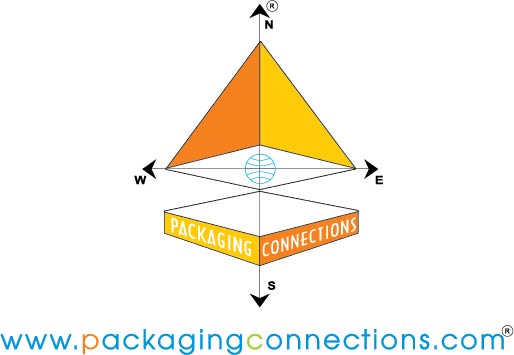
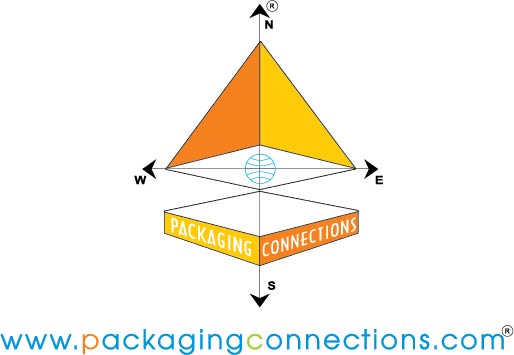
Activity
-
-
Quality is not a vision sick at interpac...
Waldkirch, May 2017 – At Interpack 2017, SICK will present itself as the supplier of a wide range of sensors for the consumer goods industry. The products, systems and services that it puts on display will include compact, easily integrated devices, configurable stand-alone solutions and programmable high-speed cameras. As well as individual components, the sensor manufacturer offers a comprehensive portfolio of technological solutions to meet individual customers' requirements.
SICK will focus in particular on quality assurance at Interpack. The fast throughput speeds and short cycle times of production lines and machines in the packaging industry allow for high productivity. However, this can only be achieved if a comprehensive quality control system is in place. SICK will present new solutions consisting of its own modules and integrable functions from image processing libraries that offer intelligent support for the packaging industry in areas such as quality assurance, traceability, object data acquisition and preventive maintenance.
A 3D inspection system is the ideal solution in this area. It can reliably identify faulty product features, incomplete packaging units and inadequate labeling. The data and measurements produced by the vision sensors and their integration into real-time fieldbus environments enable them to provide valuable information that can be used in today's manufacturing plants and in the smart factories of the future. The vision sensors have the necessary intelligent detection, measurement, assessment and communication functions to allow for future-proof process and quality controls in the context of Industry 4.0.
Image -
To the point laser expertise from sick
Waldkirch, May 2017 – SICK will be presenting its wide range of laser sensors at Interpack 2017. The sensors detect objects reliably even with large sensing ranges and the tightest of installation conditions, they provide excellent performance and security in a compact housing, they measure quickly and precisely in the µm range, and they guarantee high reliability up to 35 meters thanks to HDDMTM technology.
SICK sensors with laser technology offer a wide range of solutions for any application where the smallest objects, the finest details or minute deviations on products or in production facilities need to be detected. Their precise laser beam also makes it possible to detect objects and features through small openings, and enables easy alignment during commissioning.
For example, the Dx35 family of distance sensors, based on HDDM technology, combine maximum reliability, measuring capabilities, flexibility, and a perfect price-performance ratio in one very compact housing. Depending on the application, sub-product families are available for distance measurement on natural objects (DT35 and DS35) or on reflective tape (DL35 and DR35). The sub-product families also come with different interfaces. In addition to the IO-Link function, which all the devices have, the product family also offers sensors with analog and switching output (DT and DL) or the option of two switching outputs (DS and DR). Its final distinguishing feature when selecting the right sensor for the application is the light sender: infrared or red emitted light in laser class 1 or 2.
The OD Mini displacement measurement sensor impresses with its compact and rugged housing, which is available in either an aluminum or stainless-steel version. It is equipped with the latest CMOS receiver technology for precise measurement, regardless of the brightness and color of the surface material. The integrated amplifier unit enables the OD Mini to work on a stand-alone basis. For more complex measuring tasks, up to two OD Mini Pro sensor heads can be connected to the OD Mini evaluation unit and calculated together. The OD Mini is simple to configure due to its intuitive design and display with four status LEDs. The OD Mini can also be remotely programmed via the external teaching input. The large number of available interfaces also simplifies integration into industrial networks. This ensures the highest possible reliability and precision when solving a wide range of measuring tasks.
For the first time, the PowerProx MultiTask photoelectric sensor offers all of the advantages of time-of-flight technology in the world’s smallest housing – coupled with a high detection speed. Objects being conveyed at high speed, small and flat objects, and jet-black or shiny objects can now be reliably detected at sensing ranges between 5 cm and 3.8 m. For even more flexibility, up to eight switching points can be defined via IO-Link. The four variants – “Distance”, “Speed”, “Precision”, and “Small” – are designed to be used in different applications. This means that PowerProx offers not just the best solution, but the right one in each case – from occupied bay and clearance detection via rapid counting and precise edge detection right through to use in handling, assembly, and packaging technology.
Image -
A good eye for contrasts and colors kts ...
Waldkirch, May 2017 – With its KTS and KTX product families, SICK is presenting new, powerful contrast sensors from a forward-looking, innovative platform. The patented TwinEye technology for improved contrast detection and sensing distance tolerance (+- 5 mm), the specially developed three-color LED with its high-precision, color-mixed light spot, and the jitter that has been minimized to a level never before seen, coupled with absolute high-speed switching frequencies, open up a world of new possibilities when it comes to detecting contrasts and – for the first time in a sensor – colors too.
IO-Link and additional integrated functions such as recipe management ensure maximum versatility, while the innovative, multifunctional 7-segment display guarantees simple yet customized sensor setup, operation, and visualization.
Familiar applications such as the detection of print marks or the control of industrial labeling processes benefit from even greater process stability and performance. The sensors detect high-gloss materials and complex contrasts, even on heavily jittering materials. The integrated color mode also enables reliable detection of even the most minor contrast differences and color features.
