Spray system replaces interleaver for th...
Sustainable slicing and packaging of products without interleaving film
Wolfertschwenden, 7 May 2021 – Slicing and packaging cheese, ham and vegan products sustainably: With its innovative spray system, MULTIVAC Sustainable Liquid Interleaving, MULTIVAC is introducing a sustainable solution for packaging thinly sliced or highly sticky products. This means that there is no requirement for the conventional interleaving film between the slices of these products – and the consumption of plastics during packing can be reduced to the bare minimum. Thinly sliced cheese, ham or vegan products are presented very attractively in the pack, and the individual slices can be removed cleanly by the consumer. The new system can be integrated into existing slicer lines, and it is available with immediate effect for individual tests and product development in MULTIVAC's new Center of Excellence for Slicers & Automation Solutions.
Precision nozzles on the spray system atomise a liquid interleaving medium, which is both odourless and tasteless and can be tailored to the particular properties, e.g. fat content, of the sliced product. It is applied evenly to the underside of the slices. The adhesion between the individual slices is therefore reduced, but the product itself (taste, smell, colour) however is not altered. This procedure is common practice in the food industry, e.g. with bakery products or sweets.
Customised applications in the Center of Excellence
Food producers can now convince themselves of the benefits of the new solution: “We want to offer Sustainable Liquid Interleaving to our customers as another innovation for the sustainable processing and packaging of their products. They are therefore invited to get an impression of our innovative solution in our new Center of Excellence for Slicers & Automation Solutions,” explains Manfred Achenbach, Senior Vice President of the Slicing Business Unit. “There we will be conducting customised tests with their sliced products in order to develop a bespoke system, which is designed perfectly for the particular product characteristics and the requirements of their slicing solution.”
At the beginning of the year, MULTIVAC put its new Center of Excellence for Slicers & Automation Solutions into operation as part of the so-called Training and Application Center (TAC) at the company's headquarters in Wolfertschwenden. There it is possible to view practically all the solutions from the MULTIVAC product range, which are used in the food industry. This includes the presentation of complete lines from product infeed to end-of-line, and these are tailored precisely to the needs of customers. The visitors get a feeling for the complete process chain, which is then reproduced later in their own production environment. The process chain ranges from a demonstration of the various slicers, through to the presentation of the different loading solutions downstream of the slicer, and right up to the actual packaging process itself. Working together with the customer, MULTIVAC's experts conduct customised tests with the particular product, while also examining the eventual solution for feasibility, output, give-away and yield - as well of course as the return on investment.
[3,323 characters incl. spaces]
About MULTIVAC
MULTIVAC is one of the leading providers worldwide of packaging solutions for food products of all types, life science, and healthcare products, as well as industrial items. The MULTIVAC portfolio covers virtually all requirements of processors and producers in terms of pack design, output, and resource efficiency. It comprises a wide range of packaging technologies, as well as automation solutions, labellers, and quality control systems. The product range is rounded off with solutions upstream of the packaging process in the areas of portioning and processing, as well as bakery technology. Thanks to our extensive expertise in packaging lines, all modules can be integrated into complete solutions. This means that MULTIVAC solutions guarantee a high level of operational and process reliability, as well as efficiency. The MULTIVAC Group has approximately 6,500 employees worldwide, with some 2,300 based at its headquarters in Wolfertschwenden. With over 80 subsidiaries, the Group is represented on all continents. More than 1,000 sales advisors and service technicians throughout the world use their know-how and experience to the benefit of customers, and they ensure all installed MULTIVAC machines are utilised to their maximum. Further information can be found at: www.multivac.com.
Company enquiries
MULTIVAC Sepp Haggenmüller SE & Co. KG
Tanja Nickels
Bahnhofstr. 4
D-87787 Wolfertschwenden Germany
Tel.: +49 (0) 8334 601 – 1544
E-mail: tanja.nickels@multivac.de
www.multivac.com
Press contact
REDAKON
Vera Sebastian
Seestr. 18
D-80802 Munich
Tel.: +49 (0) 89 – 31 20 338-21
E-mail: vera.sebastian@redakon.com
www.redakon.com
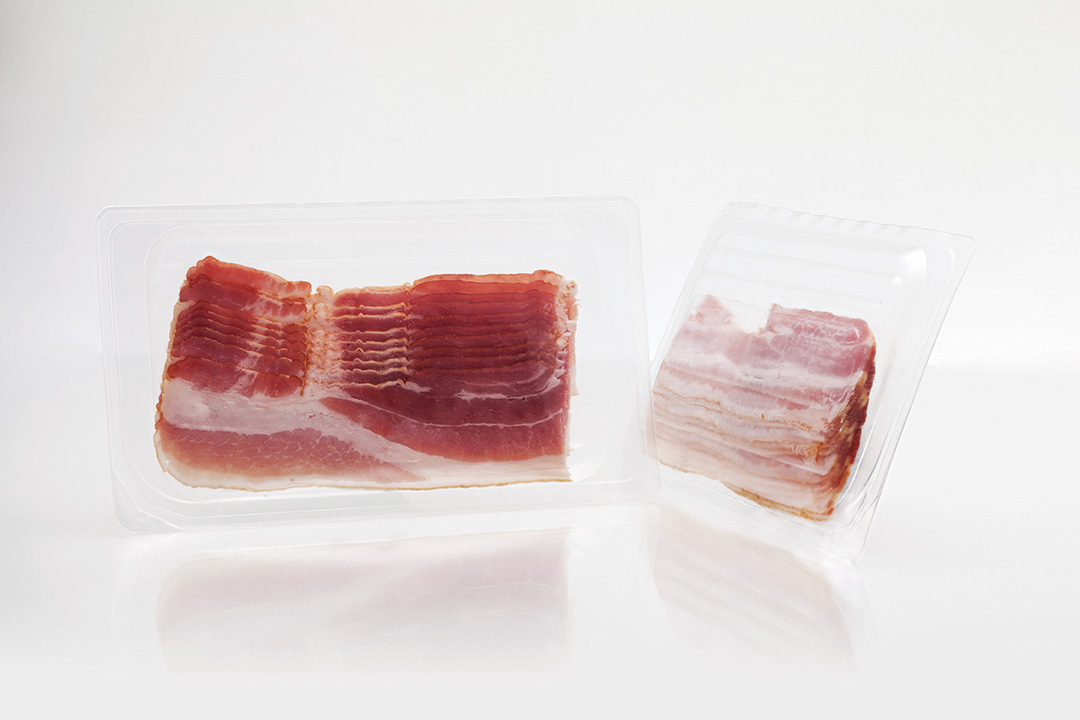