Wax paper packaging
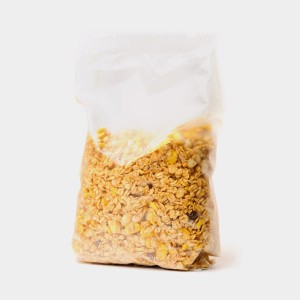
Stora Enso’s pulp customers are getting more and more questions about their products’ sustainability and if these pro
• Airnov continues to invest strongly in the local Chinese market with state-of-the-art manufacturing sites in Changshu and Dongguan
• Airnov currently produces a range of sector-leading products, including HAT®-SNAP, HAT®-IN and desiccant packets
• China Association of Clinical Laboratory Practice Expo (CACLP) moved to June
Airnov Healthcare Packaging, a global leader in controlled atmosphere packaging, continues its strong support of the Chinese market after recent investments in expanding its production capabilities across a range of product lines.
As a global leader in shelf-life preservation solutions, Airnov’s products are designed to protect pharmaceutical, nutraceutical and diagnostic products from moisture and oxygen.
Airnov’s dedicated diagnostic portfolio includes HAT®-SNAP, HAT®-IN and desiccant packets.
HAT-SNAP is an active and ergonomic vial featuring a container with temper-evident desiccant stopper.
HAT-IN, meanwhile, is an active and ergonomic flip-top container featured with an advanced desiccant polymer (ADP) technology integrated into the vial itself, to provide a high moisture barrier, as well as excellent moisture adsorption to protect even the most sensitive test strips and nutraceutical products.
Airnov also produces a range of desiccant packets at its Chinese facilities, located in Changshu and Dongguan.
These include the Continu-Strip® packets and the rimless packets, available in a wide range of sizes. These packets are typically used in rapid tests, urinalysis strips, ELISA kits and a variety of in-vitro and clinical diagnostic devices.
“The Chinese market continues to be of crucial importance to Airnov,” commented Albert Zhao, General Manager of Airnov Asia Pacific. “It is a key reason why we have state-of-the-art manufacturing facilities operating in the cities of Changshu and Dongguan.”
Airnov remains committed to growing its presence in the Chinese market having recently invested in expanding capabilities at Changshu. The modernization of the site 150 kilometers northwest of Shanghai includes the installation of new production lines that enables the company to produce a wider range of products at greater volumes.
This includes HAT-SNAP, which is seeing heightening demand due to the growing Chinese market.
“No matter what product our customers seek, Airnov guarantees high quality, complete compliance certification of FDA, EU and NMPA, and a stable supply for customers both in China and around the world,” added Albert Zhao.
Airnov is due to participate to the 19th edition of China Association of Clinical Laboratory Practice Expo (CACLP). The event was scheduled for March 2022, but is now postponed and set to be held in Nanchang City on new dates of June 10-12.
About Airnov Healthcare Packaging
Airnov Healthcare Packaging is a global leader in shelf-life preservation solutions to protect pharmaceutical, nutraceutical and diagnostic products from moisture and oxygen. This includes drop-in sorbents such as canisters and packets, integrated desiccant systems, and specially designed container-closure systems. Airnov has five manufacturing plants located in France, the U.S., China, and India
Pianoro (Bologna) – Marchesini Group is reopening the doors of its factories and once again investing in Italian trade fairs and major corporate events for customers, stakeholders and students. Despite the highly volatile international situation due to both the conflict in Ukraine and to challenges relating to energy and raw material supply, the Group hopes to return to face-to-face meetings following the difficult years of the pandemic.
From 26 to 30 April, partially coinciding with the Cosmopack trade fair in Bologna, the first Open House of the cosmetics division will be organised, showing guests the Beauty Division opened last year: 5,500 square meters where technologies and workers connected to the cosmetic packaging world have been concentrated. During the Open House, visitors will be shuttled between the BolognaFiere pavilions and the Pianoro plants, where they will be guided along themed routes and take part in gastronomic and recreational events, the best way to resume social interaction in the workplace.
