAC TTR fore vacuum gauges and PENNINGVAC PTR high vacuum sensors. Connected sensors are detected and pressure readings are automatically shown on the display.
All critical parameters and operating conditions such as errors, warnings, frequency, temperature etc. are automatically recorded in an internal memory based on a standard time interval and can be adjusted by the user directly on site. An integrated web server allows remote control, monitoring and configuration of the TURBOLAB devices from the mobile device or from the computer via browser.
A full portfolio of sensors and controllers makes the measurement and control of processes easy. Leybold offers real innovations with its sensors for vacuum measurement in numerous applications in the pressure range of 2000 to 10-12 mbar.
These measuring devices offer higher precision, an extended measuring range, improved reproducibility and process stability. They complement the portfolio with novel interfaces and additional areas for use in lock chambers.
Leybold offers sensors of various designs with their own characteristic measuring ranges. A distinction is made between direct and indirect pressure measurements.
These gas type independent vacuum sensors cover measurements directly and mechanically:
▪ capacitive CERAVAC measuring devices and
▪ capacitive DI/DU and piezo pressure sensors
The indirect, gas type dependent pressure measurement is possible with the sensors
▪ THERMOVAC, a thermal conductivity vacuum gauge according to Pirani ▪ PENNINGVAC cold cathode ionization vacuum gauges based on the principle of the reversed magnetron. ▪ IONIVAC hot cathode ionization vacuum gauges according to Bayard-Alpert
The controllers of the Graphix and Display series complete the range of accessories.
Leybold offers from one source everything from consulting to after sales options to support the customers in achieving their goals.
For further information:
Christina Steigler
Corporate Communication
T: +49 221 347 1261
F: +49 221 347 31261
christina.steigler@leybold.com
About Leybold Leybold is a part of the Atlas Copco’s Vacuum Technique business area and offers a broad range of advanced vacuum solutions for use in manufacturing and analytical processes, as well as for research purposes. The core capabilities centre on the development of application- and customer-specific systems for the creation of vacuums and extraction of processing gases. Fields of application are secondary metallurgy, heat treatment, automotive industry, coating technologies, solar and thin films such as displays, research & development, analytical instruments, food & packaging, as well as a multitude of other classic industrial processes.
About Atlas Copco Great ideas accelerate innovation. At Atlas Copco, we have been turning industrial ideas into business-critical benefits since 1873. By listening to our customers and knowing their needs, we deliver value and innovate with the future in mind. Atlas Copco is based in Stockholm, Sweden with customers in more than 180 countries and about 37 000 employees. Revenues of BSEK 95/ 9 BEUR in 2018. For more information: www.atlascopcogroup.com
Oberdiessbach, Switzerland – Hoffmann Neopac, a global provider of high-quality packaging for a broad array of industries and applications, will debut DigitAll360°, its new direct-to-shape digital decoration service for tubes, at Luxepack New York, May 6-7. DigitAll360° was developed to address growing industry demand for high-quality variable printing, precision color matching, flexible batch sizes and expedited delivery.
DigitAll360° prints photorealistic graphics and text on the entire surface of cylindrical containers. Available for a wide variety of substrates and almost unlimited color palettes, DigitAll360° offers benefits that include:
Unparalleled all-around decoration: True to its name, DigitAll360° offers 360° decoration with no slit or overlap, and also delivers outstanding on-cap, seam and shoulder printing. As impressive as where it can print is what it can print: highly opaque whites and glosses, vividly displayed to make products stand out from competitors.
Unprecedented digital color matching: DigitAll360° can employ up to 10 simultaneous colors and select lacquers at up to 600 DPI resolution. This ultra-wide color gamut and micron-level color registration yields photorealistic images and superb color matching ideal for half-tones, gradients and other special hues.
Digital-level variability: Digital printing also makes variating decorations or text far more economical. From mosaic printing, promotions and prototypes to packages printed in different languages, DigitAll360° offers unsurpassed versatility.
Quick delivery: Neopac can deliver DigitAll360° products on short lead times, a consistent industry challenge for printing with this level of style, sophistication and brand impact.
Increased Sustainability: From initial decoration to product manufacturing to consumer recycling, DigitAll360° delivers major sustainability enhancements and reduces environmental footprint throughout product lifecycles.
New SpringTube™ Maintains Shape for Aesthetic and Decorative Advantages
Also at Luxepack New York, Neopac will features its new SpringTube™, a packaging solution for cosmetics and personal care products. Developed by subsidiary 3D Neopac, the tube is specially designed to maintain its shape while delivering a host of additional benefits for consumers, brand owners and manufacturers.
Featuring a tamper-evident, push-on flip-top cap, the printer-friendly SpringTube™, can be decorated via digital, flexo and metallic foil processes. For product protection, an ethylene vinyl alcohol (EVOH) barrier preserves oxygen-sensitive formulas, and helps extend the shelf life of beauty and personal care products.
# # #
About Hoffmann Neopac
Hoffmann Neopac is a privately-owned company, headquartered in Thun, Switzerland. The group produces high-quality metal and plastic packaging in six locations: HOFFMANN tins in Thun and CMP tins in Holland; Polyfoil® and plastic tubes with NEOPAC in Switzerland, Hungary and the US; and 3D Neopac in India. Its longstanding customers include internationally active pharmaceutical, cosmetics and consumer goods manufacturers in the European, North American and Asian markets.
Including its new production facility in the United States, Neopac employs around 1,250 employees and has a capacity of 1.3 billion tubes. The company is dedicated to sustainability in both its manufacturing processes and corporate culture, including a dedicated eco-conscious packaging portfolio. For more information, visit www.neopac.com.
Neenah, Wis. – Amcor, a leader in global consumer packaging, works with the world’s leading brands to conceive, build and commercialize innovative, increasingly sustainable and recycle-ready packaging that wins with consumers and industry experts, alike.
This year, Amcor celebrates two gold and six silver Flexible Packaging Association (FPA) Achievement Awards with five customers: MITG, Predilecta Sacciali, Cargill, Full Moon, and Tyson.
“It’s exciting to be recognized for developing and producing new, leading packaging formats for our customers in food, pharmaceutical, and home- and personal-care,” said Amcor Chief Technology Officer William Jackson. “It’s even more exhilarating – as sustainability becomes an increasingly important design feature – to offer innovative products, services and processes that create winning outcomes for our customers, consumers and the environment.”