More applications, more flexibility
The KTX product family offers compatibility without compromise: Both the hole pattern for mounting the sensors and the electrical connectivity facilitate a 1:1 migration from the SICK product families that are already proven and widespread on the market to the new technology platform. In its space-saving compact housing, the KTS meets all requirements of modern machine concepts. The KTS contrast sensors come in “CORE” and “PRIME” configurations; these offer different levels of functionality, enabling a variety of different automation needs to be met individually and cost-effectively. The even more finely granular grayscale resolution of the KTS and KTX, the integrated color mode, and the large number of other technical innovations in both product families are setting a new standard in the market for contrast sensor technology – and opening up additional areas of application at the same time, such as the detection of wafers, the management of reel changes, or quality control.
Image -
Image processing 4.0 programmable inspec...
Waldkirch, May 2017 – The programmable InspectorP6xx camera from SICK is the solution for complex image processing tasks. Optics, illumination, evaluation, and interfaces – everything is integrated and highly customizable. The pre-installed, high-performance HALCON image processing library and the flexible design of web-based user interfaces make it possible to adapt the solution to specific customer requirements.
The InspectorP6xx product family consists of three programmable camera types that differ in terms of their design, evaluation speed, and camera sensor resolution. But they all have one thing in common: In conjunction with the new SICK AppSpace platform, the cameras offer the freedom and flexibility to develop application software for specific tasks. This makes it possible for system integrators and original equipment manufacturers (OEM) to implement tailor-made solutions and custom apps for individual customer needs. As the finished app is tailored precisely to the relevant application, its complexity can be reduced significantly. Furthermore, all cameras provide exceptionally convenient functions, such as aiming lasers, acoustic and optical feedback, as well as an SD memory card, which offer easy setup and operation and make simple analyses possible during use – perfect for Industry 4.0.
The InspectorP family provides programmable cameras for industrial image processing tasks. With a camera resolution of 1 to 4 megapixels, a flexible high-end optical design, integrated illumination even for large sensing ranges and fields of view, and the IP65/67 protection class, it is the ideal solution for demanding automation environments. Alongside the use of standard C-mount or S-mount lenses, the InspectorP6xx series even offers a variant with dynamic focus adjustment, which enables automated focus position adjustment from object to object so that parts can be easily analyzed at varying distances.
Image -
Printed electronics makes its way into e...
The new OE-A Roadmap presents a diverse range of application examples as well as challenges for organic and printed electronics
Munich, Germany, March 29, 2017 – Organic and printed electronics has become established in many important industry sectors. From the Internet of Things, consumer electronics and healthcare to automotive, smart packaging and buildings – printed electronics is now used in numerous products and industries worldwide. This is one of the central results of the seventh edition of the Roadmap published by the OE-A (Organic and Printed Electronics Association), a working group within VDMA, on the occasion of LOPEC 2017.
Continuous increase in interest and wider use in different fields of application and industries
„Major industries, including automotive and consumer electronics, have come to embrace organic and printed electronics by integrating this technology in their products. It is clear that OLED displays and lighting are still the driving force for this technology. The new OE-A Roadmap reflects this development by including important industry sectors and by explaining how printed electronics enhances their products,” says Dr. Wolfgang Clemens, Spokesperson of OE-A Roadmap and Head of Product Management PolyTC at PolyIC. “Of course, we also examine the progress made in individual application clusters ranging from OLED Lighting, OPV, OLED and Flexible Displays, to electronics & components and integrated smart systems – and not to forget the development in materials and processes,” he adds.
These positive findings are also reflected in the key parameters reliability, capital expenditure, cost, environmental impact, and standards. By now, there is hardly any differentiation between application and technology parameters anymore, which underlines the increasing maturity of the printed electronics industry.
The OE-A’s experts expect continued strong growth in the coming years, triggered by new and improved materials, equipment, processes and device design. However, there are also some areas where technological barriers, also referred to as “Red Brick Walls”, need to be overcome. These are also identified in the Roadmap, including to point out areas where additional development is needed.
A summary of the seventh edition of the OE-A Roadmap for Organic and Printed Electronics is included in the new OE-A Brochure, which is available at the OE-A booth 510 (Hall B0) at LOPEC 2017 as well as on the OE-A website. The “White Paper: OE-A Roadmap for Organic and Printed Electronics” will be published in June 2017, containing more details about the applications and technologies.
Image -
The organic and printed electronics indu...
Positive outlook from OE-A members on the development of organic and printed electronics announced at LOPEC 2017
Munich, Germany, March 30, 2017 – The signs are still set for growth in the organic and printed electronics industry. This is the clear message to result from the latest business climate survey conducted by the OE-A (Organic and Printed Electronics Association). 80 percent of survey participants expect the industry to continue its positive development in the coming year. The results of the survey, carried out for the seventh time, were presented by OE-A Chair Dr. Jeremy Burroughes to the international press at LOPEC 2017 – the international trade fair and conference – in Munich, Germany.
The semi-annual OE-A Business Climate Survey sheds light on the anticipated growth of the Organic and Printed Electronics industry. During each survey, OE-A members – from material suppliers to end-users – are asked to provide qualitative data on the state of the industry and their expected sales development.
The organic and printed electronics industry continues to grow
With a projected sales revenue of 8 percent, 2017 will be a very successful year for OE-A members – even if the growth is 9 percentage points lower compared to the forecasts from 2016. “It is understandable that companies are careful in making predictions at the beginning of the year”, states Dr. Jeremy Burroughes.
For 2018, a continuation of the positive trend in the organic and printed electronics industryis expected, in all areas, from material suppliers to end-users, and in all regions: Europe, Asia and North America. The companies expect further development and a growth in revenue of 16 percent.
Thin, lightweight and flexible – these are the characteristics of organic and printed electronics. These features enable applications in numerous areas. OE-A members in particular target the following sectors: consumer electronics, medical and pharmaceutical, automotive, lighting, as well as energy. “The importance of these sectors for the organic and printed electronics industry is apparent at LOPEC 2017”, says Dr. Jeremy Burroughes. “Applications in the areas of wearables, automotive, and consumer electronics are key topics, at the trade fair as well as at the conference”.