Immediately after the end of the Open House, company logistics will be reorganised for another event named Open Door Pharma: in parallel with the Pharmintech fair in Milan (3-6 May), from 2 to 6 May, the gates of the Pianoro plants will remain open for guests from the pharmaceutical industry, who will be able to witness the launch of the new corporate sustainability project enhanced by the presence of machines that use paper rather than plastic or organic plastic instead of normal PVC in their packaging cycles.
The program will end with the Talent Open Days, scheduled from 9 to 13 May: five days dedicated to schools and universities, which will allow students from technical institutes in the area and from universities to witness the production stages in person and to talk to their peers undertaking internships and to specialists.
“After two years of teleconferencing, remote testing, and stalled international travel, we are finally starting to plan in-house physical events again. Among other events, one of the most important trade fairs in our industry, the German Achema, will take place in August this year. We have taken the opportunity to further invest in Italy” commented Marchesini Group board member Valentina Marchesini. “This is a terrible time for many people not far from us; we hope that our return to social interaction will be a good omen”.
The company’s renewed openings, which have always been appreciated by industry professionals, will also benefit from a confidence booster provided by the latest company figures, which show strong business growth: the 2021 consolidated turnover returned to growth, approaching a threshold of 500 million euros (490 million, + 9.1% compared to 2020), 76% of which was generated by exports.
This performance can be partly attributed to strong demand for packaging lines for Covid vaccines. In 2021 alone, these sales accounted for 46 million euros of consolidated turnover, generated by orders that include individual lines and machines involving the entire vaccine packaging process, from filling in bottles to packaging in pallets.
The cosmetic packaging machine segment, which in recent years has joined the core pharmaceutical segment, also achieved impressive results.
Its growing share of consolidated turnover – 44 million euros (+8.9% compared to 2020) – is the successful outcome of targeted investments in the sector: the latest was the creation of the company’s Beauty Division, which reorganised and extended the production of the MG Beauty, Axomatic, V2 engineering, Cosmatic and Dumek brands. Despite the decline in interest during the pandemic for products such as lipsticks and creams, the growth in cosmetic sales has confirmed the public’s enormous interest in beauty products, no longer limited to women.
“The figures tell us that in these two years, despite the difficulties, we have been resilient and shrewd. We had to change our priorities but this allowed us, for example, to understand that we can assemble a production line in six to eight months instead of the standard twelve” stressed CEO Pietro Cassani. “When everything becomes more stable, some things will remain, such as certain remote testing, while others will become a new norm such as the application of flexible hours for entry to work at our locations. The pandemic accelerated existing market dynamics, which will change again – enormously – as a result of the conflict in Ukraine. Continuing to be resilient is the only possible solution for all of us”.
Problem-solving, industry-changing packages garner top awards from the Flexible Packaging Association (FPA)
Neenah, Wis. – Amcor – a leader in global consumer packaging – is the proud recipient of three 2022 Flexible Packaging Achievement Awards, winning across multiple categories out of a record number of entries. The awards recognize Amcor for solving complex customer challenges, advancing sustainability and elevating the overall contribution of flexible packaging.
The awards were presented during the FPA Flexible Packaging Achievement Awards Ceremony and Welcome Dinner on March 23 in Bonita Springs, Fla.
Amcor Flexibles North America Research and Development Vice President Brian Carvill accepted the awards for the company.
Amcor received a Gold Award for extending the use of flexible packaging with the AmPrima™ Recycle Ready Pouch for the Tyson® Instant Pot family meal kit; a Silver Award for Technical Innovation with the Clear Anti-Grease jerky pouch; and a Silver Award for Sustainability with AmPrima™ Recyclable PE shrink film with 30% post-consumer recycled content.
“We are honored to once again be recognized for innovative achievement by the FPA,” said Carvill. “These winning packages demonstrate how Amcor applies deep material science capabilities to create exciting opportunities for brands, and a better experience for consumers. This year’s awards reflect the resiliency of our research and development teams.”