The FPA Achievement Awards have been showcasing industry innovation and advances that have changed the packaging industry since 1956. For recognition in expanding the use of flexible packaging, technical innovation, sustainability, printing and shelf impact, and packaging excellence, this year’s nominations included more than 200 entries across 73 package samples; delivering only 48 achievement awards across 30 packages, including:
“What makes this technology so exciting is the ability to confirm seal strength in real time,” said Jackson. “Then, through ETO sterilization, the color is reversed so there is no visual difference for the end-user.”
Group strategy driven by the challenge of assembly in the Closures field, resulting in the takeover of one of Europe's leading companies in this industry. The goal? To bring about new, immediate product and market synergies
SACMI recently purchased Abruzzo-based Velomat, a leading designer and manufacturer of high-speed assembly machines for caps, micro-pumps and medical devices. Completed on 19th February, this takeover is part of a broader strategy by SACMI - the world's leading provider of closures-beverage solutions - to expand and diversify opportunities in the industry in light of recent regulatory, product and market developments.
"The industry", explains the President of SACMI Imola, Paolo Mongardi, "is evolving towards multi-line and multi-material solutions that require careful assessment of the technology package in order to meet production requirements. Rising to that challenge will involve research into both new materials/solutions and component assembly: and when it comes to the latter, Velomat is just the firm we've been looking for to help implement our growth strategy".
The world's leading producer of machines and complete plants for the manufacture of plastic and metal caps and capsules, SACMI has no intention of being anything less than fully equipped to face the challenges posed by today's closure market: "To give just a few examples", continues Paolo Mongardi, "just consider the new lines for complex aluminium-plastic caps/capsules or the new slitting solutions for tethered applications, all areas where there's significant, immediate synergy with Velomat's know-how and product range.
Now 70% SACMI-owned – with a 100% buyout option – the Abruzzo-based company already leads the way on European markets and is a key supplier to numerous sectors (not only food but also, but not mainly, pharma, housekeeping, cosmetics, etc.). The international SACMI Group has a turnover of 1.4 billion euros and a structured presence in 30 countries: joining its Global Network opens up major new internationalisation prospects for Velomat, with SACMI setting up new synergies and ensuring managerial continuity.
Currently a customised prototyping specialist, Velomat will, by joining the Group, be able to standardise its product range and aim it at a broader target by taking the global market as its frame of reference and becoming a stable component of the SACMI Group sales, production and assistance network.
From modular labellers to complete capsule, container and preform manufacturing solutions, plus a wide range for the chocolate and packaging industries. The watchwords: maximum flexibility and efficiency, with a sharp focus on sustainable packaging
SACMI is gearing up for Djazagro 2020, the international agro-industrial fair being held from 6th to 9th April 2020 in the city of Algiers. There follow five good reasons to visit the SACMI stand, which will be showcasing new, sustainable, versatile solutions that reduce the consumption of both energy and raw materials.
FlexiKube, market-leading versatility. With its latest range of FlexiKube labellers, SACMI has set a new standard for the medium-speed labelling sector. Developed for applications with output rates of up to 20,000 cph, the FlexiKube platform stands out on account of its capacity to handle - with maximum efficiency - multiple technologies and labelling systems, all on one platform. Alongside fully modular labelling stations (roll-fed, self-adhesive, cold glue, hot melt), the user-friendly FlexiKube platform has ultra-low maintenance requirements and offers the long-term reliability that stems from SACMI Beverage's unmatched know-how and experience.
Blo 2 Fill XL, a single large-format container stretch-blowing and filling interface. This solution completes the SACMI range for sizes of up to 12 litres. All models are designed to operate directly on the line with SACMI electronic-volumetric fillers. In the Blo 2 Fill configuration, the system allows for the control of both stretch-blow moulder and filler - preform insertion and extraction included - via a single HMI panel, without any need for mechanical set-up.
CCM, the advantages of first-class technology. Shorter cycle times and lower energy consumption, independent control of individual cavity-moulds, flexibility as regards employed resin type and quantity: three key factors that have made CCM a huge success. Now, this closures compression press range is available for multilayer applications (single-serve capsules) and, thanks to integration with the anti-tamper band slitting solution, tethered applications too. Processes that use lower quantities of virgin material and also utilise compostable resins are just two advantages of an intrinsically superior technology that SACMI has now applied in the adjacent sector of container production (CBF, compression blow forming), most notably in the pharma and dairy sectors.
IPS, new horizons for sustainable PET. What makes the latest generation of SACMI injection presses so outstanding is their ability to operate - to the highest standards of productivity and efficiency on the market - with 100% recycled PET (and raw materials in flake form in quantities as high as 50%). Easily recycled, PET is playing an ever-greater role in the drive towards sustainable packaging. The advantages of the SACMI range include the ability to process recycled resins with standard machines, thus ensuring outstanding reliability, efficiency and process performance.
Packaging&Chocolate, the 'sweet side' of SACMI. For many years now, Djazagro has been a first-class showcase for SACMI's Carle&Montanari, OPM and FIMA brands, providers of first-class solutions for the processing and packaging of chocolate and other confectionery products.
Offering all the skill and reliability that stem from over a century of experience, SACMI Packaging&Chocolate is the ideal partner for start-ups and established chocolate producers alike that are looking for a skilled sole provider who can guide their choices and provide support throughout the entire process. Alongside a new range of chocolate preparation and moulding solutions (a sector in which the Carle&Montanari brand has led the way for over 50 years) customers can now count on new robotized solutions for wrapping, primary and secondary packaging, with a range that, in secondary packaging, extends to other food and non-food products.
Come and see us at Djazagro 2020 (stand #CT F076). The SACMI team will be at your disposal to illustrate the full range of solutions and the advanced assistance package that SACMI Customer Service provides before, during and after the sale.
SACMI. Leading the way. Worldwide.
For manufacturers and retailers of natural and organic products, the uniformly positive eco-balance of their products is an important competitive factor. When deciding on their packaging tape, they therefore prioritise the use of cardboard packaging made from corrugated cardboard. The gummed tapes from Schümann have established themselves as closing products that are as secure as they are sustainable. As they consist of paper and potato starch and nothing else, they are the natural partner for cardboard. In Hall 6 of the Biofach 2020 (12–15.2.2020), Schümann will be presenting its full range of environmentally-friendly packaging tapes.
