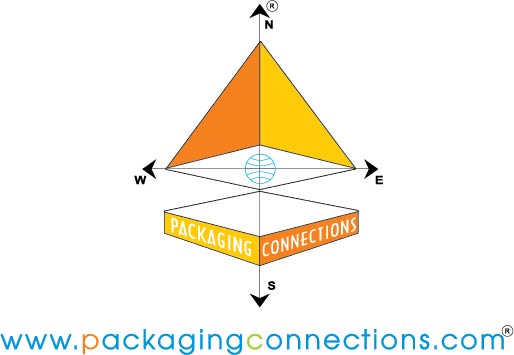
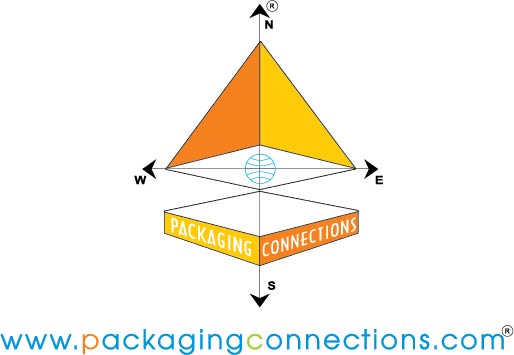
Activity
-
-
Smurfit kappa invests in circular approa...
Smurfit Kappa has completed a large-scale sustainability project at its Zülpich paper mill in Germany, which significantly reduces the plant’s CO2 emissions. The €11.5 million investment included a major redesign of the plant’s multi-fuel boiler to provide a more sustainable fuel source for the generation of steam and electricity.
The mill, which produces approximately 500,000 tonnes of paper annually, is now powered by a combination of its own biogas, which is a by-product of its circular water treatment plant, natural gas, and the residual materials or so-called ‘rejects’ which occur in the paper recycling process that would otherwise be considered waste.
The project reduces CO2 emissions at the Zülpich paper mill by more than 25% and saves 55,000 tonnes of CO2 annually, which represents a 2% reduction in Smurfit Kappa’s global CO2 emissions. Smurfit Kappa has the goal of achieving a 55% intensity reduction in fossil CO2 emissions by 2030 and at least net zero CO2 emissions by 2050. The packaging leader has also had its 2030 emissions reductions targets validated by the Science Based Targets initiative as being in-line with the Paris agreement.
The Zülpich circular approach also extends beyond its own operations to create loops with Smurfit Kappa’s Parenco and Roermond paper mills in the Netherlands. The rejects from Parenco and Roermond are a valuable source of fuel for Zülpich’s boiler.
Commenting on the Zülpich project, Pim Wareman, CEO of the Smurfit Kappa Recycled Paper Cluster, said: “The unveiling of this state-of-the-art multi-fuel boiler is yet another example of how, at Smurfit Kappa, sustainability is part of our DNA. The project shows that economic efficiency and sustainability are by no means mutually exclusive but can go together hand in hand taking the mill on a very positive journey.”Company NameSmurfit Kappa Group plcImage -
Multivac awards the prize to a microplas...
Wolfertschwenden, 28 June 2022 - Microplastics in food: The spectre that haunts the media. But what is the truth about fears, that particles from plastic packs could contaminate food? Luisa Kristina Murer, a student at the Technical University of Munich (TUM), has addressed these questions in her work for her Masters degree. She has been awarded the Hans-Joachim Boekstegers Prize 2022 by MULTIVAC for her commitment to safe food.
Whether salami, cheese or minced meat, it is inconceivable that food can dispense with plastic packs in everyday life. With good reason. Packs protect products against contamination and extend the shelf life through modified atmosphere - they also reduce the quantity of food waste and improve the CO2 balance of the food sector. And today the packs themselves consist to an ever growing degree of recycled plastic material. All good then on balance? Yes and No. Speculation continues to circulate in the media, that microscopically small plastic particles from packs can transfer to food and get into the human body. Conjecture that is hardly substantiated scientifically - but there is unfortunately little or no data and knowledge about the role of the manufacturing process in the production of packs.
Luisa Kristina Murer is developing a new method of determining the number of microplastic particles
In her work for her Masters degree, Luisa Kristina Murer, who is studying "Technology and Biotechnology in Food" at the TUM, is approaching the speculation about residual microplastics in food from a scientific perspective. The thesis observes in concrete terms the factors, which influence the potential occurrence of microplastics during the manufacture of food packs made from plastic films. The work of the TUM student has developed a standardised method, by which the number of microplastic particles in different plastic films can be determined. By using standardised food models, she has also pursued the question of whether these microplastics can transfer to food.“It was important personally for me to handle this sensitive topic in a neutral way, since the subject is often misunderstood and falsely represented in the media,” says Luisa Kristina Murer. “My work for example includes not only absolute figures, but also comparable values with natural particles, so that the quantities of microplastics are put in context.” But further research work is necessary, in order to increase the statistical relevance, and also be able to make reliable statements about the significance of plastic particles. The work has however already produced the following findings: The manufacturing process of plastic packs does influence the number of microplastic particles.
