Nestlé a+ launches ‘cartons to classr...
Nestlé a+ has joined hands with Tetra Pak to launch ‘Cartons to Classroom’- a unique initiative to increase awareness about recycling in India by converting used beverage cartons to create classroom furniture for schools for less-privileged children. The initiative will begin in Mumbai and it marks the start of a long-term collaboration between Nestlé a+ and Tetra Pak, duly supported by our retail partners- Reliance Retail and RUR Greenlife, a social enterprise. Cartons to Classroom is an extension of Tetra Pak’s ‘Go Green with Tetra Pak’ Program. It brings together two important goals of increasing recycling of used beverage cartons and providing quality education infrastructure for less-privileged children.
Beverage cartons such as the ones made by Tetra Pak, are paper-based, recyclable and can be converted into useful items like classroom furniture. A key catalyst in increasing recycling of cartons are environmentally conscious consumers. With an intent to make this initiative accessible to all Nestlé a+ consumers, 54 collection points across Reliance Smart Superstores and Sahakari Bhandar outlets will be made available in Mumbai. Through these, Nestlé a+ aims at collecting more than 10,00,000 cartons which would get recycled into composite sheets, almost 100+ desks for schools.
Commenting on this initiative, Mehernosh Malia, Director- Dairy, Nestlé India, said “Nestlé a+ is proud to partner with Tetra Pak on this unique recycling initiative that not only champions the cause of responsible waste management, but also contributes effectively towards education of less-privileged children. ‘Cartons to Classroom’ program is the first step by Nestlé a+ in this long-term collaboration on sustainability with Tetra Pak. We are committed to work towards more such initiative across our brands”.
“We are happy to have the support of a reputed brand like Nestlé a+ on Cartons to Classroom, which speaks volumes about the power of partnerships. A responsible manufacturer, brand owner, retailer and social enterprise, all coming together to make a real difference in the area of environmental sustainability. Building on our flagship program Go Green with Tetra Pak launched in 2010, this campaign will bring alive how one small step of depositing used cartons for recycling can positively impact communities as well as the planet,” says Jaideep Gokhale, Sustainability Director – Tetra Pak South Asia.
“As India’s home-grown and respected retail brand, it is our responsibility to actively lead and participate in initiatives that matter. Go Green with Tetra Pak is a program that is very close to our hearts, and we are thankful to our loyal customers who have extended their support to the program for 11 years! I am confident that our customers will respond with even more enthusiasm and play their part in supporting Cartons to Classroom,” adds Damodar Mall, President & CEO – Reliance Retail
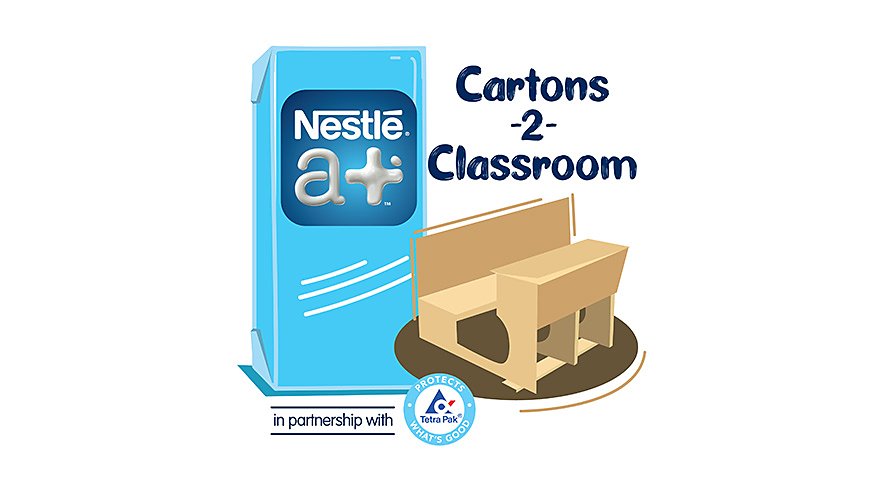