The winning entries spanned a range of packaging applications and categories:
Amcor’s AmPrima™ Recycle Ready Pouch for Tyson® Instant Pot Meal Kits received a Gold Achievement Award for ‘Expanding the use of Flexible Packaging.’
The pouch replaces a three-part tray, lidding and overwrap system with a single, convenient high-barrier carrier eligible for consumer recycling at store drop off locations or curbside where available. The new pouch leans into consumers’ increased demand for recyclable packaging and achieves Tyson’s goal of incorporating more sustainable materials in their brand packaging, providing an 80% reduction in overall carbon footprint and a 75% reduction in packaging weight. It is also produced using 84% less water and eliminates chloride-based PVC materials.
The Clear Anti-Grease Jerky Pouch received a Silver Award for ‘Technical Innovation.’
This unique, high-barrier pouch material is extremely effective in preventing grease buildup and scratches on clear meat snack packaging, a long-standing problem for hard, high-fat products like jerky.
Improved optics help Amcor customers create brand advantage among meat snacks – a category with record growth.
Proprietary anti-grease agents are included in the barrier film’s sealant layer to repel fats and resist abrasion, which provides a clear view of the product and a premium brand image while being efficient to produce and delivering consistent, reliable, anti-grease properties across the entire package.
AmPrima™ Recyclable PE Shrink Film with 30% PCR received a Silver Award for Sustainability.
A recyclable shrink film with renewable content, AmPrima™ PE shrink film with 30% post-consumer content offers the billion-dollar beverage industry a more sustainable alternative to corrugate and traditional shrink wrap.
AmPrima™ Recyclable PE film reduces upstream product waste and resource use. It also lowers greenhouse gas emissions by up to 10% and uses 24% less energy in the distribution channel over the conventional 100% virgin solution. It supports production efficiency by not compromising line speeds or machinability; qualifies when clean and dry for store drop-off and can be reclaimed in curbside recycling in certain U.S. communities.
The FPA Achievement Awards have been showcasing industry innovations that have changed the packaging industry since 1956. This year’s nominees included a record 325 entries across 100 package samples (some packages were entered in multiple categories), which resulted in twenty-seven packages being honored.
First things first – how are you and your colleagues?
To get the inside story on these updates, we caught up with Gian de Belder, technical director of R&D packaging s
CheMondis, the leading marketplace for chemicals in Europe, has partnered with trustshare, an escrow infrastructure for online B2B marketplaces. CheMondis will offer all buyers and suppliers a simple, fast and cost-efficient way to pay while ensuring maximal protection for both parties.
The platform helps buyers and suppliers to establish new bThrough this partnership, CheMondis is further strengthening its position as the leading European marketplace for chemical products. Along with its partners, CheMondis is continuing to shape the digital future of trade in the chemical industry usiness relationships, it automates order flows for existing business relationships and it provides profound data insights for market participants to improve their business efficiency. The platform has now made the next step to facilitate digital trade: the launch of online payment and escrow services for their users.
The new feature is enabled by a partnership with trustshare, an escrow infrastructure developed primarily for B2B marketplaces like CheMondis. It allows buyers and suppliers to choose a safe way of payment directly embedded into the platform. Next to the mere transfer of funds, this payment service includes an escrow option, which adds extra security and trust to the network. The buyer pays in advance; yet funds are only released after successful and satisfactory shipment and delivery.
Sebastian Brenner, Managing Director of CheMondis, said: “CheMondis’ Payment Services aim at further growing the trust between buyers and suppliers of chemicals during their negotiations on our marketplace. We believe that Payment Services will help in connecting, innovating, and digitalizing the chemical industry.” trustshare, CheMondis’ partner for this service, provides a solution where buyers can checkout into a dedicated account for their order on the marketplace. The supplier can see the payment has been made, so it is safe to ship the products.
Once the order is fulfilled, the buyer releases the funds to the supplier for payout. This process is superior to traditional pay on invoice and payment in advance services in speed, transparency, security and costs.