The positive forecasts for 2017 are also reflected in other areas. Survey respondents want to continue to invest in expanding production in particular. Nearly half of the companies even want to increase these investments. They also want to continue expanding capacity in R&D activities. Furthermore, there are good opportunities for employees in the organic and printed electronics industry: 33 percent of the companies surveyed plan to hire more employees in the next six months.
Image -
Interactively discover printed electroni...
OE-A publishes new brochure with integrated NFC tag at LOPEC 2017 in Munich, Germany Frankfurt, Germany, March 01, 2017 – The new OE-A Brochure with an integrated NFC tag will be presented at LOPEC. This publication not only contains the latest information on organic and printed electronics but also serves as an example of this cutting-edge technology.
The OE-A, a working group within VDMA, will publish the 7th edition of the brochure “Organic and Printed Electronics – Applications, Technologies and Suppliers” as a guide for the latest trends and developments. This brochure will also include market data and an overview of the products and services of the OE-A members.
NCF tag connects paper with smartphone
The NFC tag integrated in the OE-A Brochure is a perfect example of the versatile characteristics of organic and printed electronics: thin, lightweight, flexible, robust and able to be produced in high volume. 10,000 pieces have been printed by OE-A member Arjowiggins, and one is integrated into each OE-A Brochure. By placing your smart device in close proximity of the NFC tag, you will automatically be taken to the OE-A website.
However, this is merely one of the countless application possibilities a NFC tag could be integrated in. Using it as an information indicator or smart label on medicine packaging, sharing a curriculum vitae via a business card, or unlocking and starting your car with a digital key are just a few additional application examples.
“Intelligent paper with embedded NFC technology enables new cross-media applications”, says Dr. Klaus Hecker, OE-A Managing Director. “And the combination of printed antennas, conducting paths and an integrated silicon chip is an impressive example of a hybrid system.”
Organic and printed electronics complement conventional electronics
Organic and printed electronics is a revolutionary new type of electronics. This technology provides the answer to developing a great number of electronic components in cost-effective processes, thereby enabling mass production. Integrating these electronics in objects used in everyday life constantly opens up new areas of application. Because of its flexibility – in contrast to silicon electronics – printed electronics allows for an abundance of potential new applications.
You have become curious? Then pick up your copy of the OE-A Brochure with a NFC tag at the OE-A exhibition booth 510 (Hall B0) at LOPEC 2017, 28-30 March 2017, ICM, Munich, Germany.
Image -
Oe-a elects new international board of d...
New OE-A Board to represent the entire international value chain of organic and printed electronics.
Frankfurt, Germany, April 07, 2017 – The members of the OE-A (Organic and Printed Electronics Association), a working group within VDMA, reappointed Dr. Jeremy Burroughes, CTO of CDT Ltd. and Sumitomo Chemical Fellow, as the Chairman of the Board of Directors during the annual General Assembly in Munich, Germany. Jaap Lombaers, Holst Centre and Stan Farnsworth, NovaCentrix Corp. are confirmed in their positions as Vice Chairman Europe and North America respectively. Dr. Xiaolin Yan, Guangdong JUHUA Printing has been elected as the new Vice Chairman Asia.
Chairman
Dr. Jeremy Burroughes, CDT Ltd, Great Britain
Vice Chairman Asia
Dr. Xiaolin Yan, Guangdong JUHUA Printing, China
Vice Chairman Europe
Jaap Lombaers, Holst Centre, Netherlands
Vice Chairman North America
Stan Farnsworth, NovaCentrix Corp., USA
Additional members of the board
- Dr. Peter Fischer, Thin Film Electronics ASA, Norway
- Dr. Mark James, Merck Chemicals Ltd., Great Britain
- Prof. Toshihide Kamata, AIST, Japan
- Dr. Stephan Kirchmeyer, COPT.Center, Germany
- Thomas Kolbusch, Coatema Coating Machinery GmbH, Germany
- Dr. Arto Maaninen, VTT – Technical Research Centre of Finland, Finland
- Dr. Giovanni Nisato, CSEM SA, Switzerland
- Dr. Nina Riegel, Osram OLED GmbH, Germany
- Thibaud Le Séguillon, Heliatek GmbH, Germany
On behalf of OE-A, Dr. Jeremy Burroughes expressed his gratitude to both Markus Bamberger, Merck and Prof. Reinhard Baumann, Fraunhofer ENAS/TU Chemnitz, for their countless services to the organization. After two respective twelve year periods as Board members, they have decided to no longer run as candidates. “Prof. Baumann has been a member of the Board since its founding and has earned great recognition for his international collaboration between universities and the industry. He has also been a strong and essential proponent of enhancing education to support the members future activities and employment needs”, says Dr. Burroughes.
He equally acknowledged Prof. Toshihide Kamata, AIST for his five years of dedicated work as Vice Chairman Asia. “Prof. Kamata significantly strengthened OE-A’s position in Asia and initiated numerous types of cooperation. With this, he provided important impetus for the continuing internationalization of the organization. We are delighted that he will remain on the Board and look forward to his continued support of the OE-A membership in Asia and the rest of the world”, says Dr. Burroughes.
“Printed electronics has already been applied in various sectors, ranging from the automotive industry to consumer electronics”, explains OE-A Chairman Dr. Burroughes. “OE-A will continue to actively support our industry in its ongoing commercialization. One key point of focus: Continuous education of the potential of the OE-A membership technologies with end-user industries as well as promoting collaboration between OE-A members and the wider industry. This is clearly reflected in the composition of the new Board of Directors”. Moreover, the role of the OE-A as association with a European focus, needs to be internationally strengthened. In North America and Asia cooperation with regional associations will be expanded.
Image -
Oe-a appoints oe-a fellow and announces ...
Special merits, innovative ideas as well as start-up companies were offered a platform at LOPEC 2017 to support the continuous development of the international market for organic and printed electronics.
