manufacturers of aluminum tubes and aer...
Düsseldorf, February 01, 2021 - The manufacturers of aluminum tubes and aerosol cans organized in the German Aluminium Association (GDA e. V.) got away with a black eye in 2020. The demand for aluminum tubes declined only slightly by around one percent, as the good demand from the pharmaceutical and food sectors almost offset the decline in cosmetic products.
Deliveries of aluminum aerosol cans to Germany fell by around 9 percent due to lower sales in the core market of deodorants. Despite the brisk demand for disinfectants in the first quarter of 2020, the industry was not nearly able to compensate for this decline. Nevertheless, the overall result in 2020 is still moderate compared to other end-use markets in the aluminum industry.
"Due to the ongoing pandemic, the slow start of vaccinations and the associated restrictions for the population in Germany and Europe-wide, the market situation is expected to remain difficult until the middle of the year, because customers plan carefully and drive on sight", says Johannes Schick, Chairman of GDA’s Division for Tubes, Cans and Impact-Extruded Parts. In particular, the demand from the cosmetics market will continue to suffer from the mobility restrictions, as the shops in the cities will be closed at least until mid-February and other important sales channels such as duty-free shops in airports are also shut down. A sustained upturn in the market is only expected from the third quarter of 2021. Until then, the market situation will remain rather erratic.
Aluminum packaging fully in line with EU's Green Deal
The recyclability of packaging will play an even more important role in 2021. Here, aluminum packaging can score because it can be recycled almost infinitely without any loss of quality. The current recycling rate for aluminum packaging in Germany is 93.2 percent.
The growth potential for aluminum packaging in the German packaging market is considerable because it currently only accounts for around one percent of total packaging consumption in Germany. Coupled with the outstanding protective performance of aluminum, which efficiently prevents product spoilage and loss, an ecologically convincing overall package is delivered. Aluminum packaging is therefore fully in line with the EU Commission's Green Deal approach for more resource efficiency and sustainability.
_____________________________________
Contact:
Gregor Spengler
Gesamtverband der Aluminiumindustrie e. V. (GDA)
T + 49 211 4796-144
gregor.spengler@aluinfo.de
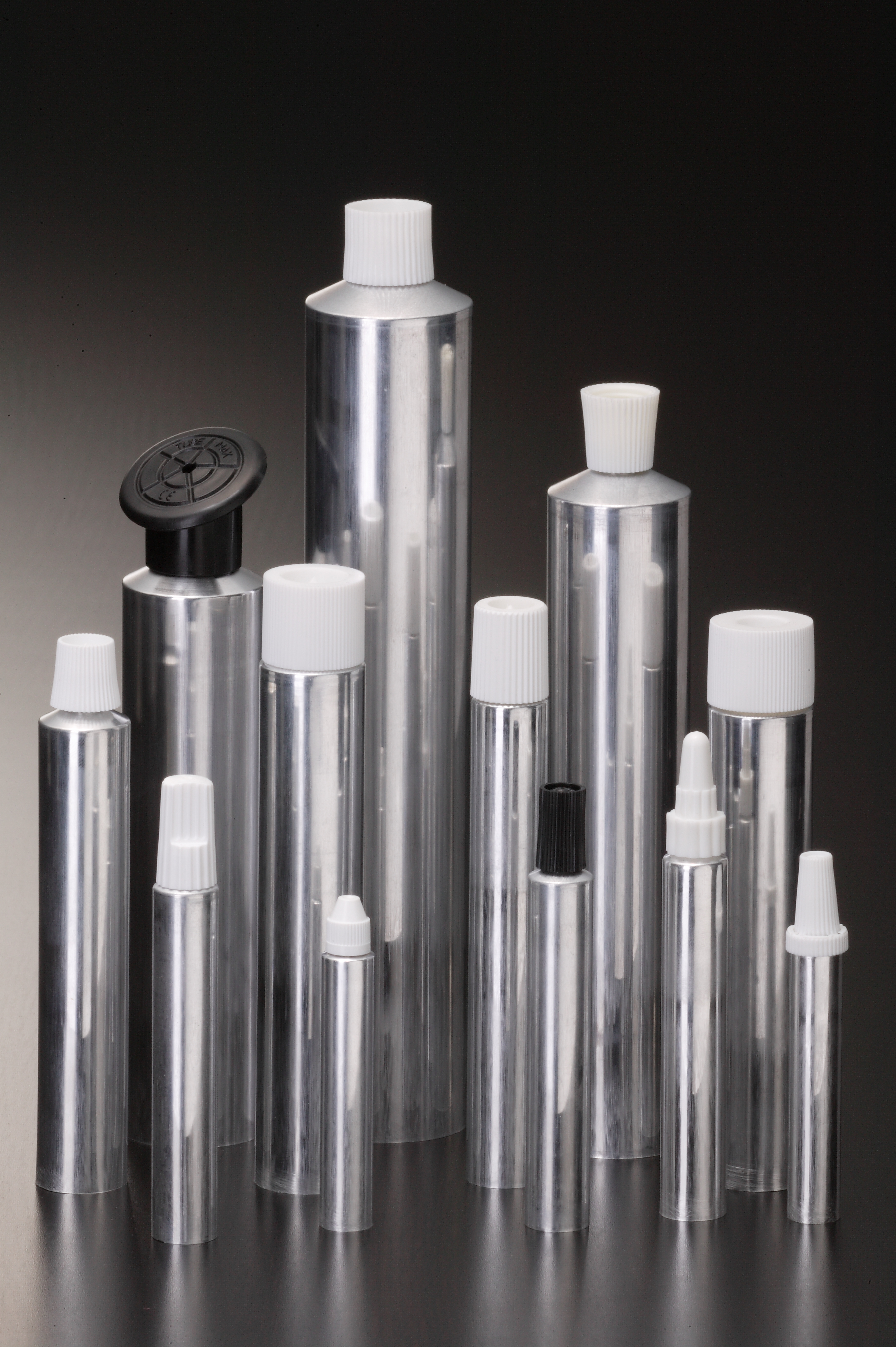