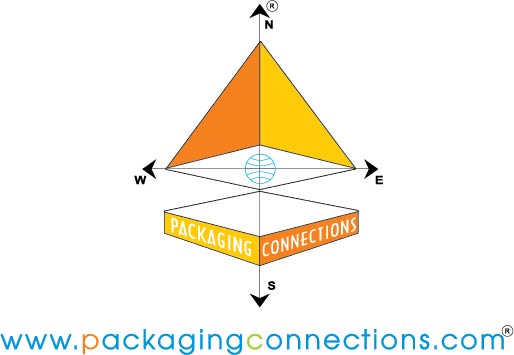
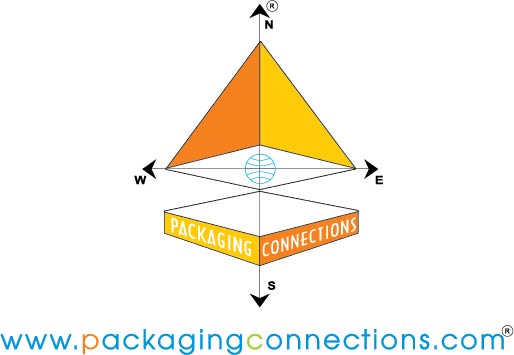
Activity
-
-
Packagingconnections webinar on sustaina...
Gurugram, India, July 27, 2020 - PackagingConnections has started with a series of webinars during July’2020. After successfully completing the first one on “Introduction to PackagingConnections”, the company is coming up with a new paid webinar on an important topic SUSTAINABILITY. The company has completed the initial research on Sustainability in Packaging and is ready to present its findings to the packaging community. The webinar will cover the current practices, challenges, and ways forward. This webinar would also take its audience through many examples that are already implemented. Details of the webinar are as follows:
Topic: Sustainability in Packaging: Current state & Way forward
Presenter(s): Grania Jain, Technology Lead PackagingConnections
Sandeep Goyal, Founder & CEO Packaging Connections
Venue: Digital world through gotowebinar platform
Date: 05 August 2020
Time: 4:00pm IST/12:30pm CET/6:30am ET/5:30am CT
Link to join: https://www.packagingconnections.com/webinar/sustainability/PackagingConnections team look forward to meet you virtually.
For more information, write to Packaging Connections at info@packagingconnections.com.
About Packaging Connections Founded in 2005, Sanex started with an online platform as “your destination for anything in packaging”. The company progressed with innovative models of bringing new technologies to world through support to foreign packaging companies. Sanex is a company of packaging professionals who have worked with multinationals for live packaging projects. This is first packaging consulting company to have ISO 9001:2015 certification. Sanex is Indian partner for top German pharma companies and have a wide network of packaging professionals across the globe. Witnessing fast brand recognition and network growth, company has come up with various verticals in packaging. The company has given niche solutions to packaging industry such as packaging brains (job dedicated portal), online packaging material store and packaging books. The newest service is into Packaging Education and the company has launched “The Big Book of Packaging - Science, Art & Technology”. Please find more details on www.packagingconnections.com/about-us.htm
Sanex Packaging Connections Pvt. Ltd.
Sandeep Goyal
CEO & Founder
Tel: +91 124 4965 770
Chhavi Aggarwal
Lead Consultant | Packaging Technology
chhavi.goel@packagingconnections.com
Tel: +91 124 4965 782
ImageDesignationLead Consultant | Packaging Technology -
How this current pandemic changed produc...
-
Mondi produces and donates protective me...
- Three Mondi plants in Germany (Halle, Steinfeld and Gronau) are set to produce and donate 10,000 protective gowns to workers in local nursing homes and retirement facilities
- The initiative will involve using extruded PE tubes to be assembled into single-use protective garments
15 May 2020 – Mondi, leading global packaging and paper group, has contributed material and processing expertise to produce plastic protective gowns for staff at local nursing homes and retirement facilities in order to help mitigate the spread of the COVID-19 pandemic in Germany. The first 100 of these disposable, single-use garments have been delivered to the regional district’s Civil Protection Authority in Diepholz, who will oversee the distribution to facilities that need it most. Mondi plans to produce at least 10,000 further gowns in the coming months.
Creating the gowns has required the collaboration of three Mondi plants alongside partnering with local company Borgerding, who will assist in the assembly of the gowns. The process has involved Mondi Halle extruding a 750 mm-diameter polyethylene film tube that forms the body of the slip-over gown. Mondi Gronau is using its R&D Centre to extrude smaller, 250 mm-diameter PE tubes that will form the sleeves on the gown, and Mondi Steinfeld is converting the bodies and the sleeves. Borgerding is manually attaching and sealing the sleeves to the bodies of the larger tube.
Mondi employees worked extra shifts over the Easter holiday weekend to help develop this solution and have already started to produce the first batch of the needed components.
Alfons Kruse, Mondi’s plant manager in Steinfeld, stated: “We’re very pleased that Mondi could respond to this request and quickly devise a solution to help protect front-line staff and health care workers in the region. As a packaging producer, it involved creatively rethinking materials and production processes in order to make protective garments. Mondi's employees rose to this challenge to support our local communities and we are proud of their work.”
About Mondi
Mondi is a global leader in packaging and paper, contributing to a better world by making innovative, packaging and paper solutions that are sustainable by design. Our business is fully integrated across the value chain – from managing forests and producing pulp, paper and plastic films, to developing and manufacturing effective industrial and consumer packaging solutions. Sustainability is at the centre of our strategy and intrinsic in the way we do business. We lead the industry with our customer- centric approach, EcoSolutions, where we ask the right questions to find the most sustainable solution. In 2019, Mondi had revenues of €7.27 billion and underlying EBITDA of €1.66 billion.
Mondi has a premium listing on the London Stock Exchange (MNDI), and a secondary listing on the JSE Limited (MNP). Mondi is a FTSE 100 constituent, and has been included in the FTSE4Good Index Series since 2008 and the FTSE/JSE Responsible Investment Index Series since 2007.
Company NameMondi GroupImage -
Plastic packaging still confronting sust...
The coronavirus has only helped to underscore the importance of plastic packaging when it comes to keeping food contamination-free and to preserving its freshness and usability for longer. This is particularly vital now, given how millions of people worldwide are sheltering in place, and doing their best to make their provisions stretch.
But the COVID-19 pandemic has also accelerated another trend that has a major impact on product packaging -- e-commerce. Online shopping already was showing strong growth, but the current stay-at-home phenomenon has only increased demand. An even broader awakening to the convenience of delivery to your doorstep may forever reshape parts of the retail sector.
An April 4 story by DigitalCommerce360 cites data to underscore the current trends.
In North America, it reported, the number of online orders for web-only online retailers soared 52% year-over-year in the United States and Canada for the period of March 22 through April 4, according to an online tracker from marketing platform Emarsys and analytics platform GoodData. Revenue for web-only retailers in the U.S. and Canada was up 30% year-over-year for the period.