Frankfurt, Germany, April 06, 2017 – New visions and creative concepts in the area of organic and printed electronics are what the OE-A (Organic and Printed Electronics Association), a working group within VDMA, aims to promote in its annual OE-A Competition. Once again this year, there were numerous submissions coming from all corners of the world. The four best submissions were awarded at LOPEC 2017 – the international trade fair and conference for printed electronics – in Munich, Germany.
“The OE-A competition was well-received by both companies and exhibition visitors”, says OE-A Chairman, CTO of CDT UK and Sumitomo Chemical Fellow, Dr. Jeremy Burroughes. “We are particularly pleased, that more products and prototypes from different sectors, ranging from packaging and consumer electronics to automotive and wearables, could be showcased. This reflects the development of this innovative industry”.
The twelve-member jury, consisting of representatives from international companies and institutes rated 28 submissions from 12 countries – a new record – in three categories. LOPEC attendees also got a vote. At the OE-A booth, where all demonstrators were on display, they were encouraged to choose their favorite demonstrator. The awards were handed out during the LOPEC Dinner to the following winners:
Best Prototype / New Product
Sensor Platform Schreiner Group (Germany)
Best Freestyle Demonstrator
Thin-Film Full Printed PAD eurecat & NovaCentrix (Spain & North America)
Best Publicly Funded Project Demonstrator
Integrated X-Ray Sensor System iFlexis Project (EU)
Public Choice Award
Thin-Film Full Printed PAD eurecat & NovaCentrix (Spain & North America)
The OE-A Competition 2018 will be launched soon. More information about the OE-A Competition can be found at www.oe-a.org/demonstrator
OE-A Fellow awarded for the first time
For the first time the title of OE-A Fellow was awarded. With this the OE-A recognizes individuals who have made significant, sustained contributions to the field of organic and printed electronics and the OE-A itself. OE-A Fellow 2017 is:
Wolfgang Mildner
CEO & Founder MSWtech und General Chair LOPEC
When Dr Jeremy Burroughes presented the certificate to Wolfgang Mildner he said; “Wolfgang Mildner had played a significant role in the founding of the OE-A and was chairman of the OE-A board of directors for six years. As General Chair for LOPEC since 2009, he has also helped in forming LOPEC and bringing it to today’s leading position. He has made exceptional contributions to the OE-A and LOPEC and we are looking forward to continuing our cooperation”.
OE-A presents two LOPEC Start-up Forum Awards 2017
Young companies are promoted by the OE-A at the LOPEC Business Conference. Many innovative companies are looking for investors to bring their products and ideas to fruition. To continue the development of their technology and marketing strategies, they introduced their companies during the Start-up Forum. “The excellent quality of the presentations in this year's Start-up Forum clearly showed the progress of printed electronics," says Thibaud Le Séguillon, LOPEC Business Conference Chair, OE-A board member and CEO of Heliatek. A jury consisting of international industry leaders and researchers determined the winners.
Two awards were presented:
Best Business Case
Pylux: Novel polysulphide substrates for flexible electronics Dr. Apostolos Voutsas, Ares Materials, Inc. (North America)
Most Impactful Technology / Product
NIR photodetectors based on organic semiconductors Dr. Ronny Timmreck, TU Dresden IAPP / Senorics (Germany)
Based on the great interest in the demonstrators and lectures -- particularly by end-users -- the OE-A will once again hand out awards in the various categories during the next LOPEC, scheduled to take place March 13-15, 2018.
Image -
Robotgrader revolutionises fixed weight ...
Weighing and packing equipment specialist Ishida Europe has extended its range of solutions for poultry, meat and fish packaging with a unique system that improves yields and efficiencies in the packing of fresh protein.
The new RobotGrader combines weighing and pick and place technologies to grade protein products of varying weight and pack them to a fixed weight straight into the tray. The system reduces giveaway to less than 1% per pack and can correctly place and orientate the pieces, at speeds of up to 320 pieces per minute,
By comparison, a manual operation can be extremely labour intensive with a single operator only able to pack 30 pieces/min, while overfill can be anywhere from 5% to up to 20%.
The RobotGrader weighs products on a belt weigher. The information is then fed into the system’s unique sorting algorithms that determine the robot’s selection of the pieces. The robot stores the information on a large number of weighed pieces and the system also optimises the number of trays within the reach of each robot, maximising availability from which to create each complete pack. The robot gripper has been specially designed to grasp each piece firmly but gently and to orientate it correctly in the trays, for example placing two chicken drumsticks in opposite directions.
Depending on the model, the RobotGrader can handle two, three or four different tray types at the same time. In addition, the system can identify and sort pieces whose weight is unsuitable for tray packing, and direct these to bulk bins (which are integrated into the RobotGrader) as well as freezers, slicers and marinating operations.
The RobotGrader’s space-efficient design with overhead-mounted robots, and the elimination of manual work stations, provide a compact overall footprint and an impressive Return on Floorspace (RoF). The hygienic constructionenables rapid and effective washdown. Easily-movable tray guides mean product changeovers are fast and simple.
The RobotGrader can also integrate easily with existing factory ERP and control systems.
“With modern processing lines able to operate at extremely high speeds, the filling of two or more pieces into fixed weight packs has been one area that has until now resisted efficient automation,” explains Ulrich Nielsen, Ishida Europe’s Director for Business Solutions.
“Using proven technology, the Robotgrader solves this problem to deliver near-continuous accurate process packing.”
The RobotGrader can be incorporated into Ishida fresh food packing lines alongside other Ishida equipment, including X-ray systems, tray sealers, seal testers and checkweighers, to provide bespoke solutions, tailored to individual customer requirements.
Image -
Innovation in leak detection minimises f...
Ishida Europe’s recently-launched leak detector is helping food manufacturers to minimise spoilage in pre-packed retail packs, including bags, pouches and trays.