Stadtallendorf, January 2020. – As the industry event for the manufacturers and providers of natural products and sustainable packaging equipment, the Biofach trade fair in Nuremberg is now a force to be reckoned with. In 2020, it is taking place for the 31st time, and the company Schümann – a long-standing manufacturer of packaging tape for cardboard packaging and paper bags – has been attending for several years. This time, the key focus of its exhibition programme is on the presentation of its environmentally-friendly gummed tapes for the dust-tight and tamper-proof closure of corrugated and solid cardboard packaging. After all, among the manufacturers of both natural and organic products, and in the areas of online retail, wholesale and stationary retail, these packaging closing tapes made from paper and potato starch are now considered to be the preferred form of packaging tape. As they integrate perfectly in terms of the materials, they are the natural partner for the cardboard packaging and support the achievement of coherent and holistic eco-balances. In other words: when using the gummed tapes from Schümann as packaging tape, the entire packaging of the product gains in terms of sustainability. Furthermore, the analogy between the contents of the parcel and the packaging increases the overall credibility of an offer in the eyes of the end customers, who are frequently very critical.
With or without reinforcement
At its trade fair stand 281 in Hall 6 of the Biofach, Schümann will be providing an overview of its full range of gummed tapes. In addition to its unreinforced packaging tape for small and lightweight packaging, the company will also be showing the reinforced packaging tapes from its Green Line range, which are recognisable at first glance with their green core. The especially successful gummed tapes in this group include, among others, the Green KF/KF2 gummed tapes for medium-weight cardboard packaging, as well as the Green MAX7, which is designed for the closure of heavy-duty packaging. The key factor here: all the gummed tapes in the Green Line have reinforced filaments made from natural raw materials. The filament layer is consistently integrated in the gummed tapes so that the cardboard packaging is further stabilised. This can play a decisive role in the packaging used for bottles, glass and other fragile products in particular.
Tampering becomes visible
One of the key strengths of the gummed tapes from Schümann is that they provide packaging with an exceptional high degree of safety against tampering and unauthorized opening. This also takes place on a one-hundred-percent ecological basis: the natural glue used in the paper strips, which is based on potato starch, creates an inseparable material composite seal with the corrugated or solid cardboard packaging immediately after its application, and can only be removed with destructive force. Therefore, if an attempt is made to open the package with criminal intentions during its transport, such unauthorised handling remains visible as tampering. The moistening of the natural glue and the application of the gummed tape to the cardboard can take place either manually or with automated equipment.
For the substrate material of the gummed tapes from Schümann, Kraft paper is used, the production of which prioritises the use of wood that originates from sustainably managed forests in the EU. And with the printing of the top side of the packaging tape with text, logos or ID codes, exclusive use is made of soluble inks. The packaging tapes from Schümann can be disposed of and shredded together with the used cardboard in one go, and without any further separation of the materials.
Ideal for various premium organic and specialty products, latest member of Neopac’s EcoDesign portfolio comprises 100% recycled steel, aligning with circular economy sustainability.
Thun, Switzerland – Hoffmann, a global provider of high-quality packaging for a broad array of industries and applications, will introduce a new line of tinplate cans comprised of 100% recycled steel at the Interpack, May 7 to 13, 2020 in Düsseldorf, Germany. Made possible by collecting separated consumer packaging steel from standardhousehold recycling, the company’s groundbreaking RecyCan® portfolio essentially closes the loop on sustainability through packaging that is not only completely recycled but also perpetually recyclable.
All tinplate cans contain some recycled steel. At the inception of the RecyCan process, typical household steel like used cans, closures and crown corks are collected for recycling. After steel elements are separated from aluminum and plastic packaging via magnet, they are shredded and detinned before being pressed into cubes. They are then melted down to raw steel and cast into slabs. The slabs are hot-rolled, cold-rolled and tin-plated to produce packaging steel, which can be printed and formed into fresh new tinplate packaging cans.
Ideal as packaging for a variety of premium organic and specialty products including organic infant nutrition, coffee, tea, dry or pasty cosmetics and tooth powder, Hoffmann’s RecyCan® tins are available as three-piece, two-piece or deep-draw cans that provide ample protection against light, air/oxygen and moisture. In addition to being fully recycled and recyclable, the fully circular packaging solutions offer a host of other eco-friendly benefits, including the savings of raw materials.
“In Europe, North America and other major markets, metal tins are synonymous with sustainability as they are recycled in well-established recycling streams,” said Mark Aegler, CEO of Hoffmann Neopac AG “The RecyCan® line of products takes eco-consciousness to the next level by achieving full circularity – completely recycled products that can continue to be recycled. And of course, these environmental benefits are achieved without sacrificing product protection or branding aesthetics.”
# # #
About Hoffmann Neopac
Hoffmann Neopac is a privately-owned company, headquartered in Thun, Switzerland. The group produces high-quality metal and plastic packaging in six locations: HOFFMANN tins in Switzerland and Holland; Polyfoil® and plastic tubes with NEOPAC in Switzerland, Hungary and the US; and 3D Neopac in India. Its longstanding customers include global pharmaceutical, cosmetics and consumer goods manufacturers in the European, North American and Asian markets.
Including its new production facility in the United States, Neopac employs around 1,350 employees and has a capacity of 1.3 billion tubes and 300 million tins. The company is dedicated to sustainability in both its manufacturing processes and corporate culture, including a dedicated eco-conscious packaging portfolio.
For more information, visit www.hoffmann.ch.
Visuals:
Picture of a RecyCan® Product
Infographic of Recycling Process
Picture of a steel coil
Video links: https://www.youtube.com/watch?v=ntiChn2NTFA
Hod-Hasharon, Israel, 27th February 2020 - Hats off to SC Plastica SRL, a Romanian packaging specialist coming up to its 30th year, for its long history of visionary investments.
Founded as a family company in 1992 by Ioan Holdis and his wife, Plastica originally focused on producing polyethylene packaging. Then, as the market developed and Plastica won large retail jobs, the Holdis family realized they would need to invest in state-of-the-art printing equipment. Several rounds of major investments between 1997 and 2013 were instrumental in propelling the company toward its current focus on producing packaging for the pharmaceuticals, food and agricultural products industries.
Looking beyond printing capabilities
Having acquired some of the most advanced printing and laminating solutions available, Plastica soon saw that its printing equipment lacked vital capabilities in the areas of print process control and error detection, tracking, selection and marking. Ioan Holdis, Plastica’s General Manager, says they decided that the next investments would have to bring them those missing capabilities.
Fast-forward to 2018, when the Plastica management team decided to make new investments, this time, to help control and optimize the entire production process. A review of the market soon drew Plastica’s attention to AVT, a leader in print process control, quality assurance, and press control.
At that time, the company added an AVT Argus Turbo HD 100% Inspection system to its existing Comexi printing press, to detect, record, mark and eliminate defects in the production process.