In the Asia-Pacific (APAC) region during the same two-week period, year-over-year transactions for web-only retailers grew by 23%, according to Emarsys/GoodData. During the same period, year-over-year revenue was up 19% in the region.
E-commerce growing sharply
Virus or not, retail e-commerce is rising sharply. New York-based consumer research firm Statista Inc. said that U.S. online retail sales of physical goods amounted to $365.2 billion in 2019, and projects that will rise to nearly $600 billion in 2024.
Consider also that China’s annual, 24-hour online shopping spree known as Single’s Day -- last held on Nov. 11, 2019 -- generated record sales estimated at some $38 billion.
The darker side of such a sales boom relates to the impact on the environment of so much product packaging. China’s State Post Bureau reported that e-commerce giants delivered 1.88 billion packages from Nov. 11 to Nov. 16 last year, an annual increase of almost 26%. Greenpeace estimated that the waste generated exceeded 250,000 tonnes.
The volume of packaging material used by China's e-commerce and express delivery sectors hit 9.4 million tonnes last year, and is on course to more than quadruple to 41.3 million tonnes by 2025 if they keep up the rate of increase, according to Greenpeace and other non-government bodies.
Sustainability still important
So, booming e-commerce offers sales growth for key sectors as well as greater convenience (and safety) now for many, but it clearly comes at a cost. While public health trumps sustainability concerns at the moment, it’s clear that the packaging sector cannot afford to take its collective eye off the ball when it comes to being eco-conscious.
As Dow Inc. CEO Jim Fitterling mentioned in ANTEC 2020 virtual conference on March 31: The COVID-19 crisis is going to end, "but the air we breathe, our water and the land we live on is here forever. And we can't afford to lose the momentum that we've started to gain already to safeguard the environment and help us move to a more circular economy."
Leaders in the European Union also are concerned that the current virus-driven economic slump will cause the focus on sustainability to wane, writing in a joint statement in mid-April, “We should withstand the temptations of short-term solutions in response to the present crisis that risk locking the EU in a fossil fuel economy for decades to come.”
These conditions offer both extreme challenges and enormous opportunities for brand owners, consumer packaged goods (CPG) companies, and for those designing and manufacturing the packaging.
Multiple approaches being pursued
Such firms are exploring and advancing multiple strategies to address these issues, including increased plastics recycling, more reusable packaging, greater use of biomaterials, reduced material use, and design for circularity. Package designers also need to take into account the different priorities for on-shelf vs. e-commerce products. Eye-catching package design is less vital for products sold online than in the store, but ensuring the shipped product arrives at its destination undamaged is vital.
Advances in these areas take diverse forms, but consider the efforts being by CPGs to redesign the e-commerce-friendly and highly popular –– but largely unrecyclable –– flexible pouches to make them more eco-friendly. This mostly involves finding a way to convert those pouches’ multilayer, multimaterial constructions, which till now have been needed to protect the contents from such unwelcome factors such as moisture, oxygen, and ultraviolet light, into recyclable, mono-material structures.
For example: mono-material pouches
Another new technology, called AeroFlexx and developed by Procter & Gamble Co., enables liquid packaging in a flexible yet rigid package. Made with coextruded flexible film, the product leverages compressed air to inflate specific portions of the pouch, specifically along the edges, to bring a degree of rigidity not otherwise possible in a flexible package.
An AeroFlexx package uses half the plastic needed to blow mold a traditional bottle and can be delivered as roll stock to a filling facility, meaning it is easier to ship throughout the supply chain. In addition to significantly reducing plastic at the source, the Chicago-based company’s vision is to be 100% recycle ready by 2025. While enabling seamless, edge-to-edge artwork, AeroFlexx also features a no-leak, self-sealing valve that offers easy, one-handed operation by the consumer.
Loop platform touts reusability
New Jersey recycler TerraCycle Inc., meanwhile, is taking a completely different approach with its Loop circular shopping platform. Loop has gained support from many of the world’s best-known brands, ranging from Unilever, PepsiCo, and Nestlé to Danone, Procter & Gamble, and UPS.
The Loop system uses UPS to ship a variety of food, household cleaning, and personal-care products in a reusable and collapsible, padded container called the Loop tote. The products are dispensed from reusable containers, which are returned in the same reusable tote when empty. Some have dubbed it “the milkman model,” in a nod to the old days when milk was delivered to your doorstep in glass bottles, which were later collected, cleaned, and reused.
“Loop,” maintains TerraCycle founder and CEO Tom Szaky, “is an engine for CPGs to shift from disposable products that consumers own to durable ones they borrow.” The brand owners, meanwhile, actually own the package, which is meant to be reused at least 100 times. The impact on packaging is obvious – instead of trying to make the cheapest possible disposable package or container, the brands are incented instead to design handsome, reusable containers out of durable materials.
Numerous companies are also investing in initiatives and technologies to advance both mechanical and chemical recycling, and to develop biocompatible and compostable materials.
See you at CHINAPLAS 2021CHINAPLAS is further postponed to April 13-16, 2020 to be held in the Shenzhen World Exhibition & Convention Center, PR China. Focusing on “Smart Manufacturing” , “Innovative Materials”, and “Green & Circular Solutions”, the organizer is expect to present 400,000 square meters of exhibition space. For more information about CHINAPLAS 2021, please visit www.ChinaplasOnline.com.
About CHINAPLAS 2021
CHINAPLAS 2021 is organized by Adsale Exhibition Services Ltd., Beijing Yazhan Exhibition Services Ltd., and Adsale Exhibition Services (Shanghai) Ltd. and co-organized by China National Light Industry Council - China Plastics Processing Industry Association, China Plastics Machinery Industry Association, Guangdong Plastics Industry Association, Messe Düsseldorf China Ltd., the Plastic Trade Association of Shanghai. The event is also supported by various plastics and rubber associations in China and abroad.
First introduced in 1983, CHINAPLAS has been approved by UFI (The Global Association of the Exhibition Industry) since 2006. CHINAPLAS is exclusively sponsored by the Europe's Association for Plastics and Rubber Machinery Manufacturers (EUROMAP) in China for the 31st time. CHINAPLAS is currently Asia's leading plastics and rubber trade fair.
Image -
Glenroy inc. recognizes essential manufa...
MENOMONEE FALLS, Wis., May 18, 2020 (GLOBE NEWSWIRE) -- Glenroy™ Inc., an essential manufacturer and Wisconsin-based converter and printer of flexible packaging for over 50 years, is committed to the health and safety of all employees, customers, partners, and communities served during the COVID-19 pandemic. Glenroy initiated a campaign to recognize their manufacturing staff as heroes who come to work every day to continue to produce flexible packaging for essential products like food, medical supplies, sanitizers, and soap for their customers.