Designed for use with a wide variety of foods such as fresh, cooked and cured meat and poultry, seafood, ready meals and salads, the Ishida AirScan uses advanced laser technology to identify leaks of CO2 from holes as small as 0.25mm in sealed modified atmosphere packaging (MAP) packs at speeds of up to 180 packs per minute.
The Ishida AirScan offers fast, 100% reliable and completely non-destructive identification of leaks. It has been designed to be easily integrated into existing production lines, ensuring maximum quality control and brand protection without compromising on high throughput and minimum packing time.
In addition, by maintaining the optimum gas fill for each pack, the leak detector provides consistent product quality, and allows production problems to be identified and rectified quickly. It also reduces the amount of packaging that has to be scrapped, while the non-destructive testing process ensures that product can be re-packed.
The Ishida AirScan is part of Ishida Europe’s quality control range, which also includes X-ray inspection systems, checkweighers, weigh-price-labellers, seal testers and vision systems.
Image -
New ishida remote monitoring and interve...
Weighing and packing line equipment specialist Ishida Europe has introduced a unique remote customer care software solution that combines machine performance monitoring with comprehensive data capture and in-depth analysis. This enables food manufacturers and packers to operate their lines to maximum performance and efficiency, and avoid unnecessary and unwanted downtime.
The new Ishida Sentinel™ software connects compatible Ishida machines, anywhere in the world, to a central system manned by Ishida engineers. This provides complete monitoring of machines, however widely distributed, with Ishida experts on hand to identify and rectify any faults or poor performance.
With a number of different Sentinel™ pack options available, customers can mix and match the different services to their needs. In addition to the monitoring and reporting pack, a variety of intervention options are also available. Customers can for example select live performance monitoring, with Ishida engineers keeping a continual check on their line’s performance and informing them when this drops or a fault occurs.
In this way, uptime is maximised and potential and recurring problems can be identified early and dealt with before they become critical.
Equally important, Ishida Sentinel™ is able to produce clear, easy-to-read daily or weekly reports from production line data that can be easily accessed by designated personnel. These reports (available in multiple languages) enable quick and preventative actions to be taken, often without the need for an engineer call-out.
Nearly all equipment that contributes valuable information to the packing line management process can be linked into Ishida Sentinel™ including multihead weighers, checkweighers, tray sealers, graders and bag-makers. Contact with Ishida engineers can be made by email, phone or directly using a video conferencing VOIP access feature via a webcam that is fitted to individual machines’ Remote Control Units.
In addition, the Ishida Sentinel™ Web Client facility provides instant access from any Smart phone, tablet, laptop or PC worldwide so that machine operation can be monitored and assessed at any time or place.
Ishida has incorporated a high level of security into the software design to create a fully secure, virus-immune network that ensures remote access can only be performed by authorised personnel.
“Performance monitoring and reporting is not part of most companies’ core business, nor is the gathering of such information generally an area of expertise, yet they can play a huge role in helping to create a more profitable and efficient operation,” comments Ian Atkinson, Multihead Weigher Business Manager at Ishida Europe.
“With Ishida Sentinel’s™ full data capture and analysis capabilities, our new software relieves operators of a whole area of ‘information gathering’ tasks, and they can instead concentrate on using clear-cut, tailored information to make rapid, informed decisions.”
Ian Hodgson, Ishida Europe’s Control Systems Manager, adds: “The Ishida Sentinel™ Web Client facility allows factory personnel to directly monitor machine operation and assess performance whenever and wherever they wish. In this way, our new software is like a ‘use-anywhere window’ onto real-time production data.”
“More and more businesses are adopting fully-integrated production and packing lines to get the best out of each piece of equipment in order to maximise throughput and minimise costs,” continues Ian Atkinson. “Ishida Sentinel™ is simply pushing this concept further, enabling companies to achieve optimum benefits from this approach.”
Image -
New weigher design enhances hygiene stan...
Ishida has expanded its high-performance hygienic multihead weighers for fresh and frozen applications with the introduction of a range of models with a new open frame design that allows fast and easy access for cleaning and inspections, particularly in the timing hopper area.
The new design for the Ishida CCW-RV 10 and 14 head WP waterproof models means there is no conventional base unit to restrict access to the lower contact parts. In addition, the design allows the weigher to be positioned lower in the separating floor of a factory. The frame itself can also be integrated into a concrete floor and sealed, preventing excessive wash down water drain onto equipment installed below the weigher.
Other features include a sloped dispersion feeder cover and frame, which are self-draining and free of crevices, exposed screw threads, and other areas where bacteria and debris might accumulate. The power control unit is securely isolated in a separate waterproof cabinet, which can be mounted on the weigher frame or remotely located up to 20m away. This effective protection of the sensitive electronics means all product bearing surfaces can be thoroughly and regularly cleaned without the need to protect water- and temperature-sensitive parts in that process.
The new weighers are available with product hoppers in 3, 5 and 7 litre capacities, making them ideal for a wide range of fresh and frozen meat, poultry, seafood, vegetables, fresh fruit or salad applications. Rapid hopper opening and closing cycles deliver weighing speeds of up to 180 per minute depending on the application. …/
In addition all models are pre-configured for the new generation of ‘smart’ factories and are available with a choice of packages incorporating Ishida’s pioneering Sentinel™ remote customer care software. This provides users with the options of automated daily reporting of production line data, remote interventions or a live performance monitoring service.
Image -
Ishida rve multihead weighers raise the ...
Ishida is launching a new series of mid-range multihead weighers for the high performance weighing of free-flowing and semi-sticky products for a large number of of dry, fresh and frozen food applications.
The new Ishida RVE range is available in a wide choice of models – including 10, 14, 16 and 20 head models – together with a broad selection of radial troughs, hoppers (from 3 to 7 litres) and discharge chutes. This enables the weighers to be tailored to individual product requirements with models available for mono-, mixed product (handling up to four different products simultaneously) and multiple-outlet weighing, and from small to large target weights. Speeds are dependent on model and application and can reach 120 weighments per minute.