Dramatic bottom line benefits
Soon after installation, the AVT system’s advantages were strongly apparent. Mr. Holdis says: “With this easy-to-operate system, we were able to reduce production costs by 25%, increase productivity by 30%, and also reduce preparation time for all jobs.”
The clear benefits of the AVT Argus Turbo HD installation prompted Plastica to invest in additional AVT solutions. First, Plastica added AVT’s Workflow Link to connect its printing and finishing equipment. Then, it installed the AVT Apollo Multi-Stop inspection and waste control solution.
“Through these AVT solutions, we eliminated all the faults we had in the production process. As a result, customers are now 100% satisfied with the delivered products,” notes Mr. Holdis.
“We now have 100% print inspection and 100% error detection. With these advantages, we are able to produce more, and we have completely eliminated the risks of non-compliant products.”
Ultimately, the printed film rolls are delivered to the customer without any defects.
“With AVT, we have managed to deliver the perfect package and achieve 100% customer satisfaction.” concludes Mr Holdiș.
Watch this video to see how Plastica has done it all, with AVT.
A word about Plastica’s AVT solutions:
The Argus Turbo HD automatic 100% inline Inspection, AVT’s flagship solution, delivers a unique combination of 100% high-resolution print inspection and superior zoom process control, to detect imperfections in real-time.
AVT’s Workflow Link is the link between printing and finishing. It automatically stops the rewinder at the relevant defect location for fast and efficient waste removal, to ensure shipment of defect-free material.
The Apollo Multi-Stop is an inspection and waste control solution offering unprecedented rewinder workflow integration and efficiency at both high resolution and high speeds.
About AVT
AVT is the global leader in print process control, quality assurance, and press control for the packaging, labels, and commercial print industries. With more than 8,000 AVT systems installed worldwide, our integrated solutions empower converters and printers to enhance print quality via automatic online and offline inspection and sophisticated color measurement and control, synchronized with other vision-centric press controls. With this, our solutions address key industry challenges, including lack of automation, long production setup cycles, waste materials, increasingly stringent demands for image quality and inadequate process and quality control.
AVT is headquartered in Israel and has subsidiaries in Europe, Asia, and the U.S., where we also have a network of marketing, sales and customer support teams. Our global team of skilled and experienced engineers brings together experts in understanding of image processing, color science, electro-optical design and printing press systems, coupled with software and hardware development. We are part of the Product Identification Platform of Danaher Corporation, a global science and technology innovator.
For more information, please visit https://www.avt-inc.com.
About SC PLASTICA SRL
Plastica is a family owned company, located in Satu Mare, in northwestern Romania and it was founded more than 28 years ago, having as main activity the production of flexible packaging. Today, the company is still managed by the founder, together with the second generation and it can offer a wide range of packaging solutions based on its full production operations like: extrusion, flexographic printing, lamination, slitting & finishing, converting and recycling.
Thanks to its efforts to constantly keep up with the latest innovations in the field and major investments in advanced technology, Plastica has become one of the most appreciated and demanded flexible packaging companies in the country, being among the top premium packaging manufacturers in Romania.
Plastica offers a wide range of products like PE and PP blown extruded films, shrinkable films, barrier films, printed & laminated films, labels, shopping bags, biodegradable and compostable bags, waste bags, tissue paper bags, toilet paper bags, diaper bags, hygiene bags, courier bags, wicket bags, pouches, industrial sacks, for several markets and applications (food, beverages, hygiene & personal care, detergents, pet food, agriculture, constructions, textiles & clothing, automotive, e-commerce & shipping).
For more information, please visit http://www.plastica.ro.
AVT contact:
Hagit Rozov Paz
Director of Marketing Communications
Office: +972 52 894 1558
Email: hagitr@avt-inc.com
Press contact:
Ingrid Van Loocke
PR Director @pr4u
Mobile: +32 478 514 415
Email: Ingrid@pr4u.be
Gebr. Becker GmbH is expanding its range of rotary vane vacuum pumps in the O5. series by the sizes O 5.10, O 5.16 and O 5.21. These pumps have been specially developed for applications in the food packaging industry. The pumps have a maximum flow rate of 10 to 23.5 m3/h.
The extremely compact design of the new vacuum pumps is one of their design features: All three pumps have a construction height of only 160 mm. This opens up the possibility for manufacturers, especially of tabletop packaging machines, to build machines with smaller dimensions and to achieve better ergonomics. The almost identical dimensions also allow a modular machine setup: All three pumps can be optionally integrated in the same machine. This gives the machine builder flexibility and also gives the user additional options when selecting the machine.
The pump design is also based on modularity: All three models can be optionally equipped with a small or large oil tank and motors with a different power output. From the perspective of the machine manufacturer, this makes it possible, for example, to offer the option of a premium version with a bigger oil tank and a correspondingly larger air de-oiling element, in addition to a compact basic version with a smaller oil tank, which enables not only longer maintenance intervals but also increased water vapour tolerance. The oil tanks can be split for easy, residue-free cleaning of the tanks.
Thanks to the modular design, Becker can also offer the user of the new vacuum pumps various options for the position of the oil filler opening, oil drain and oil sight glass. This simplifies both the service process and the 1 to 1 substitution of the O5. series in existing machine designs. The innovative and patented twist-lock on the air de-oiling element ensures quick replacement and maximum serviceability.
Regardless of the size and equipment chosen, the pumps in the O5. series stand out with their robust design and highly reliability. Neither low ambient temperatures or contaminants in the oil or frequent start-stop cycles without a long lead time affect their service life. Another feature is the quiet opera-tion, which is achieved by the special geometry of the discharge valve.
With these features, the new Becker rotary vane vacuum pumps in the O5. series, first introduced at the IFFA 2019, are ideally suited for the vacuum packaging of fresh or perishable products (meat, fish, sausage and cheese) as well as for other applications in which reliable and efficient vacuum generation is required.
One of the pilot users of the O5. series is VAMA Maschinenbau GmbH in Wilpoldsried, a leading supplier of vacuum chamber machines for the food industry and other user industries. VAMA considers the requirements that the company places on vacuum pumps to be implemented very well in the O5. series: Managing director Kurt Hörburger: “We need pumps that are characterized by compact dimensions, running smoothness, quiet operation and high reliability. The rotary vane pumps from Becker have this broad property profile.” That's why VAMA already uses the new pumps: Gebr. Becker's IFFA booth exhibited a compact VAMA table-top vacuum chamber machine, which generates the vacuum with an O 5.16 type pump.