“One of my greatest aims in life is to leave the world in a slightly better state"
The jury for the Hans-Joachim Boekstegers Sponsorship Prize was very enthusiastic about the research work by Luisa Kristina Murer. Professors at the TU Munich and the TU Dresden, as well as representatives from MULTIVAC, were all of one mind: Luisa Kristina Murer's thesis was the best of all the Masters and degree work in the area of packaging technology, and which was also relevant to industrial-scale food processing, and her thesis therefore won the day against the other submissions from students at the Technical Universities of Munich and Dresden, as well as those from the Fraunhofer Institute for Process Technology and Packaging (IVV) at the Freising and Dresden sites. The panel therefore awarded the sponsorship prize and the sum of 1,000 euros to Luisa Kristina Murer.“I feel very honoured to receive the sponsorship prize,” says Luisa Kristina Murer, for whom it is much more than just about herself. “In my opinion, the subject of microplastics is very topical today. It means a lot to me, that this subject has been put under the spotlight thanks to the Hans-Joachim Boekstegers Sponsorship Prize. That shows me that innovations, which are relevant to the environment, are of great importance.” Luisa Kristina Murer now feels even more motivated to start a professional career in research and development. And to tackle subjects, about which nobody has yet thought. “It sounds a bit melodramatic. But one of my greatest aims in life is to leave the world in a slightly better state.”
About Hans-Joachim BoekstegersHans-Joachim Boekstegers started working at MULTIVAC on 1st April 2002 as the first Group President, who was not a family member. He significantly advanced the successful development of the company right up until his retirement in January 2020. He developed an international corporate group with a global network of sales and service subsidiaries out of a medium-sized machine manufacturer. He was always an advocate for investing in training and further education, and he supported cooperative partnerships with universities. MULTIVAC acknowledges his commitment to promoting young talent with the Hans-Joachim Boekstegers Sponsorship Prize.
About MULTIVAC
MULTIVAC is one of the leading providers worldwide of packaging solutions for food products of all types, life science and healthcare products as well as industrial items. The MULTIVAC portfolio covers virtually all requirements of processors and producers in terms of pack design, output and resource efficiency. It comprises a wide range of packaging technologies as well as automation solutions, labellers and quality control systems. The product range is rounded off with solutions upstream of the packaging process in the areas of portioning and processing, as well as bakery technology. Thanks to the company's extensive expertise in packaging lines, all modules can be integrated into complete solutions. This means that MULTIVAC solutions guarantee a high level of operational and process reliability as well as efficiency. The MULTIVAC Group has approximately 6,900 employees worldwide, with about 2,400 based at its headquarters in Wolfertschwenden. With over 80 subsidiaries, the company is represented on all continents. More than 1,000 sales advisors and service technicians throughout the world use their know-how and experience to the benefit of customers, and they ensure that all installed MULTIVAC machines are utilised to their maximum. Further information can be found at: www.multivac.com
Company NameMULTIVAC Sepp Haggenmüller SE & Co. KGImage -
New anti-fouling additive for the pp and...
Palsgaard has announced the introduction of an efficient new plant-based, food-grade anti-fouling additive for the polypropylene and polyethylene polymerisation process. The new product, Einar® 981, has been developed to remove severe concerns about the ethoxylated amine chemistry currently used. Einar® 981 will officially be introduced to the market at K 2022 in Düsseldorf, Germany.
Visit Palsgaard at K 2022 in Düsseldorf from October 19 through 26 in Hall 7, Level 1, Booth D20 to meet the company’s product and market specialists and discuss the sustainable benefits and superior performance of Einar® plant-based polymer additives.
About Palsgaard A/S
Palsgaard is a world leader in plant-based emulsifiers and polymer additives for the global food, packaging and plastics industries. Since its founder Einar Viggo Schou invented the modern plant-based food emulsifier in 1917, the company has provided advanced industry know-how and innovation to an increasingly diversified customer base. From application centres around the world, Palsgaard’s experienced technologists support brand owners and manufacturers in optimising their sustainability by the use of natural, renewable ingredients and additives to mitigate their carbon footprint.
Palsgaard helps manufacturers grow and protect their brands by meeting consumer and regulatory demands for greater responsibility. The company is currently the world’s only commercial source of fully sustainable emulsifiers and additives based on RSPO SG-certified palm oil as well as rapeseed, sunflower, and other vegetable oils. All products are non-GMO, have full EU and FDA food contact approvals, and also meet halal and kosher requirements.
The company’s food emulsifiers and emulsifier/stabiliser systems have a long history of adding to the quality and shelf-life of bakery, confectionery, condiments, dairy, ice cream, and margarine products. At the same time, they can significantly improve the taste, mouthfeel and texture while using fewer resources. Palsgaard’s plant-based polymer additives, including anti-fog and anti-static formulations for food and other packaging, build on this expertise and are rapidly emerging as highly effective and sustainable alternatives to conventional petrol-based additives.
