Uflex to showcase advanced machine techn...
National Capital Region: India’s largest multinational flexible packaging and solutions company, is participating in PlastFocus 2024, and will feature its advanced machine technology at Booth No. A 51, Hall 1, at Yashobhoomi (IICC), Dwarka, New Delhi from February 1-5, 2024. Recognized as an ideal platform for the plastics and packaging sector, PlastFocus 2024 will feature UFlex's state-of-the-art machine technology, primed to redefine industry standards.
At the event, UFlex will highlight the technological prowess and capabilities of two of its groundbreaking machines:
CI flexo Machine: UFlex presents its CI flexo Machines, including the first-ever made-in-India gearless central impression flexo printing machine,
introduced in 2017. Building on this legacy, UFlex has ventured into manufacturing a central impression, up to 10 colours, 800-1600mm web width CI flexo printing press. This collaborative endeavor with Italy-based Comiflex has resulted in a machine that offers unparalleled performance. With a printing speed of up to 400 meters/minute, this system is equipped with modem connectivity to UFlex's service team for remote monitoring, diagnostics, and troubleshooting, ensuring real- time assistance to clients.
Combi Lamination Machine: UFlex’s Combi Lamination Machine features a digital AC vector drive and AC vector grade motor technology. This versatile model facilitates the lamination of two different substrates seamlessly using any of the two modes at a given time. The machine includes unwind and rewind features, a solvent-less coating unit, a gravure coating unit, a lamination unit, and a drying tunnel. With a speed of up to 300 meters/minute for solvent- based operations and 450 meters/minute for solvent- less operations, this machine sets new benchmarks in efficiency and performance.
UFlex invites industry enthusiasts and stakeholders interested in these pioneering technologies to experience live demonstrations of these machines at its Noida manufacturing facility. These exclusive plant visits will provide a first-hand experience of UFlex's avant-garde manufacturing processes and technological advancements. Moreover, during the visit, engage in discussions about the upcoming launch of the ELS (Electronic Line Shaft) Rotogravure Printing machine models G-24/G- 25, set to be rolled out in the near future.
Join the UFlex team at Booth No. A 51, Hall 1, Yashobhoomi (IICC), Dwarka, New Delhi, to delve into the future of printing technology for converters. The team will be available for discussions, showcasing how these machines can enhance packaging processes, taking efficiency and sustainability to new heights.
For queries: corpcomm@uflexltd.com
About UFlex Engineering business:
The UFlex engineering business vertical, established in 1985, is amongst the leading manufacturing companies for top-of-the-line packaging, printing, and allied machinery, and technical services. The engineering business is committed to providing high-performance machinery and customized solutions — that deliver global standards while reducing the total cost of ownership. The business caters to a wide range of engineering requirements — from machines with simple and basic specifications to highly sophisticated ones with advanced engineering. The product portfolio includes packaging machines, printing machines, converting machines, slitters, extrusion machines, laminators, and recycling machines. For more details, please visit: https://www.uflexltd.com/engineering.php
About UFlex Limited:
UFlex is India’s largest multinational flexible packaging and solutions company. Since its inception in 1985, UFlex has grown from strength to strength and has built a strong presence across all verticals of the packaging value chain — packaging films, chemicals, aseptic packaging, flexible packaging, holography, engineering, and printing cylinders.
With a 10,000+ strong multicultural workforce across global regions that works toward developing innovative, value-added, and sustainable packaging solutions, the company has earned an irreproachable reputation for defining the contours of the ‘Packaging Industry’ in India and overseas. It provides end-to-end solutions to numerous Fortune 500 clients across various sectors such as FMCG, consumer product goods, pharmaceuticals, building materials, automobiles, and more, in more than 150 countries. Headquartered in Noida, the National Capital Region, India, UFlex enjoys a global reach with advanced manufacturing facilities in India, the UAE, Mexico, Egypt, the USA, Poland, Russia, Nigeria, and Hungary.
A winner of various marquee global awards for product excellence, innovation, and sustainability, UFlex is the first company in the world to earn recognition at the Davos Recycle Forum in 1995 for conceptualizing the recycling of mixed plastic waste. For more details, please visit: www.uflexltd.com
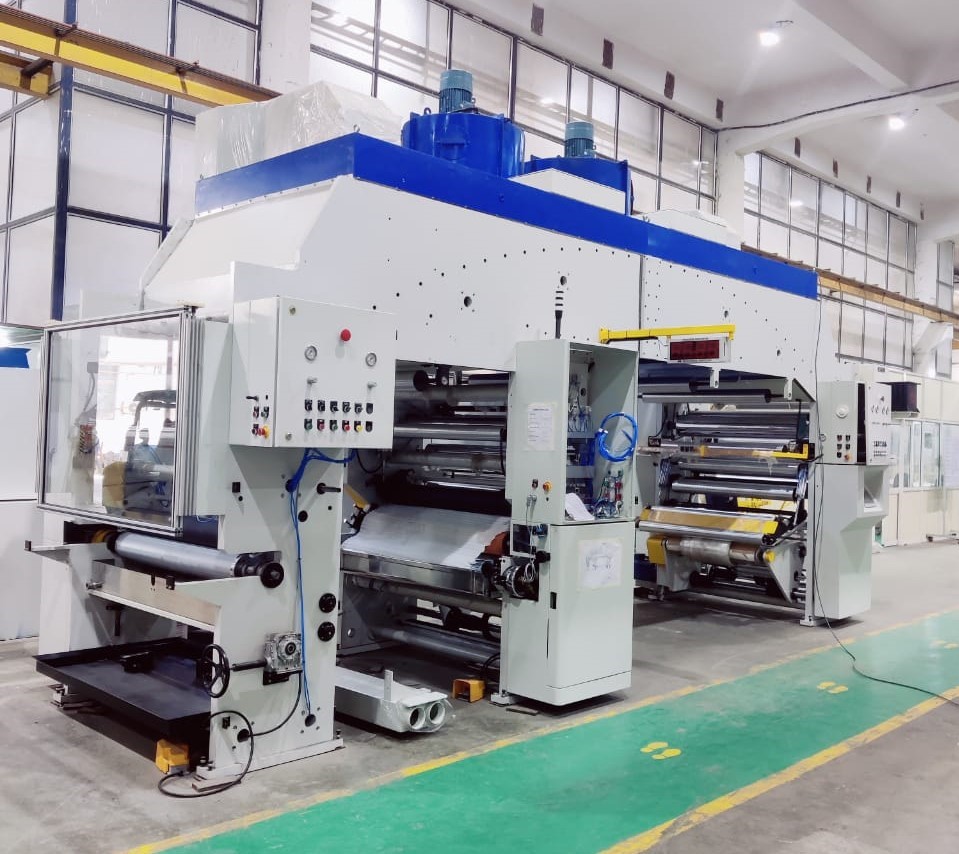