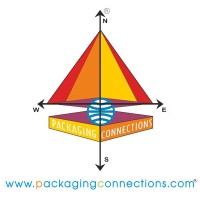
Introducing the odc 960 sensor from roll...
Roll-2-Roll Technologies is proud to announce the introduction of its latest product, the ODC 960 sensor.
Roll-2-Roll Technologies is proud to announce the introduction of its latest product, the ODC 960 sensor.
Can the liquid packaging industry — a frequent target of environmentalists — find a path to sustainability that’s als
AB Graphic International (ABG) recently opened its doo
The Accraply Revolve machines leverage next-generation controls and an intuitive human-machine interface (HMI) to sim
The V520 feeder can handle both bare soap bars and soap packaged in flow pack wrappers, and the G35 wrapper is equipp
The recyclable packaging solutions, developed by A. Hatzopoulos S.A.
The FDA’s Center for Devices and Radiological Health (CDRH) has issued two final guidance documents to assist with tr
The legendary tercentenary whisky house has entrusted Cosfibel with the production of two boxes, wit
Wooden pallets are often used for transporting goods. But some alternatives could have critical advantages.
While AI has proven