Palsgaard, with headquarters in Juelsminde, Denmark, is owned by the Schou Foundation and has 653 employees across 17 countries. The company operates plants, sales offices and warehouses across four continents. All of their six production sites in Denmark, the Netherlands, Mexico, Brazil, China and Malaysia are carbon-neutral. In 2021, Palsgaard achieved a turnover of USD 260 million (DKK 1.7 billion) with products sold to customers worldwide in more than 120 countries.
Learn more about the company’s product and service portfolio at www.palsgaard.com/polymers.
Company NamePalsgaardImageDesignationSenior Brand Communications Specialist, Palsgaard A/S -
How to minimise waste through packaging
-
Toppan’s gl barrier mono-material pack...
Toppan’s prototype high barrier laminated tube with mono-material polypropylene (PP) composition using GL-BP, a PP-ba
-
Cremer introduces fast, accurate countin...
Fully servo-driven HQS 1250 Counting & Dispensing Machine provides 100% accuracy for bottling nutraceutical & confectionary gummies.
Cremer, a leading supplier of product counting machines in the U.S. for a wide array of applications, has introduced its HQS 1250 Counting & Dispensing Machine, designed specifically for gummy applications in the nutraceutical and confectionary sectors. Drawing on over 40 years of experience in the pharmaceutical market, Cremer developed the long-awaited gummy solution in partnership with filler manufacturer Spee-Dee.
The new 12-lane counter can precisely apportion gummies of all shapes and sizes to a downstream bottler or single belt setup. With an average output of 150 bottles per minute on a 60-count gummy product, the HQS 1250 is ideal for a wide variety of gummies in typical sanded or sugared formulations.
Market reports indicate the nutraceutical gummies market has experienced a compounded growth rate (CGR) of 12.5% between 2016-2020, and a forecasted 15.0% CGR is expected over the next decade. This makes the Cremer/Spee-Dee gummy solution a timely one.
Importantly, the HQS 1250 effectively alleviates two common obstacles that gummy manufacturers and co-packers routinely face: accurate counting and filling at medium-to-high speeds. Traditional multi-head scales are not 100% accurate when filling by weight, and gummies tend to clog when filled into a small bottleneck opening. The HQS 1250 seamlessly streams gummies without blocking in the bottle neck while also ensuring accurate counts at high speeds.
Counting food and various other products by the piece is regarded as the most efficient, cost-effective alternative to modern weighing and pick-and-place systems, as counting accuracy is not affected by small weight variations between individual pieces. Optical counting – as opposed to weight-centric quality control – guarantees that the net contents in terms of count is 100 percent accurate for both wholesale and retail packages. Optical counting also prevents product loss, avoids product wastage, and maximizes production efficiency.
Cremer’s HQS 1250 Counting & Dispensing Machine also brings benefits that distinguish it from competing counting solutions. For instance, its seamless integration with Spee-Dee allows for high-speed counting and filling with no clogs or jams, and offers industry-leading speed and accuracy and per-product customization. In addition, the HQS 1250 is delivered pre-assembled with all wires quick-locked for faster installation, and allows for quick, toolless changeover. The HQS 1250 counter is compact in size and, to preserve precious production floorspace, can be placed directly atop a packaging machine for bottle filling applications.
“At a time when the gummy market is rapidly growing, we are thrilled to have partnered with Spee-Dee on the new HQS 1250 counter to bring a reliable, high-speed counting and dispensing solution to gummy manufacturers,” states Brian Pomponio, Business Development Manager of Cremer North America. “Our innovative solution ensures consistent, accurate counts and reduces costly product loss in what is typically a very challenging application due to the sticky nature of gummy products.”
About Cremer
Since 1949, Cremer is the leading global supplier of counting machines and packaging solutions for the pharmaceutical, food, consumer goods and agricultural industries. As part of the Uhlmann Group, the Netherlands-based company is known worldwide for its dedicated focus on quality control.
Cremer’s highly technical and innovative machinery provides unsurpassed speed and precision, ensuring companies can count and package their products in a guaranteed accurate, fast, and profitable way. Cremer’s commitment to customized equipment solutions has led to a customer base ranging from small family-operated businesses to multinational corporations. For more information, visit www.cremer.com.
Company NameCremerImage -
Siegwerk’s deinking primer technologie...
With its UV- and water-based deinking primers for labels and sleeves, Siegwerk offers validated solutions for a safe and economic deinking of energy cured ink systems that have been so far considered as non-deinkable. This sets new norms to drive deinking as industry standard and further improve recyclability & circularity of plastic packaging.
Siegwerk, one of the leading global providers of printing inks and coatings for packaging applications and labels, today announced its most recent development for an improved deinking especially for rigid plastic packaging which is adding a substantial value to industrial mechanical recycling.
Beside the already existing water-based deinking primer (officially approved by The Association of Plastic Recyclers (APR)) Siegwerk is now offering an UV-curing deinking primer that is suitable for pressure sensitive and wrap around labels, and shrink sleeves made of Polyolefin- and Polyester-based materials. This development closes a gap as it now allows an inline printing of deinkable materials in a 100% UV-Flexo press setup.