Key to the excellent performance of the new RVE weighers is the introduction of several advanced technology features from Ishida’s top-of-the-range RV multihead weighers, including programmable digital filtering and advanced automatic feeder adjustment. In addition, critical components such as loadcells and drive units are exclusively designed and manufactured by Ishida to ensure high performance standards are maintained.
An important benefit of the RVE range is that all models are pre-configured for the new generation of ‘smart’ factories and are available with a choice of packages incorporating Ishida’s pioneering Sentinel™ remote customer care software. This provides users with the options of automated daily reporting of production line data, remote interventions or a live performance monitoring service. …/
In addition, along with the proven robust construction of all Ishida weighers, the RVE WP models offer a unique ‘dew sensor’ and ‘temperature sensor’ option for the live monitoring of moisture ingress or extreme temperatures during production. Any problems, for example caused by a door cover left open or the failure of a loadcell membrane, will be immediately detected and flagged up on the weigher’s Remote Control Unit (RCU) or as part of Sentinel™ monitoring. This allows fast intervention to protect companies against unnecessary downtime and help deliver enhanced maintenance and longer machine life.
The weighers also feature a new high-processing speed ROHS-compliant RCU (Remote Control Unit), with intuitive simple-to-use controls for fast set-up and adjustments. The clear and easy-to-read screen prevents operator errors and simplifies procedures to help minimise downtime and maximise production efficiencies. Plug and play USB data import/export and Ethernet connectivity ensure easy data management.
“The new RVE range represents a major step-forward in the provision of advanced multihead weighing solutions at a competitive price,” comments Ian Atkinson, Ishida Europe’s Business Manager – Multihead Weighers.
“The speed, accuracy and reliability of every model will ensure they deliver a fast return on investment.”
Image -
Iml decoration of thermoformed packs on ...
Heilbronn and Düsseldorf, May 5, 2017 – At his year's Interpack ILLIG; the systems provider for thermoforming solutions, will be presenting its thermoforming lines in their latest stage of development customized for the demands of the food and dairy industries. In focus will be the FSL 48 form, fill and seal line with multi-lane filler and integrated IML (In-Mold Labeling) station. Moreover, the Heilbronn machine manufacturer will demonstrate the latest IML-T IC-RDM 70K production line with the compact IML RDML 70b unit for flexible decoration of nearly any cup geometry. Currently, ILLIG is the only machine manufacturer of IML-T that offers all required modules which have been optimally synchronized with one another from one source.
FSL 48 with variable filler up to hygiene class V according to VDMA
The FSL 48 form, fill and seal line developed by ILLIG is suitable for requirements by the food and particularly the dairy industry. The multi-lane filler with CIP (cleaning in place) and SIP (sterilization in place) functions can be equipped technically in such a way that it will meet the different hygiene demands by the food industry, even up to hygiene class V according to VDMA (hygienic filling machines). The hygiene levels of the machines reach from forming with sterile air, a completely closed filling range (tunnel – also available in CIP/SIP version), and with lid material sterilization by UVC radiation or H2O2 treatment. In the aseptic version the formed cups (inside) undergo additionally spraying with H2O2 steam and subsequent drying by means of hot sterile air. Everything takes place within the closed aseptic module (filling range/filler) and there is no adverse effect on machine or surroundings.
The controlled motion sequencing of the line, which is completely servo driven, results in very smooth running. This means that even very liquid products can be filled and there is no product spilling on the sealing rims of the packs. All standard materials suitable for FFS lines can be processed on the FSL 48, such as PS, PP, multilayer materials (e.g. PS/EVOH/PE), APET and even materials made of the biopolymer PLA (polylactic acid).
The FSL 48 forming area allows a complete cycle output – e.g. twelve standard curd packs – to be placed directly in a box adapted in size to the dimensions of a Euro pallet, after filling,sealing and punching. The machine is area is suitable for the production of single or double cups, 4-up or 6-up trays by adjusting of the punching tool. Dairy products, also in different flavors, can be filled in pre-labeled packs in one machine cycle using single-lane or multi-lane fillers. Four different flavors will be filled at the same time on the line presented at Interpack, with 12-up layout, at a working speed of up to 30 cycles/min.
FSL 48 combined with IML-T: Individual labeling for the food industry
The specially designed IML unit integrated in the forming station of the FSL 48 works with printed label blanks from the magazine. Numerous decoration options can thus be realized in a simple way: One-sided, two-sided, three-sided (e.g. U-shaped), four-sided or even five-sided (including bottom decoration e.g. with integrated barcode). A great variety of cup shapes can be smoothly decorated with attractive labels in photo quality since walls don't have to be vertical for IML decoration.
Inserting of labels in the mold is an additional work step in the thermoforming process. This step is performed parallel to the ongoing forming process in the FSL 48 so the high productivity (cycle speed) is still achieved. The lower mold part is designed as a cube which turns by 90 degrees with each cycle. The labels are pre-formatted before they are inserted in the mold and held in the individual cavities by vacuum with positional accuracy.
During the subsequent forming process the label bonds true to contour and permanently with the cup wall. In principle, the cup or tray-shaped pack can be designed almost without limits. The large decoration area is a special benefit provided by IML-T technology. Subject to its geometry and properties, the label increases the strength of the whole pack. Consequently, the thickness of the packaging material used can be reduced (saving of material costs), but the required top load of the pack is still achieved. The fact that every cavity of the mold can be equipped with an individually printed label is a further benefit provided by the IML-T technology developed by ILLIG. Thus a product change can be carried out fast and with only a small effort. All conventional label materials can be processed. Thus packs can be manufactured which in principle can be recycled, provided that labels and cups are made of the same material.
Cost-effective decoration with IML thermoforming
In live demonstrations at the trade fair stand ILLIG will show practical IML-T application on the IC-RDM 70K production line together with the compact RDML 70b IML unit. The 18-up mold employed will manufacture rectangular PP cups with three different decorations. In standard operation the machine achieves an output of 17,280 cups/hour. They are decorated on all four side walls and the bottom directly during forming.
