Reifenhäuser presents sustainable packa...
Troisdorf, April 9, 2021
After a forced break due to Covid-19, Chinaplas 2021 marks a new start of the trade show season for Reifenhäuser. From April 13 to 16, the specialist in plastics extrusion will exhibit in Hall 10 / Booth G07 at the Shenzhen World Exhibition and Convention Center. The company’s focus at the show will be on sustainable packaging solutions for a functioning circular economy. Ulrich Reifenhäuser, CSO of the Reifenhäuser Group, explains: “I am delighted to finally be able to resume in-person exchange with customers and partners - of course, in compliance with local hygiene regulations. Even if the ongoing travel restrictions mean that our Chinese colleagues from Reifenhäuser Plastics Machinery (Suzhou) Co., Ltd. are mainly in charge of the trade show appearance, it is a first step back to normality.”
Monomaterials and digital recycling solutions
Sustainable packaging solutions are the megatrend in the industry - and this is also the case at the largest plastics trade show in the Asian region. As a leading solution provider for Circular Economy products, Reifenhäuser promotes its production machines for monomaterial composites as well as other components. The problem with today's plastic packaging lies primarily in the material mix which cannot be separated in the recycling phase, or only with great difficulty. Therefore, no pure recyclates are obtainable from standard packaging, which explains why recyclability is low.
The solution: Customers produce monomaterial laminates (All-PE film) for flexible packaging on Reifenhäuser EVO Ultra Stretch blown film lines. The regular PET layer is replaced by stretched PE. With maximum stretching of
up to 1:10, the Ultra Stretch stretching unit gives PE film completely new mechanical properties. This is a simple replacement for PET and there is no need to adapt downstream processing steps. The unique and patented position of the stretching unit directly in the haul-off of the blown film line makes the process particularly stable and efficient. The film still warm from extrusion is stretched at the ideal time and without reheating. In addition, this simultaneously extends the natural annealing phase until the film is winded and gives the film the necessary time to adopt its new properties. The Ultra Stretch process is unique on the market and offers decisive advantages over film stretching that takes place conventionally between the haul-off and the winder. Visitors to the exhibition booth can experience the Ultra Stretch technology as an impressive 3D animation video and as part of a virtual 360° tour through the Reifenhäuser development center (Technology Center) projected on large event screens.
Reifenhäuser also presents a special highlight at the show: To be able to recycle fully recyclable plastic packaging at a high standard, special marking and data standards are required to identify packaging reliably when sorting waste streams and to make recycling properties transparent. Reifenhäuser is therefore promoting the R-Cycle tracing standard which is driven by a cross-company initiative. The standard can be networked as an open industry platform on all production and processing machines along the plastic packaging value chain and can store recycling relevant information automatically in a digital product passport. This information can then be retrieved in the waste sorting phase using digital watermarks in the printed image of the packaging.
Reifenhäuser will present this unique combination of fully recyclable monomaterials and digitalized recycling not only at its trade show booth, but also in a lecture at the "Plastics Recycling and Circular Economy Conference and Showcase 2021" that will take place at the Crowne Plaza Shenzhen Nanshan on April 12.
Biofilm for the Asian market
Another approach to sustainable packaging is biopolymers - plastics made from renewable raw materials. Reifenhäuser EVO Bio blown film lines are optimized specially to process biopolymers. They have a higher cooling capacity since biopolymers have a lower thermal conductivity. The range of applications is enormous and demand is growing on the Asian market. For example, milk bags popular in this country, or even mailing bags, can be easily produced using biopolymers. They have another advantage: After use, they are compostable. Customers can also process both bio-based and conventional raw materials flexibly on Reifenhäuser EVO Bio lines to respond rapidly to changing market requirements. To compensate for additional costs arising from the use of biopolymers, the line can be equipped with the optional EVO Ultra Flat Plus stretching unit which achieves savings of up to 40% in material resources. The stretching process makes the film stronger and stiffer, which means it can be made thinner with either identical or enhanced properties. In addition, stretching provides a better visual appearance.