Products from Glenroy are essential to the supply chain and operations in critical industries, including pharmaceutical, medical device, personal hygiene care, and food that are keeping communities healthy and safe. To safely keep up with demand during the pandemic, Glenroy implemented CDC and WHO-inspired guidelines such as social distancing, increased hygiene and cleaning practices during all shifts, non-production employees working remote, virtual meetings, visitor and travel limitations, employee temperature checks, outdoor tents/tables/chairs to increase space for breaks and lunches, face coverings required for office employees on production floors, gloves required for outside vendors, and all future visitors to sign a COVID-19 symptom-free form.
Realizing the importance of its employees to produce essential products, Glenroy created a campaign to honor and recognize those manufacturing workers using the #EverydayHeroes social media hashtag and sharing photos of staff working inside Glenroy’s manufacturing facilities.
According to Tom Danneker, Glenroy President & CEO, “As an essential manufacturer, all of Glenroy’s manufacturing operations are running as normal and we are continuing to communicate regularly with our customers to meet their needs. While meeting this demand, Glenroy has remained focused on the safety of our employees and doing our part to limit the spread of COVID-19 in our community. We want to recognize not only our own employees as everyday heroes but the entire community of first responders, health care workers, and other essential workers during this time.”
About Glenroy Inc.
Since 1965, Glenroy Inc. has been a trusted converter and printer of sustainable flexible packaging. A privately-held company headquartered in suburban Milwaukee, Glenroy manufactures high-quality flexible packaging films and stand-up pouches for a variety of end uses, including food and beverage, household and personal care, pharmaceutical, nutritional, cosmetic, animal health and pet care, medical device and industrial. Glenroy is also the exclusive converter of the premade STANDCAP Pouch. For more information on Glenroy's flexible packaging solutions, visit www.glenroy.com or call (800) 824-1482.
Image -
The d-flex from haselmeier wins red dot ...
Stuttgart, Germany, May 5, 2020 - The Red Dot Jury has made its decision: The D-Flex® emerged victorious from the Red Dot Award: Product Design 2020 and won a Red Dot for its good design quality. This means that the Haselmeier Group is one of the winners in the world’s most renowned design competition.
D-Flex® - The Innovative Injection Pen from Haselmeier
The D-Flex® from Haselmeier is a product platform of a new generation of disposable injection pen systems for subcutaneous self-injection. The patented D-Flex® Technology is bridging the gap between simple fixed dose pens and normal variable-dose pens as known in the Diabetes or Hormone-Therapy. This innovative technology allows easy adaptation to the titration requirements of drugs for specific therapies where multi distinct fix doses are required. All essential fix doses can be realized on just one D-Flex® Pen. These doses can be flexible selected by the customers according to their specific requirements on the titration-scheme of the special drug. It just needs the modification of just one part of the D-Flex® Pen Platform. Thus, the customers save time and money in the development of the combination product. Furthermore, the special D-Flex® Technology creates additional value for the patient by preventing injection errors and unintended dosages, thus resulting in an improved patient safety.Red Dot CEO Professor Dr. Peter Zec on the laureates
“The winners of the Red Dot Award have proved that they have created excellent products worthy of winning an award. The products won over the jury not only through their aesthetic, but also thanks to their incomparable functionality. With their designs, the award winners are setting new standards in their industry. I wish to congratulate them most sincerely on their success,” said Professor Dr. Peter Zec, founder and CEO of Red Dot.Detailed evaluation of the products entered
The Red Dot Award: Product Design offers designers and manufacturers from all over the world a platform for assessing their products. In 2020, designers and companies from 60 countries entered more than 6,500 products in the competition. The international jury comprises experienced experts from different disciplines and has been convening for around 65 years in order to select the year’s best designs. The adjudication process lasts several days and is based on two essential criteria: The jurors test all of the entries in order to assess not just the aesthetic but also the materials selected, the level of craftsmanship, the surface structure, ergonomics and functionality. After intensive discussions, they make a decision on the design quality of the products. True to the motto “In search of good design and innovation”, only the best designs receive an award.D-Flex® in exhibitions, online and in the yearbook
On 22 June 2020, D-Flex® will be added to the exhibition “Design on Stage” in the Red Dot Design Museum Essen, where all of the award-winning products will be on show. The museum will thus be a hot spot for best-in-class industrial design. From that date, the winning product from Haselmeier will also be presented in the online exhibition on the Red Dot website. The Red Dot Design Yearbook 2020/2021 comes out in July 2020.About Haselmeier
Haselmeier, headquartered in Switzerland, is a leading provider of solutions for subcutaneous injection systems for the safe self-administration of liquid drugs. As a reliable development partner, Haselmeier offers customer-specific solutions from design and conception with prototype construction, engineering and product development to industrialization in modern production facilities. Additional services such as lifecycle management, pharmaceutical packaging, packaging design and regulatory support complement the range of services. The customized development is always based on patented proprietary platform technologies for injection devices.In addition, the company actively develops innovative digital solutions that help shape the future of smart medical healthcare. Haselmeier currently employs 240 people in six countries with sales offices in Europe, the USA and India and state-of-the-art production facilities in Buchen (DE), Dnešice (CZ) and Bengaluru (IND). Haselmeier has over 100 years of experience in the health care sector and has always contributed to reliability and success in therapy.
About the Red Dot Design Award
In order to appraise the diversity in the field of design in a professional manner, the Red Dot Design Award breaks down into the three disciplines of Red Dot Award: Product Design, Red Dot Award: Brands & Communication Design and Red Dot Award: Design Concept. With more than 18,000 entries, the Red Dot Award is one of the world’s largest design competitions. In 1955, a jury convened for the first time to assess the best designs of the day. In the 1990s, Red Dot CEO Professor Dr. Peter Zec developed the name and brand of the award. Ever since, the sought-after distinction “Red Dot” has been the revered international seal of outstanding design quality. The award winners are presented in the yearbooks, museums and online. More information is available at www.red-dot.de.
Press Contact at HaselmeierSilvia Wilkes
Marketing Haselmeier Group
Vaihinger Straße 48
70567 Stuttgart, Germany
Phone: +49 711 71978-158
s.wilkes@haselmeier.comPress contact at Red Dot
Julia Hesse
Manager PR & Communications
Red Dot GmbH & Co. KG
Gelsenkirchener Str. 181
45309 Essen, Germany
Phone: +49 201 30104–58
j.hesse@red-dot.de
www.red-dot.org/pressImageDesignationMarketing Haselmeier Group -
Retail scenario and emerging packaging t...
Businesses are to create wealth, this is the general understanding. So its said that all major industries create wealth but if there is one industry that plays a unique role by way of both creation ofPost category -
Ecosistant launches first digital compli...
According to the EU packaging waste directive and national waste legislation, online shops are obligated to license their packaging with recycling schemes in their target markets. The startup ecosistant has digitised these processes for the first time and is now offering their algorithm-based service via web-platform. Online retailers can now fulfil their legal recycling obligations cheaper, faster and more effectively.