Contact person:
Lars Brandstäter
Marketing Manager
Telephone: +49 202 697 2310
E-mail: brandstaeter@becker-international.com
London, 24 February 2020 - SharpEnd, the London-based Agency of Things™, has signed a strategic partnership with Guala Closures Group, a world-leading manufacturer of closures for spirits and wine, and pioneer in connected caps.
The deal consists of the initial acquisition of 20% of shares of SharpEnd by Guala Closures, with potential further capital injections in the company. Guala Closures will remain a minority investor while Cameron Worth, SharpEnd’s founder and current sole shareholder, will retain the majority of the company’s shares.
Guala Closures is a pioneer in connected closures with its NěSTGATE™ proprietary technology, enabling industrial use in supply chain management as well as consumer engagement programmes.
Founded in 2015 as the world’s first IoT agency, SharpEnd is known for being a pioneering creative technology partner with an appetite to push the boundaries of consumer engagement with a global client list including AB-InBev, PepsiCo, Nestlé, Unilever and Pernod Ricard. This partnership enables SharpEnd to continue this journey and accelerate its growth strategy through Guala Closures’ backing.
SharpEnd and Guala Closures already have a consolidated relationship based on their ground-breaking work together on NFC-enabled closures. Most recently, they partnered with Californian wine brand Böen, the first United States wine brand to deploy NěSTGATE™ NFC technology. By simply tapping the cap with their smartphones, consumers are taken to an interactive farmhouse with a range of content experiences.
Guala Closures’ investment in a strategic partner follows its intent to provide turnkey solutions to customers by becoming a technology integrator of connected packaging solutions. SharpEnd will scale up the development of its IoT software platform to be implemented by GCL’s clients, extending to supply chain management, stock management, theft prevention and ultimately product security, anti-tampering and forgery prevention.
Paolo Ferrari, Guala Closures Group Chief Marketing Officer and M&A Director, says: “SharpEnd’s expertise will allow us to accelerate our Internet of Closures strategy development to help our clients provide better brand experiences to their consumers via the most advanced digital marketing solutions, turning data into valuable consumer insights.”
Cameron Worth, CEO and founder at SharpEnd, adds: “The partnership with, and growth capital from, our friends at Guala Closures gives us access to their vast R&D facilities and accelerates everything we are doing across creative technology and data in key verticals such as fashion, FMCG, spirits and cosmetics.”
ENDS
Notes to editors
About SharpEnd
SharpEnd is moving brands closer than ever to consumers by connecting packaging, retail and experiential activity. You can find out more at https://wearesharpend.com
About Guala Closures Group
Guala Closures Group has more than 4,700 employees and operates in 5 continents through 30 production plants and markets its products in over 100 countries. The Group sells nearly 20 billion closures each year with a 2018 turnover of 543 million Euros. Thanks to a policy of continuous business development and technological innovation, the Group is recognized as a global benchmark in the production of alcohol safety closures and is a leading manufacturer of aluminium closures for spirits, wines and beverages. From August 2018, Guala Closures S.p.A. has been listed on the STAR segment of the Italian Stock Exchange, entering the FTSE Italia Mid Cap index in September 2019.
Find out more on www.gualaclosures.com or on www.nestgate-gualaclosures.com
For more information contact:
Guala Closures Group Press office
Elisa Mendicino
T +39 02 8545 7089
elisa.mendicino@havaspr.com
SharpEnd Press office contacts
Bhavna Mistry: bhavna@velvetpr.biz 020 8996 1802
Stuart Heckford: stuarth@velvetpr.biz 020 3 176 6996
Information:
When cutting edge packaging technology combines with inspirational design to create genuine brand differentiation, the teams behind a development can take justifiable pride in the achievement. After securing a gold trophy 2 months ago, Trivium Packaging’s original metal can designs in 2019 for Gaya Coffee gained the company the added satisfaction of a much coveted 2020 iF Design Award.
The highly competitive awards, now in their 67th year, attracted a record entry of 7,298 innovative products that were launched in 2019, making life very challenging for the 78 distinguished international judges. They had no hesitation in declaring the Gaya can a winner in the Packaging Discipline.
Manufactured at Trivium’s manufacturing plant in Deventer, the Netherlands, for its Dutch customer Concept Drinks, the exquisitely-designed shaped can was made possible by several innovations along the supply chain. Notable was the expansion of the can size by an impressive 26 per cent under 40 bar pressure to achieve the desired shape.
Another distinguishing feature of the patented design is gold printing on both the lid and the base of the can, complementing the gold speckled printing over the sophisticated dark green body.
Guus Backelandt, co-owner of Gaya Gold Coffee is thrilled with this latest award and adds, “Concept Drinks came to Trivium with a challenging concept where the packaging has to express the premium brand DNA of our product. Both Trivium’s technical know how and creativity, as well as constantly seeking the boundaries of what is technically possible, made this whole project such a success.”
Trivium’s Martin de Olde, Head of Marketing and Business Development in Europe views the accolade as an important milestone in contemporary metal packaging: “For the Gaya can to have won over the judges demonstrates the value of high quality metal cans as stylish and functional, able to fulfill the most demanding marketing, branding and environmental requirements.”
Notes to Editor:
• Trivium Packaging is a leading packaging manufacturer of infinitely recyclable, metal packaging for the world’s leading brands. Trivium has more than 60 locations worldwide, employs close to 8,000 people with sales of $2.7bn.
• First awarded in 1953, the iF DESIGN AWARD is the oldest independent design seal in the world. It is a symbol of outstanding design achievements that focuses on the innovative power of design.
Further information:
Josephine ter Mors
Head of Global Communications
E: jose.termors@triviumpackaging.com
New options for Logistics and CEP sector customers include a unit offering
six independent scales for dramatically increased throughput,
and a premium warehouse scale with predictive maintenance.
Lawrenceville, GA – WIPOTEC-OCS, a leading manufacturer and supplier of precision in-motion weighing and X-Ray scanning equipment, will feature a pair of accurate, high-throAt MODEX, WIPOTEC-OCS to Showcase
Two New Precision Catchweighers
ughput new catchweighers at MODEX 2020, Booth 9219, March 9-12, in Atlanta. Both scale systems offer premium weighing solutions for the logistics and courier, express & parcel (CEP) sectors.
Triple Scale Catchweigher: Six Virtual Scales in One
The new HC-FL-T Triple Scale Catchweigher combines three hardware scales into six virtual ones, each capable of operating independently – a feature permitting product gaps as narrow as 10” (250mm). The triple scale design delivers a 60% throughput increase at the same speed as a double scale design, while guaranteeing first-class performance and durability. Depending on product length, the triple scale catchweigher can weigh as many as three products simultaneously.