Today, consumers expect higher recycling levels of plastic packaging where a meaningful reuse of the recycled material is mandatory instead of wasting the material into downcycling streams. This sustainability-conscious demand has driven brand owners to rethink their packaging to switch to 100% recyclable packaging in the near future. “Achieving this 100% packaging circularity requires a sufficient and consistent quality of recyclates,” explains Ralf Leineweber, Head of Global Technology Development at Siegwerk. In mechanical recycling as the today’s only established industrial recycling process, deinking of printed packaging material is one - if not the most - viable technology to meet this requirement. Only deinking can bring here clean and clear recyclates with a suitable quality back into the packaging stream to consequently reduce the need of more virgin plastic material. “That’s why we are committed to support customers with innovative solutions facilitating deinking and thus contribute to establish deinking as industry standard further improving packaging recyclability and circularity,” adds Guido Lander, Vice President Narrow Web EMEA at Siegwerk.
To integrate deinking into the recycling process, recyclers need to implement a hot washing step first, if not already existing. Here, it is critical that the deinking does not negatively impact the recycling process for example by contaminating the wash water. Besides, the lower the needed washing temperature for deinking the better - because this not only saves energy but also costs. More and more recyclers focusing on rigid plastic packaging such as trays, cups and plastic containers are implementing hot washing processes to improve the quality of their recyclates which enables an easy and seamless integration of a deinking step for a broad range of packaging materials. “We consider deinking primers as a key lever for smart deinking of crosslinked ink systems especially at low washing temperatures for sleeves, labels and other printed decoration for rigid plastic packaging,” explains Leineweber.
Siegwerk’s deinking primers enable a smooth and reliable deinking at any hot washing condition currently used in the recycling industry. They are compliant with different film materials like cPET, PE or PP and do not require the use of a dedicated ink series to keep complexity for users rather low. Besides, any printing process can be used in combination with our deinking primer portfolio – from flexo, offset and screen printing to foiling, metallic and other decorative embellishments. With its UV-curing deinking primer, the company especially offers a solution for converters who are using a pure UV flexo press and are not able to process a water-based primer. This primer shows best compatibility with UV-curing inks facilitating quantitative deinking according to the washing protocols of EPBP and APR. Applied under bleeding resistant UV-cured ink layers, the primer layer dissolves in the hot washing process and thus enables the generation of high-quality colorless recyclates, while the non-bleeding ink formulations ensure a clean and reusable washing solution.
Siegwerk is currently engaged in various deinking projects for all kind of rigid packaging solutions with in-mold and pressure sensitive labels as well as for direct printed rigid containers. “The greatest opportunities to improve plastic recycling in line with a circular economy obviously lay in areas where hot washing already became a standard step within the recycling process, such as in the PET bottle 2 bottle recycling,” adds Ralf Leineweber. Siegwerk has for example developed deinking technologies for shrink sleeves allowing a 100% recyclability of bottle and sleeve in food contact grade quality. Furthermore, the ink expert sees excellent opportunities to recover high-quality recyclates from postindustrial flexible packaging waste via deinking. Post-consumer waste is supposed to follow as well at a certain time due to its volume related importance.
Next to deinking primers, printing inks and coatings, Siegwerk also offers its customers technical services along the value chain to support an optimized and consistent deinking process. The company can also provide optimized deinking chemistry based on a systematic development to ensure fast deinking resulting in clean flakes with almost virgin quality of the recyclate. “Deinking is not a product for us, it is a “Full Service Offering” where everything needs tie together,” says Lander. “That’s why we follow a holistic approach and also offer the execution of deinking tests according to the most common washing protocols in our specialized laboratories.” Based on its deinking expertise, Siegwerk can guide customers through the entire process, from the unprinted substrate to the deinked and recycled packaging material, finally helping to optimize plastic packaging recycling in line with a circular economy.
About Siegwerk
Siegwerk, a sixth-generation family-owned company, is one of the leading international manufacturers of printing inks and individual solutions for packaging, labels, and catalogs. With more than 180 years of experience, the company has solid expertise in and knowledge of many printing procedures. A global manufacturing and service network ensures customers consistently high-quality products and services. In keeping with the company’s philosophy “Ink, Heart & Soul,” Siegwerk seeks long-term cooperation with its business partners. Siegwerk employs some 5,000 people worldwide in more than 30 country organizations and is headquartered in Siegburg near Cologne. Further information on Siegwerk can be found at www.siegwerk.com
Company NameSiegwerkCategory -
Catering to modern consumers’ sustaina...
Launches eco-friendly mattresses, mattress toppers, pillows and bed linens made with 100% natural materials enabling consumers to make smart sustainable choices
India’s leading sleep solutions brand, Duroflex, is at the forefront of research and innovation. The brand has wide product portfolio that caters to every kind of consumer. Over the past few years, there has been an upward trend in the number of consumers who seek products that not only meet their needs but are also good for the planet. To help these consumers extend their conscious choices to their sleep space, Duroflex has revamped and extended their eco-friendly range of mattresses and sleep accessories - Natural Living. On the occasion of World Environment Day, Duroflex has introduced mattresses, mattress toppers, pillows and bed linens made entirely of natural materials - 100% Natural Latex, Rubberised Coir, Cotton, Tencel and Ethicot.
