Efsa-compliant process produces food-saf...
Reifenhäuser Cast Sheet Coating - the Reifenhäuser Group's business unit specializing in cast film, sheet extrusion, and extrusion coating lines - has developed a particularly efficient production process that allows PET recyclate to be processed directly into food-safe sheet without an upstream drying process.
If recycled material comes into direct contact with food, it requires special certification from the European Food and Safety Authority (EFSA). Up to now, the production of sheet for food packaging of this type has been very laborious and complicated. Reifenhäuser MIREX PET lines now simplify the task for processors. By using a co-rotating twin-screw extruder and a specially developed high-performance vacuum system, the certified process allows PET recycling material to be processed directly without pretreatment and predrying - processes that are usually required. Processors then save their investment in an extra line component and avoid additional energy and maintenance costs. It also allows for quick material and product changes, for example from post-consumer PET bottle flake (PCR) to post-industrial PET production waste (PIR) or to virgin PET. The end product, such as a meat tray, then meets extremely high hygiene standards and is EFSA-compliant for use in direct contact with food
Reifenhäuser Cast Sheet Coating supports customers during the certification process with the competent authorities. This includes the cleaning process of the flake material, quality monitoring of the feed material, and production under the criteria defined by EFSA.
Another feature is the automatic documentation of relevant production data. EFSA audits require recipe- and product-related data from the certified process to be stored for several years. The ExtrusionOS Production Compliance software bundle was specially developed to monitor and securely document production processes and compliance with EFSA-related thresholds in a real-time database. A live dashboard provides a transparent display of ongoing production and thresholds, permitting rapid response to anomalies. ExtrusionOS Production Compliance is based on Reifenhäuser's connectivity solution ExtrusionOS Core & c.Hub Middleware. It can also be retrofitted to existing lines.
Via ExtrusionOS production data can also be transferred to a digital product passport - for example, via the open R-Cycle standard. Digital product passports are data records clearly linked to preliminary and end products that contain specific data on the materials, ingredients, and utilization of the product. Specific markings allow their use for data-based and therefore more precise waste sorting and recycling processes, among other things.
About the Reifenhäuser Group
The Reifenhäuser Group together with its highly specialized business units is the leading provider of innovative technologies and components for plastics extrusion. Founded in 1911, the company is a global supplier of high-tech solutions. With its technologies and the know-how of its 1,750 employees, Reifenhäuser has the world's largest network of expertise in plastics extrusion technologies. The CEO of the Group is Bernd Reifenhäuser.
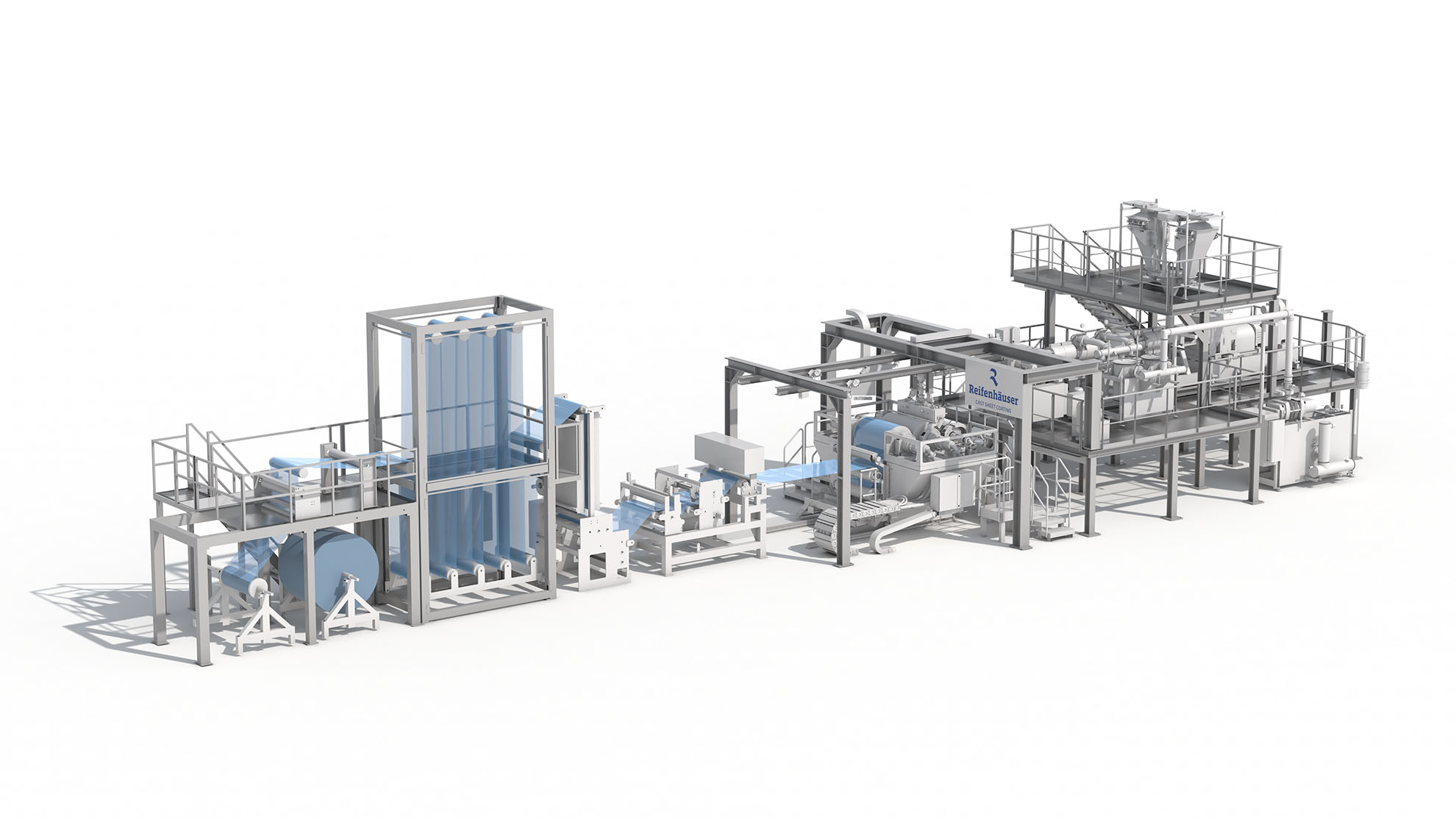