In terms of costs IML thermoforming developed by ILLIG is more favorable than IML injection molding also used for decoration of plastic packs. Most cup shapes can be flexibly decorated with labels using IML-T. Moreover, investment costs for molds and maintenance costs are lower than in injection molding. Thermoformed articles can be manufactured with thinner walls and are thus lighter than injection molded articles. And furthermore less energy is required for processing in addition to the considerably lower material consumption. IML thermoforming provides economic benefits due to more cavities per mold.
ILLIG is a leading global supplier of high-performance thermoforming machines and molds, as well as solutions for the packaging industry. The company's product and services portfolio includes the development, design, manufacture, installation and commissioning of complex production lines and components. With branches and sales agencies in over 80 countries, ILLIG is locally present in all markets around the globe. For nearly 70 years, the owner-operated enterprise has been serving its customers across the globe as a reliable partner for the cost-effective manufacturing of complex precision thermoplastic parts with innovative technology of unsurpassed quality and comprehensive worldwide after-sales support.
Image -
Illig is benefiting significantly from s...
Heilbronn and Düsseldorf, May, 5, 2017 – Interpack, Düsseldorf, the international leading trade fair, has always been a useful indicator for the current economic situation and the mood in the packaging sector. For Karl Schäuble, Managing Director of ILLIG, the Heilbronn based manufacturer of thermoforming machines, this is a recurring occasion for looking back and also for an outlook to the future of the packaging technology with a focus on thermoforming. „In economic respect ILLIG could conclude the last three years very successfully and at a high level. This applies to our complete machine range“, states Karl Schäuble retrospectively and continues: „This culminated in the excellent and diverse receipt of orders in the business year 2016, the highest level of orders received in our 70-years company’s history”. ILLIG could increase sales by a good 10 % compared to 2015 which is clearly above the sector average.
A positive outlook
We are confident that ILLIG can maintain this momentum in 2017 as well“, says Schäuble. This can be primarily attributed to the new developments presented during the last two years. They were widely appreciated by our long-term customers; and this particularly applies to the IML-T technology. ILLIG thinks that in the future there will be further demand for IML-T in most markets. „For this purpose we offer to our customers a whole solution for packs with highest demands with respect to decoration – everything from one source, everything ILLIG“, states Schäuble. Moreover, at Interpack ILLIG will present its new „Pactivity“ business sector for the first time. 360° Custom-made packaging development in thermoforming, from the packaging idea to the pack and through to the production system.
Strong sales in non-European markets
ILLIG remains on the course for success and could once again expand sales in non-European markets. Today ILLIG delivers more than 60 percent of its machines and lines to non-European countries. Customers in Asia, the Arab region, as well as in North, Central and South America employ this technology to meet the increasing demands with respect to packs in their countries. ILLIG has been observing that process reliability and availability of production lines grow more and more important; also in regions outside the typical industrial countries. „Quality and hygiene demands for packs continue to increase in most regions. In economic terms this can only be realized with constant, reproducible, high product quality and high productivity at the same time“, says Schäuble.
The increasing demand for packaging machines and form, fill and seal lines is very noticeable at ILLIG. This can be illustrated by using a major contract from Iran as an example where investment is made in state-of-the-art technology. ILLIG supplies a total of nine thermoforming and packaging systems. The thermoforming machines are equipped with the latest IML-T technology as well as the current IC generation.
The packing systems are equiped with ultra clean and aseptic versions. End of line systems are also inclued.
ILLIG continues to expand its network
We founded a further sales office in Brazil due to the positive development in the non-European markets. And we signed a contract to install a customer center for thermoforming machines and molds with representatives of the Chinese local government „Administrative Committee of Zhejiang Haining Economic Development Zone“ at the last K fair“, explains Schäuble. It is the intent of Haining Economic Development Zone to establish companies of the plastic processing and supplying industries there. From Haining ILLIG will provide technical training for thermoforming technology for Chinese customers and offer on-site services. The production site in India, founded at the end of 2015, runs very well in the meantime. Production lines are manufactured for local markets.
Especially southern European markets clearly show weak investment performance since their economic growth will most likely be minimal. The same also applies to the eastern European markets, according to Schäuble.
The future of thermoforming
With a look to the future of thermoforming ILLIG sees the focus of development in the coming years on the expansion of automation and “clean” production. „We expect that in the future the increase of quality time for ILLIG lines will be of major importance, also with large batch sizes and a high automation level. This will result from the fact that we will continue to increase speeds in the thermoforming and punching process since quality and reproducibility of parts can thus be further improved. We are convinced that by optimizing the so-called planned standstill times we can considerably improve the productive running time of thermoforming lines“, says Schäuble. ILLIG also meets the requirements of the trend that batch sizes of packs are getting smaller in many sectors which calls for shorter tooling times. Cleaning intervals are also a major factor today, so increasing hygiene demands can be met. Here, ILLIG is developing solutions so dust development during material transport in the machine or during punching is prevented, as well as lubricant or oil ingress.
In Heilbronn ILLIG continued to make investments in efficient production technologies in 2016, such as the replacement of machines in mechanical processing and further optimization features in the flow assembly of individual modules and machines.
Industry 4.0 at ILLIG
The world of production and the production technology will continue to fundamentally change in the future. There is no way around Industry 4.0. ILLIG engineers succeeded in creating a significant basis with the „IC“ Intelligent Control Concept. One single module controls all steps in production sequencing and synchronizes with all compatible modules. ThermoLineControl® allows individual machines in a line to be centrally controlled by one control panel. ILLIG NetService allows direct remote diagnosis of the thermoforming line.
ILLIG is a leading global supplier of high-performance thermoforming machines and molds, as well as solutions for the packaging industry. The company's product and services portfolio includes the development, design, manufacture, installation and commissioning of complex production lines and components. With branches and sales agencies in over 80 countries, ILLIG is locally present in all markets around the globe. For nearly 70 years, the owner-operated enterprise has been serving its customers across the globe as a reliable partner for the cost-effective manufacturing of complex precision thermoplastic parts with innovative technology of unsurpassed quality and comprehensive worldwide after-sales support.
