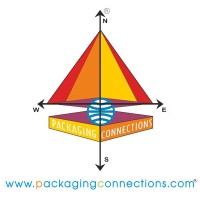
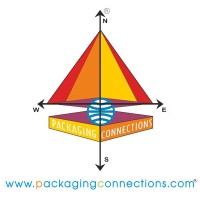
Activity
-
-
Global print pack tech expo-2023
GPPT 2023, aligned with UAE aiming to become a "Printing & Packaging Hub" by 2030 is a perfect platform to showcase your printing technologies and solutions, including the latest machinery, software, and product launches for graphics, signage, decor, packaging, fabricating, labeling, and 3D printing in the market that is flourishing with latest -
A new technology increases sterility ass...
Pulsed light decontamination sterilizes the outside of ready-to-use (RTU) tubs containing syringes, vials, or cartrid
-
4 types of fertilizer packaging bag ! ! ...
-
Isdinceutics essential cleansing by isdi...
Gerresheimer's most recent post-consumer recycled packaging solution was made for their partner ISDIN, a leading Span
-
Robot marine plastic pollution collector...
-
Autentico develops anti-counterfeit pack...
The rising parallel market of counterfeit alcohol poses a threat to public health.
-
Schreiner group to start climate-neutral...
The goal of the Paris Agreement is to limit global warming to a maximum of 1.5 °C.
-
First wave innovations and proampac part...
FirstWave Innovations, a wholly owned subsidiary of SinnovaTek and a co-manufacturer of aseptic food products, has pa
-
Mylife loop offers new remote monitoring...
-
Remi becomes waterless & condensed skin ...
When you entered the Bathroom the only thing you saw was Plastic, there was a lot of it.
-
Syringe-closure-wrap: multifunctional la...
-
Recyclable wraps for food packaging
-
Polyrec launches recotrace, the multipol...
PolyREC has now been recognized as an official data collector for the Circular Plastics Alliance (CPA). PolyREC will
-
Efi nozomi c18000 plus- revoltunize your...
-
Pamex -2023 "of the printers-for the pri...
India’s premier printing exhibition, presenting the latest products and solutions. The largest gamut of LIVE running machines! One-on-one meetings and unparalleled business & networking opportunities. PAMEX attracts QUALITY visitors from all across India and neighboring countries providing a global business and networking platform to participating -
Cepac acquires ew carton ltd ,launches f...
Steve Moss, Managing Director, Cepac Group, has confirmed the company recently completed the acquisition of a majorit
-
Fiber bottle collective based on dry mol...
The Bottle Collective is committed to industrializing a recyclable, high-speed, low-cost Dry Molded Fiber bottle proc
-
Ingede symposium 2023- hybrid & munich
The future is green: All printed products become recyclable. All printing inks become de-inkable. All adhesives application become removable. All packaging becomes sortable. All about paper for recycling, alternatives, availability, sorting, and sustainability. -
Know more about the intaglio printing ak...