“The licensing of e-commerce packaging is extremely complex, time-consuming and expensive,” says Andreas Landes, CEO of ecosistant. “At ecosistant, we aim to speed-up and save costs by completely digitising all compliance management related tasks.”
The new service caters to EU and UK online shops, specifically founders, compliance, logistics and operations managers in the b2c e-commerce industry.
The EU packaging waste directive governs EU-wide recycling targets for packaging waste. Producers and retailers are obligated to participate in the recycling of their packaging. For this purpose, several countries maintain public waste producer registers, such as the LUCID Packaging Register in Germany. Possible risks for non-compliant online shops include monetary penalties, trading bans, or damaged reputation for ignoring their corporate social responsibility.
By digitising the consulting service for packaging compliance with the newly developed ecosistant algorithm, online retailers experience five-figure annual cost savings. First, customers input data on their business activity and target markets. The algorithm subsequently generates manuals containing all necessary information for the customer about the prevailing recycling laws, amendments, institutions and state-licensed recycling schemes for up to 30 European countries. With steady updates of the information, ecosistant ensures that online shops always stay legally compliant across all EU member states. Clients are also consistently notified of any open tasks or deadlines through their account.
The service can be purchased annually or by paying a subscription fee over multiple years. A premium upgrade includes the handling of all operational tasks by a personal ecosistant account manager. This includes the registration and communication with recycling schemes as well as mandatory periodic declarations of packaging quantities.
Further information at www.ecosistant.eu
About ecosistant GmbH:
ecosistant is a consulting agency for recycling compliance based in Berlin, Germany. It specialises in packaging and product compliance, CSR, circular economy and other topics related to sustainability in e-commerce. The ecosistant platform enables online retailers for the first time to perform the EU-wide packaging licensing digitally. Their algorithm-based process makes it easy and quick to fulfil packaging compliance obligations at a considerably lower cost compared to conventional CSR consultants. The team is led by its founders Andreas Landes and Johannes Kohlmann.Company Nameecosistant GmbHImageDesignationCo-founder & CEO -
Corona virus-interpack 2020 postponed
New date 25 February to 3 March 2021
Messe Düsseldorf is postponing the leading international trade fair interpack. It will now take place from 25 February to 3 March 2021.In doing so, Messe Düsseldorf is following the recommendation of the crisis management team of the German Federal Government to take into account the principles of the Robert Koch Institute when assessing the risk of major events. Based on this recommendation and the recent significant increase in the number of people infected with the new corona virus (SARS-CoV-2), including in Europe, Messe Düsseldorf has reassessed the situation. In addition, there is the general ruling issued by the city of Düsseldorf on 11 March 2020, in which major events with more than 1,000 participants present at the same time are generally prohibited.
"The decision was taken in close consultation with our advisory board and sponsoring associations," emphasises Werner M. Dornscheidt, Chairman of the Board of Management of Messe Düsseldorf GmbH. It also reflects the wishes of individual industries: "As their partner, we are currently doing everything in our power to reduce the economic losses suffered by our exhibitors".
"The city of Düsseldorf is following the instructions of the state government. Our aim is to slow down the spread of the corona virus so that the health system can continue to function properly," emphasises Thomas Geisel, Lord Mayor of the state capital of Düsseldorf and Chairman of the Supervisory Board of the Düsseldorf trade fair company.
Delaying the spread of the virus as much as possible is also a declared goal according to the Robert Koch Institute (RKI). In order to fulfil Messe Düsseldorf's responsibility for risk prevention, the company primarily had to minimise the increased risk of infection at major events. Measures to reduce the risk of transmission at major events, which the Robert Koch Institute has clearly defined - such as ventilation of the venue appropriate to the risk of infection, the exclusion of persons from risk groups and the comprehensive installation of entrance screening, were practically impossible to implement. Also comparable measures were and are unreasonable in view of the unforeseeable rapid development and the size of the various events with up to 60,000 participants.
interpack’s industry partners support the decision to postpone the fair and together with those responsible, are counting on a successful event next year. "interpack is the absolute top event for the international packaging industry and related processing industries. The trade fair thrives on personal encounters and direct exchange between people from all over the world. This is only possible if there are no health risks involved. Therefore, the postponement is responsible and right. We are looking forward to next year's event to discuss the issues that are defining the industry, such as sustainability, and to present appropriate solutions," comments Christian Traumann, President of interpack 2020 and Managing Director & Group President at Multivac Sepp Haggenmüller SE & Co. KG.
"The corona virus and the associated restrictions now represent a major challenge for the entire mechanical engineering sector. The possible and currently unforeseeable effects of the pathogen with an incalculable risk of infection, the threat of quarantine for returnees, general travel restrictions in some countries, but also considerable travel restrictions on the part of many companies unfortunately make it impossible to successfully hold the interpack in May. The VDMA, as a supporting association of interpack, welcomes a postponement under the given exceptional circumstances. The new date now ensures reliability in planning" says Richard Clemens, Managing Director of the VDMA Food Processing and Packaging Machinery Association.
The Düsseldorf hotel industry is also sending out an important signal through its umbrella organisation DEHOGA (Trade Association for the Hospitality Industry): "We appeal to our members and the entire industry to be flexible when it comes to rebooking by exhibitors and visitors. The Düsseldorf trade fairs such as interpack play an enormously important role for the city, the hotel industry and the catering trade. It would be counterproductive not to show goodwill in this situation,” as both DEHOGA-Representatives Giuseppe Saitta (Chairman Düsseldorf/District Group Rhein-Kreis Neuss) and Rolf D. Steinert (Düsseldorf/Rhein-Kreis Neuss Hotels and Tourism Group) emphasise.
Werner M. Dornscheidt is pleased about the general consensus and encouragement in this special situation: "We would like to thank all our partners for their excellent cooperation in making these difficult and time sensitive decisions. We are pleased that together a date was found so quickly in order to allow all those affected to reliably plan."
Image -
Uflex invests in laser scoring technolog...
Noida, 03 April 2017: Have you felt the angst of standing under the shower trying to tear a shampoo sachet which simply refused to yield and finally you had to bite it open? Quite a nightmare --- isn’t it?One of the most important dimensions of flexible packaging is ‘Convenience’ of handling which also happens to be a pivotal component of the pack’s functionality. The moment this convenience is compromised upon, the utility of packaging nose dives - and simultaneously erode with it, consumers’ faith & confidence and brand image.
“As India’s largest multinational flexible packaging materials and Solution Company, one of the commonest asks that our clients have from us is to incorporate easy to open features” says, Mr. Arun Anand, Executive Vice President Marketing at Uflex Packaging.
“Uflex has been the first company to introduce laser scored flexible packaging in India. By the sophisticated Laser Scoring Technology the outermost layer of a laminate is incised with laser beams. Virtually every type of incision can be made by this technology. Predefined tearing path is created which guides the end-user to conveniently open the packaging. Commendable is the fact that all of this is done without compromising the barrier properties required by the product packed inside.