The products in this range are crafted from ethically sourced sustainable materials and are produced without any intervention of heavy machinery. The GOLS certified latex used for the production of this range is sourced from the company’s own rubber plantation in Kerala. Currently, Duroflex is the only brand in India using GOLS certified latex. The chemical free pure cotton and bamboo fabrics contributes towards one’s health and well-being. They are hypo-allergenic, soft to touch, naturally resilient and highly breathable. The natural coir used in the mattress keeps the person naturally cool. Because of its use of natural materials this range is also highly recommended for people with allergies, respiratory disorders, and those who need extra care.
Speaking on the occasion, Mr. Mohanraj J, CEO, Duroflex, said, “As a responsible consumer brand, our endeavour is to support our consumers towards a sustainable lifestyle. With our Natural Living range, consumers will find everything they need for an eco-friendly and safe sleep space. The mattresses and sleep accessories under the range are made of GOLS certified latex, chemical free pure cotton and bamboo-cotton blend fabrics which contribute towards one’s health and well-being while being eco-friendly. The fact that we are one of the few brands with our own latex production in the country bears testament to the kind of quality we want to provide to our consumers.”
The mattresses under Natural Living range comprises four variants – Tatva, Prana, Kaya and Avaasa:
1. Tatva mattress combines the goodness of two natural materials latex and coir providing firm support
2. Prana mattress is made of Latex with Pocket Spring, where the best of nature meets the scientific support of spring
3. Kaya is a 100% Latex mattress, fully natural, and 100% biodegradable
4. Avaasa comes with a combination of latex layer and rubberised coir layer for comfortable firm support and is economically priced
The sleep accessories under Natural Living incudes Meha mattress topper, Nidraa Pillows and two types of bed linens under the name Sarrva made from different combinations of natural materials.
1. Meha mattress topper offers super comfy sleep and is made of 2” thick 100% Natural GOLS certified Latex. It can add a plush, supportive layer to any of your current mattress providing a healthy breathable full body support for sleeping in the natural environment.
2. Nidraa pillow offers immersive sleep experience which is chemical free with 100% Natural Latex. Ergonomically designed contour with two thickness options in each pillow shall offer best neck and head support irrespective of your preferred sleeping posture be it on the back, side or stomach.
3. Sarrva Cotton Tencel Bedsheet offers dreamy sleep experience which is softer than cotton, naturally cool surface with moisture wicking property
4. Sarrva Cotton Ethicot Bedsheet is eco-consciously sourced and diligently crafted to offer comfort, use of pre-consumer recycled cotton reduced the dependability on fresh natural cotton without compromising on goodness of 100% natural cotton.
Each product offers different levels of comfort and support based on individual needs. All these products will available across the brand website, major e-commerce platforms, retail outlets, as well as the company’s exclusive experience centres. To locate Duroflex brand experience centre near you, visit https://www.duroflexworld.com/a/store-locator/list.
About Duroflex
Duroflex is one of India’s leading sleep solutions providers with a wide range of premium mattresses and sleep accessories. This revolutionary brand with over five decades of expertise and state-of-the-art technology is redefining the meaning of quality sleep. Duroflex has distinguished itself as a leader in the industry with an innovative and cutting-edge range of products that is the first of its kind in India. Its signature range – Duropedic is India’s No.1 doctor recommended orthopaedic mattress range. The brand is today synonymous with quality, innovation, and comfort. Its product portfolio is backed by strong technical know-how, modern equipment, and the ability to understand future needs.
Company NameDuroflexImageCategory -
Mondi’s retortpouch recyclable wins sw...
- Mondi’s stand-up RetortPouch Recyclable scoops Swiss Packaging Award, demonstrating packaging innovation and creativity
- Packaging developed in partnership with Hilcona, a European market leader in fresh, ready-to-eat food, for Coop’s own brand range
- New mono-material packaging is recyclable and its exceptional durability helps to reduce food waste
Mondi, a global leader in sustainable packaging and paper, has been recognised by the Swiss Packaging Institute (SVI) for its RetortPouch Recyclable solution. The packaging won the Swiss Packaging Award for the Sustainability category and was developed for Coop’s private label range of healthy pulses and grains sold in Switzerland.
RetortPouch Recyclable, made of polypropylene (PP)-based mono-material, offers exceptional shelf life and reduces potential food waste. The innovative packaging can replace complex multilayer unrecyclable packaging that uses aluminum or metallised layers to provide high barrier food protection.
RetortPouch Recyclable is able to withstand high temperatures during the retort process used in food preparation and is suitable for a wide range of applications in the ready-made food and pet food industries. The packaging, which is used for Coop’s products that are manufactured by Hilcona, has an attractive yet sturdy stand-up design that includes a transparent window to allow consumers to view the product on-shelf.
“We are very proud of this award. Hilcona has played a key role in the development of a truly collaborative approach to this award-winning packaging, looking closely at how we could protect the product, while delivering convenient packaging that worked for Coop and the consumer in a sustainable way,” explained Hilcona packaging expert Julia Bredemeier.