Through this partnership, CheMondis is further strengthening its position as the leading European marketplace for chemical products. Along with its partners, CheMondis is continuing to shape the digital future of trade in the chemical industry
About CheMondis:
CheMondis is the leading B2B marketplace for chemicals in Europe, connecting buyers and suppliers from the chemical industry. With about 10.000 verified companies and more than 80.000 available products, it combines chemical expertise with outstanding technological know-how. Founded in 2018, CheMondis aims at building a global professional network to provide information and new business opportunities.
Solution uses historical analytics to predict component performance, streamlining and customizing maintenance for decreased downtime.
WIPOTEC-OCS, a leading manufacturer and supplier of precision in-motion weighing, track and trace/anti-counterfeiting solutions and X-Ray scanning equipment, will introduce new predictive maintenance functions for its line of high-precision catchweighers at MODEX Booth #B7232, March 28-31 in Atlanta. The analytics-driven solution allows parcel processors to proactively predict when its catchweighers will need maintenance, resulting in well-planned tune-ups that minimize downtime.
The new tools essentially allow catchweighers operators to “see the future,” providing a more accurate picture of when maintenance will be needed. The result is a data-driven ability to anticipate when a component actually needs repair or replacement, rather than the comparative guesswork of general guidelines and recommendations.
With WIPOTEC-OCS’ predictive maintenance solution, a potential part failure can be detected at an early stage, then proactively prevented without interrupting operations – a downtime minimization that quickly meets and exceeds the cost of investment. The system also allows parts to be utilized for their actual lifespan rather than their recommended one. The resulting additional usage for any number of components can amount to significant spare parts savings. Finally, much of the data obtained from implementing predictive maintenance software – including optimal throughput for the most accurate checkweighing – can be applied to boost overall equipment effectiveness and productivity.
WIPOTEC-OCS catchweighers feature the company’s signature Electro-Magnetic Force Restoration (EMFR) weigh cells, a next-generation technique that guarantees optimal weighing results even at high line speeds. The machine features a revolving weighing system that segregates each product, weighs it independently, and returns it to the line, providing exemplary accuracy even at high speeds. The resulting precision helps eliminate reputation-damaging underfills or costly overfills.
WIPOTEC has consistently been at the technological forefront for quality control solutions in the materials & logistics sectors. For example, the company’s HC-FL-T Triple Scale Catchweigher combines three hardware scales into six virtual ones, each capable of operating independently – a feature permitting product gaps as narrow as 10” (250mm).
The HC-FL-T’s triple scale design delivers a 60% throughput increase at the same speed as a double scale design, while guaranteeing first-class performance and durability. Depending on product length, the triple scale catchweigher can weigh as many as three products simultaneously. The HC-FL-T can accurately weigh up to 19,000 parcels/hr at transport speeds up to 3.4 m/s (670 ft/min). The use of a high-tech electro-magnetic force restoration (EMFR) weigh cell delivers NTEP weighing accuracy of 50g even when running at top speed.
WIPOTEC-OCS, Inc. is a leading manufacturer and supplier of precision in-motion product weighing, X-Ray scanning, product inspection, parcel dimensioning, package marking, and serialization and aggregation equipment. The company's weighing, inspection, and track and trace solutions serve applications in a broad array of industries, including pharmaceutical, food, chemical, cosmetics, healthcare, e-commerce and logistics.
Located in the Atlanta, GA suburb of Lawrenceville, WIPOTEC-OCS headquarters includes a demonstration showroom, customer application engineering labs, a spare parts warehouse, and state-of-the-art meeting and training rooms. The company is part of Germany-based WIPOTEC group, which employs more than 1,000 people worldwide and has been pioneering dynamic weighing solutions for more than three decades. For more information, call (678) 344-8300 or visit http://www.wipotec-ocs.com/us/.