One of the conventional tools that have been used to create tearing paths on flexible packaging is serrated cutter fitted on Form, Fill and Seal Machines. This is not considered as a very conducive option as the tool gets worn out with a frequent need of replacement.
With the laser scoring technology we are able to offer a non-contact, clean processing solution that eliminates the need for mechanical tooling or associated consumables. The laser system is capable of precise scoring process that adds accurate features not obtainable through other mechanical methods. This also reduces production downtime, as pattern or design modifications are made rather instantaneously.
The high-quality laser scoring technology that we have invested in provides the ability to precisely and consistently score flexible packaging at controlled depths at varying web speeds. Score lines are created in specified areas of the film/laminate, forming a narrow channel in the material for a tear to follow. Effectively, a laser weakens targeted layers of packaging material to produce score lines without compromising the barrier properties of the flexible film. Various laser scoring configurations like half-moon cut, wedge cut, umbrella cut, slant cut to name a few are possible at our packaging manufacturing plants” adds Mr. Anand.
“With the help of the value added laser scoring technology we have offered easy to tear flexible packaging solutions to various FMCG brands of snack food, ketchups, condoms, pet food, tea, coffee, rice, spices etc. For a leading snack brand in India, we engineered a three layered laser scored diaphragm (opening) comprising PE/MET PET/PE which has spelled tremendous ease of opening for end-users. The demand for laser scored easy to open flexible packaging has been on a rise not only in India but in overseas as well” concludes Mr. Arun Anand.
Emphasizing upon easy to open flexible packaging, Mr. Ashok Chaturvedi, Chairman & Managing Director, Uflex Limited said, “Ease of opening a pack for accessing the product is fundamental to an end-user’s overall experience. Some substrates within a laminate are really difficult to tear open without using a cutter/ blade. In line with our business strategy of innovation to create value added differentiation to the advantage of our clients, we have invested in sophisticated laser scoring technology that permits perfect incision in a laminate at controlled depths and variable web speeds. This in turn allows the consumers to easily open the pack, adding to experiential delight and upholding the very ethos of flexible packaging.
About Uflex
Uflex is India’s largest multinational flexible packaging materials and Solution Company and an emerging global player. Since its inception back in 1985, Uflex has grown from strength to strength to evolve as a truly Indian Multinational with consumers spread across the world. Uflex today has state-of-the-art packaging facilities at multiple locations in India with installed capacity of around 100,000 TPA and has packaging film manufacturing facilities in India, UAE, Mexico Egypt, Poland and USA with cumulative installed capacity in excess of 337,000 TPA.
All Uflex plants are accredited with ISO 9001, 14001, HACCP & BRC certifications. Uflex caters to markets spanning across the globe in over 140 countries like USA, Canada, South American countries, UK and other European Countries, Russia, South Africa, CIS, Asian and African nations. Integrated within its core business profile are allied businesses like Engineering, Cylinders, Holography and Chemicals which further give Uflex a superior edge above competition.
Uflex Limited is also a part of the D&B Global Database and winner of various prestigious national and international awards for its products’ excellence. Uflex offers technologically superior packaging solutions for a wide variety of products such as snack foods, candy and confectionery, sugar, rice & other cereals, beverages, tea & coffee, dessert mixes, noodles, wheat flour, soaps and detergents, shampoos & conditioners, vegetable oil, spices, marinades & pastes, cheese & dairy products, frozen food, sea food, meat, anti-fog, pet food, pharmaceuticals, contraceptives, garden fertilizers and plant nutrients, motor oil and lubricants, automotive and engineering components etc.
Some of Uflex’s clients on the global turf include P&G, PepsiCo; Tata Global; Mondelez, L’ Oreal, Britannia, Haldiram’s, Amul, Kimberly Clark, Ferro Rocher, Perfetti, GSK, Nestle, Agrotech Foods, Coca Cola, Wrigley, Johnson & Johnson among others.
For further information, please contact:
- Rohit Sharma, Manager, Investor Relations, PR & CSR, Uflex Limited
Mobile No.: 09910300187
E-mail: rohit.sharma@uflexltd.com
Image -
Absolut comeback bottle celebrates recyc...
Absolut Vodka works with Ardagh Group to create their recycled ‘Absolut Comeback’ bottle
The latest limited-edition bottle from Absolut Vodka epitomises a circular economy, highlighting the need to recycle and reuse our existing resources.The Absolut Company, together with communication and design agency Drama Queen Communications, first briefed Ardagh Group’s Design Team to create a bottle design based on recycled glass, to promote and visualise the benefits of recycling. Together they developed the ‘Absolut Comeback’ design: a bottle using actual pieces of broken, recycled glass, reflecting the recycled glass that goes into every Absolut Vodka bottle.
To create the ‘recycled’ bottle design, Ardagh’s designers used the reverse engineering technique. Product Designer, John Oczabruk explains:
“Because this is a completely original bottle design, we first needed to create a sculpture by attaching pieces of recycled Absolut bottle glass to a 3D print of an Absolut bottle, to maintain the bottle’s iconic look and shape.“The reverse engineering began by digitally scanning the sculpture into our modelling system, then reconstructing the design to work smoothly in Production.”
The detailed process required a pan-European approach: UK, Swedish and German design teams were all involved, using 3D prints, digital scanning and virtual sculpting techniques to create the final 3D shape.
The result is an impressive ‘recycled glass’ version of the iconic Absolut vodka bottle, which symbolises the bottle’s recycled content and aims to celebrate recycling and inspire others to recycle too, for more sustainable, circular living.Further information
Rebecca Firth, Marketing & Communications at Ardagh Group, Glass – Europe,
Email: rebecca.firth@gmail.com, +44 7789 403893Image -
Ar metallizing announces acquisition of ...
Berlin, 8 November 2019
Global leading metallized paper manufacturer AR Metallizing announces today that it has secured a deal to acquire Eurofoil Paper Coating GmbH (hereinafter: Eurofoil) in Berlin. The closing of the transaction is subject to approval of the German Cartel authorities.
Read further in German here
Eurofoil is a leading European manufacturer of laminated and metallized inner liners. In the past 60 years they have built a comprehensive portfolio of inner liners encompassing laminated, metallized and pure slitted and coated paper products.
The Berlin plant is well-equipped and enjoys a strong asset base with highly automated equipment, including water-based lacquering and metallizing lines, which are among some of the fastest in the world. The plant enjoys all the key certifications to serve its customers efficiently.
Extending AR Metallizing’s global reach with a factory in Berlin will complement the company’s existing plants in Belgium, Italy, North America and Brazil. Eurofoil will eventually be rebranded to AR Metallizing. Staff will be fully integrated into the company, taking AR Metallizing’s global headcount to approximately 700.