The HC-FL-T can accurately weigh up to 19,000 parcels/hr at transport speeds up to 3.4 m/s (670 ft/min). The use of a high-tech electro-magnetic force restoration (EMFR) weigh cell delivers a weighing accuracy of 50g even when running at top speed. within addition, the new AVC (Active Vibration Compensation) ensures even more precise weighing results in vibrational environments. The AVC solution filters environment-induced interferences out of the measurement results without any loss of speed and accuracy.
Precision Warehouse Scale Equipped with Precision Maintenance
Recently upgraded to incorporate predictive maintenance, the HC-Warehouse Scale offers unsurpassed precision and reliability. Available as single or multi-interval scales, EC-Warehouse units offer a maximum weighing capacity of 35kg and weight accuracy less than or equal to 5g – a level of precision made possible via WIPOTEC’s ultra-fast weigh cells whose technology is unique to its price range.
To maximize throughput, the HC-Warehouse allows exceptionally small gaps between weighed products. The unit is available with weighing belt lengths from 600-1,000mm, and belt widths from 400-700mm. A variety of system component options are available; such as a barcode reader, camera system, or dimensioning system.
New for 2020, the HC-Warehouse scale now offers predictive maintenance. Designed to reduce downtime, the system provides real-time reports on various machine metrics, giving operators advance notice of pending maintenance for weigh cell cleaning, calibration, belt line wear and tear and other issues.
# # #
About WIPOTEC-OCS, Inc.
WIPOTEC-OCS, Inc. is a leading manufacturer and supplier of precision in-motion product weighing, X-Ray scanning, product inspection, parcel dimensioning, package marking, and serialization and aggregation equipment. The company's weighing, inspection, and track and trace solutions serve applications in a broad array of industries, including pharmaceutical, food, chemical, cosmetics, healthcare, e-commerce and logistics.
Located in the Atlanta, GA suburb of Lawrenceville, WIPOTEC-OCS headquarters includes a demonstration showroom, customer application engineering labs, a spare parts warehouse, and state-of-the-art meeting and training rooms. The company is part of Germany-based WIPOTEC group, which employs more than 1,000 people worldwide and has been pioneering dynamic weighing solutions for more than three decades. For more information, call (678) 344-8300 or visit http://www.wipotec-ocs.com/us/.
Echternach – The industrial robot manufacturer FANUC and the automotive group BMW AG have signed a framework agreement for the supply of 3,500 robots for new production lines and plants. FANUC robots will be used in the production of current and future generations of BMW models. The first robots were installed at the end of 2019. Further robots will be used at German and international production sites of the BMW Group in the coming years. FANUC winning this project is an important milestone as a strategic partner of the BMW Group. The robot manufacturer is continuously investing in research and development as well as in the expansion of its service network to support its customers all over the world. Various FANUC robot models will be used by the BMW Group in the future – including newly developed ones that have been tailored to the customer's individual requirements. The robots will be primarily used in body shop construction and for the production of doors and bonnets. In cooperation with manufacturers of hose packages and traversing axes, FANUC is rounding off its range of supplies to the BMW Group by providing peripheral components. With over 110 robot models in the range, FANUC offers the widest range of robots for industrial applications worldwide. These include particularly powerful types such as the M-2000, which can safely carry loads of up to 2.3 tons and move them flexibly via its six axes. The company is not only successful in the automotive industry: more than 600,000 FANUC robots have already been installed worldwide across a wide range of industries.
About FANUC
The FANUC Corporation is one of the worldwide leaders in factory automation for CNC control systems, robots and production machinery (ROBODRILL, ROBOCUT, ROBOSHOT and ROBONANO). Since 1956, FANUC is the pioneer in the development of numerically controlled machines in the automation industry. With 264 FANUC locations worldwide and more than 7,000 employees, FANUC offers a dense network in sales, technical support, research & development, logistics and customer service.
For more information, please contact:
FANUC Europe Corporation S.A.
7, rue Benedikt Zender, L-6468 Echternach, Luxembourg
Phone: + 352 (0)72 7777-0
Email: pr@fanuc.eu
Home: www.fanuc.eu
West Caldwell (New Jersey) – The Marchesini Group returns to the Jacob K. Javits Center in New York (April 28-30) for the 41th edition of Interphex, the premier pharmaceutical, biotechnology and device development and manufacturing event in the U.S.
Marchesini Group USA - the American subsidiary of the Marchesini Group - is expecting high attendance at booth 3125 where two stand-alone machines will be on show: the Marchesini BL-A420 CW labeler and the CMP PHAR.MA SV inspection machine.
BL-A420 CW labeler is much more compact than the classic solution (carton labeler/print/inspect machine and separate stand-alone checkweigher) and much more compact than the versions offered by the competitors.
The cartons are fed and accumulated in-line on the inlet belt to ensure a continuous flow of products, even at high speeds. A patented timing device positions and sets the cartons apart correctly on the toothed belts with adjustable opening, which also prevent slipping.
The function of the timing device is to set the cartons at the correct distance apart; its special feature is that it is synchronised with the speed of the whole conveyance system and there is no need for any size change-over adjustments.
A load cell is fully integrated into the stepper conveyance system and is able to check the weight of each carton. By integrating the load cell into the toothed belt system of the BL-A420 CW, the machine is able to verify the position of the cartons at all times. If the weight is correct, the product will then proceed to the next step (printing, inspection/serialization and sealing). If the weight is not correct, the subsequent processes are skipped and the carton is rejected, according to the “Fail Safe” operating logic.
The first operation to be performed after the cartons have been checkweighed is the application of the vignette label on the upper panel of the cartons. After the vignette has been applied, the unique 2D code (Datamatrix) and the corresponding human readable data are printed on the side flaps and sometimes on the upper panel. The unique code identifies and makes it possible to track each carton.
A camera then verifies both the codes and the readable data. After print inspection, two self-adhesive Tamper Evident seals are then applied on the corner closing points of the cartons.
The model showcased is equipped with a new operator interface called “Easy Door”. This version has several improvements from both a functional and aesthetic point of view. The new software makes the operating system more powerful and faster. The wider screen is more ergonomic, and the touch screen is easier to use, similar to that of a mobile phone.
The high level of flexibility of the BL-A420 CW means that all types of printing and vision systems available can be installed on it, which can be customised according to all the current standards worldwide. This special feature makes the BL-A420 CW the most suitable and complete machine for tracking, serialising and labelling cartons, giving a unique identity to all the pharmaceutical products packaged.