The need to sustainably transform the food industry and find alternative sources of nutrition has never been more pressing, concludes a report by the U.S. Food and Agriculture Organization (FAO). As a technology partner to the industry, GEA aims to lead the way to tomorrow’s safe, accessible and affordable nutrition by driving game-changing advances in the novel food market. At Anuga FoodTec 2022 in Cologne, GEA will showcase its new pilot line for cell cultivation and fermentation that allows customers to fast-track cellular agriculture’s development from the laboratory to commercial production.
“We will be providing a sneak preview of how technology can help combat increasing food insecurity. Our Anuga showcase under the guiding principle of ‘A Taste of Tomorrow’ will shine a light on GEA’s model New Food initiative, which promotes innovation in the emerging cellular agriculture sector,” says Heinz-Jürgen Kroner, Senior Vice President Liquid & Filling Technologies at GEA. Highlight will be a modular, Mobile Test Center to help customers pilot and scale these new foods.
From the lab to the factory
For the first time, GEA will showcase its Mobile Test Center (MTC) for new food applications. Available for customers to rent or purchase for use on their own or GEA’s premises, this fully equipped, pilot-scale process line for cell cultivation or fermentation can be individually configured.
“While laboratory setups alone are enough to provide experimental evidence that a particular formula or cell growth might work for a specific end product, it is only possible to evaluate those results and develop a viable concept for industrial scaling with a pilot line. Our MTC turns concepts into reproducible processes,” says Kroner. In a word, the GEA Mobile Test Center will bridge the gap between laboratory work and demo plants. Using the test center, customers are able to not only determine parameters ranging from cell viability through mass balance to yield but also to efficiently design processes and develop a future-proof business model for subsequent commercial production.
Reliable concept studies to go
Up until now, making the leap from lab testing novel foods to validating processes on an industrial level has required a significant investment in a demo plant – despite there being no guarantee of success. With its Mobile Test Center, GEA is offering a new way of providing proof of concept for cellular agriculture. Best of all, customers do not need to invest in a full pilot plant to facilitate the process of scaling up to commercial cell-based manufacturing. Instead, they can use the MTC to study cell cultures and microbes as well as improve fermentation strategy, modify formulas, alter growth media and ingredients plus tweak process parameters so as to increase yield and repeatability.
“We need to not only find new ways of feeding people but also to make that food readily available and affordable,” says Kroner, describing the challenge. “Since GEA is a technology expert, this is where our strength lies – in providing our customers with an exceptionally high level of investment security when they enter into novel foods.”
Mobile Test Center with an end-to-end process line
The MTC comprises eight industry-approved, food-grade technologies, including the GEA multifunctional fermenters or bioreactors as well as equipment for mixing, heat treatment, homogenization, separation and filtration. With the freedom to alter the sequence of the various steps and add or repeat process stages, customers are empowered to test cultivation and fermentation strategies as well as product recovery. Thanks to the test center’s flexible process architecture, GEA can individually configure, install and commission the plant on site.