‘The acquisition of Eurofoil is the ideal next step in AR Metallizing’s growth strategy, allowing the team to increase production capacity and better serve our growing customer base,’ says Dr. Bart Devos, AR Metallizing’s CEO. ‘This newest acquisition also gives us the opportunity to continue the expansion of our innovative product portfolio and increase our R&D facilities. Incorporating Eurofoil will allow us to work towards our goal of positioning AR Metallizing as a leading provider of choice for multinational firms looking to use eco-friendly, paperbased packaging and labelling materials. Through the acquisition, AR Metallizing will also be further developing and serving our customers with an increased number of products for direct food contact,’ adds Bart.
‘Nissha continues to encourage the growth of our subsidiary, AR Metallizing. The acquisition of Eurofoil marks a new chapter for AR Metallizing, and they can count on Nissha’s ongoing support as they look to extend the portfolio of products available under the AR Metallizing brand, most notably sustainable paper based materials’, says Junya Suzuki, Chairman of the Board, President and CEO of Nissha.
‘We’re delighted that AR Metallizing will acquire our Berlin facilities,’ says Managing Director Michael Koblitz of Eurofoil. ‘Particularly, we are looking forward to being part of a global company that’s reputed in the industry for its product quality and customer care – qualities that very much match Eurofoil’s company spirit,’ continues Michael.
About AR Metallizing
AR Metallizing is the global market leader in the manufacturing of metallized paper and paperboards for use in the food, beverage and consumer packaging goods industries. AR Metallizing is a subsidiary of Nissha. Nissha is listed on the Tokyo Stock exchange and is highly regarded for its technological leadership.
Press Contact:
Mail: Henriette.vanhedel@mauperville.com
Cell: +31 6 303 97 830Image -
Rondo-pak hires new senior vp of sales &...
Packaging Industry Veteran David Phillipes Joins Leading Healthcare Sector Provider of Folding Cartons and Printed Components
Camden, NJ – Rondo-Pak, a leading provider of quality folding cartons, printed components to the pharmaceutical, medical device and consumer industries, has hired packaging industry veteran David Phillipes as Senior VP of Sales & Marketing. In this role, Mr. Phillipes will collaborate with the company’s senior-level executives to develop sales strategies for Rondo-Pak’s two core markets: packaging solutions and printed marketing materials.
Mr. Phillipes joins Rondo-Pak in the wake of the company’s recent strategic merger with Contemporary Graphic Solutions, as well as a move into an expanded facility in Camden, NJ. The relocation included a $30 million investment in new state-of-the-art printing and finishing equipment, added and enhanced services and capabilities, and increased warehousing capacity for a more streamlined order fulfillment process. The facility will be home to several new packaging technologies currently under development.
Mr. Phillipes brings with him a wealth of experience. Most recently, he served as a sales leader for Rohrer Corporation, a specialty packaging manufacturing company in the carded blister and visual packaging sectors. He also has deep experience in the pharmaceutical folding carton, leaflets and labels business, having served as VP of Sales for both Multi Packaging Solutions and Caraustar. Mr. Phillipes also held the position of Director of Sales at Cadmus/Cenveo, where he was responsible for pharma market brand positioning via packaging and printing solutions.
“With his impressive professional background, David is well suited to help Rondo-Pak continue to develop its unique value proposition: the ability to create solutions that provide the precision of packaging with the agility of marketing,” said Victor Dixon, President & COO of Rondo-Pak.
Mr. Phillipes is a member of several industry organizations, including PDE and HCPC. He earned a degree in Chemical Engineering from Georgia Tech. He has been married for 26 years and is a father of two; he resides in Emmaus, PA.
About Rondo-Pak
Rondo-Pak is a global print and packaging specialist providing effective solutions and comprehensive services to the pharmaceutical and life sciences industries.
Rondo-Pak’s unique core competency is the combination of packaging and support materials including an extended range of printed packaging formats such as inserts, leaflets, medication guides and regulated marketing materials. The company’s portfolio of sophisticated packaging solutions addresses precise requirements for compliance, child resistance, anti-counterfeiting, e-pedigree and more.
Rondo-Pak has been a recognized leader in pharmaceutical folding cartons for over 70 years, and is a proud part of the Körber Medipak Systems network of companies.
For more information visit www.rondopak.com
Image -
Propak asia 2019 at 85% capacity
SPACE AT PROPAK ASIA 2019 IN HIGH DEMAND WITH LIMITED STANDS REMAINING
Known as Asia’s number one packaging and processing exhibition ProPak Asia 2019 is at 85% capacity of the 60,000 square metre location with four months remaining until the show opens.
According to Mr Justin Pau, General Manager of UBM Asia (Thailand) Co., Ltd, there are a number of zones within the show that have wait lists, which is a reflection of the standing that the show has in the ASEAN Region.
“To be held from the 12 to 15th of June in Bangkok, Thailand, ProPak Asia has been serving the ASEAN Region for 27 years and is the regional hub for connecting packaging and processing manufacturers and suppliers,” Mr Pau said.
“We anticipate that ProPak Asia 2019 will showcase over 20,000 products and solutions across 1900 exhibitors from 50 countries within 9 zones over 4 days. There will be 18 pavilions from 13 countries including Australia, China, Denmark, France, Germany, Italy, Japan, Korea, Singapore, Spain, Taiwan, UK, and USA,” he said.
ProPak Asia is divided into nine targeted zones for visitors including ProcessingTechAsia, PackagingTechAsia, DrinkTechAsia, PharmaTechAsia, Lab&TestAsia, Materials Asia, Coding, Marking & Labelling Asia, Coldchain, Logistics & Warehousing Asia and Printech Asia.
Mr Pau added that ‘ProPak Asia 2018 attracted 48,799 buyers from 79 countries which saw a 9.19% increase from the previous year, and we are really excited about the projections for 2019,’
“With ProPak Asia being an established brand in the ASEAN Region the show receives a high number of international visitors and buyers with the Top 12 Asian Countries attending from Philippines, Malaysia, Singapore, Japan, China, Myanmar, Vietnam, Cambodia, India, Indonesia, Korea and Sri Lanka. The figures show increasing demands for technology and automation solutions and a global belief that ProPak Asia is Asia’s most important destination for anyone in the processing & packaging industries,” Mr Pau said.
“ProPak Asia welcomes everyone from across the globe to come and join us for our 27th show on the 12th to 15th of June and for those companies still deciding whether they should exhibit we would recommend that you don’t delay.” he said.
…ENDS…
This media release has been written and distributed by UBM Asia (Thailand). For further information on ProPak Asia please email Wantita Porntanawong Wantita.P@ubm.com
Image -
Uflex sweeps away seven titles for packa...
January 09, 2019, Noida (India): Uflex was recognized with seven awards at the recently concluded SIES SOP STAR AWARDS 2018 for packaging innovation and product development. In its endeavor to support and encourage the packaging sector, The SIES School of Packaging announced the awards for excellence in packaging with emphasis on Innovation, Creativity, Development and New Concepts.