Image -
Mocon launches new map headspace gas ana...
Minneapolis (April 27, 2017) – Food companies who market their products in Modified Atmosphere Packaging (MAP) will now be able to significantly improve testing accuracy, as well as reduce the time needed to analyze oxygen and carbon dioxide headspace gas.
MOCON, Inc. (NASDAQ: MOCO), a leading international provider of instruments and services for testing, measuring and analyzing invisible gases, is launching the Dansensor® CheckPoint 3 portable, battery-powered, headspace analyzer. It will be shown for the first time at Interpack, May 4 – 10, Düsseldorf, Hall 5 / J03.
The CheckPoint 3 features the latest solid-state sensor technology which enables improved accuracy at twice the speed when compared to the previous model. The unit also offers improved measurement stability. It is ideal for a wide variety of food products in MAP including meat, seafood, cheese, snack foods, salads, vegetables, powdered milk and coffee.
“Its accuracy capabilities are particularly meaningful when the food product requires a low oxygen concentration. The more accurate your data is, the better able you will be to meet your shelf life goals,” Nick Markussen, Area Sales Manager, MOCON Europe A/S. “Regarding its capability to provide results in less than 10 seconds, if you are running more than 100 tests per day, this improved capability benefit operating efficiencies.”
Another key aspect is that the oxygen sensor on the CheckPoint 3 is expected to deliver more than a two-year “life” which represents a significant improvement. The extended sensor life means a reduction in total cost of ownership.
In addition to its significant performance improvements, the CheckPoint 3 also features a dramatic aesthetic departure from the visual appearance of traditional industrial equipment. The red arch that is part of MOCON’s visual branding, has become a structural part of the analyzer. The hollow section under the arch also provides an ergonomic resting spot so that the user’s hand can cradle the unit.
“We wanted to bring these latest capabilities to market via unique structural and visual attributes. The new structural design also enabled us to position the sensor in way to make it easier to store and use,” said Markussen.
Additionally, the CheckPoint 3 features an intuitive graphic interface and is available in three models to meet a wide variety of food processor data needs. Depending on the unit selected, data can be accessed or settings can be altered via a web browser or a smartphone.
Image -
Globally available map leak testing syst...
Minneapolis (April 20, 2017) – A fully automated, leak testing system which has been developed to help food processors ensure that individual Modified Atmosphere Packages (MAP) do not have undetected micro leaks will now be available globally.
After a well-received soft launch last year, MOCON, Inc. (NASDAQ: MOCO), a leading international provider of instruments and services for testing, measuring and analyzing invisible gases, is now expanding the availability of its Dansensor® LeakProtego first-of-its-kind on-line system. The LeakProtego has been engineered to test for potential leaks at levels lower than previously possible. This is of particular significance for processors who are pushing the shelf life envelope. The LeakProtego will be shown at Interpack, May 4 – 10, Düsseldorf, Hall 5 / J03.
Because MAP leaks degrade shelf life, compromise product safety and negatively impact brand image, MOCON’s goal was to develop an in-line system that provides food processors with package integrity information further upstream to facilitate cost savings. Currently, most food processors test for leaks further down the line when the product has already been placed into cases or shipping crates. Solving the problem at that stage becomes more labor intensive and costly.
“The LeakProtego has been commercially installed for several months and we are now able to confirm to its reliability in a food processing facility. We have also learned that the system is not sensitive to changes in the plant environment such as variation in surrounding carbon dioxide. Food processors can be confident in the data’s reliability and the ability to objectively ensure the integrity of each MAP package produced in the facility,” said Steen Andreasen, Product Manager, MOCON Europe A/S.
The LeakProtego uses a patent-pending sensing system with CO2 as a trace gas to detect leaks down to 50 microns. The technology relies on modular units, each of which can test up to 12 packages per minute. Multiple modules can be combined so that individual package testing can keep up with MAP equipment output. The modules provide processors with critical information such as individual leak size and rate so that production line optimization can be made quickly.
Typical applications for the LeakProtego include MAP pasta, bread, cheese, sliced meats and ready-to-eat meals.
Image -
Gebo cermex wins best modular machine aw...
Following a global launch at Interpack 2017, Gebo Cermex has announced that its CareSelect™ bottle infeed system has won the ‘Modular Machines’ category of the ‘Best Future Machine Award’ sponsored by Rockwell Automation.
CareSelect™ is a patented universal and modular shaped-bottle infeed and collating system for robotic or traditional case packers, powered by Rockwell Automation’s iTRAK ® technology.
Commenting on winning the category, one of five in the Best Future Machine Award’s scheme, Marc Aury, President & Managing Director of Gebo Cermex, said, “We are naturally delighted to receive this global recognition by a jury comprising some of the world’s leading brands. This demonstrates we are rightfully placing our emphasis where it matters most: to bring Smart Factories to life, to create a world of greater choice and unique consumer experience driven by packaging mass customization and product diversity.”
CareSelect™ is capable of achieving speeds of up to 400 products per minute depending on package size, shape and weight, easily surpassing traditional ‘endless screw’ collation systems in terms of bottle integrity and protection. The system delivers shaped bottles to the packing machine with precision and care in the correct orientation and pitch, turning each bottle 90°. Even unstable shaped products are smoothly and individually handled via independent movers. To eliminate contact between products, flow is managed without accumulation at the infeed and ‘friction time’ between the bottle and the system - when the bottles come into contact with machine parts - is dramatically reduced (by at least 20 times) compared to traditional infeed systems. It also offers fully automatic changeovers in less than one minute, with no need for mechanical adjustments.
Didier Saussereau, Product Manager at Gebo Cermex, said – “We have received an excellent response at Interpack to the “Smart Machine” concept that we are demonstrating on our booth. CareSelect™ is part of Gebo Cermex’s Agility 4.0™ program, which is already helping producers achieve the benefits of Industry 4.0, by making packaging manufacturing plants more connected, flexible and responsive. This award demonstrates that we have a role to play in the Industry 4.0 movement and we look forward to continuing to contribute to this journey.”
Image