We’re delighted to have the RetortPouch Recyclable recognised by the Swiss Packaging Institute (SVI). This solution is a result of our EcoSolutions approach to creating sustainable fit-for-purpose packaging, working in close collaboration with our customers and partners. RetortPouch Recyclable is an innovative, easy to use mono-material packaging solution that can reduce food waste while being an attractive option for food manufacturers and retailers alike.
About Mondi
Mondi is a global leader in packaging and paper, contributing to a better world by making innovative packaging and paper solutions that are sustainable by design. Our business is integrated across the value chain – from managing forests and producing pulp, paper and plastic films, to developing and manufacturing effective industrial and consumer packaging solutions. Sustainability is at the centre of our strategy and intrinsic in the way we do business. We lead the industry with our customer-centric approach, EcoSolutions, where we ask the right questions to find the most sustainable solution. In 2021, Mondi had revenues of €7.7 billion and underlying EBITDA of €1.5 billion.
Mondi has a premium listing on the London Stock Exchange (MNDI), and a secondary listing on the JSE Limited (MNP). Mondi is a FTSE 100 constituent, and has been included in the FTSE4Good Index Series since 2008 and the FTSE/JSE Responsible Investment Index Series since 2007.
Company NameMondiImageDesignationSenior Communication Manager Flexible Packaging & Engineered Material -
Corrbox solution
“Sustainable packaging regulations, zero-defect production, rising cost pressure, the increasing shortage of skilled
-
How a warehouse management system impact...
There has never been a time as it is now when the demand for efficiency is so high in the manufacturing sector. Manufacturers face the challenge of producing more products within only a limited time -
Schreiner group receives important us pr...
Airbags save lives, but need to be labeled correctly and deploy at the right moment to do so. A marking label and an airbag tape from Schreiner Group ensure that. Now both products have been recognized with the prestigious TLMI Award.
Every year, the American Tag and Label Manufacturers Institute (TLMI) nominates the best products of the printing industry. In selecting award-winning entries, the judging panel places particular emphasis on innovation and technical achievement. The prestigious recognition has previously gone to Schreiner Group from Oberschleissheim, Germany, on several occasions. In the 2021 TLMI Awards competition, Schreiner Group was able to celebrate two wins: a first-place award for its marking label of an airbag control unit and a second-place award for its airbag tape. Both are products from the Schreiner ProTech business unit that develops innovative marking solutions and film-based functional parts specifically for the Mobility market.
All the individual components have to be installed correctly to ensure the protective effect of an airbag. The marking label from Schreiner ProTech that won a first-place TLMI Award supports that. The special aspect of this product is a combination of the material and adhesive system ensuring reliable adhesion of the label throughout the entire lifecycle of the airbag control unit. Security slits prevent non-destructive removal of the label, for instance by product pirates to mark counterfeit components—which enhances product safety for manufacturers and consumers significantly.
A second-place award went to the airbag tape, another entry from Schreiner ProTech. This product has several functions as well, featuring customized printing and serving as an installation aid and tape rolled into one. The tape is produced specifically for head and shoulder airbags, which are tube-like, folded airbags attached to the vehicle’s body shell. The airbag tape keeps them in their folded condition—from pre-assembly to installation in the vehicle to potential airbag deployment.
For CEO Roland Schreiner, the awards are tremendous motivation: “I am delighted that we were so successful in the TLMI Awards once again—this time with as many as two awards. That shows that our innovations are seen and motivates us immensely.” The high-tech company has had its own US site in Blauvelt, New York, since 2008–and has been a supplier to the American market for more than 20 years.
+++
SGR_TLMI-Award-2021:
In the 2021 TLMI Awards, Schreiner Group was recognized twice for multifunctional airbag labels.
+++
For more information, please contact:
Susanne Höppner, Corporate Communications
Phone +49 89 31584-5852, susanne.hoeppner@schreiner-group.comAbout Schreiner Group
Schreiner Group GmbH & Co. KG is an internationally active German family-owned company and regarded as a preferred partner in the Healthcare and Mobility markets. Its core business is focused on top-quality functional labels enhanced by complementary system solutions and services. Schreiner Group’s innovative high-tech labels and functional parts create new dimensions for smart solutions and help make life healthier and safer, and enhance human mobility.
More than 1,200 employees generate total annual sales of about 190 million euros. The high-tech company has four locations: In addition to the headquarters in Oberschleissheim and another production site in the Munich metropolitan region (Dorfen), they include the two international manufacturing facilities in the United States (Blauvelt, New York) and in China (Fengpu, Shanghai).
Collaboration and exchange are shaped by the core values of Innovation, Quality, Performance and Enthusiasm. Schreiner Group defines itself as a company committed to acting sustainably and therefore deliberately assumes responsibility for people, the environment and society.
Company NameSchreiner GroupImageDesignationCorporate Communications -
2022: the road ahead
-
Lighter cap from berry contributes to a ...