The eminent jury members followed a strict judging criteria based on innovation & creativity, graphic design & improved aesthetics, user friendliness & new developments, thus recognizing the R&D efforts of Uflex in developing newer materials, forms, process, machinery and technology in the field of packaging.
The Winners of SIES SOP STAR AWARDS 2018 are:
Sr NoProduct
Category
Description
1
Beach Magic – High Barrier Tube for Sunblock Lotion
Flexible Packaging – (Innovation / Creativity / Development)
A unique personal product in flexi tube, with high graphic reproduction in a matte surface, which provides premium aesthetics with sharp images.
2
Forest Essential Shampoo – Premium Matte Finish with Hot stamping
Flexible Packaging – (Innovation / Creativity / Development)
A uniquely created flawless white tube with sharp printing and silver stamping that enhances the brand prominence and makes it premium in the shelves.
3
Oshea Herbals – Premium Tube for Personal product
Flexible Packaging – (Innovation / Creativity / Development)
A wide format 360 printing in different shades represent a range of products. The pastel shades created identifies products and have excellent consumer attraction.
4
Rasna Fruit Juice Concentrate – Shaped profile pouch with spout and handle
Flexible Packaging – (Innovation / Creativity / Development)
The stand-up pouch made from high barrier laminate with unique shape and spout. The design feature includes spill free ease in dispensing and complete use of product.
5
Teenager Bra – Inner garment packaging with anti-counterfeit feature
Flexible Packaging – (Innovation / Creativity / Development)
The package essentially addresses to the daunting challenges from duplicates through a holographic image of brand logo, embedded company name with multiple security elements.
6
Richie Plus Ajwain – Metallic effect in 2 ply transparent laminate
Flexible Packaging – (Printing / Graphics / Aesthetics)
The development highlights technology capability in printing and special cylinders and ink. The unique combination of metallic and transparent areas provides high POP influence and consumer benefits.
7
Cimmo Petrochem Carbon Black – Block bottom valve bag
Product Packaging – (Innovation / Creativity / Development)
Woven laminated block bottom bag with self-closeable valve provides higher productivity, high space utilization besides excellent product protection.
Expressing delight over this win, Amitava Ray, Executive Director at Uflex Ltd. said, “I heartily thank the Jury of SIES SOP STAR AWARDS for recognizing the efforts of Uflex in today’s packaging world. Packaging is an integrated component of any system besides being an essential input in its distribution and marketing management. Packaging, considered a luxury till recently, has now gained recognition as a need of the industry, country and the society. These awards serve as a testament towards the value added differentiation that we create for each of our customers and will keep motivating us to do even better.”
About Uflex:Uflex is India’s largest multinational flexible packaging materials and Solution Company and an emerging global player. Since its inception back in 1985, Uflex has grown from strength to strength to evolve as a truly Indian Multinational with consumers spread across the world. Uflex today has state-of-the-art packaging facilities at multiple locations in India with installed capacity of around 1,35,000 TPA and has packaging film manufacturing facilities in India, UAE, Mexico Egypt, Poland and USA.
All Uflex plants are accredited with ISO 9001, 14001, HACCP & BRC certifications. Uflex caters to markets spanning across the globe in over 140 countries like USA, Canada, South American countries, UK and other European Countries, Russia, South Africa, CIS, Asian and African nations. Integrated within its core business profile are allied businesses like Engineering, Cylinders, Holography and Chemicals which further give Uflex a superior edge above competition.
Uflex Limited is also a part of the D&B Global Database and winner of various prestigious national and international awards for its products’ excellence. Uflex offers technologically superior packaging solutions for a wide variety of products such as snack foods, candy and confectionery, sugar, rice & other cereals, beverages, tea & coffee, dessert mixes, noodles, wheat flour, soaps and detergents, shampoos & conditioners, vegetable oil, spices, marinades & pastes, cheese & dairy products, frozen food, sea food, meat, anti-fog, pet food, pharmaceuticals, contraceptives, garden fertilizers and plant nutrients, motor oil and lubricants, automotive and engineering components etc.
Some of Uflex’s clients on the global turf include P&G, PepsiCo, Tata Global Beverages, Mondelez, L’Oreal, Britannia, Haldiram’s, Amul, Kimberly Clark, Ferrero Rocher, Perfetti, GSK, Nestle, Agrotech Foods, Coca-Cola, Wrigley, Johnson & Johnson amongst others. For more details, click on: www.uflexltd.com
For further information, contact:
Media Queries:
Aarti Laxmanan Kanika Sood
Uflex Limited PR Professionals
Mobile No: 9899813325 Mobile No: 9873744888
E-mail: corpcomm@uflexltd.com Email: uflexpr@prproessionals.inImage -
Nicelabel named one of the leading softw...
NiceLabel has been named to the FL 100+, Food Logistics magazine’s annual list of the top 100-plus software and technology providers for the food and beverage industry. The list serves as a resource guide of software and technology providers whose products and services are critical for companies in the global food and beverage supply chain.
Food Logistics magazine, dedicated to covering the movement of product through the global food supply chain, this week released the 15th annual FL100+ list of software and technology providers that hold influential roles in the global food and beverage supply chain. Their products benefit the industry in multiple ways, from reducing food waste and extending shelf life, to facilitating safe and sanitary transportation of product while assuring regulatory compliance.
“The digital supply chain continues its rapid emergence, bringing with it expanded capabilities that impact visibility, security, compliance and efficiency,” remarks Lara L. Sowinski, editorial director for Food Logistics and Supply & Demand Chain Executive. “Every aspect of the global food supply chain stands to benefit from new and innovative software and technology that is fundamentally changing the global food supply chain.”
"We are honored to have again been selected among the 100 leading technology companies supporting the global food and beverage supply chain," said Ken Moir, VP Marketing at NiceLabel. "NiceLabel's next generation technology and professional services help F&B suppliers of any size digitize their labeling, reduce direct and indirect costs and avoid missed opportunities. F&B companies need to be agile enough to adapt to changes in the market, and have the most effective processes in place to ensure labels are accurate, available and compliant. Whether that means implementing an on-premise label management system or turning to the cloud for help, the outcome is the same: better labelling and better safety for consumers.”
Companies who earned a spot on the FL100+ list are featured in the current issue of Food Logistics, as well as at the magazine’s website.
Image -
Matrix demonstrates high speed iqf bagge...
Visit Matrix at the 2019 Northwest Food & Beverage World, January 8-10, in the Oregon Convention Center, Portland, Ore., Matrix Packaging Machinery, a ProMach brand, will be showcasing its high speed Morpheus XL vertical form/fill/seal (vf/f/s) bagging machine. The focus at the show, will be demonstrating the high-speed large bag solution for IQF filling solutions. (Matrix Booth #1031)
Matrix has advanced engineering that has optimized the Morpheus XL for quality sealing at high speeds with multiple film types, including film used in individually quick frozen (IQF) packaging. At the show, Matrix will simulate how Morpheus XL forms, fills and seals a pillow bag for frozen French fries using craft paper/poly film. The Morpheus XL is capable of producing pillow and gusted bags from 2.75 inches wide all the way up to 15 inches wide and up to 25 inches in length. With its fast, precise changeover and broad range of bag sizes and types, a single Morpheus XL can replace two slower and older machines for significantly lower capital investment and reduced labor costs on the packaging line.