The machine can process up to 400 cartons per minute.
Alongside the BL-A420 CW will be the SV model designed by CMP Phar.ma. The SV is a semi-automatic machine for the inspection of liquid, lyophilized or powder products in ampoules, vials and cartridges or pre-filled syringes. It is equipped with brushless motors for fast rotation (before inspection) and slow rotation (during inspection) to guarantee complete and efficient product control.
The machine can handle up to 100 pieces per minute.
Following the CMP acquisition in December 2018, the Marchesini Group now can offer complete lines for producing and monitoring the whole pharmaceutical packaging process, from start to finish, including the Group’s partner, SEA Vision, which also participated in the CMP transaction.
Press Contact: Antonio Leggieri
antonio.leggieri@marchesini.com
Company Contact: Emilio Maffei
emilio.maffei@marchesini.com
Marchesini Group S.p.A.
Marketing&Communications Department
Via Nazionale, 100 | 40065 PIANORO
BOLOGNA | ITALY
Short Hills, NJ – TCP Reliable, a parent company serving the life science and industrial markets, has undergone a corporate rebranding and is now officially Integreon Global. The rebranding encompasses not only a new name, but a revamped website and reimagined logo design applying to its subsidiary companies, further promoting organizational synergy.
Taking place 30 years after TCP Reliable was founded, the company is being rebranded to better communicate the unique, integrated solutions and services offered by the subsidiary companies of Integreon Global: Cryopak, DDL, LaunchWorks, and NexKemia. Together, the four companies collaborate to ensure product integrity and protection through innovative materials, testing services, packaging and monitoring solutions, and contract manufacturing.
“The rebranding effort showcases our commitment to delivering tailored end-to-end solutions that meet each customer’s unique set of challenges,” says Maurice Barakat, CEO of Integreon Global. “Not only are we promoting internal collaboration, but also the partnering of Integreon specialists with our clients. This is key to maintaining product integrity throughout manufacturing and distribution.”
The four companies that make up the pillars of Integreon Global offer a range of products and solutions: Launchworks is a premier contract development and manufacturing organization; Cryopak designs and develops cold chain packaging and temperature monitoring devices; DDL provides packaging, product and material testing services; and NexKemia manufactures expandable polystyrene (EPS) resin. Each company in the Integreon brand is unique, and under the combined strength of this new image will be well-positioned for additional growth.
###
About Integreon Global
Founded in 1990, Integreon is a complete packaging solutions provider dedicated to providing goods and services to maintain the integrity of our clients’ products. Our team includes a full complement of engineers, designers, and manufacturing specialists with the collective skills, gathered in one close-knit organization, to assure easy access to leading experts.
For more information visit www.integreonglobal.com
Williamston (MI, USA), 26.11.2019: The Bekum group celebrated recently three anniversaries – 60 years Bekum in Berlin Germany, 50 years Bekum in Traismauer Austria und 40 years Bekum in Williamston, USA. As part of the celebrations at the American location, the groundbreaking ceremony for the expansion of production capacities was made on November 26, 2019. A new building with a production area of 3,700 m² and almost 700 m² of office space will be added. This increases the site's operational area to more than 15,000 m².
Michael Mehnert, Managing Partner, who traveled from Germany for this celebration, comments proudly: “My father founded this company sixty years ago. Today I’m standing here and lay the foundation for a new production hall in order to be able to serve the continuously increasing demand in the USA in the future!”
„This is a historic week for Bekum America,” said Steve London, COO and President of Bekum America Corporation. “The groundbreaking on our new facility was a great kick off to our 40th anniversary celebration with our dedicated employees. The Bekum team has continually been providing state of the art products for our clients, and this event is the perfect opportunity to celebrate all the individuals who complete Bekum.”
Bekum America was established in 1979 with the mission to introduce top quality blow molding machinery, designed to produce plastic bottles, containers and other large plastic parts in the North American marketplace, via blending German design and technology with American skill and ingenuity. Bekum’s customer base includes large multi-national customers, as well as owner/operator plastic bottle manufacturers.
Released for Publication – Copy Requested.
Volume: 272 words | 1.746 characters
Captions:
Caption 1 (opening image): Managing Director Michael Mehnert (2nd from left) during the at groundbreaking with the managers of the US subsidiary CFO Owen Johnston, Chairman Martin Stark, President & COO Steven London (from left)
Image sources: All images are from Bekum (unless otherwise indicated)
About Bekum +++++++++++++++++++++++++++++++++++++
Pioneer and Trendsetter in Blow Moulding Technology
Founded in Berlin in 1959, Bekum Maschinenfabriken GmbH is one of the world’s leading manufacturers of extrusion blow moulding machines.
Founder Gottfried Mehnert conceived the name Bekum as the acronym (Berliner Kunststoff Maschinen).
The company began to flourish in its founding year with the development of the world’s first neck-rim calibration. Numerous innovations and patents followed, confirming that Bekum, with its innovative and customer-oriented machinery solutions, has always been ahead of its time – and remains so to this day.
When innovative and economical machinery solutions with high productivity for individual packaging requirements of hollow packaging are in demand, then Bekum, with 60 years of experience in blow-moulding technology, is the first choice worldwide.
Product Range and Applications in Food and Non-food
With future-oriented and reliable production processes and fully electric, as well as hydraulic machinery for the commercial production of blow moulded containers ranging from 5 ml to 3000 l, Bekum offers everything for plastic packaging from one source.
Philosophy of the Company
Building and maintaining long-term relationships with market partners through future-oriented, predictable company policy determine the actions of the first and second generation of the family, represented by Michael Mehnert. This strategy ensures the jobs of dedicated and experienced staff. The preservation of traditional structures, an established network of partners and far-sighted adaptation to change form the basis for continuous development and inspiration for the company in the interest of partners, customers and employees.
Innovation and Technology
Process reliability, availability, efficiency and sophisticated design characterise the high standard of Bekum production lines for blow moulding. Bekum contributes the expertise that has grown based on these references, associated with various patents in blow moulding, to the fulfilment of every customer requirement.
The level of process design is key for process reliability, reproducibility, parts quality and cost-efficiency. A high-quality production line for extrusion blow moulding, consisting of machine, die and automation which is impressive in terms of speed, wear resistance, availability, process reliability and stability alike, is critical for return on investment (ROI) and the level of added value.
