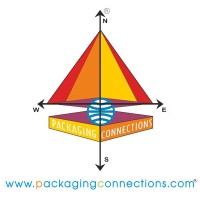
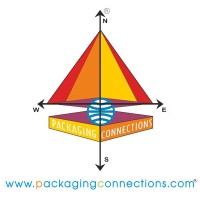
Sustainability in the packaging industry has transformed from being merely a buzzword to becoming a vital focus and a genuine commitment for numerous companies. Here's why:
Concrete Actions: Many companies have taken substantial steps towards sustainability. They're investing in research and development to create eco-friendly materials, implementing efficient manufacturing processes, and designing packaging that minimizes environmental impact.
Regulatory Compliance: Companies are adhering to increasingly stringent environmental regulations. This isn't just about compliance but showcases a genuine effort to align their practices with global sustainability goals.
Consumer Demand: The shift in consumer preferences towards eco-friendly products has been a significant driver. Companies are responding to consumer demands for sustainable packaging, realizing that it's not just a trend but a market necessity.
Corporate Responsibility: Many organizations have incorporated sustainability into their core values. They understand the responsibility they hold in reducing their ecological footprint and contributing to a better environment.
Innovation and Collaboration: Collaboration across the industry for sustainable solutions and innovations in materials, processes, and supply chain management is evidence of the industry's genuine commitment to sustainability.
Reporting and Transparency: More companies are openly reporting their environmental impacts and sustainability efforts. They are actively pursuing transparency, which suggests a genuine commitment to accountability.
While there might be instances of greenwashing—superficially promoting eco-friendly efforts without substantial action—many companies are earnestly working towards sustainability. The global acknowledgment of climate change and environmental concerns has made sustainability an imperative goal rather than just a marketing strategy. Although challenges exist, the packaging industry's concerted efforts demonstrate that sustainability is more than a buzzword; it's a fundamental objective shaping the future of the industry.
In the pursuit of culinary perfection, chefs adhere to a creed of precision, excellence, and finesse.
In a world where snack enthusiasts often face the dilemma of breaking their snack pouches while trying to access thei
Ypsomed recognizes the mounting challenges posed by ever-increasing regulatory requirements, intricate project planni
The "Blue Angel" is a voluntary and prestigious product label that has been granted for over four decades in Germany,
DS Smith is proud to announce the inauguration of 'R8,' its groundbreaking Research & Development (R&D) and I
"Sustainable Drinks Producer Broadland Drinks Partners with Frugalpac for Mass Volume Filling of Low Carbon Paper Bot
In the pharmaceutical industry, ensuring quality assurance in the crimping of vials is of utmost importance. The quality of sealed vials, achieved through proper crimping processes and the use of high-quality seal caps, is vital for ensuring patient safety and product integrity.
Vaccine vials, commonly used for injectable solutions, consist of a glass vial sealed with a rubber stopper and an aluminum seal cap (e.g., flip-off cap). This sealing process plays a critical role in protecting the product from contamination and environmental factors, as well as maintaining medication safety and product integrity.
Choosing the right crimping equipment is crucial, especially in high-speed filling lines. It's essential to ensure that the equipment can efficiently crimp aluminum caps onto vials and glass bottles while maintaining the highest quality standards. Look for equipment that offers adjustable rotation speed, table height, and crimping pressure settings, allowing for precise control over the crimping process. Additionally, opt for hardened crimp jaws to enhance equipment durability and reduce maintenance costs.
Quality control in crimping vials involves assessing the crimping technique and the quality of the crimp cap itself. Proper adjustments of pressure and height during crimping are essential to avoid over-crimping or under-crimping, which can lead to product defects and issues such as coring, inadequate sealing, or evaporation problems. Closure Integrity Tests (CCIT) are vital for ensuring hermetic sealing and leak-free vials.
A quality aluminum seal, such as a flip-off cap, guarantees a perfect seal every time. These caps offer tamper evidence, safety features to protect against contamination, and ease of use. Once removed, the lid cannot be resealed, ensuring product integrity. Various shapes, colors, dimensions, and printing options are available to enhance safety and product differentiation.
By following these quality control measures and using high-quality crimping tools and caps, pharmaceutical manufacturers can maintain the highest quality standards, ensuring the safety and reliability of crimped vials used in pharmaceutical applications. This commitment to quality is essential for upholding patient safety and maintaining trust within the pharmaceutical industry.
If you have any queries or require further information, please don't hesitate to get in touch with us. Reach out to us at growth2@packagingconnections.com or info@packagingconnections.com, and we'll be happy to assist you.
For more details, you can also visit our partner page: Partner Page Link
We look forward to serving your pharmaceutical seal needs!
Ahlstrom Expands Its Range of Sustainable Packaging Tape Solutions
Berry Global has achieved a significant milestone in the packaging of hazardous liquids through its advanced technica
Respectueuse, the eco-friendly cosmetics brand, has proudly introduced a new product line featuring Sonoco's innovati
German health food and wellness retailer, Vom Achterhof, has successfully transitioned its product packaging for sele
By using multiple sources of energy, Robustex