Images (please use the link to download high-resolution material; the link is valid for 30 days)
Fig. 1: Available for customers to purchase, rent or use on GEA’s premises, the GEA Mobile Test Center (MTC) is a fully equipped, pilot-scale process line for manufacturing cellular and acellular new foods. Photo: GEA
GEA Mobile Test Center technologies
Fig. 2: GEA BATCH FORMULA® PRO High Shear Mixer: Capable of blending end products with a solids content of up to 80 percent or a viscosity of up to 100,000 centipoise, this high shear mixer can handle complex products. Photo: GEA
Fig. 3: GEA UHT pilot plant: This plant is a flexible, highly automated system that indirectly heat treats liquid products such as cell culture media or dairy products. Photo: GEA
Fig. 4: Bioreactor/fermenter (pilot line consists of two units with 50-liter and 500-liter volume): GEA’s plug-and-play bioreactor or fermentation solution is available in two sizes and can be used either for cell cultivation and/or fermentation reactions. The adaptable two-in-one pilot plants are suitable for scaling development processes and producing test batches. The picture shows the 500-liter version. Photo: GEA
Fig. 5: GEA Ariete Homogenizer 3030: During homogenization, cell membranes are mechanically ruptured, releasing their contents, which can then be separated and further processed. The GEA Ariete high-pressure homogenizers ensure optimum cell disruption with high flow rates, making them ideal for industrial processing in cellular agriculture. Photo: GEA
Fig. 6: Self-Ejection Separator FSE 10: As part of the downstream process, the GEA centrifuge separates biomass from the fermentation broth. This stabilizes the product feed and consistency, helping to ensure the repeatability of the membrane filtration and other downstream processes. Photo: GEA
Fig. 7: Crossflow ceramic microfiltration plant: Thanks to ceramic microfiltration (CMF) membranes that act as a physical barrier, unwanted solids, bacteria and cells are trapped and separated from the valuable product. That means the unit is particularly good at containment, i.e. protection by way of isolating processes which, for instance, involve genetically modified organisms (GMOs). Photo: GEA
Fig. 8: Crossflow membrane filtration plant for ultrafiltration: Equipped with spiral polymeric ultrafiltration membranes, this versatile membrane filtration plant is suitable for product clarifying or fractioning as well as for concentrating and washing. Photo: GEA
Accessed through a simple smartphone app, vivid three-dimensional projections remain accessible well after the show.
the U.S. subsidiary of Maruho Co. Ltd, a Japanese healthcare company with subsidiaries in Europe and the U.S. with global sales of $800 million – is inviting visitors to this year’s WestPack to take its featured machines home with them. Virtually, that is.
The blister packaging equipment supplier will be showcasing two of its most popular machines, the EAGLE-Omni and EAGLE-Rx, at WestPack Booth #5358, April 12-14 in Anaheim, CA. In addition to live demonstrations of the physical machines, MHI will feature a special augmented reality station where attendees can view, interact with, and project each machine in full size.
In fact, the experience can last well beyond WestPack itself: The technology allows attendees to examine and interact with vivid, 3D projections of the machines at their individual facilities (or anywhere else), simply by accessing a smartphone app. A necessary invention developed during the COVID-19 pandemic, the protracted virtual showcase is designed to lead to more comprehensive, informed pre-purchasing decision-making for potential customers.
Measuring just over two meters in length and 1.6 meters tall, the reasonably compact EAGLE-Omni offers a format area of 150x95 mm, and a forming depth of 30mm (3cm) with an upgrade available to 40mm. Performing forming, sealing and punching operations at sequential stations, the versatile machine handles a wide range of forming materials – including PVC, PVDC, ACLAR, PP, PET and ALU – and all typical lidding substrates including ALU, paper, PVC, PET, and laminates.
Ideal for packaging development, materials testing and production, the EAGLE-Omni can produce up to 20 blisters per minute, and is suitable for packaging solids, powders, liquids or devices. Notably, the option of a 40mm forming depth makes it ideal for nutritional products larger than traditional tablets or capsules, such as gummies, devices and other delivery formats.
Meanwhile, MHI’s Eagle-Rx is a high-performance blister packaging machine capable of producing up to 200 blisters per minute at a format area of 90x130mm. Featuring a compact balcony design, the unit can be operated by a single person with no formal training required. The Eagle-Rx offers toolless, recipe-driven changeovers, making it ideal for efficiently alternating between multiple products with varying batch sizes. Its servo technology ensures repeatability and minimizes mechanical adjustments.
For both machines, a key differentiating benefit is the ease and expediency with which prototypes can be produced, thanks to MHI’s groundbreaking 3D-printed blister tool prototyping capabilities.
About Maruho Hatsujyo Innovations
Maruho Hatsujyo Innovations (MHI), the U.S. subsidiary of Maruho Corp. Ltd., was created in 2014. MHI distributes the high quality medical packaging machinery produced by Maruho Hatsujyo Kogyo (MHK). With more than 220 employees, MHK has over 60 years of experience in the manufacturing sector, including the design of high-performance blister machinery and high-precision metal components. MHK is Japan’s second largest medical packaging machinery company.
