Founded in 2005, Sanex Packaging Connections started with an online platform as “your destination for anything in packaging”. We progressed with innovative models of bringing new technologies to the world through support to foreign packaging companies. We are a team of packaging professionals who have worked on successful projects with multinationals for live packaging projects. We are the first packaging consulting company to have ISO 9001:2015 certification. We are an Indian partner for top German pharma companies and have a wide network of packaging professionals across the globe. Witnessing fast brand recognition and network growth, our company has come up with various verticals in packaging. We have partnered with top design and artwork agencies to support our packaging consulting projects. We also provide educational support to the industry through our publications of reports and books in packaging & innovations and also through our e-learning modules.
Haryana
Sector-49, Vatika City , Gurugram
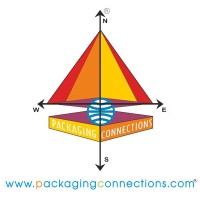