A new closure from Berry Global, specifically created for sauces, demonstrates the company’s circular design capabilities in devising a lightweight and recyclable solution while continuing to deliver consumer convenience benefits.
Berry has utilised its technical skills to create a closure that is lighter than other versions currently available, offering valuable material savings without compromising its strength and durability to ensure a consistently reliable performance. The closure is manufactured 100% in polypropylene (PP).
The closure design features an extended narrow spout that provides controlled and accurate dispensing of product for the end user. It can be specified in snap-on or screw-on versions and is suitable for bottles with a 38mm neck finish, including Berry’s extensive range of standard sauce bottles, enabling the company to offer customers a complete bottle and closure solution.
“Our new closure has been designed to be extremely versatile to meet the many different needs of the food sector, while delivering a reliable performance and helping food manufacturers to improve the sustainability of their packaging,” commented Matthias Hammersen, Sales Director, Food Market, Berry Global. “We look forward to continuing to support our customers in achieving their lightweighting objectives and developing packaging solutions that help them become even more sustainable.”
For more information on Berry’s wide range of packaging solutions, visit www.berryglobal.com
Image -
Atlas copco sets standards in connectivi...
Cologne, December 2021: For intelligent networking of machines and systems, it is elementary that industrial processes can be controlled centrally. In order to prepare industrial vacuum users for the Internet of Things and Industry 4.0 scenarios, the manufacturer Atlas Copco has developed the innovative HEX@GRID control platform.
The central multi-pump control has a multitude of intelligent functions and sets new standards in terms of connectivity and energy efficiency.
Reduced costs for operation and maintenance
In terms of optimised operating processes, users have the opportunity to improve theirvacuum performance. In addition, costs can be saved with the HEX@GRID because a properly tuned vacuum system is easier and more cost-effective to operate and maintain. "Another benefit for users relates to connectivity, because with the new controller all vacuum components can be integrated into one system," explains the responsible product
manager, Yuri Vanderveken.
Values in real time on the terminal
This allows customers to operate their systems from a single source, regardless of location: For example, if several components of a vacuum system with variable speed control (VSD) have to keep the pressure constant. "With the help of the HEX@GRID's optional 10-inch HMI interface, users get a complete insight into the central vacuum system," Yuri Vanderveken points out. "The individual, intuitive user interface allows the values of the system components to be entered and monitored in real time via laptop, tablet or smartphone," the product manager adds.
Checks become a finger exercise
Thanks to the full connectivity of the HEX@GRID, updates and new functions can also be downloaded directly. A notification function on the selected end device always keeps users up to date. Further advantages: Regular checks of the vacuum system become an easy finger exercise, and calibration also becomes easier. "If required, the user can add schedules, plan actions and thus secure the entire process. With the help of the central
setpoint control, the vacuum system can be operated in a stable and intelligent way," explains Yuri Vanderveken.
Different features, depending on the application
Depending on the application, different HEX@GRID versions are available to the user. For vacuum users with a HEX@, MK5 or other Atlas Copco controller, there is a standard HEX@GRID version as well as an updated version with Optimizer. "Both versions can also control third-party products," says Yuri Vanderveken. For vacuum systems consisting of DZS VSD+ or GVS VSD+ pumps, the VSD+ app is suitable; for a system with up to 16 vacuum pumps, the LINK HEX@GRID with pressure sensor and virtual machine control.
Maintenance intervals are optimized
With LINK control, the user has the advantage of operating the vacuum pumps as 1 virtual machine. Depending on the process, these pumps are started one after the other at 60%, each time the first pump acting as the VSD leader is reaching full capacity. Once all follower pumps are at 60% and the leader pump runs out of capacity, these follower pumps can increase their capacity in steps of 10% as 1 machine. For processes with a predefined operating time, the provision of reserve pumps is crucial. The LINK control coordinates the use of backup pumps to optimise maintenance intervals.
Master pump compensates for fluctuations in demand
The standard version of the HEX@GRID platform controls up to eight pumps. “It has virtual machine control and thus the same working principle as the LINK where we have a leader pump adapting VSD to the demand and follower pumps working as 1 within the 60-100% capacity range" Yuri Vanderveken elaborates. The bottom line is that this can lead to a reduction in energy consumption of up to 10 % compared to conventional
sequencers. "In addition, the operating hours of different pumps in a network can also be balanced out," sums up Product Manager Yuri Vanderveken. The tip of the technological iceberg however is the Optimizer control algorithm. Each individual pump in a vacuum system has a different specific energy at different speeds and inlet pressures.
HEX@GRID uses that information to continually optimizes the speed of each of those individual pumps by calculating the most energy efficient way to control the entire system based on the demand. As an addition up to 20 pumps can be controlled by the Optimizer control.Atlas Copco Vacuum Technique
Great ideas accelerate innovation. At Atlas Copco Vacuum Technique we collaborate with our customers to turn industrial ideas into leading edge technology in vacuum and abatement solutions. Our passionate people, expertise and service bring sustainable value to industries everywhere. Atlas Copco is based in Stockholm, Sweden with customers in more than 180 countries and about 40 000 employees. Revenues of BSEK 100/ 10 BEUR
in 2020. At Atlas Copco Industrial Vacuum, we have revolutionized vacuum technology. Our state-of-the-art vacuum pumps and systems exemplify today’s connected and digitalized industry. Our teams of exceptional and passionate people engineer customer-centric vacuum solutions that offer better energy efficiency, consumer safety, improved productivity and a sustainable future. Our products are the invisible force that drive all industrial applications and manufacturing.ImageDesignationProduct Manager – Accessories -
Atlas copco develops vacuum controller f...