Mondi, a global leader in packaging and paper, has unveiled a state-of-the-art flexo printing line at its plant in Gronau, Germany. The new machinery will service the hygiene industry’s growing demand for advanced printing options for films and laminates and deliver greater flexibility in feminine care pouch wrapping designs and film choices.
Mondi’s investment in the ten-colour flexo press means the company is now able to supply flexo printing services alongside its existing rotogravure capabilities. Due to the latest sleeve technology, flexo printing produces high-quality results in brilliant colour with a rapid output. In addition, Mondi’s press is able to apply effect inks and matt additives – resulting in premium looking films with the potential to influence purchasing decisions through an elevated user experience.
The new line offers the added appeal of inline siliconization, which eliminates the need for release paper, and inline embossing in answer to consumer preference for quieter, more discreet wrappers. Furthermore, the printing press gives customers the freedom to request complex designs thanks to precise registered printing for eye mark accuracy. This allows Mondi to feature different prints on the front and back of wrapping films and provides the option of partial siliconization for a more cost-effective printing run.
Jürgen Schneider, Managing Director, Personal Care Components at Mondi, comments: “The new flexo printing line enables us to better serve our customers in the hygiene industry through an altogether smarter printing process. Inline inspection systems for colour and silicone quality guarantee product reliability, while low ink consumption, minimal waste and shorter set-up times make this type of printing efficient and therefore also highly suitable for customers with varying lot sizes. What’s more, our installation can handle different film materials, including biodegradable or recycled content stock, which supports our customers’ sustainability goals.”
In the run up to the installation of the new flexo printing line, Mondi’s team in Gronau consulted closely with colleagues from its plant in Jackson, USA, which has offered flexographic printing services for personal care components since 2014.
About Mondi
Mondi is a global leader in packaging and paper, contributing to a better world by making innovative packaging and paper solutions that are sustainable by design. Our business is integrated across the value chain – from managing forests and producing pulp, paper and plastic films, to developing and manufacturing effective industrial and consumer packaging solutions. Sustainability is at the centre of our strategy and intrinsic in the way we do business. We lead the industry with our customer-centric approach, EcoSolutions, where we ask the right questions to find the most sustainable solution. In 2021, Mondi had revenues of €7.7 billion and underlying EBITDA of €1.5 billion.
Mondi has a premium listing on the London Stock Exchange (MNDI), and a secondary listing on the JSE Limited (MNP). Mondi is a FTSE 100 constituent, and has been included in the FTSE4Good Index Series since 2008 and the FTSE/JSE Responsible Investment Index Series since 2007.
About Mondi Personal Care Components
Mondi Personal Care Components (PCC) is part of Mondi’s Business Unit Engineered Materials and a leading global supplier of surgical face masks, nonwovens for wipes, melt-blown nonwovens, unique elastic films and laminates, siliconized wrapping films and mechanical fastening components. Committed to quality and producing products that are sustainable by design, we serve the hygiene industry by offering comprehensive baby care, adult incontinence and femcare solutions. Mondi PCC strives to make comfort a way of life and supports every generation by prioritising sustainability through responsible use of resources and, wherever possible, designing for recycling or biodegradability without compromising on performance and comfort. Our geographical footprint includes four plants in China, Germany and the US all supported by a state-of-the-art R&D Centre and pilot plant in Gronau, Germany.
Greater efficiency, lower costs, less plastic and still the same taste and convenience: When MULTIVAC exhibits at the two leading trade fairs, Anuga FoodTec 2022 (Hall 8.1, Stand C010) and IFFA 2022 (Hall 11.1, Stand B11), it will be showing a future-proof solution for packing thinly sliced or very sticky sliced products as part of a slicer line. Thanks to MULTIVAC's innovative Sustainable Liquid Interleaving spray system, there is no requirement for the conventional interleaving film between the individual product slices, and the consumption of plastics during packing can therefore be reduced to the bare minimum.