Facts and figures
With 18,000 machines delivered and installed worldwide - about half of them still in use - the Bekum Group has achieved by far the largest production of blow moulding machines of any brand.
The Bekum Group serves approximately 100 countries around the world directly or through representatives.
Today, 350 employees work for the Bekum group worldwide at three locations in Europe and in the US (Berlin (Germany), Traismauer (Austria) und Williamston (USA)).
Our Technology – Your Success
Berlin | Deutschland
Traismauer | Österreich
Williamston | USA
Bekum Maschinenfabriken GmbH
Kitzingstraße 15/19 • 12277 Berlin • Deutschland
Tel.: +49 (0)30 7490-0 • Fax: +49 (0)30 7490-2441
E-Mail: sales@bekum.de • www.bekum.com
Geschäftsführer:
Gottfried Mehnert
Dipl.-Ing. Michael Mehnert
Ust.-Id.-Nr.: DE136701335
Deutsche Bank AG, Filiale Berlin
BIC DEUTDEBBXXX
IBAN: DE55 1007 0000 0386 9500 00
Amtsgericht Charlottenburg, 92 HRB 3533
Luxembourg (Feb. 11, 2020) – Ardagh is delighted to have received prestigious Leadership class ratings from the Carbon Disclosure Project (CDP) for climate change (A-) and for supplier engagement (A). Ardagh’s efforts for water security have been rated as Management class (B).
CDP, a global environmental impact group, drives companies and governments to reduce their greenhouse gas emissions, safeguard water resources and protect forests. Ardagh has worked with CDP since 2011.
Environmental performance as part of an overall sustainability strategy is a key focus for Ardagh, which recently established a Global Sustainability Board Committee to drive initiatives in this area, including co-ordinating its global sustainability work, accelerating sustainability programmes and increasing responsiveness.
Ardagh’s vision is to be the preferred packaging partner to the world’s leading brands, supplying sustainable and infinitely recyclable metal and glass solutions. Sustainability is at the core of Ardagh’s activities and is defined by Ardagh as not only delivering a reduced environmental impact but also achieving sound economic performance while making a positive social contribution.
"Achieving this important external validation from CDP underlines Ardagh’s commitment towards environmental management," said John Sadlier, Chief Sustainability Officer, Ardagh Group.
Further information
Maeve Desmond,
Group Communications,
Notes to the editor
Ardagh Group is a global supplier of infinitely recyclable metal and glass packaging for the world’s leading brands. Ardagh operates 56 metal and glass production facilities in 12 countries, employing more than 16,000 people with sales of $6.7bn.
Wolfertschwenden, 10 February 2020 – From 21 to 23 April at Seafood Expo Global in Brussels, MULTIVAC will be exhibiting packaging solutions, which contribute to extending the shelf life of fish and seafood, as well as ensuring that the product is presented attractively at the point of sale. In addition to concepts for producing high-quality vacuum skin packs, the focus of MULTIVAC's presence at the trade fair will include sustainable packaging solutions and a presentation of the company's expertise in automation.
This year in Brussels MULTIVAC will be focusing primarily on the subject of sustainability. On display will be a range of concepts, which contribute to reducing the use of plastics in packaging production, as well as concepts for producing packs that meet recycling requirements. The MULTIVAC PaperBoard range comprises a wide variety of paper fibre-based materials, which MULTIVAC has developed in conjunction with leading packaging manufacturers, and which can be used to produce MAP and vacuum skin packs on thermoforming packaging machines and traysealers.
The focus will also be on MultiFresh™, a process for producing high-quality vacuum skin packs. In addition to a wide spectrum of packaging machines, there is also an extensive range of films available, which was developed in conjunction with leading film manufacturers, and which ensures that optimum packaging results are achieved. This means that even food products with sharp edges or hard areas, such as bones or shells, as well as those with high product protrusion, can be packed securely and attractively. At the trade fair this solution can be seen on the compact R 105 MF thermoforming packaging machine, which will be producing PaperBoard packs, as well as on the fully automatic T 800 MF traysealer. Whereas the compact R 105 MF makes it possible to pack smaller batches very efficiently, the high-output traysealer is designed for large batches and for packing products with a protrusion of up to 20 mm. The traysealer is also equipped with a L 310 full wrap labeller for applying labels to the packs. In this process the label is attached to the top of the pack, then over both sides and finally onto the base of the pack. Full wrap labelling offers many benefits in terms of label quality, efficiency and presentation at the point of sale. The process is very flexible in being able to run labels made from different materials and in a wide variety of shapes, and it ensures that maximum labelling quality is achieved even with unusual pack shapes.
MULTIVAC's presence at the exhibition is rounded off with a presentation of the company's expertise in automation. The possible areas of use for automation solutions within the packaging process for fish products extend from infeed and loading right up to pack inspection and secondary packaging or palletising at the end of the line. MULTIVAC customers benefit in particular from automation modules from one source, which are ideally tailored to each other, and also from the overarching machine control for all line components, which provides the maximum degree of process reliability, operating convenience and pack security.
[3,287 characters incl. spaces]
About MULTIVAC
MULTIVAC is one of the leading providers worldwide of packaging solutions for food products of all types, life science, and healthcare products, as well as industrial items. The MULTIVAC portfolio covers virtually all requirements of processors and producers in terms of pack design, output, and resource efficiency. It comprises a wide range of packaging technologies, as well as automation solutions, labellers, and quality control systems. The product range is rounded off with solutions upstream of the packaging process in the areas of portioning and processing, as well as bakery technology. Thanks to extensive expertise in packaging lines, all modules can be integrated into complete solutions. This means MULTIVAC solutions guarantee a high level of operational and process reliability as well as efficiency. The MULTIVAC Group has approximately 6,400 employees worldwide, with some 2,200 based at its headquarters in Wolfertschwenden. With over 80 subsidiaries, the Group is represented on all continents. More than 1,000 sales advisors and service technicians throughout the world use their know-how and experience to the benefit of customers, and they ensure all installed MULTIVAC machines are utilised to their maximum.
Further information can be found at: www.multivac.com.
Company enquiries
MULTIVAC Sepp Haggenmüller SE & Co. KG
Tanja Nickels
Bahnhofstr. 4
D-87787 Wolfertschwenden Germany
Tel.: +49 (0) 8334 601 – 1544
E-mail: tanja.nickels@multivac.de
www.multivac.com
Press contact
REDAKON
Vera Sebastian
Seestr. 18
D-80802 Munich
Tel.: +49 (0) 89 – 31 20 338-21
E-mail: vera.sebastian@redakon.com
www.redakon.com