Cologne, December 2021: In HEX@, Atlas Copco has developed the industrial vacuum controller of the future. It serves as an enhanced control centre for vacuum pumps and systems. Ensuring higher vacuum performance and functionality as well as increased user empowerment across a large range of applications. By also offering increased connectivity and system integration, HEX@ brings convenient remote access to their vacuum system with increased control anywhere.
Only selected values are displayed
HEX@ has a clean and intuitive user interface. This is vital. HEX@ users access key data directly on the home screen and can access further settings and controls easily using the on-display menu. Relevant pump data is displayed quickly and legibly. "The controller can be individually configured by our customers so that only selected values, such as discharge temperature, power consumption or inlet pressure are displayed" explains the responsible product manager at Atlas Copco, Alistair Darroch.
Connectivity to suit all
The communication options for HEX@ enabled pumps are also diverse, users can access the unit remotely using smartphones, tablets, laptops or PC; alternatively, access can be via the onboard HMI interface or a local device connected to the machine using wired or WiFi based connections.
“Customers can choose to connect fully to their local network and also the cloud to take complete advantage of a fully connected pump including automatic updates to software and functionality as well as remote support from Atlas Copco in the event support is required. If this level of connectivity is not desired, HEX@ can connect only to the customers network or even not at all” informs Alistair Darroch. Further, HEX@ will also support other communication protocols such as Ethernet/IP, EtherCat, Profinet, Modbus TCP, Profibus and OPC UA.Focus on four core areas
The HEX@ controller is continuously collecting and processing a wide range of pump data. When it comes to making use of this data, Atlas Copco have defined four elementary yet powerful vacuum system attributes we can use to evaluate a vacuum system: Uptime, Performance, ECO and Health.
These indicators allow customers to quickly assess the status of their vacuum pump, to understand the impact of any changes made on their vacuum system and ultimately, their process.
- The uptime is the indicator for the availability of the pump. It documents how long the pump runs without failures.
- In the case of performance, HEX@ considers if the pump is achieving the required vacuum targets set by the customer.
- The so-called ECO status provides information about the efficiency potential of the vacuum pumps. By comparing the targeted set-point pressure with the current operating pressure, users receive feedback if vacuum pump is using more energy than necessary.
- Finally, the health status evaluates failures and key measurements to assess the pumps current status and also takes into account when services are due. Informing the customer if their pump health can be improved.
Summary on HEX@ Insight Cards
"These four key performance indicators (KPI) are used to draw conclusions about the current conditions on what we introduce with HEX@ as Insight Cards, which provide feedback on the status of the vacuum system as well as optimization recommendations," says Alistair Darroch. In addition, they include recommendations for increasing pump life, reducing energy consumption, improving the carbon footprint and extending maintenance intervals.Pump settings can be recalled at any time
The configured pump settings can be saved as a “mode” and then recalled at any time. The appropriate mode ensures that the pump also calls up the required performance. These HEX@ modes can be accessed easily and quickly by the user by pressing a button on the control panel or by accessing the pump remotely. This is not all, the HEX@ has additional smart functionalities, such as Trends: Trends showcase historic data to give valuable overviews of various measured parameters, including data on inlet pressure, engine speed, power consumption oil temperature and more. By comparing the current and historic data, users can better understand the consequences of changes in process or pump settings.
There is no doubt that HEX@ puts the customer in the driving seat when it comes to monitoring, controlling and optimizing their vacuum installation and vacuum using processes.Atlas Copco Vacuum Technique
Great ideas accelerate innovation. At Atlas Copco Vacuum Technique we collaborate with our customers to turn industrial ideas into leading edge technology in vacuum and abatement solutions. Our passionate people, expertise and service bring sustainable value to industries everywhere. Atlas Copco is based in Stockholm, Sweden with customers in more than 180 countries and about 40 000 employees. Revenues of BSEK 100/ 10 BEUR
in 2020.
At Atlas Copco Industrial Vacuum, we have revolutionized vacuum technology. Our state-of-the-art vacuum pumps and systems exemplify today’s connected and digitalized industry. Our teams of exceptional and passionate people engineer customer-centric vacuum solutions that offer better energy efficiency, consumer safety, improved productivity and a sustainable future. Our products are the invisible force that drive all industrial applications and manufacturing.Company NameAtlas Copco Vacuum TechniqueImageDesignationProduct Manager – Liquid Ring Pumps & Sales Tools -
Schreiner medipharm develops fixation ai...
-
Marketing 101: can you judge a product b...
-
Packaging in space: yesterday, today & t...
Our upcoming webinar will discuss Food Packa