This process has long been standard with bakery products and sweets. Now MULTIVAC is presenting a versatile spray system, which has been specially developed for packing sliced sausage, ham and cheese or vegan alternatives. The solution can even be used with wafer-thin cut portions (e.g. shaved meat), for which the classic interleaver is not suitable. The space-saving spray system can be easily integrated into new or existing slicer lines. The individual slices are presented very attractively in the pack. Above all however, the slices do not stick to each other, and they can be removed cleanly by the consumer.
The functioning principle is simple - and perfectly designed for the product
The precision nozzles on the new spray system atomise a liquid interleaving medium, which is both odourless and tasteless and can be tailored to the particular properties, e.g. fat content, of the sliced product. The interleaving medium is applied evenly to the underside of the slices. The taste, quality and shelf life of the product are not impaired. The solution also however offers further benefits - particularly in terms of cost-effectiveness. “During our reference calculations, in which we simulated the slicing and packing of cheese, the typical film interleaves made of polystyrene generated total costs of around 3,800 euros per day. The daily costs for the interleaving liquid on the other hand amounted to only 425 euros - this equates to a saving of 85 percent,” explains Manfred Achenbach Senior Vice President of the Slicing Business Unit. The total time involved in refilling the interleaving liquid is up to 95 percent less than that for replenishing and threading the interleaver rolls. Other benefits of the spray system include: less storage space required, longer service life of slicer blades, and also less use of materials.
Trade fair exhibit
MULTIVAC will be showing the spray system at both trade fairs on a high-performance line featuring a slicer and thermoforming packaging machine. The modules for the automatic slicing, infeeding, packaging and labelling of the sliced product are integrated completely into one line, and they can all be operated efficiently and reliably from the HMI of the packaging machine or slicer thanks to the centralised MULTIVAC Line Control.
As part of the demo operation of the line, the product logs are sliced in multi-track format by the slicer, which also sprays each slice with the interleaving liquid. The individual portions are subsequently inspected on a checkweigher. Portions with the incorrect weight are ejected by means of a rocker for later weight correction by hand, while portions with the correct weight are conveyed onwards on a transport conveyor, before being grouped according to the format layout of the thermoforming packaging machine. The portions slide into the pack cavities during the advance, and the optimum loading results are achieved thanks to the flat loading angle. After the products have been packed under modified atmosphere, the MAP packs arrive at the cross web labellers, which apply the required labels to the top and base of the packs.
More added value
The technology has already been proven many times in practice. The spray system has been used successfully since 2018 on a MULTIVAC slicer at a dairy customer for interleaving cheese slices, and a ham producer uses this solution as well for extending the shelf life of his delicate products and intensifying their taste.
About MULTIVAC
MULTIVAC is one of the leading providers worldwide of packaging solutions for food products of all types, life science, and healthcare products, as well as industrial items. The MULTIVAC portfolio covers virtually all requirements of processors and producers in terms of pack design, output, and resource efficiency. It comprises a wide range of packaging technologies, as well as automation solutions, labellers, and quality control systems. The product range is rounded off with solutions upstream of the packaging process in the areas of portioning and processing, as well as bakery technology. Thanks to our extensive expertise in packaging lines, all modules can be integrated into complete solutions. This means that MULTIVAC solutions guarantee a high level of operational and process reliability, as well as efficiency. The MULTIVAC Group has approximately 6,900 employees worldwide, with some 2,300 based at its headquarters in Wolfertschwenden. With over 80 subsidiaries, the Group is represented on all continents. More than 1,000 sales advisors and service technicians throughout the world use their know-how and experience to the benefit of customers, and they ensure all installed MULTIVAC machines are utilised to their maximum. Further information can be found at: www.multivac.com.
Anuga FoodTec: 27 April 2022, 11 am Konrad-Adenauer-Saal in the Congress Centrum Nord IFFA: 16 May 2022, 11 am Raum T