Matrix’s unique servo-based adjustment system AutoPro ensures fast, accurate, and trouble-free changeover – faster by a minimum of 50 percent over competitive machines. AutoPro gives processors and contract packagers the ability to run a greater number of stock keeping units (SKUs) on the same line without the downtime and labor-overhead penalty associated with frequent changeover. AutoPro comes standard on all Morpheus models.
The Morpheus series is the most advanced vf/f/s platform in the company’s history in terms of overall speed, film handling, servo axis adjustment, ease of operation, and lowest overall cost of ownership. For more information on the innovative Morpheus XL, call 888-628-7491 and visit www.MatrixPM.com. Be sure to stop by the Matrix Booth #1031 at NWFPA 2019 for a demonstration.
Image -
Clariant unveils controled-atmosphere pa...
- Regional premier of EQius™ brand humidity-control products
- Shelf-life prediction service simulates packaging conditions
Mumbai, December 19, 2018 – Clariant, a world leader in specialty chemicals presented new products that help control moisture and prevent degradation of packaged pharmaceuticals at CPhI India, 2018. Clariant Healthcare Packaging exhibited its full range of desiccant canisters and packets, tubes and desiccant stoppers, oxygen scavengers, Advanced Desiccant Polymer (ADP) and humidity stabilizers at stand 14.A30 in Hall 14 at the trade show that was held at the India Expo Centre in Greater Noida, India, from December 12 to 14, 2018.
The show marks India debut of Clariant's new EQius brand , which encompasses all of the products and technology related to Equilibrium Relative Humidity (ERH) stabilization. These include products currently marketed as EQ-Pak®, EQ-Can®, EQ-Stopper™, and EQ-Bag™, along with the raw material that goes in them. The different forms make it possible to customize humidity control throughout the drug-product development cycle, from bulk ingredients to finished pharmaceuticals.
Matthias Brommer, Head of BL Healthcare Packaging, BU Masterbatches said, “India is a growth engine for the pharmaceutical industry and one of our main reasons for building a dedicated plant in Cuddalore to the highest quality and regulatory standards. It was a decision in the right direction and helps us to adjust to the dynamic demand of our customers and to offer shorter lead times. We will continue to invest in our capabilities here and expand our product offering for local & export markets.”
autam Arora, Sales Head for South Asia Region, BL Healthcare Packaging, BU Masterbatches, said, “With pharmaceutical regulations getting stricter across the globe, Clariant is there to support its customers with high quality product backed up with regulatory documentation. The exhibition was of special importance to us this year as it gave us a chance to present to our customers the expanded product offering that we will have from our world-class manufacturing facility in Cuddalore.”
Our experts in Clariant Healthcare Packaging discussed Clariant’s Stablus® predictive simulation service. "Pharmaceutical stability and shelf life depend on protective packaging that maintain optimal conditions for sensitive compounds even as ambient conditions change. Identifying the ideal packaging solution can be difficult and time-consuming, but Stablus can narrow the range of options through simulation, even before physical testing,” added Gautam.
Clariant Healthcare Packaging manufactures a full range of controlled atmosphere packaging solutions including pharmaceutical desiccants, equilibrium sorbents, adsorbent polymers, oxygen scavengers and pharmaceutical closures and containers. Using both active and passive packaging technologies, Clariant offers an array of standard components and complete systems, as well as full innovation and development capabilities. By understanding customer needs and expectations, Clariant is able to offer comprehensive and viable solutions that increase efficiency, reduce costs and improve the environmental compatibility of products.
Image -
Clariant offers new perspective on susta...
- Discover Clariant’s solutions for a sustainable city at Booth 7-123
- High performance additives and colors for future-proof, convenient trend-focused coatings
- New products & Automotive Styling Trendbook 2021-23 launches
Muttenz, December 19, 2018 – Clariant, a world leader in specialty chemicals, teases the first insights into its immersive European Coatings Show 2019 showcase inspired by the global need for sustainable cities (Booth 7-123).
Under the theme ‘Think.Do.Paint! For a new perspective’, Clariant invites visitors to discover colors and additives developed to help decorative, industrial and automotive coatings make a sustainable difference to the various elements of the urbanization megatrend: homes, buildings, construction, transport and lifestyle products.
In addition, the colors of the future for automotive exteriors are ready to be explored with the launch of Clariant’s new Automotive Styling Shades Trendbook 2021-2023.
People from all key industries and end market application areas for paints and coatings will be able to find added value benefits and application design freedom from the wide range of innovative Clariant products available:
Safer, easier to use, sustainable solutions for homes, buildings & construction
- New sustainable 2-in-1 dispersion additive for manufacturing safer, easier to apply, biocide-free formulations that are suitable for ecolabeled indoor paints for home and building decoration.
- New dispersant additive for waterborne organic and selective inorganic pigment and carbon black concentrates, offering enhanced colors, improved storage stability, low foaming and easier formulation.
- Sustainable wax additive based on 100% renewable resources, providing smooth touch and high scratch resistance to wood and offering enhanced pigment dispersion to increase color strength of powder coatings.
- Clariant EcoTain® certified light stabilizers for waterborne coatings, suitable for plastic, clearcoat and architectural façade coatings, bringing sustainability and performance together.
- Non-halogenated flame retardants – colorless key ingredient for transparent intumescent wood coatings, suitable on dark and light colored wood, meeting stringent fire regulations for public building applications, and ingredients for steel prolonging the shelf-life of water-based intumescent coatings and improving safety under challenging weather conditions.
- Efficient and economic production of high volume color shades for industry applications such as container ships, agricultural and construction machinery and off highway vehicles.
- Structuring of megacities with decorative roadmarkings manufactured with easy dispersible technologies.
Sustainable color boost for ‘lifestyle’ consumer goods, equipment & vehicles
- Sustainable high-performance DPP (Diketopyrrolopyrrol) pigments for brillant colors, with very high resistance to heat and UV weathering, for industrial, decorative and automotive coatings.
- Ready-to-use ‘super transparent’ preparations based on non-halogenated pigments for fast creation of latest designer colors and eye-catching metallic and mineral effects for consumer products needing a high quality aesthetic surface finish.
- Launch of Clariant’s new Automotive Styling Shades Trendbook 2021-2023.
Visit Clariant’s Business Units Additives, Industrial & Consumer Specialties, and Pigments at European Coatings Show 2019 at the Nuremberg Exhibition Center, March 19-21, 2019.
Image