Highly stable film through the use of water shock cooling
Besides sustainability, film performance naturally plays an important role - and here, Reifenhäuser offers a special technology highlight. With the EVO AquaCool series, customers produce highly robust and transparent film for particularly demanding applications, such as infusion bags for the medical sector. Instead of using air, the film tube is shock-cooled directly after extrusion by running water over the bubble. This creates the film’s special optical and mechanical properties. Subsequently, the water is removed from the film by vacuum. The vacuum calibration sets new market standards in terms of cooling capacity and film quality. With EVO AquaCool technology Reifenhäuser is one of the leading specialists in the medical sector.
Efficient flat film for safe food packaging
The coronavirus epidemic has revealed the vital importance of a safe and hygienic food supply for the ever-growing population of the world. Just as essential are methods to reduce food waste in the supply chain.
With high-performance MIREX barrier sheet systems, Reifenhäuser offers the film and packaging industry a safe and proven solution for the production of low-shrinkage and low-stress films with excellent thickness tolerances for optimized thermoforming performance. Mirex barrier systems clearly distinguish themselves from other common systems with their flexibility in combining layers and raw materials and the possibility of adjusting their distribution during ongoing production.
The patented REIcofeed Pro IE co-extrusion feedblock guarantees the best and most reliable single-layer thickness tolerances, which are critical for ensuring consistent barrier, seal and thermoforming film performance. In addition, it features a feedblock internal edge encapsulation device to reduce the use of barrier raw materials to the area of the film necessary for thermoforming. The additional edge encapsulation extruder usually required for this purpose, as well as the associated device on the flat die, can be eliminated. This saves space, energy and raw materials and increases the OEE (overall equipment effectiveness) of the extrusion line. The line has a broad range of applications, extending from standard packaging through to special "barrier thermoforming sheets" for coffee capsules.
On request, customers can obtain several product samples of the solutions exhibited on the trade show booth and receive competent advice from local Reifenhäuser experts who have many years of experience with the Asian market.
Nonwoven experts at Chinaplas
The ongoing high demand for nonwovens for protective face masks and medical protective clothing has resulted in an enormous increase in inquiries for nonwoven lines. Through its Reicofil business unit, Reifenhäuser is the global market leader for meltblown production lines - the high-performance filter material that effectively stops even the tiniest bacteria and viruses. That is why this year, in addition to film experts, nonwoven experts will also be in attendance at Chinaplas to field questions from the unabated high level of customer interest.
About the Reifenhäuser Group
With its highly specialized business units, the Reifenhäuser Group is the leading supplier of innovative technologies and components for plastics extrusion. Founded in 1911, the company supplies high-tech solutions all over the world. With its technologies and the know-how of its 1,600 employees, the Reifenhäuser Group has the world's largest competence network for plastics technology. CEO of the group is Bernd Reifenhäuser.
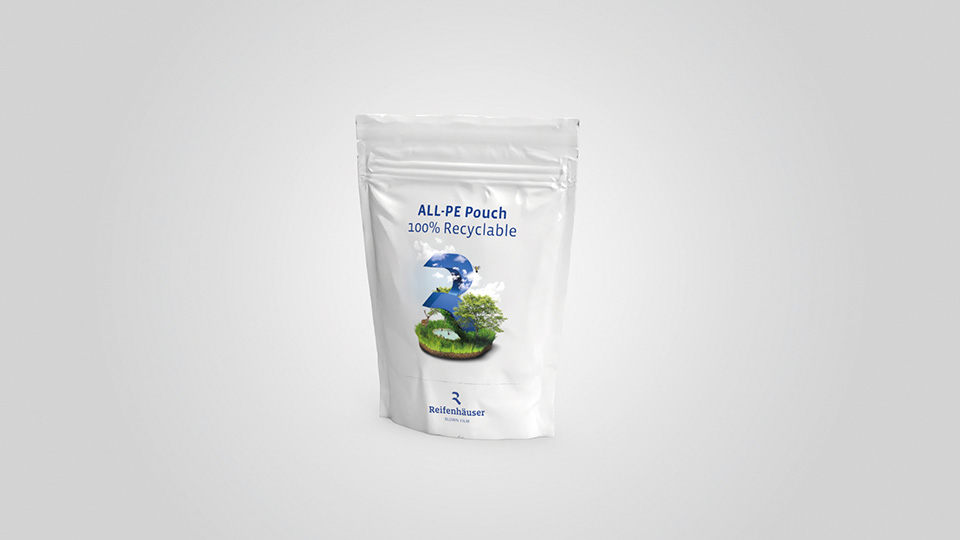